You’ve got questions about Spray Foam roofing, such as:
- What is spray foam roofing?
- What are the advantages of a spray foam roof?
- What problems do spray foam roofs have?
- How much does a spray foam roof cost per square foot?
- How does a spray foam roof get installed?
And probably much more.
Before we get started, here’s a quick, 30-second video of spray foam being installed:
What Do You Want to Learn About First?
[click on any chapter below to go directly to it]
Chapter 1: What is Spray Polyurethane Foam Roofing?
Chapter 2: What Are the Advantages of an SPF Roof?
Chapter 3: What Problems Do SPF Roofs Have?
Chapter 4: How Much Does a Spray Polyurethane Foam Roof Cost?
Chapter 5: How Does an SPF Roof Get Installed?
Chapter 6: Spray Polyurethane Foam vs Built-Up Roofing
Chapter 7: Spray Polyurethane Foam vs Single-Ply Membrane
Chapter 8: Spray Polyurethane Foam vs Silicone Restoration Membrane
Chapter 9: How Long Will an SPF Roof Last?
Chapter 10: How Is a Spray Foam Roof Repaired or Maintained?
Chapter 11: Common Questions to Ask a Commercial Roofing Contractor
Chapter 12: Case Studies on SPF Roofs
Chapter 13: How Is a Spray Foam Roof Renewable?
Chapter 14: Can You Install a Spray Foam Roof Over TPO?
Chapter 15: Can Spray Foam Be Installed Over a Commercial Metal Roof?
Chapter 16: 4 Factors That Influence Lifetime Cost of a Roofing System
Chapter 17: A Review of a Spray Foam Roof
Chapter 18: How Durable is Spray Foam Roofing?
Chapter 19: What Are the Installation Requirements to Apply Good Spray Foam?
Chapter 1: What is Spray Polyurethane Foam Roofing?
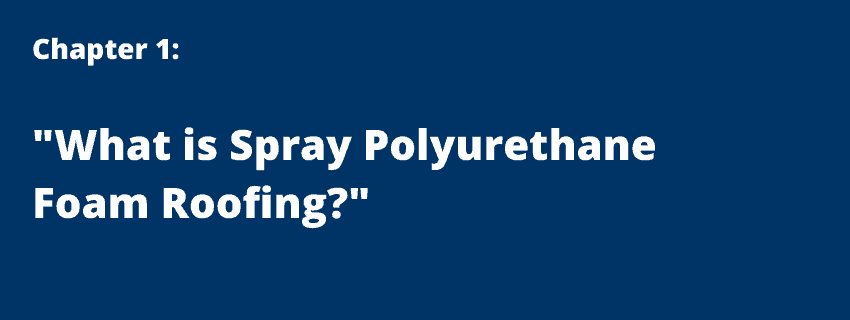
Spray Polyurethane Foam Roofing, or spray foam roofing, is a material that’s sprayed as a liquid so it can expand into a foam, creating a solid layer across an existing roof.
The usual application of spray foam is to repair and reinvigorate an existing roof by removing the saturated areas, replacing them with like materials, and then spraying foam over top of the entire roof.
While SPF roofing is not the most known type of roofing material, the technology has been around since the early 1960s for industrial, commercial, and residential facilities. An SPF roofing system can be used in any climate, and when correctly installed and maintained, can last over 50 years.
Spray Polyurethane Foam (SPF) for roofing applications is manufactured on the job site by mixing two highly reactive chemicals.
The chemicals, A (polyol/resin) & B (isocyanate), are pumped from separate containers through heated, high-pressure hoses to an internal mixing spray gun.
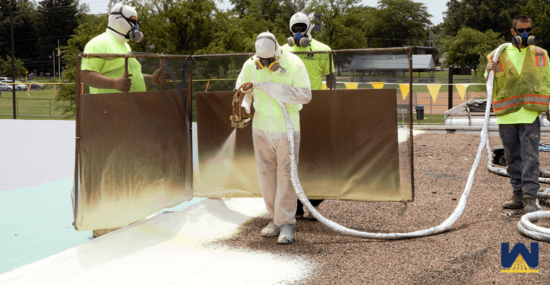
Chapter 2: What Are the Advantages of a Spray Polyurethane Foam Roof?

Here Are the 7 Primary Advantages of a Spray Polyurethane Foam Roofing System
- High R-value
- Renewable
- Quickly installed
- Self-flashing
- Seamless
- Easy to maintain
- Proven since the 1960s
1. Spray foam roofs have a high R-value
Spray polyurethane foam has the highest R-value of any commonly used roof insulation. Here are the average R-values for some common roof materials
- Spray Polyurethane Foam: 6.6 per inch
- Metal: 0.00 per inch
- BUR Gravel: 0.34 per inch
- BUR Smooth: 0.24 per inch
- XPS Insulation: 5.0 per inch
- EPS Insulation: 3.85 per inch
- Polyiso: 5.5 per inch
R-value is the capacity of an insulating material to resist heat flow. The higher the R-value, the greater the insulating power.
The higher the R-value, the less heat or cool air that will pass through. Higher R-value = less HVAC use = lower energy costs
Total payback of your new roof usually occurs in less than ten years through savings in heating and cooling costs.
2. Spray foam roofs are renewable
One of the benefits of a polyurethane roof is its ability to be re-coated.
A properly installed and maintained spray polyurethane foam roof should not require re-coating for 10 to 20 years. The best way to determine when a spray foam roof needs to be re-coated is to measure the remaining coating thickness on the roof and recoat before the coating is too thin to provide U.V. protection.
The first application of the coating is usually applied at a thickness of 20-30 mils.
After 10 years, the coating could be reduced to a thickness of 7-10 mils, depending on the wear of the roof.
Many coating manufacturers offer extended warranties with each re-coat. This option, along with scheduled maintenance, allows a spray foam roof to be a truly renewable roof system.
3. Spray polyurethane foam roofs are quickly installed
Spray foam roofs are installed quicker than other roofing systems, due to:
- Most SPF roofing projects involve little to no tear-off
- Spray foam roofs are spray-applied, meaning they can go around penetrations with ease
- Spray foam roofs require less material and equipment than traditional roofing systems
One example would be roofing around a penetration. With spray foam being “spray-applied”, it would take about 2 minutes to roof around a penetration, as opposed to rubber roofing, which can take at least 30 minutes due to the custom cutting of materials.
4. Spray polyurethane foam roofs are self-flashing
Self-flashing refers to spray foam’s ability to conform to irregular shapes. Watch the video below which shows spray foam being sprayed around a curb:
In the video, it says it might take a conventional roofer 30 minutes to flash around a curb, spray foam can be applied in about two minutes.
Other roofing systems, like rubber, will need to be custom cut to be installed properly around a curb.
Self-flashing allows spray foam to be applied faster around all penetrations, including:
- Parapet walls
- Vents
- Pipes
- HVAC units
- Skylights
- Drains
5. Spray polyurethane foam is seamless
A big advantage spray polyurethane foam has over other roofing systems is that it’s seamless.
Being seamless, and therefore monolithic and watertight, avoids traditional single-ply membrane seams that tend to be the sources of leaks.
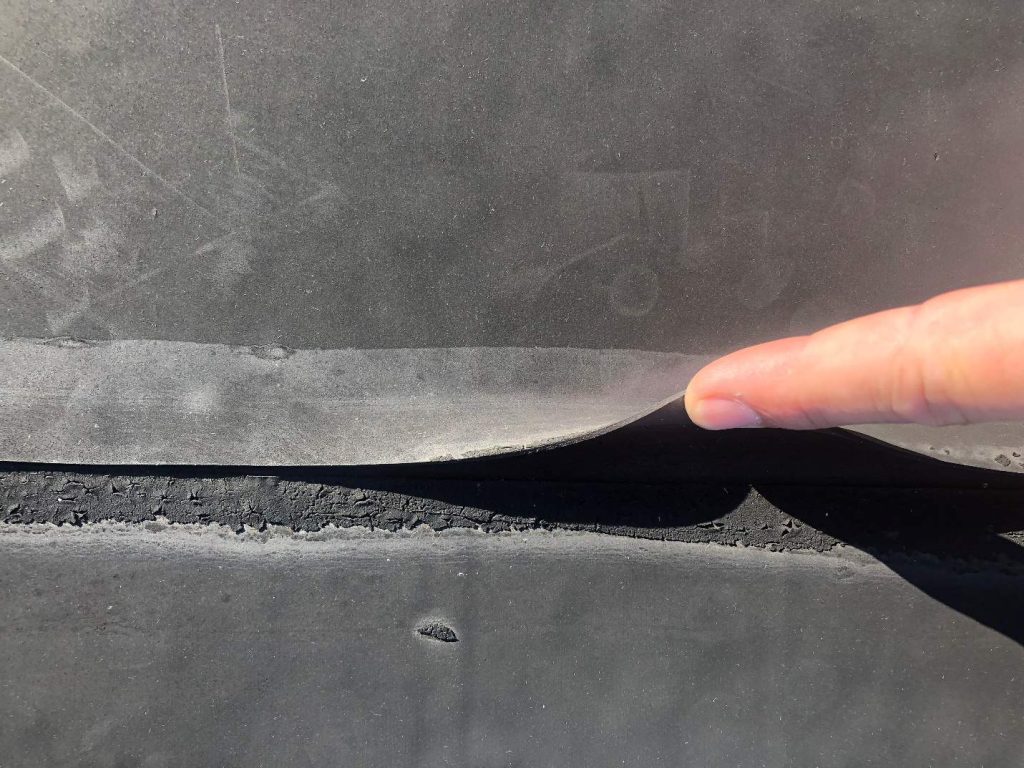
How do leaks form on a rubber roof?
Seams start to separate over time and allow water to get inside. Also, they can allow some water to get in, it freezes, and when it thaws out, it breaks apart the seam even more.
Wind uplift is also an issue with seams. Wind will eventually get underneath a slightly separated seam, loosen and eventually allow an opportunity for water to enter the building.
With spray foam being seamless, there is no opportunity for wind to get underneath a spray foam roof.
6. Spray polyurethane foam roofs are easy to maintain
Perhaps a sharp tool has been dropped or the HVAC guy planted the HVAC panels in your roof like a javelin.
To fix these minor repairs, all you’ll need is a utility knife and some caulk.
Step 1: cut out the defective area
Step 2: dry the area out
Step 3: apply caulk and smooth
That’s it. Minor repairs can be done by in-house maintenance staff.
7. Spray polyurethane foam is proven to be beneficial
Since the early 1960s, spray polyurethane foam roofs have been installed and re-coated, strengthening the popular phrase, “A spray foam roof is the last roof you’ll ever have to install.”
Multiple roofs that have been installed decades ago are going on their 2nd or 3rd re-coat.
Spray foam: A cost-effective and versatile roofing solution
Polyurethane roofs are installed quickly, resulting in a lower labor cost and less interruption. When considering the many variables in a re-roofing project, the versatility of a polyurethane roof makes it a logical and cost-effective solution.
Chapter 3: What Problems Do Spray Polyurethane Foam Roofs Have?
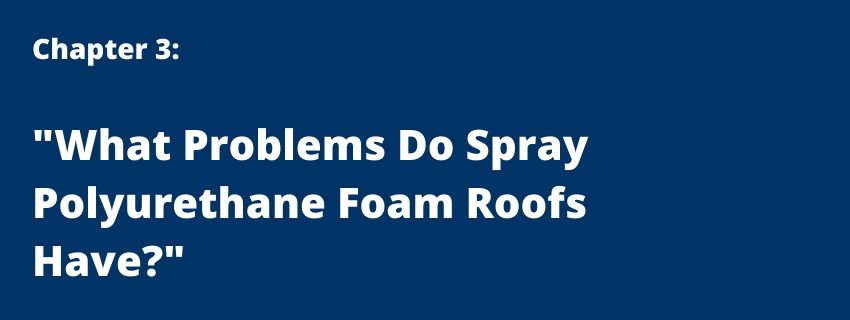
1. Weakness to UV Rays
The greatest weakness to spray polyurethane foam is its inability to resist the ultraviolet rays of the sun.
Within 72 hours, uncoated spray foam will begin to deteriorate.
Under direct sunlight, spray foam will degrade at a rate of 1/16th inch per year.
Solution
To protect a spray foam roof from UV damage, various types of elastomeric membranes are installed.
Possible membranes are:
- Silicones
- Urethanes
- Acrylics
These coatings are spray or roller applied (depending on the amount of wind) over the spray polyurethane foam, forming a seamless protective membrane.
In addition to UV protection, these coatings are engineered to provide waterproofing, impact resistance, and improved fire ratings.
Here is a video showing a spray foam roof from start to finish, but if you play the video, it’s fast-forwarded to show foam being sprayed down, and a base coat of silicone (grey-colored) sprayed over top:
2. Limited Installation Window
SPF Roofing is a spray installation, this application technique means that the SPF needs to be installed in specific weather conditions. The best weather conditions are warm and dry with minimal wind.
The temperature needs to be 50 degrees and rising to correctly apply spray foam.
Solution: Contact your contractor before your area’s roofing season, that way you can schedule your installation early, and you have plenty of time to reschedule if the weather changes.
3. Finding the Right Contractor
As foam roofing gains popularity with commercial property, you want to make sure you find a reputable contractor. Unlike traditional roofing, installing an SPF roof requires knowledge of the chemicals and application techniques. Installation requires a high degree of technical expertise and experience.
Solution: Check to see if your potential contractors are certified and take part in industry organizations. The Spray Polyurethane Foam Alliance (SPFA) has a certification program that has multiple levels and requires the contractor to pass an exam. You can find a database of certified contractors online.
4. Overspray Potential
The spray application of SPF roofing means that the wind could carry foam onto cars and other surfaces. While this does not pose a health concern, it is a concern for surrounding property.
Solution: There are multiple ways to prevent this from happening. Discuss with your contractor to ensure that they utilize industry best practices to prevent overspray. If it does happen, your contractor should cover cleanup costs.
5. Upfront Costs
For an average 20,000 sq. foot commercial roof, it will usually cost between $5.00 and $10.00 per square foot in materials and labor to install a typical SPF roofing system. Compared to other flat roofing systems, this upfront cost can be higher.
Solution: An SPF roof pays for itself quickly with energy savings and longevity of the roof. You can work with your contractor to calculate potential energy savings to make sure you installed the right thickness of SPF.
6. Maintenance
SPF roofing systems should be regularly inspected whether there is known damage or not–especially after severe weather events that could cause damage, such as hail storms, tornadoes, and hurricanes. Punctures and damage should be caught early to prevent leaking into the facility.
Solution: Most contractors have maintenance plans and warranties to keep your roofing system in decent shape.
7. Punctures
SPF does not have as high of resistance to punctures or damage. An SPF roof has a top layer of silicone; in the event of severe weather, there is a chance for the roof to suffer from a puncture. Usually, this kind of damage can be found with regular inspections before leaking occurs.
Solution: You can contact your contractor for a repair. The repair needs to be made with silicone because conventional roofing repair materials do not adhere to the silicone coating. It’s best to keep up your roof warranty so that it will be covered.
8. Expired Warranty
When you install a new roofing system, it’s best to purchase a warranty. Most manufacturer warranties require the contractor to perform repairs for the first few years after the install.
Solution: With SPF roofing, you can renew your warranty by restoring your roof with a new coat of silicone.
Spray foam: no roofing system is without problems
No roofing system is immune to needing repairs, that’s why it’s important to keep up your warranty and work with contractors that you trust. Spray Polyurethane Foam Roofing Systems are becoming the go-to roofing for commercial, industrial, and manufacturing facilities that are looking for a sustainable, economically efficient option.
Chapter 4: How Much Does a Spray Polyurethane Foam Roof Cost?
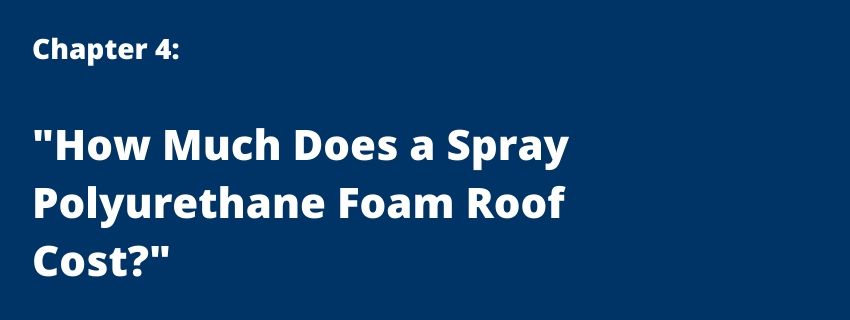
For an average 20,000 sq. foot commercial roof, it will usually cost between $5.00 and $10.00 per square foot in materials and labor to install a typical SPF roofing system. This price range is for an SPF roof of average thickness and building structure.
Other factors that impact cost include:
- The length of warranty. The most popular is a 10-20-year warranty. A 20-year warranty requires a 50% thicker coating application than a 10-year warranty.
- Amount of R-value. SPF has an R-value of 6.5 per inch of thickness. A thicker spray foam application can be installed if you want a high R-value.
- Amount of preparation. No roofing system should be installed over wet insulation. These areas must be identified, removed, replaced, and taken to a landfill. Is this 5% of your roof or 40%? The more wet insulation, the more costly the project will be.
Chapter 5: How Does a Spray Polyurethane Foam Roof Get Installed?
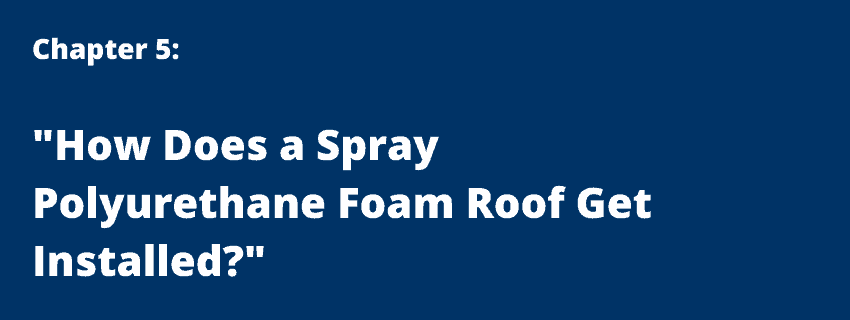
Before a spray foam roof installation can start, the existing roof (or substrate) needs to be prepared. Rather than stripping the existing roof, the contractor will most likely prepare the substrate by getting rid of all dirt, dust, and contaminants. This can be done with air pressure, vacuuming, or even just sweeping.
The first layer put down by the contractor is the polyurethane foam. This foam is created by combining two liquids (a polyol/resin and an isocyanate) as it’s sprayed onto the existing roof substrate.
As the liquid is sprayed onto the existing roof, it creates a foam that expands 20 times in size to form a solid, seamless foam surface. When the foam has expanded, this layer can be between 1 and 1.5 inches in thickness.
Since the polyurethane foam adheres to most common surfaces, it can be installed on any roof slope.
When the SPF layer has been completed, it is then coated with a layer(s) of elastomeric silicone or acrylic coating with embedded granules. This layer is generally between 20 and 30 mils (a mil is a thousandth of an inch — .001 inch.) in thickness. The coating protects the roof and SPF from UV light, weather, normal wear and provides the required fire ratings.
When the installation is complete, it will create a seamless, durable, moisture-resistant renewable foam roof covering.
Chapter 6: Spray Polyurethane Foam vs Built-Up Roofing?
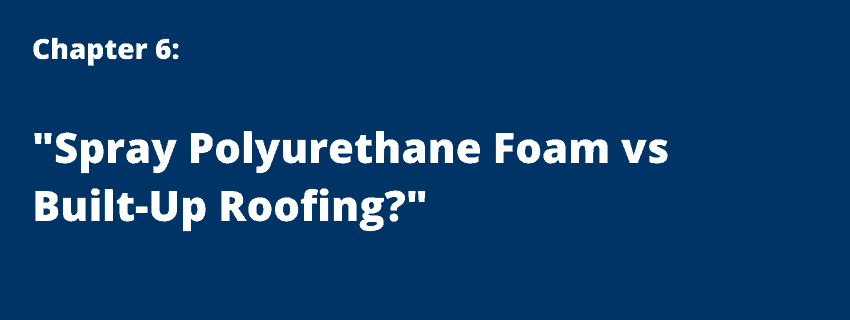
SPF Vs. Built-Up Roofing: Which Is Best For A Flat Roof?
When you think of a commercial roof, you may think of black tar being mopped on a flat roof. But nowadays you have more options to meet your pricing and performance needs.
What is the difference between “traditional” built-up roofing and Spray Polyurethane Foam Roofing?
Let’s dive into the differences between built-up and SPF roofing systems to give you all the information you need in choosing which roof is the best fit for your facility.
SPF Vs. Built-Up Roofing: The Basics
Built-Up Roofing
Built-Up Roofing Systems have been in use in the U.S. for over 100 years. These roof systems are commonly referred to as “tar and gravel” roofs. Built-up systems are installed by alternating layers of asphalt or tar and supporting fabrics directly onto the roof. You can choose the number of layers (or plies) that are installed. The final layer of a built-up roofing system consists of stone or gravel.
Spray Polyurethane Foam (SPF) Roofing
Spray Polyurethane Foam is a liquid that is sprayed on the existing roof and expands into a foam, creating a solid layer across an existing roof.
While SPF roofing is not the most known type of roofing material, the technology has been around since the early 1960s for industrial, commercial, and residential facilities.
SPF Vs. Built-Up Roofing: Cost
Built-Up Roofing
For an average commercial roof, it will usually cost between $7 – $12 per square foot in materials and labor to install a typical built-up roofing system. This price range can change depending on the materials you choose.
SPF Roofing
For an average 20,000 sq. foot commercial roof, it will usually cost between $5.00 and $10.00 per square foot in materials and labor to install a typical SPF roofing system. This price range is for an SPF roof of average thickness and building structure.
SPF Vs. Built-Up Roofing: Installation
Built-Up Roofing
The first layer can adhere directly to the roof substrate. If needed, a base sheet can be fastened to the roof to create a flat and safe workspace. A built-up roofing system is installed by alternating layers of bitumen and reinforced fabric. Property managers can choose three, four, or five-ply roofs to meet their needs and budgets.
The last layer is rock or stone, this layer protects the underlying layers from UV rays, extreme heat or cold, and wind damage. A layer of gravel can be added to be more aesthetically appealing.
SPF Roofing
Before the installation can start, the existing roof needs to be prepared. Rather than stripping the existing roof, the contractor will most likely prepare the substrate by getting rid of all dirt, dust, and contaminants.
The first layer put down by the contractor is the polyurethane foam. This foam is created by combining two liquids as it’s sprayed onto the existing roof substrate. As the liquid is sprayed onto the existing roof, it expands to form a solid foam surface.
When the SPF layer has been completed, it is then coated with a layer(s) of elastomeric silicone or acrylic coating with embedded granules.
SPF Vs. Built-Up Roofing: Advantages
Built-Up Roofing
If properly installed and maintained, a commercial built-up roof can last 40 years. There are a few other benefits of built-up roofing systems:
- Seamless and Waterproof – The continuous solid surface does not require joints or seams, removing the most vulnerable area for leaking.
- Reflects UV Rays – provides ultra-violet protection.
- Low- maintenance – Minimal upkeep needed after installation.
SPF Roofing
When properly installed and maintained, a commercial SPF roof can last 50 years. There are quite a few other benefits of SPF roofing systems:
- Energy Efficient – SPF delivers thermal, air, and moisture barriers to provide the highest R-value per inch.
- Durable – The foam material can expand and contract with the building, decreasing the likelihood of cracks and splitting.
- Seamless and Waterproof – The continuous solid surface does not require joints or seams, removing the most vulnerable area for leaking.
- Environmentally Friendly – In most cases, there is minimal stripping of the original roof – eliminating the need for costly roof tear-offs and waste. The materials that are used for SPF roofing systems are also environmentally friendly: Zero Ozone Depleting Potential (ODP), Low in the Emission of Volatile Organic Compounds VOCs), Free from Chlorofluorocarbons (CFCs), Ultra-Low Global Warming Potential (GWP).
SPF Vs. Built-Up Roofing: Disadvantages
Built-Up Roofing
Built-up roofing systems have been around for decades; their longevity can only be obtained if the roof is maintained properly. Here are other disadvantages of built-up roofing systems:
- Time – Slower installation timeframe
- Safety – Hazardous fumes and vapors when installing it
- Weight – Adds extra weight to the building structure
- Costs – Installation costs
SPF Roofing
While the advantages of an SPF roofing system outweigh the disadvantages, there are a few things you should keep in mind. Here are the disadvantages of SPF roofing systems:
- Hire the Right Professional – The contractor needs to be precise with the application and have a solid understanding of its chemicals.
- Limited Installation Window – Installation of an SPF roofing system cannot be performed during cold, windy, or rainy weather.
- Overspray Potential – Since the SPF is installed by a spray application, there is a risk of the wind carrying overspray onto surrounding cars and other surfaces.
- Maintenance – SPF roofing systems need to be inspected twice a year at least.
Chapter 7: Spray Polyurethane Foam vs Single-Ply Membrane
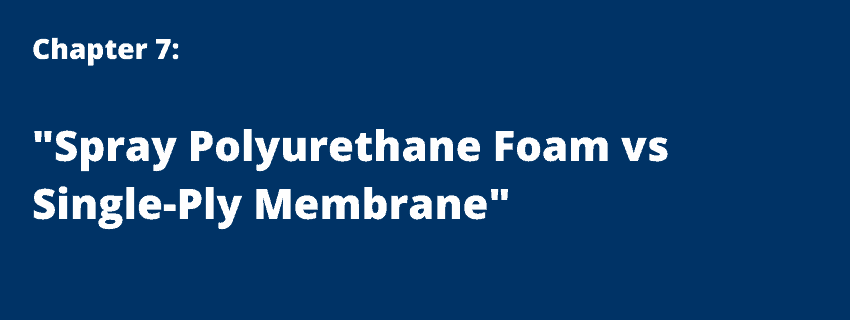
Single-Ply Membrane Vs Spray Polyurethane Foam: Which Is Best For Commercial Flat Roofs?
When we meet with future clients, they’re usually comparing several types of roofing systems. We are always asked: Which is better? Which is more affordable? Which is best for long-lasting protection?
Let’s explore the differences between the single-ply membrane and SPF roofing systems to give you all the information you need in choosing the best roof for your facility.
The Basics
Single-Ply Membrane Roofing
Single-Ply Membranes are sheets of rubber and other synthetics that can be chemically adhered to insulation or ballasted creating a layer of protection on your commercial facility.
There are two main types of single-ply membrane commercial roofing: Thermoplastic Polyolefin (TPO) and Ethylene Propylene Diene Terpolymer (EPDM). They differ in their chemical makeup, how they are installed, and their energy efficiencies.
Spray Polyurethane Foam (SPF) Roofing
Spray Polyurethane Foam, more commonly referred to as SPF, is a material that’s sprayed and expands into a foam, creating a solid layer across an existing roof.
While SPF roofing is not the most known type of roofing material, the technology has been around since the early 1960s for industrial, commercial, and residential facilities.
Cost
Single-Ply Membrane Roofing
For an average 20,000 sq. foot commercial roof, it will usually cost between $5 to $10 per square foot for EPDM and $5 to $10 per square foot for TPO, including materials and labor warranty.
Spray Polyurethane Foam (SPF) Roofing
For an average 20,000 sq. foot commercial roof, it will usually cost between $5.00 and $10.00 per square foot in materials and labor to install a typical SPF roofing system.
This price range is for an SPF roof of average thickness and building structure.
Installation
Single-Ply Membrane Roofing
The beginning of the installation process is similar between TPO and EPDM single-ply membrane roofing systems.
After the existing substrate is prepared, either by cleaning or removing the existing roof, the insulation is installed. There are a few types of insulation options the facility manager/owner can choose from Polyisocyanurate (Polyiso), Expanded Polystyrene (EPS), Extruded Polystyrene (XPS)
After the existing substrate is prepared, either by cleaning or removing the existing roof, the insulation layers are installed and covered by a cover board. There are three ways to attach the membrane to the cover board: ballasted, with an adhesive, or mechanically fastened.
The significant difference between TPO and EPDM comes when it is time to adhere the membrane seams together. TPO uses a hot-air gun to melt down the membrane at the seams and fuse them. EPDM is joined together with seam tape.
Spray Polyurethane Foam (SPF) Roofing
Before the installation can start, the existing roof needs to be prepared. Rather than stripping the existing roof, the contractor will most likely prepare the substrate by getting rid of all dirt, dust, and contaminants.
The first layer put down by the contractor is the polyurethane foam. This foam is created by combining two liquids as it’s sprayed onto the existing roof substrate. As the liquid is sprayed onto the existing roof, it expands to form a solid foam surface.
When the SPF layer has been completed, it is then coated with a layer(s) of elastomeric silicone or acrylic coating with embedded granules.
Advantages
Single-Ply Membrane Roofing
If properly installed and maintained, a commercial single-ply membrane roof can last 30 years. There are quite a few other benefits of single-ply membrane roofing systems:
- Proven Track Record – EPDM roofing has been used for commercial flat roofing for over 60 years. This amount of time on the market has allowed various laboratory and field studies to be performed and tracked.
- Customer Choice of Insulation – Since single-ply membrane roofing does not include the insulation factor, as a customer you have more options to choose from to insulate your facility’s roof.
- Class A Fire-Rated – TPO membranes and EPDM can achieve Underwriters Laboratories (UL) Class A fire resistance listings by adding fire retardant chemicals during the manufacturing process.
- Reflective or Retentive – TPO is generally white and highly reflective. On the other side of the spectrum, EPDM is often described as “Black Roofs,” due to the natural dark color of the membrane.
Spray Polyurethane Foam (SPF) Roofing
If properly installed and maintained, a commercial SPF roof can last 50 years. There are quite a few other benefits of SPF roofing systems:
- Energy Efficient – SPF delivers thermal, air, and moisture barriers to provide the highest R-value per inch.
- Durable – The foam material can expand and contract with the building, decreasing the likelihood of cracks and splitting.
- Seamless and Waterproof – The continuous solid surface does not require joints or seams, removing the most vulnerable area for leaking.
- Environmentally Friendly – In most cases, there is minimal stripping of the original roof – eliminating the need for costly roof tear-offs and waste.
Disadvantages
Single-Ply Membrane Roofing
While the advantages of a single-ply membrane roofing system outweigh the disadvantages, there are a few things you should keep in mind. Here are the disadvantages of single-ply membrane roofing systems:
- Durability – Single-ply membrane roofing does not have a hard top layer to protect the synthetic rubber from dropped tools, gravel, or loose screws from being pushed into the rubber membrane.
- Seams – Although these seams are sealed either mechanically or with melting adhesives, they are still areas that are more vulnerable to leaks than other roofing systems.
- Roofing Accessories – Penetrations such as skylights or vents need special attention during installation.
- UV Rays – UV rays that shine directly on the roof can degrade the adhesives quickly over time.
Spray Polyurethane Foam (SPF) Roofing
While the advantages of an SPF roofing system outweigh the disadvantages, there are a few things you should keep in mind. Here are the disadvantages of SPF roofing systems:
- Hire the Right Professional – The contractor needs to be precise with the application and have a solid understanding of its chemicals.
- Limited Installation Window – Installation of an SPF roofing system cannot be performed during cold, windy, or rainy weather.
- Overspray Potential – Since the SPF is installed by a spray application, there is a risk of the wind carrying overspray onto surrounding cars and other surfaces.
- Limited Colors – The silicone coating that is applied to the foam comes in two colors: white and gray.
- Maintenance – SPF roofing systems need to be inspected twice a year at least.
As you can see, both Single-Ply Membrane and SPF Roofing Systems have their benefits and drawbacks. Choosing which one is best comes down to a customer-by-customer basis.
Chapter 8: Spray Polyurethane Foam vs Silicone Restoration Membrane
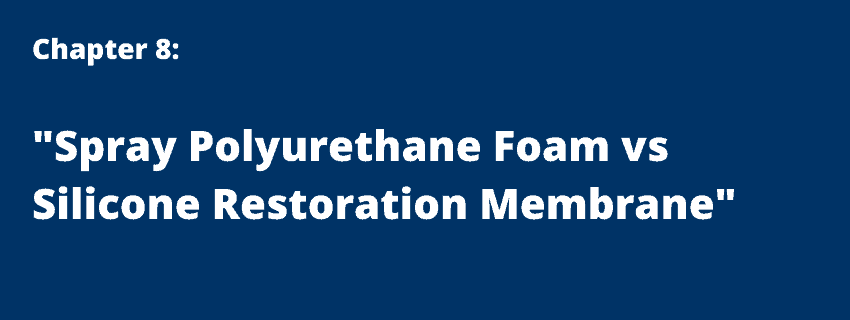
Which roofing option is better for your building?
The best answer will always come after a roof assessment. But other factors matter too, such as:
- Which roofing option provides a better opportunity for energy savings?
- Which roofing option provides waterproofing?
- Which roofing option is more cost-effective?
- Which roofing option is easier to maintain?
- Overall, which roofing option is better?
Let’s get started…
SRM vs SPF – Which roofing option provides a better opportunity for energy savings?
SRM
One reason building owners transition from a rubber roof (TPO or EPDM) and choose a Silicone Restoration Membrane roofing option, do so because of the gray/white color of the coating.
With rubber being dark, it absorbs the sunlight’s rays and is always so dang hot! In an SRM roofing job this year, we noticed a temperature of 192 degrees (F) on rubber and 142 degrees (F) on the SRM area ten feet over.
Using white silicone coating can decrease your building’s energy use by 15 to 35%.
SPF
Spray polyurethane foam provides the greatest R-value of any roofing solution. R-value is the capacity of an insulating material to resist heat flow, thus keeping the cool/heat from escaping your building.
Industry standards suggest that a spray foam roof can pay for itself with energy savings in 5-7 years.
That number can go up or down depending on the condition of your current roof.
EDGE = SPF
SRM vs SPF – Which roofing option provides waterproofing?
SRM
A silicone restoration membrane is spray or rolled over an existing roofing system. It’s smooth and covers all seams and holes from a previous system. Therefore, since SRMs are monolithic (just on the top layer though), they are considered waterproof.
SPF
Spray polyurethane foam is sprayed as a monolithic layer over an existing system. SPF will also, cover all seams and holes from a previous roofing system. SPF is closed-cell and therefore impenetrable by water.
EDGE = SPF
SRM vs SPF – Which roofing option is more cost-effective?
SRM
An SRM involves fewer materials than an SPF. An SRM is also less labor-intensive. The process of how an SRM roofing system gets done is:
- Identify wet areas
- Make repairs
- Power wash the entire roof
- Reinforce seams
- Lay down silicone
Overall, a ballpark price for an SRM roofing solution is $3-$7 per square foot.
SPF
An SPF involves all the steps the SRM does, except you might have to lay down the cover board so the foam adheres properly. Then you need to add in the cost of the materials and processes to create and distribute the actual foam.
Overall, a ballpark price for a spray foam roofing system is $5-$10 per square foot.
SRM vs SPF – Which roofing option is easier to maintain?
SRM
Maintenance on an SRM system is quite minimal. Since the SRM is restoring and strengthening the existing membrane, you may have penetrations that vibrate and pull apart, but it’s highly unlikely.
SPF
More maintenance issues can happen on a spray foam roof, such as:
- HVAC contractors who aren’t careful (jabbing panels) can penetrate the foam
- Other workers dropping screws and stepping on them, breaking the foams membrane
- Animal damage can occur. Raccoons can dig holes, birds can peck at the foam.
Although more issues can happen on a spray foam roof, repairing these problems is very simple. It usually includes a knife, cleaning/drying, applying sealant, and smoothing.
EDGE = SRM
Overall, which roofing option is better?
According to Greg “Barney” Haas, a 30+ year veteran in the roofing industry, Spray Polyurethane Foam is a better roofing option.
The #1 reason is that on an SRM, you’re relying on the underlying insulation. Also, the boards you have underneath the SRM are not monolithic, so if it’s not done correctly, you could be losing R-value.
You’re getting more R-value with spray foam because you have a 1.5”, pure monolithic, closed-cell, and waterproof layer.
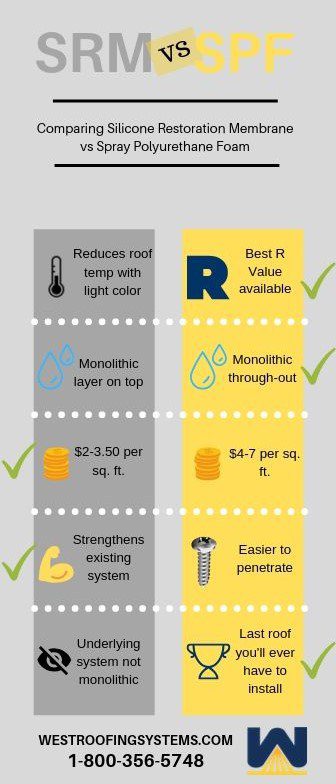
Chapter 9: How Long Will a Spray Polyurethane Foam Roof Last?
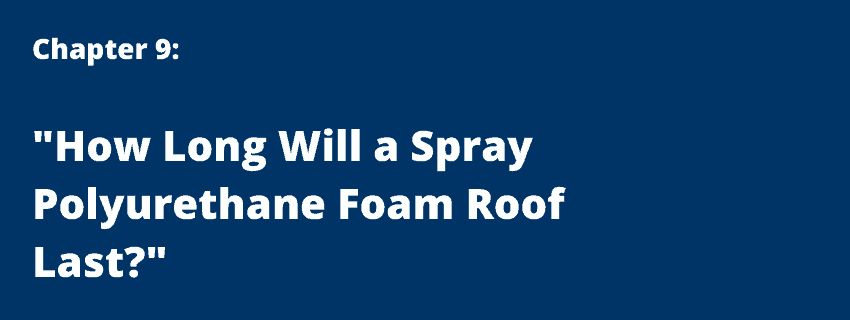
One of the first questions we get asked by property managers is, “How long will a spray foam roof last?”
The answer is that a spray foam roof will last indefinitely if you keep up with the maintenance and recoat schedule.
We have proof. One of the first spray foam roofs we ever did was at Playhouse Square in Cleveland, OH in 1972.
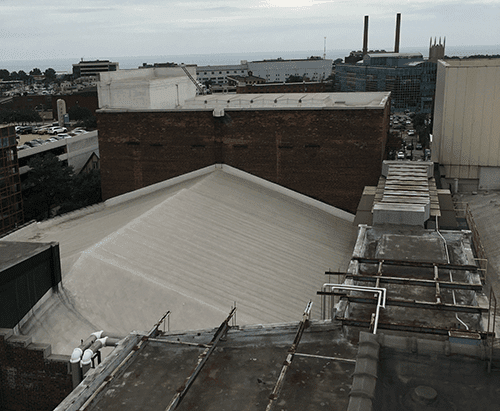
Spray foam was installed at Playhouse Square’s State Theatre Auditorium Roof in Cleveland, OH 47 years ago and it’s still performing as it did year #1.
How Does Spray Foam Last Indefinitely?
So, when we install a spray foam roof, they can come in a 10, 15- or 20-year warranty.
For example, when you get a 10-year warranty, you’ll get 10 years’ worth of silicone coating over top of the spray foam, usually 20 mils thick.
During years 1-10, we came out 2x/year to perform simple maintenance on the roof. This maintenance is recommended but not required to maintain the warranty terms. Tasks performed are:
- Visual roof inspection
- Cleaning of drain, strainers, and gutters
- Cut out any defective areas, make sure they are clean and dry
- Apply caulk/sealant to defective areas and smooth out
- Provide a roof inspection report
But on year 11, when the warranty has run out, the original 20 mils of silicone coating, you might be down to 9 or 10 mils, maybe even less. It depends on where the roof is located, the harshness of the weather that has occurred, and the amount of foot traffic.
In year 11, there’s no need for a roof tear-off. All that needs to be done is to pressure wash the roof, provide simple repairs and install a new coating.
You also have the option of choosing a new 10, 15- or 20-year warranty, whichever works best for you.
What Happens During the Spray Foam Re-coating Process?
Step 1: Pressure wash the roof
Step 2: Walk the roof and fix any mechanical damages, such as blisters, holes, or areas of wet foam
Step 3: Apply the new coating
How Much Does a Re-coat cost?
The average recoat will cost about 1/3 to 1/2 of the original cost of installation in today’s dollars.
The cost can vary depending on the distance from our locations and how much repair needs to be done before the re-coat. Performing preventative maintenance ensures your re-coat will be on the lower end of the re-coat price range.
[table id=2 /]
Spray Foam: the last roof you’ll ever have to put on
In short, a spray foam roof should be the last roof you ever have to put on. After initial installation, it’s basically a maintenance item that can always be under warranty.
Throw in the energy savings of having a spray foam roof, and it instantly becomes a cost-effective option.
Chapter 10: How Is a Spray Foam Roof Repaired or Maintained?
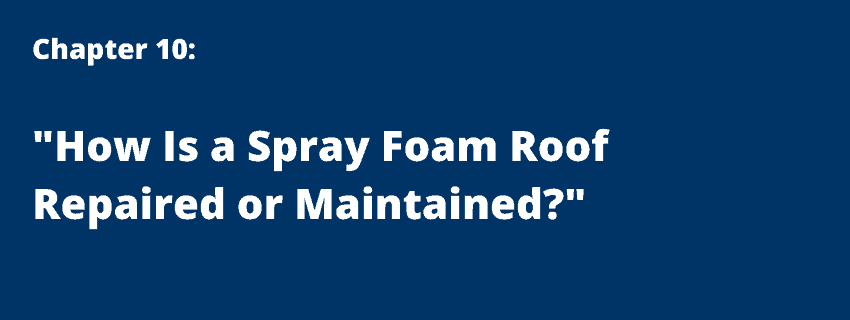
With a spray foam roof, you can simply do a recoat, and/or add sealant to the visible damage and you’re good to go. The level of repair depends on frequency and depth.
Here is a chart from the SPFA on mechanical damage and repair recommendations:
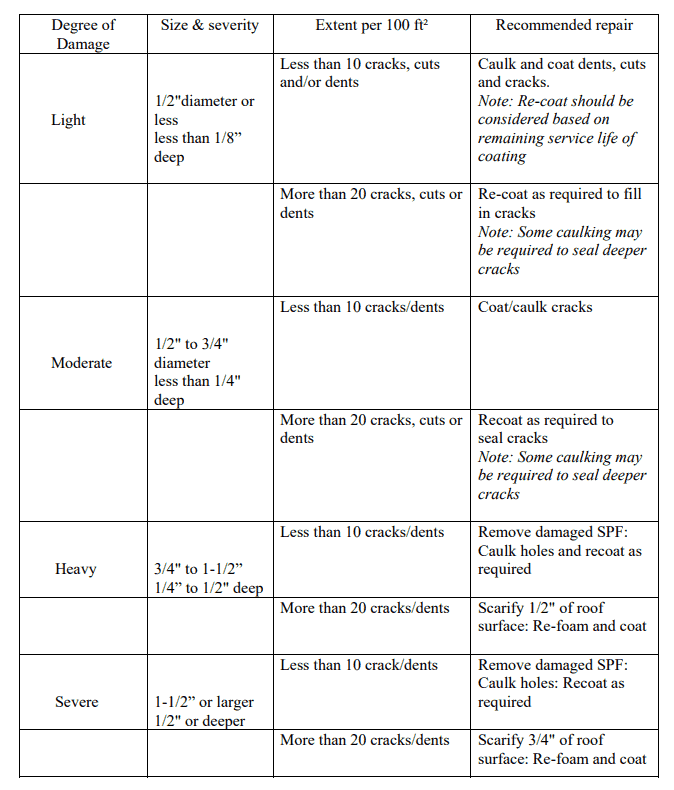
A spray polyurethane foam roof is maintained (usually twice a year) by a:
- Visual roof inspection
- Cleaning of drain, strainers, and gutters
- Cut out any defective areas, make sure they are clean and dry
- Apply caulk/sealant to defective areas and smooth out
- Provide a roof inspection report
After 10 years of routine maintenance, your original 20-30 mils of silicone will probably be reduced to 7-9 mils.
At this point, it’s time to restore your roof with a silicone coating to get you back to the original millage of material.
Once that’s done, it’s back to 10 more years of simple maintenance listed above in the bullet points.
Chapter 11: Common Questions to Ask a Commercial Roofing Contractor
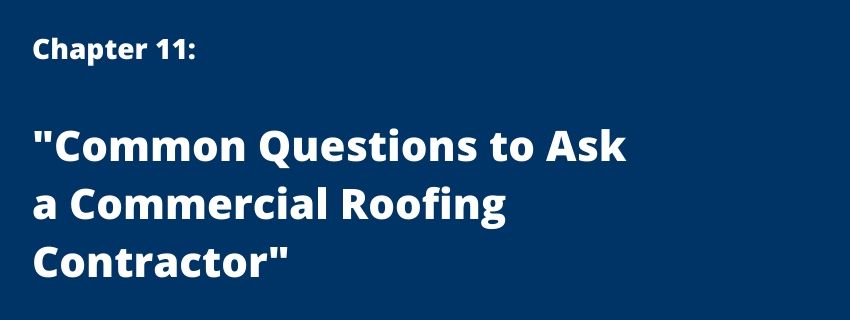
Can I re-roof or do I have to tear off my existing commercial roof?
If you only have one roof on your building that is in good shape, chances are you can save money by installing a new roof without removing the existing roof. Unfortunately, there are instances where a roof tear-off is required:
- Your facility already has two roofs: According to law, commercial buildings may not have more than two roofing layers. This is to prevent excess weight and stress on the structure of the building.
- Your facility has an unsafe roof: If your roof is damaged, saturated, or unstable, your contractor will need to strip the existing roof to install a new working roof.
How do I know if my business needs a new roof?
Our experts will perform a free roof assessment to determine the quality of your existing roof. Internal damage you may spot such as roof leaks or mold, are indicators that your commercial roof could be unstable and need replacing.
When should I schedule my roof survey?
The earlier the better! As soon as warm weather comes, contractors are up on roofing starting projects. It’s best to contact a contractor in The later summer to schedule a survey as soon as the spring comes to your area. That way, they can start your project as soon as roofing season starts.
How much will my new roof cost?
Each situation has its own unique challenges that cause the prices to fluctuate. We compete with all the viable and high-performing commercial roofing systems. Many factors contribute to the price of your new commercial roof. Some of these factors include:
- The size of your roof
- Condition of the existing roof
- Roof access
- Insulation choice
- Membrane choice
- Installation choice
- Roof penetrations
- Type of Warranty
How long can I expect my commercial roof system to last?
The longevity of your commercial is dependent on many factors, from weather conditions to roof type. There are averages for common roof systems:
- Spray Polyurethane Foam: 30 – 50 Years
- Single-Ply Membrane TPO: 15 – 20 Years
- Single-Ply Membrane EPDM: 20 – 25 Years
- Metal: 30 – 45 Years
- Built-Up: 10 – 15 Years
How long does it take to install a new commercial roof?
The time of the project is dependent on a variety of variables such as the type of roof, the size of the roof, existing damage, weather, inspections, and permits. Each job is truly unique and could take from a few days to a few weeks. When you talk to a roofing expert for an assessment, they should be able to include a proposed timeline in the survey report.
How do I know which type of roof is right for my business?
Our roofing experts will work with you to determine the best roofing system for your facility based on climate, energy costs, and facility needs. There are many roofing options for your commercial facility:
- Spray Polyurethane Foam – Read More
- Single-Ply Membrane: TPO – Read More
- Single-Ply Membrane: EPDM – Read More
- Sheet Metal – Read More
- Built-Up (Tar, Asphalt, Modified Bitumen)
- Sustainable (Green, Solar)
How can I choose the right commercial roofing contractor?
Choosing the right commercial roofing contractor to trust can be daunting. There are databases with accredited companies such as the Better Business Bureau or the National Roofing Contractors Association. In addition, ask your contractor what kind of training they do with their crews and what certifications they hold with suppliers and industry organizations.
Is there anything I need to do to maintain my commercial roof warranty?
When you install a new roof on your facility, you will have a variety of warranties to choose from. The coverage of your warranty depends on the type of warranty you purchase. The most common warranty options include Contractor’s Warranty, Manufacturer’s Warranty, and a Manufacturer’s Full System Warranty. These warranties can cover a variety of roofing issues such as:
- Roof leak repair
- High winds
- Hail damage coverage
- Roof puncture coverage
Most roof warranties require or recommend regular roof inspections and maintenance. In addition to a proper maintenance program, Roof Restoration is a great way to renew your roof warranty.
What should I do in the case of an emergency commercial roof leak?
If you find that your commercial roof is leaking, Your priority is to protect what is in your facility first. This could mean moving furniture or covering equipment to protect from water damage. When your property inside the facility is protected, mark the leak area to show a professional later. If your roofing contractor has an emergency contact number, this is the time to utilize their services. If they don’t have emergencies, contact them the next day during business hours.
Chapter 12: Examples of spray foam roofs from the 70s, 80s, and 90s
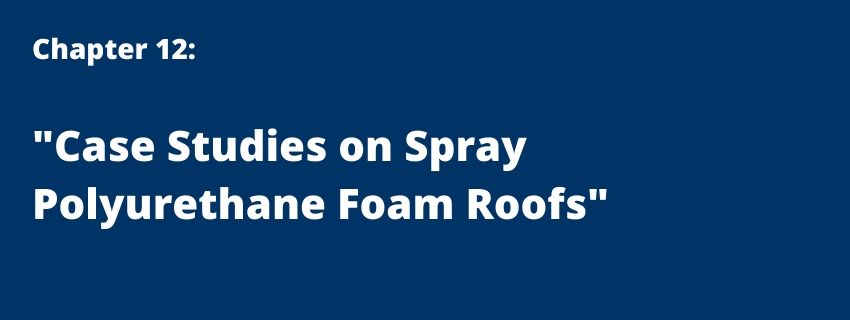
Since the early 1960s, spray polyurethane foam roofs have been installed and re-coated, strengthening the popular phrase “A spray foam roof is the last roof you’ll ever have to install”.
Multiple roofs that have been installed decades ago are going on their 2nd or 3rd recoat.
In fact, our first example, Brian Chavalia (40 years of spray foam experience), was the master sprayer on a job he did 27 years ago. Now he’s going back for a recoat. Check out the video on Central Village below:
Central Village Apartments in Amherst, Ohio
Initially Installed: 1992
Number of recoats: 2
Playhouse Square in Cleveland, Ohio
Initially installed: 1972
Number of recoats: 3
Sandusky Schools in Sandusky, Ohio
Initially installed: 1980
Number of recoats: 3
Chapter 13: How Is a Spray Foam Roof Renewable?
Having a renewable roof gives you an edge over your competitors who do not have a renewable roof.
How?
It has to do with cost.
Here are the costs of spray foam vs single-ply on a 20,000 sq. ft. roof over 30 years:
Cost per sq. ft. | Sq. ft. of roof | Total cost | |
Single-Ply – Year 1 | $3.50 | 20,000 | $70,000 |
Single-Ply – Year 10 | $3.50 | 20,000 | $70,000 |
Single-Ply – Year 20 | $3.50 | 20,000 | $70,000 |
Single-Ply – Year 30 | $3.50 | 20,000 | $70,000 |
$280,000 |
Cost per sq. ft. | Sq. ft. of roof | Total cost | |
Spray foam – Year 1 | $4 | 20,000 | $80,000 |
Spray foam – Year 10 | $2 | 20,000 | $40,000 |
Spray foam – Year 20 | $2 | 20,000 | $40,000 |
Spray foam – Year 30 | $2 | 20,000 | $40,000 |
$200,000 |
Having a renewable roof means that once the warranty period is over (in this example, every 10 years), you don’t have to remove the entire roof and install a new system.
Once 10 years is up on a single-ply roof, you remove everything down to the deck and install a new single-ply system.
On a spray foam roof, there are three parts; the spray foam, the coating, and the granules.
On day 1, the coating will be installed approximately 20 mils thick.
At year 10, that coating will wear down to approximately 7-8 mils thick.
To “renew” a spray foam roof, you power wash the roof clean, install coating back to the original 20 mils, install new granules, and you’re done.
The spray foam never gets touched. Nothing gets removed.
This is why renewing a spray foam roof costs ½ to 1/3 of the original installation cost.
Saving money over the long run helps your business compete. You could lower your prices, give employees a bonus, etc.
Your competitors will use that money to install a new single-ply roof.
And the process will repeat itself every 10 years.
Chapter 14: Can You Install a Spray Foam Roof Over TPO?
Can you install a spray foam roof over a single-ply TPO roof?
The quick answer is No. You cannot apply spray foam over a TPO roof.
However, if you install a cover board over TPO, you can apply spray foam to that cover board.
So, I guess the longer answer is Yes. You can apply spray foam over a TPO roof.
At West Roofing Systems, we’ve installed spray foam roofs over popular single-ply membranes, including TPO, since 1979.
Today we wanted to share some of your TPO roof characteristics, how you can upgrade your roof by installing spray foam over top, and describe to you how the installing process works.
Let’s begin…
First of all, if you’re unaware if you have a TPO roof, we wanted to provide a few indicators.
A TPO roof is:
- Usually white in color
- Comes in sheets that are 10, 12, or 20 feet wide
- Once rolled onto a commercial roof, the seams are welded together using a hot-air gun
Here is an example of the seams being welded together with a hot-air gun:
Here is an example of a TPO roofing section:
Now that you can determine if you have a TPO roof, let’s get into spray foam roofing and how it can be applied over your roof.
Going back to the beginning, you need to install a cover board to apply spray foam to a TPO roof.
What kind of cover board is used when applying spray foam over TPO?
What’s typically used is a half-inch, high-density, wood fiber cover board. (Wow, that’s long. If it’s cool with you, we’ll address this simply as “cover board”? Cool? Cool. Let’s move on…)
The reason you need the cover board is due to the way a TPO roof system is secured to the existing assembly or deck. TPO is typically attached along the seams, so the center is loose. Sort of like a square, where the perimeter is attached to the roof, but the area in the middle is not:
Spraying foam directly over TPO could create an unlevel surface where the TPO is not secured to the deck, which could impact how water travels around the roof.
It’s never a good idea to apply spray foam to a surface that isn’t properly secured.
To ensure spray foam is applied to a level surface, the cover board must be used.
Does the condition of your TPO roof matter when installing spray foam?
Yes.
If your TPO roof has saturation (or is wet) underneath, then you’ll need to remove those areas and replace them with similar material.
A roofing contractor has a few options to determine if your roof has saturation:
Core samples
A core sample allows the roof to reveal itself. After a core is pulled, a roofing contractor will know:
- approximately how old the roof is
- how many layers it has
- and if there’s any saturation
Where to pull these core samples is determined by common indications of saturation, including darker areas on the roof, where water flows along the roof, if water is designed to run into a parapet wall, and many, many other circumstances.
Every roof is different.
A roofing contractor with years and years of experience will know where to pull core samples to get an accurate measure of substrate saturation.
Infrared Survey
An infrared survey can be performed to determine saturation where the naked eye cannot see.
A roofing contractor will come out after dusk, around the time when the roof is beginning to cool. During this time, the roof will be cool, but the water underneath will still be warm from the day’s sun.
The infrared survey will identify those warmer areas, which is an indication that water is present.
A roofing contractor will mark those areas with spray paint to highlight the saturated areas of the roof that need to be removed.
During the quote phase, a roofing contractor will usually put a separate cost for the removal of saturated areas. It will look something like this:
Cost of spray foam roof = $4 per square foot x 20,000 sq. ft. = $80,000
The cost of removal of saturated areas will add $2/sq. ft. to the overall cost.
***This is a very basic quote with estimated pricing***
The 5 steps to install spray foam over your TPO roof
Before we go through the steps, here’s a start to finish video of a spray foam installation (sorry it’s not TPO though):
Back to a TPO installation:
STEP 1 – PERFORM ROOF INSPECTION
A roofing contractor will walk the roof, take cores and determine how many layers the roof has. If there are already two layers, then your TPO roof will need to be removed before installing a spray foam roof.
Building codes state that a commercial roof can have a maximum of two layers. For the sake of complexity, let’s say your roof only has 1 layer and there’s little saturation.
STEP 2 – PREPARE THE ROOF
If you’re putting spray foam over TPO, the roof doesn’t have to be super clean due to installing a clean cover board over the top of the TPO.
A roofing contractor will remove all debris and loose particles from the roof using a broom or with pressurized air.
STEP 3 – INSTALL COVER BOARD
The cover board will be mechanically fastened to your TPO roof. Mechanically-fastened means using stress plates and screws to keep the cover board in place.
STEP 4 – APPLY SPRAY FOAM ROOF
Spray foam will usually be applied with an average of 1.5” in thickness.
Thickness can be increased or decreased depending on the R-value the building owner desires.
Spray foam can be 2” in the middle of your roof and 1” at the edges. Every roof is different, but the goal is to provide a fully customized route for water to exit your roof.
Next, a base coat of silicone coating will be sprayed or rolled over the foam the same day the foam was applied. This is to prevent one of the few weaknesses of spray foam; its inability to resist UV rays.
The following day, a topcoat of silicone coating with embedded granules will be applied to the roof.
STEP 5 – WARRANTY
The building owner has a choice between a manufacturer’s warranty or a roofing contractor’s warranty.
The duration of the warranty is directly correlated with the thickness of the silicone coating that’s applied:
10-year warranty = 20 mils of coating
15-year warranty = 25 mils of coating
20-year warranty = 30 mils of coating
Chapter 15: Can Spray Foam Be Installed Over a Commercial Metal Roof?
One of the most common questions our sales team gets is, “Can a spray foam roof be installed over a metal roof?
The most honest answer I can give is…absolutely!
Some building owners don’t realize that spraying over metal is an option.
If you have a roof leak with your metal roof, installing spray foam over top can close all those leaks and provide you with more R-value.
In fact, spray foam has a 100% chemical adhesion across the entire metal roof. Spray polyurethane foam will mirror what the existing metal roof is.
What can spray foam do for a metal roof?
The first benefit is that spray foam can close all those little holes that produce leaks.
The second benefit is that spray foam increases your roof’s R-value, or its ability to keep heat in during the winter, and cool in during the summer, which will save you money on your energy bill.
What condition does the metal have to be in to be ready for foam?
For spray foam to stick to any roofing platform, it must be cleaned and completely dry. For metal roofs, we’ll power wash the roof to get all the contaminants off.
If you don’t get all the contaminants off, the spray foam might have a difficult time adhering properly to your metal roof.
In addition, one difference you’ll encounter when dealing with metal roofs is rust.
Obviously, with installing SPF on a rubber or built-up roof, rust doesn’t factor into the job preparation.
To deal with rust, a roofing contractor will use a rust inhibitor primer, which will stop the oxidation process in rusting metals that have been exposed to oxygen and water.
If this step is skipped, rust will continue to grow on your metal roof, accelerating the rate of decline in your roof’s projected lifetime.
What if my roof has holes, can I still get a spray foam roof?
Yes.
If there are plenty of small holes (pinhole size), a roofing contractor can spray foam right over the top of them. If you have larger holes, a piece of metal will be laid and connected over that area. Of course, any holes that present a structural or safety issue need to be corrected before any re-roofing.
We’ve encountered holes the size of school buses on some roofs!
What if my metal roof is currently leaking?
Most of the time, a roof leak is the #1 reason a roofing contractor is called. A spray polyurethane roof can be installed over a leaking metal roof. Since spray foam is monolithic and closed-cell, it will create a watertight barrier over the entire metal roof.
Most of the time, extreme heat shifts cause that leak. Your metal roof expands when it’s hot and contracts when it’s cold.
Over time, the grommets underneath the fasteners will wear out, exposing a small hole in the metal roof.
Will spray foam restrict the thermal movement of the metal panels?
Yes, but it’s no cause for concern.
If you’re unaware, metal panels expand and contract with the weather changes.
Spray foam tends to put the metal roof to sleep so it doesn’t see the extreme heat and cold cycles.
Most of the time, the “shifting” is what causes fasteners and grommets to move, crack/break, and therefore create an opportunity for water to enter the building.
Chapter 16: 4 Factors That Influence Life Time Cost of a Roofing System
Learn about 4 factors that influence the lifetime cost of a roofing system:
1. What are the approximate initial costs of different roofing systems?
Here are the most popular commercial roofing systems and their approximate price per square foot:
- Spray polyurethane foam – $5-$10
- Metal – $10-$15
- TPO – $5 – $10
- EPDM – $5 – $10
NOTE: these prices are ballpark, meaning MANY variables can shift the price to either side of the range.
What variables can influence a commercial roofing price?
Roof Attachment – What kind of decking does your building have? Say you have a concrete deck. To install a single-ply system, you’ll need to fasten your insulation and single-ply sheets to that concrete deck, which is expensive and difficult to do. On the other hand, a spray foam roof can be sprayed directly over the concrete and eliminate all the labor and difficulty with fastening.
Location – A roofing contractor that does metal roofing (most expensive) might be cheaper than an EPDM roof (cheapest) if the metal roofing company is 2 miles from your facility and the EPDM roofer is 150 miles away.
Penetrations – if you have a roof with only a few penetrations, a roofing system that can be installed with rolled-out material will have minimal interruption, which reduces labor costs. A roof with pipes, drains, HVAC units, exhausts, and other penetrations make the labor difficult for rolled roofs since the sheets will need to be custom cut. A spray foam roof can be sprayed around penetrations, which reduces the time the project takes.
Worker skill – a roofing contractor that’s brand new will have newer roofers which have lower labor costs. A roofing contractor that’s been in the game for 40 years, will most likely have installers with 10, 20, or 30 years of experience. These roofers get paid more, but their performance makes up for it. On your 20,000 sq. ft. roof that you’ll spend $100K on, it’s beneficial to the long-term performance of the roof if it’s installed by experienced roofers.
These are just a few variables that can impact price.
Word of advice: Don’t worry about the ballpark costs with each system. With all the other variables involved, your best option is to get a few quotes from contractors doing different roofing systems, and then weigh all the pros and cons each roofing system provides.
One way a roofing system can provide value over other systems is through its R-value.
2. What’s the R-Value of different roofing systems?
If you’re unfamiliar with R-value, it’s a material’s ability to resist thermal movement through it. The higher the R-value, the more insulation that material provides.
Stronger insulation reduces the amount of heat/cool that escapes through your building’s roof, therefore lowering your energy bills.
Here are the R-values of the most popular commercial roofing systems:
- Spray Polyurethane Foam: 6.6 per inch of thickness
- Metal: 0.00 per inch of thickness
- TPO: 0.24 per inch of thickness
- EPDM: 0.33 per inch of thickness
- BUR Gravel: 0.34 per inch of thickness
- BUR Smooth: 0.24 per inch of thickness
- XPS Insulation: 5.0 per inch of thickness
- EPS Insulation: 3.85 per inch of thickness
- Polyiso: 5.5 per inch of thickness
A spray foam roof can pay for itself through energy savings in 5-10 years. The amount of time it takes to recoup the investment relies on a few factors, such as:
- How much R-value does your current roofing system have?
- How often do you run your HVAC units?
- How energy efficient are your HVAC units?
If we’re talking about the lifetime cost of a roofing system, in essentially 10 years, a single-ply roof might need to be completely removed and installed with new material.
With a spray foam roof recouping its cost over 10 years, the lifetime cost is zero.
But what happens after year 10?
3. What’s the renewability of different roofing systems?
After year 10, 15, or 20 (however long your roof warranty is), what happens next?
On most roofing systems, you need to remove them completely, transport all the materials to a landfill, and then re-install the system from scratch.
One roofing system that stands out is spray foam.
The reason is that it’s a renewable roofing system.
How?
The initial application is usually 1.5” – 2” of spray foam, 20-30 mils of silicone coating, which is either rolled or spray-applied in two separate coats, and then granules are embedded into the top coat of coating.
After year 10, the initial 20 mils of coating might be down to 5-8 mils.
To renew the roof, all that needs to be done is to make minor repairs (if any), which is done by cutting around a small hole, drying the area, and filling it with silicone coating or caulk.
Smooth out the area and you’re done.
Once these are done, a roofing contractor will install coating and granules at the original measurements. This process is called a “recoat” and generally costs ½ to 1/3 of the original installation.
A renewable roof system is great, but I’m not living forever. What happens if I want to sell this building one day?
4. How does the current roof system affect resale value?
Whether you’re looking to buy a building or you’re selling one, the current roof condition can greatly affect the value of the building.
Think about it:
Would you want to buy a building that just had the roof re-done last year? Heck yea!
Would you want to buy a building whose roof is 20 years old and currently leaks? Heck no!
If everything else was the same, do you think those two buildings would be the same price?
Absolutely not. An average price for a commercial roof is around $5 per sq. ft. If that roof is 20,000 sq. ft., that’s $100,000.
If an adjuster or building inspector determines the roof has approximately one year of life left, you could expect the value of the building to decrease by around 100K.
This is why it’s important to think about how the roof you install today can help, or hurt you financially down the road.
Would you rather purchase a building that I know I’ll need to completely remove and replace someday, or one that can be renewed over and over again at a fraction of the original installation?
NOTE: Some spray foam contractors allow the warranty to be transferred to the new owner. Bonus selling point!
Chapter 17: A Review of a Spray Foam Roof
Master Bolt’s spray foam installation date: June 14, 2019
Location of Master Bolt & Manufacturing: Elyria, OH
Number of sq. ft. of spray foam installed: About 35,000 in 4 different sections/phases
Greg: Can you give me a background on what Master Bolt’s roof was like and what work got done?
Kenny: Our building was built in the 1930s or 1940s and they kept adding on and adding on.
Every section has a different roof or different configuration on it. West Roofing Systems was able to blend it all in.
I got here about a year and a half ago and the roof was leaking everywhere.
We had tarps in the rafters, 55-gallon drums laying around, the office was leaking, it was just terrible and West Roofing Systems was able to come in and take care of all these issues for us.
So why spray foam? You certainly had a choice to install any roofing system.
Kenny: The guys identified the areas of the roof that had wet insulation, and only removed those wet areas before installing the foam roof. If a core was pulled out and it was dry, that section can be left alone.
SATURATED CORE SAMPLE
NON-SATURATED CORE SAMPLE
Going with a new rubber roof would have required the entire roof to be ripped off.
So, it was three things:
#1 – it’s cost. We wouldn’t have been able to pay for an entire roof replacement.
#2 – spray foam lasts.
#3 – the application is simple.
Video: How is a spray foam roof installed from start to finish?
Did you ever get a quote for a full rubber roof replacement to see what the cost was?
Kenny: No, we did not. We’ve kind of knew Chris West outside of work, and Jeff Johnson and our owner John Gaydosh also know them. We kind of asked them, “What do you guys recommend?” And they are very honest with us.
Obviously, they want the sale, but it wasn’t like that.
They said spray foam is economical, it’s going to last, you can trust us. When you’re doing a large project like that and you’re making a large investment in building maintenance, you want to make sure you trust somebody.
With the relationships we have with those guys, it was a no-brainer.
Have you had any problems with the spray foam roof?
Kenny: Nope. It’s been really, really good, no complaints.
Read more: What Problems Can a Spray Foam Roof Have?
People are skeptical of spray foam because they’ve never heard of it before. Do you have anything you’d like to say that could lower that skepticism?
Kenny: My grandfather was in the roofing business and they only did rubber roofs, he swore by rubber roofs, and I told him what was going on, and he said that this was not the right thing, and I said, “Pops, this is different than what you had in the 1970s.”
I would have no problem talking to anybody, telling them that the application is easy, it’s mess-free, we have not had any issues, and it’s also added R-value to our roof.
And we’ve noticed in the wintertime, we retain heat a lot better.
It seals up any tiny nooks and crannies…and it’s made a believer out of me. Not that I wasn’t a believer in the first place, and I’m not a roofing expert, but it’s been performing great.
SMALL HOLE ON MASTERBOLT’S ROOF
Have you noticed any difference in your energy bills since the roof has been up?
Kenny: We’ve noticed a slight difference in our energy bills and we’re anticipating seeing even more savings this year because we did our roof in sections.
The front section is where the office was, we did that and another large area in the shop, and we have definitely noticed a difference in the Summertime.
We have an older brick building, and the section we just did, it’s 5-10 degrees cooler than it is in the back part of the building. Now there’s some different manufacturing going on but at the same time, you can definitely tell there’s a difference.
In the winter, it’s the same thing. It’s a lot hotter up here because it’s obviously holding the heat better.
SEAMLESS SPRAY FOAM ROOF AT MASTERBOLT
Chapter 18: How Durable is Spray Foam Roofing?
Spray foam has a compression strength of 50-60 PSI.
You can absolutely walk on it.
If you need to frequently service rooftop machinery, walkways can be installed by adding a double broadcast of granules into the topcoat of coating.
Chapter 19: What Are the Installation Requirements to Apply Good Spray Foam?
To apply good foam, it needs to be:
- 50 degrees F and rising
- dry
- not much wind
Although windscreens and spray foam booths can be used to combat windy conditions.
WRAPPING IT ALL UP
Greg: I told Kenny that I wouldn’t use his name or business in this review.
Kenny immediately countered and said that he didn’t mind if anybody wanted to contact him about his experiences with spray foam or West Roofing Systems.
Kenny’s contact information:
Phone: 440-476-6668
Email: ken.vance@masterbolt.com
I wanted to point out the real reason Kenny chose to do a spray foam roof with West Roofing Systems. He trusted what his friends advised was the best option for his specific problem.