As Spray Polyurethane Foam (SPF) becomes more popular for commercial roofing, building owners want to know what problems the system can have.
Here are the 7 problems spray foam roofs have:
- Limited installation windows
- Finding a contractor that knows how to correctly apply the foam
- Overspray potential
- Upfront costs
- Maintenance is recommended
- Impact resistance
- Not performing a recoat
West Roofing Systems has installed all types of roofing since 1979, and none of them are without problems.
And just so you’re aware, we only write articles about true events and experiences. Every piece of content written at West Roofing Systems is produced in-house. Every article is reviewed and edited by a roofer/salesman with more than 30+ years of experience in the field.
Let’s get started!
Here are the problems with spray foam roofing:
1. Limited Installation Window
Spray foam is fluid-applied, which means that the foam needs to be installed in specific weather conditions. The best weather conditions are warm and dry with minimal wind.
If you aren’t aware, here’s a 30-second video of spray foam being installed:
Spray foam can only be installed when it’s 50 degrees or above.
This means that you are at the mercy of Mother Nature to get your roof repaired or installed.
Solution: Contact your contractor before your area’s roofing season, that way you can schedule your installation early, and you have plenty of time to reschedule if the weather changes.
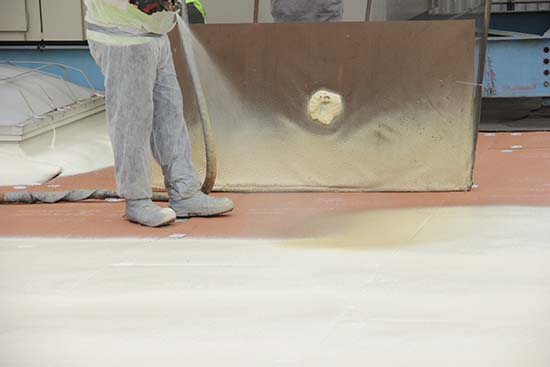
2. Finding the Right Contractor/Applicator Errors
As foam roofing gains popularity with commercial roofing, you want to make sure you find a reputable contractor.
Unlike traditional roofing, installing a spray foam roof requires knowledge of the chemicals and application techniques. Installation requires a high degree of technical expertise and experience.
Solution: Check to see if your potential contractors are certified and take part in industry organizations. The Spray Polyurethane Foam Alliance (SPFA) has an ISO-17024 compliant certification program that has multiple levels and requires the contractor to pass an exam and meet the criteria for certification.
3. Overspray Potential
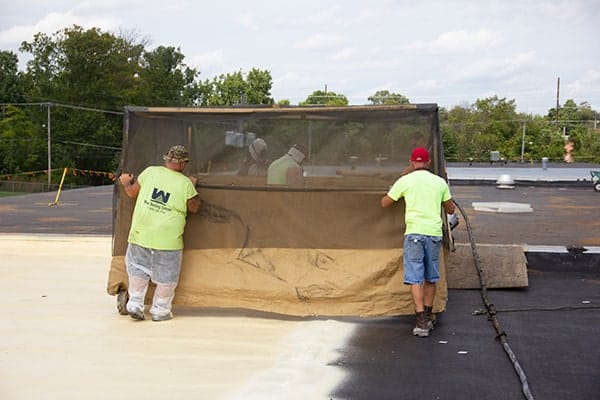
High winds can carry the foam onto cars and other surfaces. While this does not pose a health concern, it is a concern for the surrounding property.
This is what spray foam contractors call “Overspray”.
Solution: There are multiple ways to prevent this from happening. Discuss with your contractor to ensure that they utilize industry best practices to avoid overspray. If it does happen, your contractor should cover cleanup costs.
4. Upfront Costs
The cost of a spray foam roof is usually between $5.00 and $10.00 per square foot. Compared to other flat roofing systems, this upfront cost can be higher.
Here are the costs per square foot of popular commercial roofing systems:
NOTE: There are lots of factors that influence the price of a commercial roofing project.
Solution: A spray foam roof pays for itself quickly with energy savings and roof longevity. You can work with your contractor to calculate potential energy savings to make sure you installed the right thickness of spray foam.
5. Maintenance
Like any roofing system, spray foam roofs should be regularly inspected. Severe weather events can cause damage, such as hail storms, tornadoes, and hurricanes. Punctures and damage should be caught early to make the repair process the easiest..
Solution: Most contractors have maintenance plans and warranties to keep your roofing system in decent shape. West Roofing System’s M.a.R.S. Program offers multiple packages to fit your needs.
6. Punctures
The spray foam used for roofing has a compression strength of 50-60 Pounds per Square Inch (PSI). This is similar to the strength of the pegs your refrigerator sits on.
A spray foam roof has a top layer of silicone; in the event of severe weather, there is a chance for the roof to suffer from a puncture. Usually, this kind of damage can be found with regular inspections before leaking occurs.
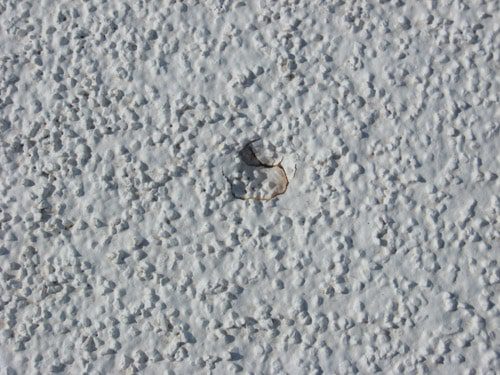
Solution: You can contact your contractor for a repair. The repair needs to be made with silicone because conventional roofing repair materials do not adhere to the silicone coating. It’s best to keep up your roof warranty so that it will be covered.
7. Expired Warranty
When you install a new roofing system, it’s best to purchase a warranty. Most manufacturer warranties require the contractor to perform repairs for the first few years after the installation.
The problem is some building owners don’t renew their warranty and the foam roof begins to degrade.
An elastomeric coating protects the foam roof. It’s usually installed in 20 – 30 mils of thickness.
After the coating wears away (after 10-20 years), a recoat is necessary to keep the foam roof protected from UV rays.
Once a recoat happens, a new 10-20 year warranty is granted.
Solution: With Spray foam roofing, you can renew your warranty by restoring your roof with a new coat of silicone.
What should you do now?
Your next step is to learn about the pros and cons of all commercial roofing systems.
That way, you can make the best decision for your unique roofing situation.
If you’d like to just learn about spray foam roofing, please view the cheat sheet below: