When I bring up spray foam roofing to a friend or someone new that I meet, they always have a strange look on their face.
They say, “I’ve never heard of that before” or “I’ve never seen that on a roof”.
If you are like most, this is the first time you’ve heard about spray foam roofing.
But don’t worry.
In this guide, you’ll learn:
- What a spray foam roofing system is?
- Why building owners choose spray foam over traditional roofing systems?
- The common problems spray foam roofs have.
- The myths, rumors, and misconceptions of spray foam.
In the end, I’ll include some photos taken from a drone of recently completed spray foam roofs.
Let’s get started!
What is a spray foam roofing system?
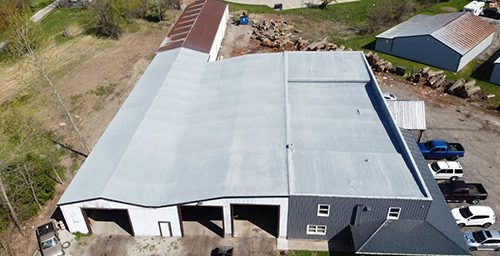
A spray foam roofing system has four parts:
- Spray polyurethane foam
- Basecoat of coating
- Topcoat of coating
- Granules
Here’s how they are installed over an existing roof:
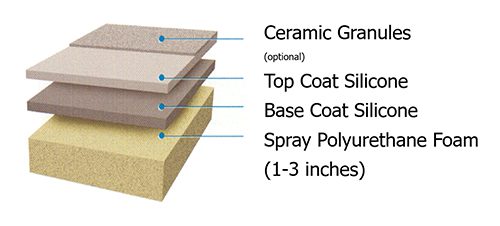
NOTE: Your existing roof would be at the bottom.
Spray polyurethane foam is a mixture of two chemicals. The two chemicals called an A-side and B-side are pumped from separate containers at a job site.
The chemicals sit in 55-gallon containers, which are stored in a box truck that’s parked near the roof.
The chemicals are heated and transferred through hoses. At the end of the hose is a mixing gun. The mixing gun mixes the chemicals and produces the spray foam material.
Here’s a video showing spray foam being applied to a roof:
How thick is spray foam installed?
Spray foam has to be installed at least one inch thick to perform correctly.
The thickness of foam is custom to provide proper sloping and to meet minimum R-value requirements.
An example could be 2” of foam around penetrations and 1” of foam around drains and perimeters.
Most installations average a thickness of 1.5” to 2”.
What happens after spray foam is installed?
One bad thing about spray foam is that it will degrade from UV rays. This means that a protective coating must be installed over the foam within 72 hours.
Spray foam contractors install different types of elastomeric coatings over spray foam.
Elastomeric means that the coating can expand and contract with the roof during temperature changes without losing any performance.
Silicone is the most-used type of elastomeric coating, but acrylic and urethanes are used as well.
It’s important to note that the coating is installed in two separate coats.
Once the basecoat cures, then the topcoat is installed.
Granules are embedded into the topcoat.
Now that we know what a spray foam roofing system is and how it’s installed, let’s look at why building owners choose spray foam over traditional roofing systems.
Why do building owners choose spray foam over traditional roofing systems?
It all comes down to money!
Here are some of the advantages spray foam roofing has over traditional systems.
Ease of installation
Since spray foam is fluid-applied, it’s very easy to install. There are no screws, plates, or adhesives. A certified SPFA applicator simply presses the gun and the material comes out.
This saves money on a roofing project because it requires fewer people and fewer hours to install.
I wanted to bring up roof penetrations, such as skylights, HVAC units, flashings, curbs, etc.
Traditional roofing systems need to cut rubber sheets, use termination metal, use sealants, or other types of custom-fitting techniques to make sure these areas are watertight.
Spray foam just presses the gun and the foam material adheres directly to the penetration, making it watertight.
Minimizes tear-off
Spray foam roofs are mainly installed over existing commercial roofs. These roofs usually have some sort of leaking, or their warranty has expired.
To install a traditional roofing system and get a new warranty, your roof will need to be 100% torn off. This is wasteful because tear-off takes a long time to do, is bad for the environment, and is very costly.
Then you have to install a whole new roofing system.
An advantage the spray foam roofing system has is that tear-off is minimized.
A spray foam contractor will identify areas of the roof’s insulation that are holding water. These areas need to be removed and replaced.
Generally, this can be from 1% to 25% of the roof. A visual inspection, the pulling of core samples, and infrared surveys will identify these areas.
Once the wet areas are removed and replaced, spray foam can be installed over the field of the roof.
NOTE: If there is excessive water in the existing system, as in more than 25%, it’s probably best to do a complete tear-off. Also, if two or more roofing systems are installed, at least one roofing system will need to be completely torn off.
Reduces future energy costs
If your current roof is leaking, there’s a good chance that your heating/cooling is leaking as well. Since spray foam is fluid-applied, it will seal any holes in the roof (even the microscopic ones).
Air can still pass through a roofing system. But the amount/speed of air transfer is what’s known as R-value.
R-value is a measurement of a material’s ability to withstand the transfer of hot and cold air.
The higher the R-value, the more resistance against heat and cold airflow a material has.
Spray polyurethane foam has an R-value of 6.5 per inch of thickness. This is the highest R-value of any roofing insulation available. The R-value will not decrease over time.
Polyiso board is a common insulation that’s used on traditional roofing systems. Polyiso has an initial R-value of 5.5 per inch of thickness, but the R-value decreases over time.
The amount of energy savings varies by the conditions of the current roof. Texas A&M University has a famous case study where they recouped the cost of the spray foam roof’s installation through energy costs in only 5 years.
Seamless
Since the spray foam roofing system is fluid-applied and fully-adhered, there are no seams.
Seams are what’s used on metal, single-ply, and built-up roofs to combine sheets of roofing material.
Usually, fasteners, plates, adhesives, screws, or some type of heat-welding are used to fasten the sheets together.
Most roof leaks are caused due to seam and penetration failure.
This is due to the stress created when the roof expands and contracts with fluctuating temperatures.
With spray foam roofs having no seams, it removes the most common location where a roof can leak.
Renewable and sustainable
There are spray foam roofs that our current owners were the sprayers or hose-holders back in the 1980s. Now they are supervising the next generation.
These roofs are still being recoated and getting new warranties.
How???
Let’s say that in 1980, a spray foam roof was installed over an existing gravel built-up roof. The roof was given a 20-year warranty.
The warranty length is in direct correlation with the amount of protective coating installed over the foam.
- For a 10-year warranty, 20 mils of coating are installed
- For a 15-year warranty, 25 mils of coating are installed
- For a 20-year warranty, 30 mils of coating are installed
After 20 years, the 30 mils of coating will naturally wear away to around 7-8 mils.
So in the year 2000, a spray foam contractor will perform a recoat (add new coating onto the roof) and bring the level to 30 mils again.
A new 20-year warranty would be granted.
In 2020, another recoat can be done. A new warranty can be granted.
NOTE: This is different from traditional roofing systems. When their warranty is up, there is no way to renew them. A building owner is forced to install another roofing system over what they already have or perform a costly complete tear-off.
Easy to maintain
When you get a new roof installed, you want to make sure it doesn’t leak. No roofing system out there can survive without some sort of routine maintenance.
It’s like your car, regardless of the manufacturer, they all need oil changes, new tires, new brakes, etc.
If you ignore maintenance, the car will not last (or perform) how it was meant to.
A spray foam roofing system is easy to maintain versus traditional roofing systems.
On a spray foam roof, since there are no seams, you can easily identify any cracks or punctures in the roof.
A contractor would cut these areas out, dry them, and fill the area with caulk and coating. Smooth the area out and you’re done.
On traditional roofing systems, a contractor will need to inspect every screw, every seam, and every penetration in great detail to make sure it’s watertight.
If water is entering the roof, a contractor needs to cut the membrane, cut the insulation, add new materials, and piece them together creating more seams.
There’s more opportunity for leaks, they take longer to repair, and water entry points are harder to identify on traditional roofing systems.
Closed-cell insulation
What happens if you do get a hole, crack, or puncture in your roofing system?
Because of weather, foot traffic, hail, animals, and about a hundred other things, you will likely have some sort of problems with your roof.
Spray foam has what’s called “closed-cell insulation”. This means that if there’s a puncture in the roof, water will sit in the puncture and not spread.
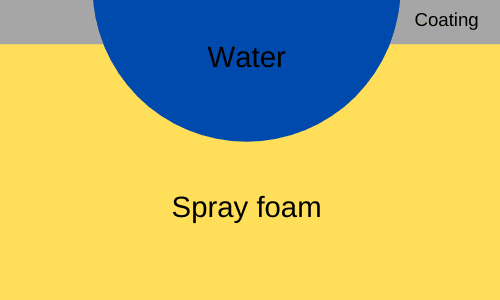
The opposite is true for traditional roofing insulation, such as polyiso board. When water reaches polyiso board, it will saturate and expand, making more of the insulation wet.
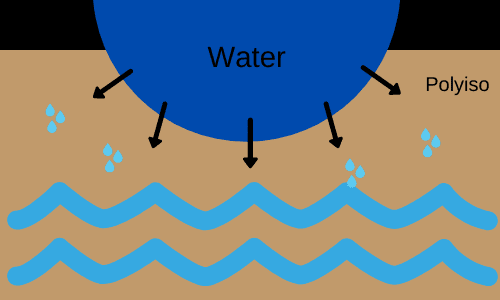
There could be a teeny tiny water entry point, but if that water can travel and spread, a large area of the roof’s insulation could be saturated.
Now that we know some of the reasons why building owners choose spray foam roofing, what problems do they have?
The common problems of a spray foam roofing system
No roofing system is without problems.
For spray foam roofing, here are some of its problems:
Overspray
Overspray is when a spray foam contractor is applying the foam and it gets taken away by the wind. The foam can get onto windows, nearby cars, other structures, basically anything close to your roof.
Contractors combat wind with windscreens, spraying foam in a booth, or just not spraying when it’s too windy.
Hard to find good applicators
Spray foam is easy to apply, but hard to master.
When the temperature of the roof deck increases throughout the day, the temperature at which the chemicals are heated needs to be adjusted.
When it cools back down at the end of the day, the temperature needs to be adjusted again.
On larger projects that go multiple months, say from August to October, an entirely different set of foam (based on reaction time per the seasonal temperatures) may be used at the end of the project as opposed to the beginning.
There’s a lot of science involved with spray foam roofing. Only the contractors that master the “Three E’s” should be applying the product.
The problem is, there are some bad spray foam applicators. When the contractor doesn’t know the correct way to apply foam, and the roof looks bad, it makes it look like the product failed, when that’s not true.
So, if you’re deciding on going with spray foam, ask the contractor for a database of case studies. A database in which you can contact other building owners and ask them “How has your spray foam roof been performing?”
Good spray foam contractors have client lists that go back 30+ years.
Need good weather to install
I know we talked about wind, but there are also temperature restrictions when applying the foam.
It needs to be at least 50 degrees Fahrenheit and rising to spray foam correctly.
If you spray foam under 50 degrees, the foam will not cure correctly, and it will not perform as it’s meant to.
The roof also needs to be dry, meaning it cannot rain during installation.
If there’s rain the previous day, a contractor will blow all the water towards a drain and wait for all the water to evaporate before installing spray foam.
Now that we know the problems with spray foam roofs, I wanted to dig into some of the myths, rumors, and misconceptions of spray foam roofing.
The myths, rumors, and misconceptions of spray foam
Since spray foam roofing is unknown, there are lots of speculation floating around the internet.
From a company that’s been around spray foam since 1979, we’ve come to lay these rumors to rest.
Here are some of the myths about SPF roofing.
It’s only a temporary solution
Non-spray foam roofing fans will argue that spray foam is just a temporary solution. While it’s true that spray foam can be installed in certain areas to get the roof through a season, it’s not intended to be a temporary repair, but can be in an emergency.
A common example is that a customer will reach out to us in the Fall, hoping to eliminate some leaking spots before Winter.
Customers might need to make a decision moving forward with their board, ownership, and get their financing or budget in place, which could take some time.
A spray foam contractor can fix the roof today, and then come back in the Spring and repair the entire roof.
But to say that spray foam is only good for spot fixes is just flat-out wrong.
Not sustainable
Most spray foam roofs come with a 10, 15, or 20-year warranty. Once the warranty is up, more coating is installed and you’d get a new 10, 15, or 20-year warranty.
If damage happens on your roof, it’s easily repaired using caulk/coating.
As long as the roof has some sort of routine maintenance (like all roofing systems need), the spray foam roof will last as long as it’s designed to.
If you have doubts that a spray foam roof will last, contact a contractor who will give you a client list of roofs that have surpassed the original warranty and are on their 2nd and 3rd recoats.
Can’t be walked on/weak
Some say that spray foam roofs are weak and cannot be walked on. This is false. Spray foam roofs have a compression strength of 50-60 pounds per square inch.
This is roughly the same strength the pegs on your refrigerator have.
Birds peck at it
Some say that birds have pecked their foam roof. The birds left the foam exposed to the UV Rays, and then the roof got a hole in it.
This may have been a slight issue in the past, but with the application of granules embedded into the coating, this issue has been eliminated.
It’s new
Since no one has heard of a foam roof, people think it’s a new phenomenon.
Spray polyurethane foam is not new.
West Roofing Systems has been applying millions of sq. ft. of foam roofing since 1979. The application goes back to insulation in the ‘60s, and there have been stories of foam being used in the 1950s as well.
Either way you slice it, spray foam roofing is not a new concept.
What is new is the formula used to make the A and B sides of the foam. The chemicals to make foam used to contain ozone-depleting substances, but do not any longer.
Tends to hold dirt
All roofing systems hold dirt. Naturally, the perfectly white roofs after installation don’t stay perfectly white for very long.
Roofs are exposed to the harshest of weather conditions.
While they all hold some level of dirt, what’s most important is that they don’t hold water.
Photos from a drone of recently completed spray foam roofing
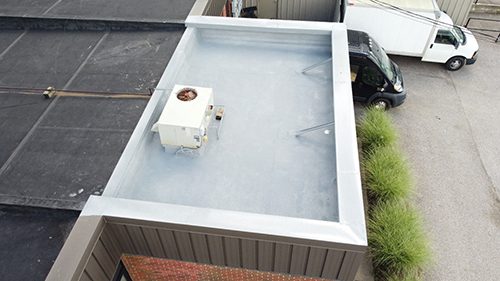
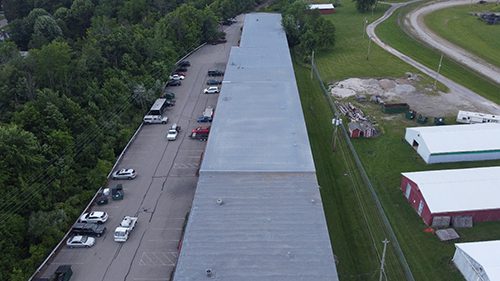
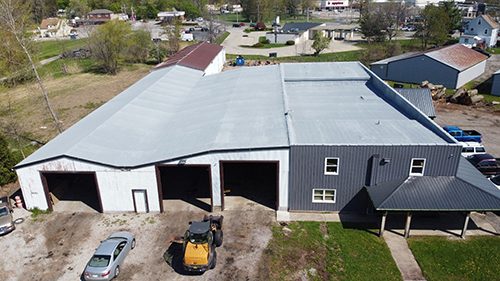
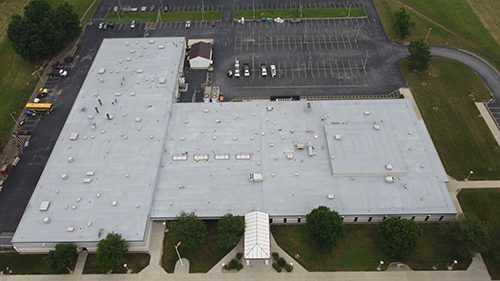
What are your next steps?
Now that you got your feet wet with spray foam roofing, it’s time to learn more.
Here are some of our most popular articles:
- The Pros and Cons of Spray Foam Roofing
- The Ultimate Guide to Spray Foam Roofing
- Cost of a Spray Polyurethane Foam Roofing System
West Roofing Systems has been installing, repairing, and servicing spray foam roofing systems since 1979. We’ve done over 60 million square feet of spray foam roofing!
Every roof is designed differently, and every building owners’ goals are different.
We’re here to solve your roofing problems in the most cost-effective way possible.