Ah, Florida. The land of sun tans, perfect bodies, and…extreme heat.
The temperatures in upper Florida, near Jacksonville, average 90 degrees in the Summer months, while temperatures in lower Florida, near Miami, can average around 96 degrees.
It’s no wonder why so many Floridian building owners want to install spray foam roofs.
Wouldn’t it be great to have a roofing system that provides:
- The most energy savings
- Provides the greatest wind uplift potential
- Is renewable
- And complies with current Florida building codes?
In this article, we’ll share 5 things to consider (3 good and 2 bad) that you should look at before choosing a spray foam roof for your commercial building in Florida.
Let’s begin…
Should you get a spray foam roof in Florida?
1. Spray foam roofs have the most significant energy savings of any roofing system
Anyone from Florida or who has been to Florida knows that the state can get hot!
In fact, Florida is one of the three states with the highest average temperatures during the summer.
What does this mean for you as a building owner?
This means the costs to keep your building cool will be high. There’s a clear correlation between high temperatures and air conditioning (AC) costs.
To keep the AC from continuously running, you need a roofing system to keep the cool air in as much as possible.
Enter a spray foam roof.
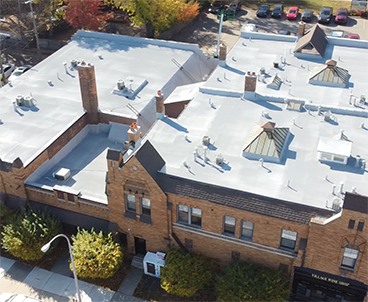
Spray foam has the highest R-value of any commonly used roof insulation. R-value is the capacity of an insulating material to resist heat flow. The higher the R-value, the greater the insulating power. Here are the average R-values for some common roof materials
[table id=5 /]The higher the R-value, the less heat or cool air will pass through.
Higher R-value = less HVAC use = lower energy costs
Total payback of your new roof usually occurs in less than ten years through savings in heating and cooling costs.
However, since Florida is always hot, the payback period can be shorter, closer to 5-7 years.
Note: There are several variables when determining the payback period, including the size of your building, hours of operation, building operations, if your roof requires tear-off, and much more.
2. Spray foam roofs have the greatest wind uplift potential
Did you know 40% of all US hurricanes strike Florida?
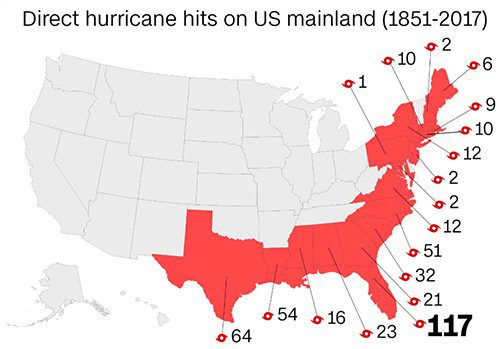
Perhaps that’s why Florida has stringent building codes regarding roofs and wind uplift potential.
In fact, I had a conversation with Mike Silvers, Director of Technical Services for Florida’s Association of Roofing Professionals (FRSA).
Here are the most critical points from our conversation about spray foam and building codes:
- Florida’s building code is separate from the international building code, which most of the country is under. This is due to Florida being exposed to higher levels of wind than most of the country.
- ASCE (American Society of Engineers) uses building code ASCE 7-10 until 12/31/2020, then ASCE 7-16 will be used.
- If you’re replacing your roof with shingles, the wind uplift is measured in Miles Per Hour (MPH). Most manufacturers produce shingles to meet the ASCE 7-10 requirements. If you aren’t sure, you can use a wind map to see what the wind speeds are for your area. You can then check the shingles to see what MPH speeds they’re certified for.
- Miami-Dade and Broward Counties use a Notice-of-Approval, a product approval system for High-Velocity Hurricane Zones.
- All other counties use a Product Approval, where you can insert the manufacturer and product, and you’ll be able to see which products are approved.
- For free, anyone can use the Roof Wind Designer. Here you can input details about your building, such as building category, wind exposure level, dimensions of your building, etc. It will give you the required wind uplift resistance in pounds per square foot. Here’s an example of the results for a small condo in New Smyrna Beach, Florida:
Note: take a look at the difference in wind uplift requirements for the roof field vs. the perimeter vs. the corners:
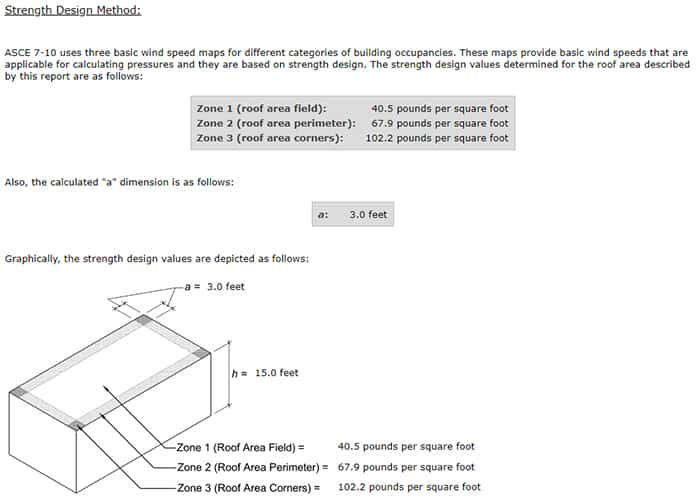
Other points from our conversation:
- Approximately 1 out of 20 roofing contractors do NOT know that if you’re going to use the existing roof system for their attachment, the existing roof system needs to meet the current uplift provisions.
- Since Hurricane Andrew (August 1992), wind uplift standards have only increased. Some roofs that are 20 years old will have 1/10th of the fastening strength required today.
- If you ignore building codes, the building owner and the roofing contractor will face consequences. If a building owner tries to sell the building, and the buyer uses a building inspector, they will know the roof is not up to code. The building owner will then need to re-roof to bring the roof up to current uplift requirements or grant credit. If a licensed roofing contractor performed the work and stated in the contract that it’s up to code, they’ll have to re-roof until it meets code.
- Re-roofing over an existing roof is a Level 1 Alteration, which can be found in the 2017 Florida Building Code.
- The bottom line is that while spray foam has excellent resistance against wind, what matters most is what that foam attaches itself to.
3. Spray foam roofs are renewable
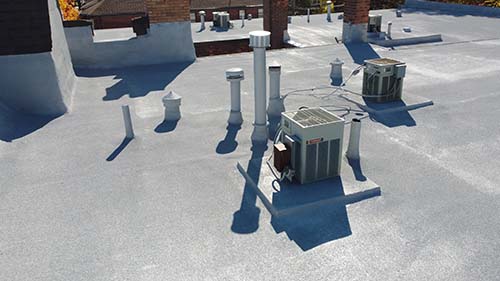
One of the most significant benefits of a spray foam roof is its ability to be re-coated. In the initial installation, a typical application of coating over the top of spray foam is 20-30 mils.
After 10-20 years, the initial thickness of 30 mils might be down to 8-10, depending on weather and foot traffic.
Once your coating reaches that point, a roofing contractor will renew it by:
- filling any holes with silicone
- ensuring the roof is dry
- and then add the coating
Once you’re at the original millage of coating, many manufacturers will offer an extended warranty. The option to re-up your warranty allows the spray foam roof to be a genuinely renewable roof system.
Why you may not want a spray foam roof in Florida
Here are a few reasons you may not want a spray foam roof in Florida.
4. Spray foam roofs need to be installed with little wind present
One of the biggest issues with a spray foam roof installation is overspray. Overspray means that the product, upon application, can get swept up in the breezes and land elsewhere.
This can cause problems when spraying near a parking lot or expensive machinery (such as airplanes, semi-trucks, etc.).
Overspray isn’t a permanent issue as the foam is removable, but it makes the job difficult on a windy day.
A roofing contractor will perform numerous tactics to combat overspray, including:
- Using windscreens held physically by roofers
- Spraying inside a burlap-enclosed cage
- Using car covers
- Or just waiting until the wind dies down
It’s not a serious issue to where you should abandon spray foam just because you live in a windy environment. It’s just an added wrench that gets thrown into a project that other roofing systems don’t have to deal with.
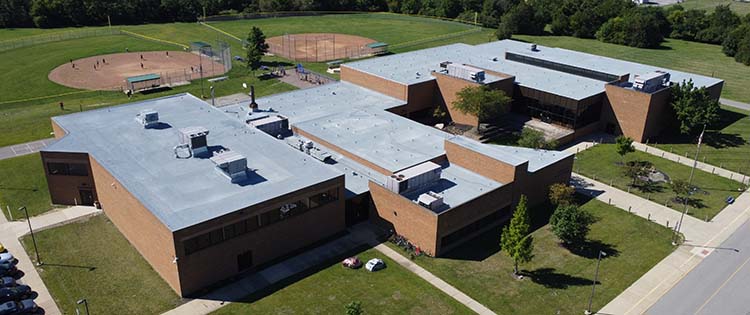
5. You aren’t open to change
Many building owners are tied to their roots. They grew up favoring tar and gravel, and when they have a roof leak, the first step is to buy another bucket of tar and slather it on there.
The same applies to Metal, TPO, or EPDM roofers.
Despite the advantages of spray foam over other roofing systems, some people aren’t open to change, so if that’s you, then a spray foam roof might not be the right fit for your building.
Other popular articles about spray foam roofing