Imagine you’re the building owner of a cold storage facility and you have roofing issues. Say a few leaks here and there.
In every market, competition is fierce, and margins are thin.
But since your building needs to be 40 degrees or lower constantly, you’re paying more to cool your building down than your competition, which has an airtight roofing system.
It’s hard to say exactly how much a cold storage facility can save on their energy bills per year by having an airtight roof vs a roof that leaks, but it has to be significant.
The amount can vary by how large your facility is, how much air leakage your building has, how energy efficient your HVAC units are, etc.
At West Roofing Systems, we’ve been installing and restoring commercial roofing systems since 1979, and in that time, we’ve helped numerous cold storage facilities keep their roofs airtight, lowering their energy bills.
A popular phrase in the spray foam industry is, “A spray foam roof can lower your energy bills enough to pay for the entire roof installation in 5-10 years.”
That’s a strong statement; let’s dive more into this…
What is a spray foam roof?
Spray Polyurethane Foam Roofing, or spray foam roofing, is a roofing system that uses a combination of two chemicals that are sprayed as a liquid so it can expand into a foam, creating a solid layer across an existing roof.
The application of spray foam is to repair and restore an existing roof by removing the saturated areas, replacing with like materials, and then spraying foam over top of the entire roof.
While SPF roofing is not the most known type of roofing material, the technology has been around since the early 1960s for industrial, commercial, and residential facilities. An SPF roofing system can be used in any climate, and when correctly installed and maintained, can last over 50 years.
Here is a video of a spray foam roof installation from start to finish:
Quick fact: Spray polyurethane foam has been around since 1937. In the 1940’s, it was used in aircraft manufacturing for the military. In the 1960’s, spray foam first made its way into commercial usage by…insulating refrigerators.
How does a spray foam roof benefit a cold storage facility?
A spray foam roof has many benefits, but specifically for cold storage facilities, there are three:
- Spray foam has the best R-value of any roofing insulation available
- A spray foam roof is seamless, which eliminates common areas where air leaks
- A spray foam roof is renewable, in 10-20 years you don’t need to tear it off
Spray foam and R-value
The #1 goal of the roof on a cold storage facility is to prevent cold air from escaping the building.
To do this, you need a roofing system that has great R-value, which is the capacity of an insulating material to resist heat flow. The higher the R-value, the greater the insulating power.
Here are the R-values of the most popular commercial roofing systems:
- Spray Polyurethane Foam: 6.6 per inch of thickness
- Metal: 0.00 per inch of thickness
- TPO: 0.24 per inch of thickness
- EPDM: 0.33 per inch of thickness
- BUR Gravel: 0.34 per inch of thickness
- BUR Smooth: 0.24 per inch of thickness
- XPS Insulation: 5.0 per inch of thickness
- EPS Insulation: 3.85 per inch of thickness
- Polyiso: 5.5 per inch of thickness
Other roofing systems can get you the same R-value as a spray foam roof, but they will have to use more material, and they will have to seam together their insulation and/or top roofing layer, which is a big disadvantage.
The disadvantages of a roofing system with seams
Popular roofing systems, such as EPDM, TPO, BUR, and Metal roofs all have some sort of seams where layers are attached together.
The layers overlap each other in order to prevent any leaks.
The problem with seams is that over time, they begin to lose their adhesion.
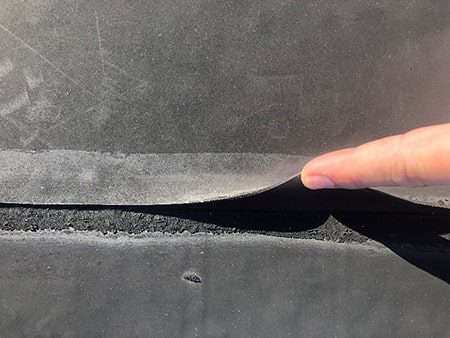
Seams are a common area where leaks occur, so eliminating the seams helps to promote a leak-free environment.
Additionally, by being seamless, thermal bridging (where fasteners and joints of insulation board decrease the actual performance of a roof system’s measured R-value) is eliminated.
A spray foam roofing system has no seams, meaning the entire roofing surface is one layer. All the penetrations are encapsulated and become part of the field of the roofing area.
Here’s a video of spray foam encapsulating a box, making the box part of the monolithic roofing system:
Note: A vapor barrier will be needed for a cold storage facility, no matter what roofing system you install. For a spray foam roof, a butyl rubber is used as a vapor barrier. For single-ply, a Visqueen plastic sheeting is used as a vapor barrier. In either instance, a vapor barrier is always installed on the warmer side of the building.
The advantages of a renewable roofing system
Most cold storage facilities require large setup costs to get started, which means they are planning on being in business for quite some time.
When some roofing systems only last 10 years, that’s a financial burden on the business.
For example, let’s say you install a single-ply roofing system, which on average, lasts around 10 years.
If your roof is 20,000 sq. ft. and each sq. ft. costs $4.00, you’ll need to spend $80,000 every 10 years to have a roof that works well.
A single-ply roofing system is not renewable because you need to remove everything down to the deck and start over each time.
A spray foam roof is renewable.
How?
Spray foam is installed on your roof, but coating and granules are also part of the roofing system.
On a spray foam roof with a 10-year warranty, 20 mils of coating with embedded granules will be installed over your spray foam, which is usually installed 1.5”-2.5” thick.
In year 10, the initial 20 mils of coating may be worn down to 7-8 mils of coating.
This happens by natural causes, such as foot traffic, wind, rain, etc. But the important part is that the foam never loses R-value, thickness, or any other performance measures.
In year 10, what will be performed is a recoat, which will bring your 7-8 mils of coating back to the original 20 mils of thickness. You’ll get a new 10-year warranty, and the process can be repeated over and over again.
This is what’s called a renewable roofing system.
The price of each recoat is ½ to 1/3 of the original installation, which is different than 100% of the original installation costs of a single-ply roofing system.
Great R-value and leak-free
For any cold-storage facility, keeping the cool air from escaping will lower energy costs significantly. But did you know that a spray foam roof is also closed-cell?
Closed-cell means that water cannot pass vertically through the surface.
If your spray foam roof gets a small crack or hole, the water will sit on top and never head south toward your deck.
For other roofing systems, once the water breaks the membrane, it heads south into your insulation, which will eventually get to your deck and cause a leak.
Spray foam roofing on cold storage facilities
If you have any questions about spray foam roofing, please let us know. We’ve been installing these systems for more than 40 years and have come across almost every scenario when it comes to commercial roofing.
Here are a few photos of cold storage facilities that we’ve installed new spray foam roofs on:
1. Fieldale Farms – Baldwin, GA – 118,000 sq. ft. over existing Gravel Built-Up Roof
Finished spray foam roof at Fieldale Farms:
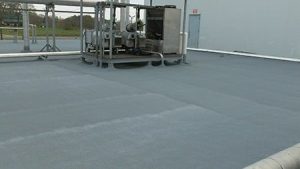
Finished spray foam roof at Fieldale Farms:
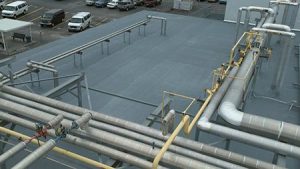
2. Michael A. Ries Ice Rink – Parma, OH – 45,000 sq. ft. over existing Gravel Built-Up Roof
Spray foam installation on Michael A. Ries Ice Rink:
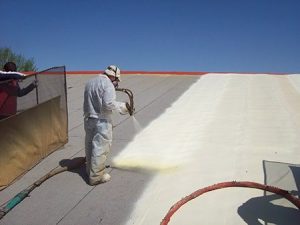
Completed spray foam roof on Michael A. Ries Ice Rink:
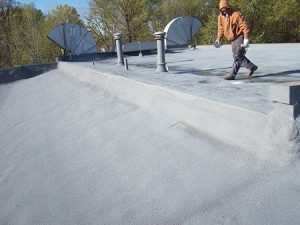
If you’d like to learn more about spray foam, please view our Spray Foam Cheat Sheet which answers popular questions, such as:
- How much does a spray foam roof cost?
- What problems do spray foam roofs have?
- What are the pros and cons of a spray foam roof?