Are you a building owner who has a leaking commercial roof?
Are you unsure which roofing system would be best to install?
This educational article is designed to provide building owners with general knowledge of today’s four basic roofing systems.
The four roofing systems are:
- Single-ply
- Metal
- Spray polyurethane foam
- Roof coating systems
The approach is simple. We list the advantages and disadvantages of each system…and then sit back so you can form your own opinion.
Single-ply vs. Metal vs. Spray polyurethane foam vs roof coating systems
Single-ply roofs are lightweight, easy to maintain, and have low initial costs if there aren’t many penetrations, but the seam and penetration integrity are extremely critical.
Metal roofs are time-tested, aesthetically pleasing, can last a long time, but are very expensive to install or replace.
Spray polyurethane foam has a very high R-value, is seamless, is quickly installed, the thickness can be customized to eliminate ponding water and it can be renewed over and over again, but the installation process is weather-sensitive.
Roof coating systems are easy to apply, seamless, the thickness can be customized to grant shorter/longer warranties, but they quickly get dirty and provide no significant R-value.
Single-Ply Roofing Pros and Cons
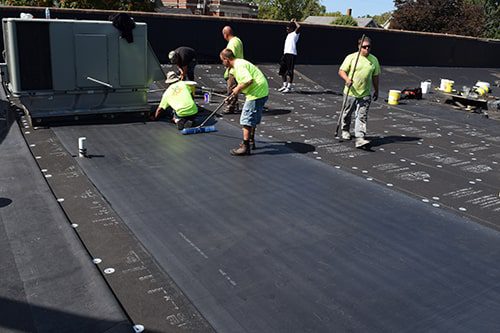
Pros of single-ply roofing
- Lightweight (when not ballasted)
- Easy to maintain (when not ballasted)
- Low-cost (if no details/penetrations)
Lightweight
If TPO and EPDM sheets are fully adhered (using an adhesive) or mechanically attached (using fasteners and screws), the roofing system can be lightweight. If ballasted (using rocks to hold the system down), the system is no longer lightweight.
Easy to maintain
A roofing contractor can maintain a single-ply roof by checking the seams, flashings, and fasteners. They will also check the membrane to make sure it’s adhered correctly and that there are no holes, cracks, or punctures.
Low-cost
A single-ply roof usually costs between $5 and $10 per square foot in materials and labor. There are many variables to pricing including:
- The condition of the existing roof
- Insulation choice (polyiso, EPS, XPS)
- Membrane choice (usually TPO or EPDM)
- Installation choice (ballasted, fully-adhered, etc.)
- Length of desired warranty
- Number of penetrations
Cons of single-ply roofing
- High cost (if many details)
- Fastener failure
- Seam health is critical
- Only one roofing layer to stop water intrusion
High cost
If a roof has many skylights, curbs, pipes, drains, anything that sticks out of the membrane, or additional taper/sloping that’s needed, the cost to install a single-ply roof can be on the higher side of the $5.00 – $8.00 per square foot range.
Fastener failure
Fasteners are prone to back out or rust. They can also be damaged by foot traffic.
Seam health is critical
There are many seams on a single-ply roof. Seam failure is where most leaks occur on single-ply roofs.
Only one roofing layer to stop water intrusion
The outermost membrane is the only waterproofing layer of the system. If water gets beyond that and into the insulation, water can travel and saturate a large area of the roof.
Metal Roofing Pros and Cons
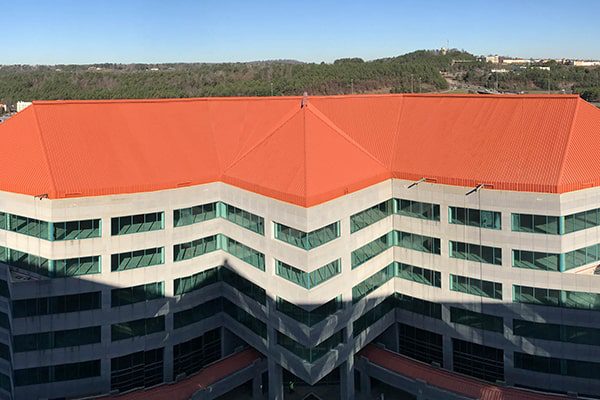
Pros of metal roofing
- time-tested
- can last 40 + years
- color choice
Time-tested
Metal roofs have been around since the 1800s. Technology has advanced metal roofs to become more lightweight, more resistant to rust, and UV stable.
Can last 40 + years
Metal roofs can last a long time, but it’s all dependent on how good the installation was, how much maintenance is kept up with, and the climate the roof is in.
Color choice
Compared to other roofing systems on this list, metal roofs are aesthetically pleasing. Metal roofs can come in any color to match a brand’s identity or to maximize reflectivity from the sun.
Cons of metal roofing
- expensive
- rust
- pinholes
- seams
Expensive
A metal roof usually costs between $10-$20 per square foot in labor and materials. There are lots of variables with pricing, but metal roofs are expensive compared to other roofing systems on this list.
Rust
Metal roofs are prone to rust, which is another problem that others on the list don’t have. Also, when repaired or restored, a rust inhibitor/primer may have to be used.
Pinholes
Pinholes can develop on a metal roof over time. This is due to old age, around rusted screw heads, blown debris, dropped tools, UV degradation, etc. Pinholes cause issues because they let water in but are hard to locate and repair.
Seams
Metal panels installed on a roof have many seams. When the metal roof expands and contracts with weather fluctuations, seams take on the most stress.
Spray Foam Roofing Pros and Cons

Pros of spray foam roofing
- Highest R-value
- Quickly installed
- Eliminates ponding water
- Renewable and sustainable
- Successful history
- Low cost
- Easily maintained
- Seamless
- Not prone to leak
Highest R-value
Spray foam has an R-value of 6.5 per inch of thickness, which is higher than any other roofing insulation. This reduces energy costs.
Quickly installed
Because spray foam roofing is fluid-applied, it’s easily installed on the field of the roof and around any penetrations.
Eliminates ponding water
Because spray foam is fluid-applied, the thickness can be customized to provide the proper slope in areas where ponding water exists.
Renewable and sustainable
After a spray foam roof’s warranty has expired (usually after 10, 15, or 20-years), it can be recoated. This gives the roof a new 10, 15, or 20-year warranty. The spray foam doesn’t lose any R-value or waterproofing capabilities over time.
Successful history
Spray polyurethane foam roofing has been around since the 1960s. Many spray foam roofs that were installed in the 1970s and 1980s still have the original foam on them.
Low cost
A spray foam roof costs around $5.00 – $8.00 per square foot for materials and labor. Many variables come with pricing. The amount of tear-off that’s required greatly influences the total cost of the project.
Easily maintained
If a spray foam roof has a crack or puncture, a contractor will cut around the area with a knife, dry the area out, and insert caulk then coating. The area is smoothed out and the repair is finished.
Seamless
Since spray foam is fluid-applied, it self-adheres to the existing roof and all penetrations. The roof is one continuous layer, meaning there are no seams.
Not prone to leak
Spray polyurethane foam has closed-cell properties. Closed-cell means that if a foam roof gets a hole or puncture, water will sit there and not move. This is different from traditional roofing insulation where water can travel throughout the insulation and saturate a large area of the roof.
Cons of spray foam roofing
- Easily punctured
- Weather-sensitive to install
- Overspray
- Few contractors to install
Easily punctured
While spray foam roofs have a compression strength of 40 PSI (equal to the pegs of your refrigerator), the membrane can be punctured with sharper objects.
Weather-sensitive to install
It needs to be 50 degrees (F) or above to correctly install a spray foam roof. It also cannot be very windy and the roof substrate needs to be dry, clean, and sound.
Overspray
Although spray booths and windscreens are commonly used on installations, spray foam can easily be carried onto undesirable areas. A common issue is an overspray with windows, patios, and nearby vehicles.
Few contractors to install
There is a sweet science to spray foam correctly. There are also high upfront equipment costs to the contractor. This brings high barriers to entry, resulting in few contractors that can apply good foam.
Roof Coating System Pros and Cons
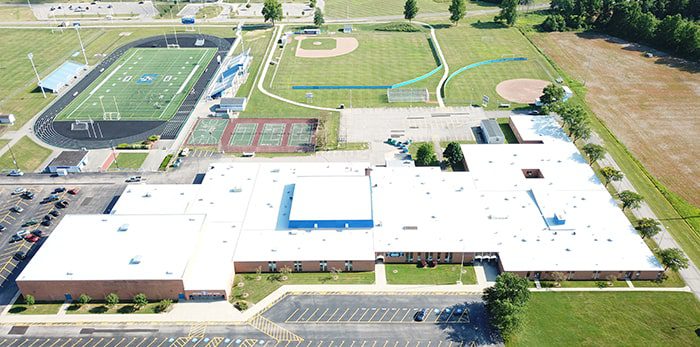
Pros of roof coating systems
- Cost savings versus complete tear-off
- Extends roof life
- Reduces future energy costs
- Easy to install
- Manufacturer warranty
- Seamless
Cost savings versus complete tear-off
A roof coating system usually costs between $4.00 – $6.00 per square foot. A complete tear-off will cost a minimum of $6.00 per square foot. There are many variables in determining the cost of the roofing project.
Extends roof life
Instead of a complete tear-off in a few years, in most cases, the life of the roof can be extended by adding an elastomeric coating over the existing roof.
Reduces future energy costs
Most building owners choose a white or light grey colored coating. This is to turn their darker-colored roof into a roof that can reflect the sun. Energy savings can be between 15-30%.
Easy to install
Roof coatings are fluid-applied (either rolled or sprayed), which makes them easy to install on the field of the roof and around all penetrations.
Manufacturer’s warranty
The manufacturer of the coatings can grant a warranty. The contractor who installed the coatings can also provide a warranty.
Seamless
Since roof coatings are fluid-applied, they will be installed over all the existing seams that a roof has. This will give the roof a seamless membrane.
Cons of roof coating systems
- Only silicone sticks to silicone
- Strict eligibility
- Unpleasant odor
- Quickly gets dirty
Only silicone sticks to silicone
Most building owners choose silicone as their choice of roof coatings because it’s a great blend of performance and price. But, once you install it, you’ll have to install a cover board or remove the roof coatings before installing another roofing system. Nothing sticks to silicone besides silicone.
Strict eligibility
There are three checkpoints a roof must have to qualify for a roof coating system:
- 70-80% of the roof’s insulation must be dry
- If there are seams, they must be in good condition/well attached
- At least annual routine maintenance has been occurring
Unpleasant odor
There is a foul smell to roof coatings during application. HVAC systems are usually turned off and wrapped when they are installed.
Quickly gets dirty
Roofs handle the harshest of weather conditions. When a roof is bright white, it quickly gets dirty.
Key Takeaways
Each of the four types of commercial roofing systems:
- Single-ply
- Metal
- Spray polyurethane foam
- Roof coating systems
They all come with their own set of advantages and disadvantages.
Pros and cons of single-ply roofing:
Single-ply roofs are lightweight, easy to maintain, and lots of contractors perform the work. However, since most leaks happen at the seams, seam integrity is critical.
Pros and cons of metal roofing:
Metal roofs are time-tested and durable, but they are very expensive to install and replace.
Pros and cons of spray foam roofing:
Spray foam roofs are seamless, have a high R-value, are quickly installed, and are renewable. However, spray foam roofs have a limited installation window and not many contractors install the system.
Pros and cons of roof coating systems:
Roof coating systems help decent/good roofs avoid the complete tear-off, but there’s strict eligibility to have one installed.
Final Thoughts
We at West Roofing Systems, hope we’ve provided you with a better understanding of the four main commercial roofing systems.
Remember “the roof system you choose is only as good as the contractor installing it.”
Do you have any questions about the four main commercial roofing systems? If so, contact us or comment below with your thoughts.
Up Next: