The best roof for a school lasts a long time, is energy-efficient, requires minimal maintenance, and doesn’t cost a lot.
Another bonus is looking at lifetime costs. Since schools last a very long time, how much is this roof going to cost me over 20 years, 50 years, etc.?
Sometimes going with the cheaper option today isn’t financially beneficial long-term.
Did you know that an average-sized high school in the US spends around $74,390 per year on heating and cooling costs?
What if your roof system could reduce that cost by 15-30%? If you assume a 22% savings, that’s $16,366 per year.
HINT: A spray foam roof can reduce energy costs by 15-30%. There are lots of variables, such as HVAC efficiency and the current condition of the roof. We dive more into this at the end of the article.
Today, you’ll learn:
- How long does each commercial roofing system last?
- How does each roof system become energy-efficient?
- What maintenance is required for each roof system?
- How much does each roof system cost?
- What is the lifetime cost for each roofing system?
- What is Co-op purchasing and how does it benefit schools?
- What are some case studies of school roofing projects?
Just so you’re aware, West Roofing Systems has been installing, maintaining, and repairing roofs over schools since 1979. Some of our current owners installed these roofs themselves in the 1980s!
Every piece of content written is reviewed by a commercial roofing expert with more than 30 years of experience.
Let’s get started.
How long does each commercial roofing system last?
Schools last a long time. Therefore, a roof that lasts the longest would be the best. Here are the most common commercial roofing systems and their life expectancy:
- Single-ply (TPO and EPDM) – 20-30 years
- Metal – 40-70 years
- Spray polyurethane foam – 20-30 years (but they are renewable, so it could last much longer)
One thing to remember is the quality of the installation. If the fasteners on a metal roof back out after 1 month, the roof will leak. If a spray foam roofing contractor doesn’t understand the science of applying good spray foam, the roof won’t last.
How does each roof system become energy-efficient?
Schools are large and always have lots of people in them. To keep everyone comfortable, the heat or air conditioning is always on. This results in high energy bills.
To reduce energy bills, insulation is installed to reduce the amount of air that escapes through the roof.
On metal roofs and single-ply roofs, what’s usually installed is a type of board (polyiso, fiberglass, etc.).
These boards are fastened to the deck before the metal or single-ply membrane is installed. Since metal and single-ply sheets are flat, the roof’s slope is created by installing different thickness levels of insulation.
On a spray foam roof, the spray polyurethane foam is an insulation and a roof membrane. There are no fasteners or screws on a spray foam roof.
This is beneficial because you can easily customize the slope of the roof by spraying more or less foam. Also, since there are no fasteners, there are no thermal shorts. Thermal shorts occur when heat/cool can exit where the fasteners are.
Since schools are always running HVAC units to keep many people comfortable, R-value should be one of the most important factors when considering a new roof.
What maintenance is required for each roof system?
Every roofing system needs routine maintenance. Drains need to be cleared, debris needs removed, and you need someone to notice signs of failure.
Maybe the rubber sheets around a flashing are coming apart?
Maybe the storm last month created a tiny hole in the roof?
Minor repairs can turn into major repairs if ignored.
Now that we know that routine maintenance is unavoidable, how does each roof system get maintained?
Metal
On metal roofs, you need to keep a close eye on the fasteners. These can back out or get damaged. When this happens, water has a clear path into your building.
The seams also need a close eye on them. Seams are where one metal panel is connected to another. These can loosen or become damaged over time due to the roof expanding and contracting with weather fluctuations.
Single-Ply
Maintenance on a single-ply roof is similar to a metal roof. You need to watch the fasteners and the seams.
If there are HVAC units, pipes, or anything that sticks out of the roof, pay close attention. Rubber sheets need to be custom cut to fit around these penetrations. Penetrations are where most leaks occur.
A problem with single-ply roofs is that if water does get under the membrane and reaches the insulation, water can travel through it, making more of the insulation wet.
This is similar to an eyedropper dropping water into the corner of a paper towel. While water is only entering through a tiny hole, eventually the entire paper towel is soaked.
A small water entry point can turn into a large area of the roof needing to be removed and replaced.
Spray foam
If a hole, crack, or puncture happens on a spray foam roof, water will sit in that hole and not move. This is because spray foam has closed-cell properties. The water has nowhere to go and will not travel and further saturate the roof.
A spray foam contractor will simply dry out the hole with a towel, cut around the area, and install caulk or coating. Smooth out the area and you’re done.
While you still need to check on the penetrations, there most likely won’t be any water entry points because spray foam is fluid-applied. There is no “custom-cutting”. Spray foam makes the penetration part of the roofing system.
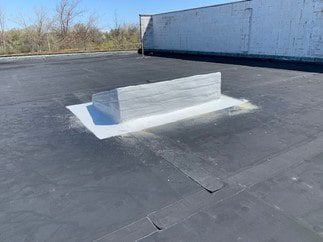
There are no seams on a spray foam roof. This is one advantage of the spray foam system as seams are where most leaks occur.
How much does each roof system cost?
Since schools have budgets allocated towards the roof, it’s important to know how much they cost. Here are the basic costs for each roof system:
- Single-ply – $10-$12 per square foot
- Metal – $12 per square foot
- Spray foam – $10-$12 per square foot
NOTE: As of April 2022, prices for materials have increased since last year. All roofing systems are more expensive due to material and labor shortages, as well as supply chain issues.
While it’s hard to predict the cost of each roofing system, some factors will influence the cost, such as:
Factor #1 – the size of the roof
There are setup and overhead charges no matter what size a roof it is. The larger the roof, the lower per square foot the cost is going to be.
Variable #2 – the amount of tear-off
A roof with 5% wet insulation requires far less labor than the same roof that’s 20% saturated. It’s also going to require fewer materials when replacing those areas.
Variable #3 – distance from the roofing contractor
Gas to get to your location and possible hotel stays factor into the cost of a roofing project.
The further away you are from the roofing contractor, the more expensive the project is going to cost.
What is the lifetime cost for each roofing system?
Most schools just look at the cost of the installation. They don’t consider future costs, such as:
- Energy savings
- Roof renewability
Energy savings
The average high school spends around $74,390 per year on heating and cooling. Because spray foam is seamless, there is no thermal shock. Spray foam can reduce energy savings by an average of 15-30%.
Let’s assume a 22% reduction in energy costs for simplicity.
$74,390 reduced by 22% = $58,024. $74,390 – $58,024 = $16,366.***
How would saving $16,366 per year look for the school budget?
Another question I would ask is, how long until the roof pays for itself?
***There are a lot of variables in this calculation, such as HVAC efficiency, size of the school, climate, and the current condition of the roof.
While metal and single-ply can create the same R-value as spray foam, they cannot eliminate thermal shock.
Roof renewability
What happens when the roof’s life is over? Does it need to be torn off and transported to a landfill? Or can it be renewed?
On some occasions, a metal and single-ply roof can be restored by installing a roof coating system. On some occasions where the roof isn’t in great shape, the roof will need to be 100% torn off.
A spray foam roof can be renewed.
When a spray foam roof is installed, a thin layer of coating is installed over the foam to protect it from UV rays.
For a 20-year warranty, 30 mils (the thickness) of coating is installed.
In year 20, the 30 mils will naturally wear away to 7-8 mils.
All a contractor needs to do is clean the roof and bring the coating back to its original thickness.
A brand-new warranty would be granted.
The renewal process can repeat over and over again. The spray foam doesn’t lose any performance or R-value over time.
No tear-off, no adding to landfills, minimal business interruption.
What is Co-op purchasing and how does it benefit schools?
Co-op purchasing through Sourcewell is a way for schools to buy things (including roofing services) through screened vendors. Sourcewell finds good companies, good products, determines fair pricing, and provides a menu for schools to choose from.
Here’s a video explaining co-op purchasing:
[]If a school chooses not to pursue co-op purchasing, they could:
- Pay more for a roof than they should
- Use an uncreditable roofing contractor
- Have the roof installed with inferior materials
This doesn’t happen often, but if you went with Sourcewell, it takes some of the hard work comparing vendors out of the equation.
Want to see some school roofing projects?
Mercer County Career Center had a 106,000 sq. ft. granulated modified bitumen roof. They chose to install spray polyurethane foam because the alternative of a complete tear-off was 3x the cost.
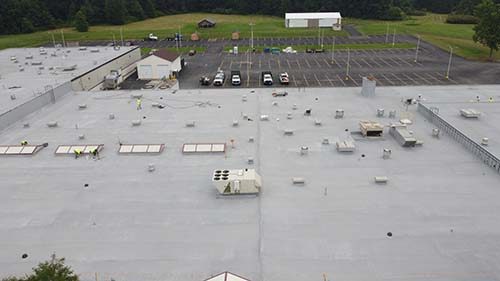
Oakview had a 36,500 sq. ft. EPDM roof. They chose to install spray polyurethane foam because they could avoid the costly tear-off of the existing roof. They also had many penetrations and flashing. With spray foam being fluid-applied, these would be 100% sealed.
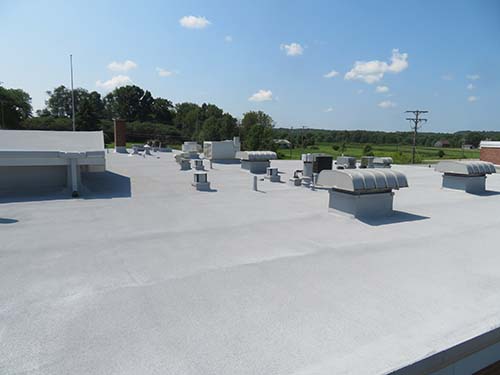