Quick answer: For an average 20,000 sq. foot commercial roof, it will usually cost between $6 and $12 per square foot in materials and labor to install a typical single-ply membrane commercial roofing system.
NOTE: As of April 2023, the pricing from manufacturers has greatly increased. Last year it was roughly $3.50 – $7.50 per square foot. Manufacturer prices are just one of the hundreds of variables influencing the cost. Let’s read more about them below.
What makes the cost go up or down?
In this article, you’ll learn the factors that affect the cost of a single-ply membrane roof, such as:
- The size of your roof
- The current condition of your roof
- How easily can your roof be accessed?
- What type of insulation would you choose?
- What kind of membrane would you choose?
- What installation method would you choose?
- How thick is the membrane?
- How many penetrations are on your roof?
- How long of a warranty would you choose?
Let’s get started!
The Size of Your Roof
When a contractor is pricing a new roofing system, the economies of scale start around 20,000 sq feet. After 20,000 sq. feet, you can start saving money per square foot of roof.
Other size factors that can impact your cost also include:
- The logistics of moving equipment up to and across a large roof
- Debris removal costs
- Material transport costs – this cost can take up 2-3% of the total project costs
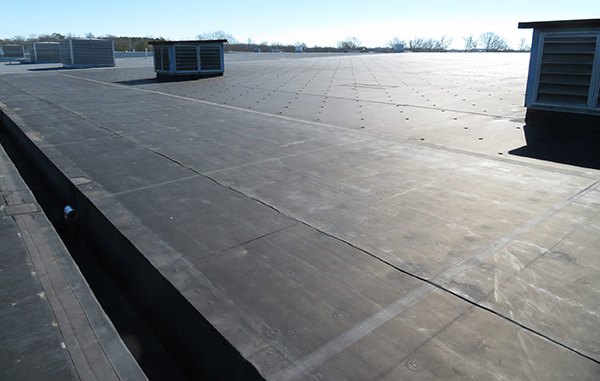
The Condition of the Existing Roof
The condition of your existing roof will be a crucial factor in the cost of your new single-ply membrane roof. There are three options when dealing with the existing roof:
Clean and Prepare Existing Roof (no significant alterations) – $0.10 – $1.50 per sq. foot
When you have a solid roof that doesn’t require major modifications or corrections, the contractor must clean and prepare the roof so the insulation adheres appropriately.
There are four ways a contractor can prepare a roof for single-ply membrane installation:
- Air Pressure Cleaning
- Powerwash
- Dry Vac/Ballast Removal
- Wet Vac for dirt, gravel, and dust removal
The price can be as high as $1.50 per sq. ft. because some roofing contractors might have to subcontract out specialized cleaning, such as Dry and Wet Vac work.
Recovery Board Fastened on Top of the Existing Roof – $0.70 – $1.40 per sq. foot
Recovery boards are commonly used to cover and improve the application surface. This process could cover joints and provide a separation layer between existing and new roofing systems.
Stripping and Removal of Roof – $1.00 – $4.00 per sq. foot
Two main reasons a contractor would need to strip and remove your existing roof.
1. A building can’t have more than two roofing systems. If you currently have two roofs, your contractor must remove them before installing your new roof.
2. If your roof is damaged, saturated, or unstable, your contractor must strip the existing roof to install a new working roof.
The cost for stripping and removal of a single-ply roof varies significantly by:
- the size of your roof
- the depth of single-ply that needs to be removed
- how high is your roof
For example, a 20,000 sq. ft. roof with 2” of single-ply that needs to be removed and only a 1-story roof may cost $1.00/sq. ft.
If the same roof is 40,000 sq. ft, it will be more cost-effective per sq. ft. because the setup cost is the same no matter how big the roof is.
Another example is a 20,000 sq. ft. roof with 2” of single-ply that needs removal but is 5 stories high. Having to tear off this high will require a crane, which ups the project cost.
The cost of stripping and removing your existing single-ply roof is between $1.00 – $4.00 per sq. ft.
Access to Roo
Not all commercial roofs are flat; not all roofs can be walked on. Additional costs can occur when your contractor has limited access to the facility roof.
The height and distances of the roof can be multipliers for the cost of your single-ply membrane roof installation. Sloped roofs often require the contractors to use a man lift or repelling gear for single-ply membrane roof installation.
Contractors may need to rent conveyance equipment, such as a crane or passenger hoist to move the crew and equipment.
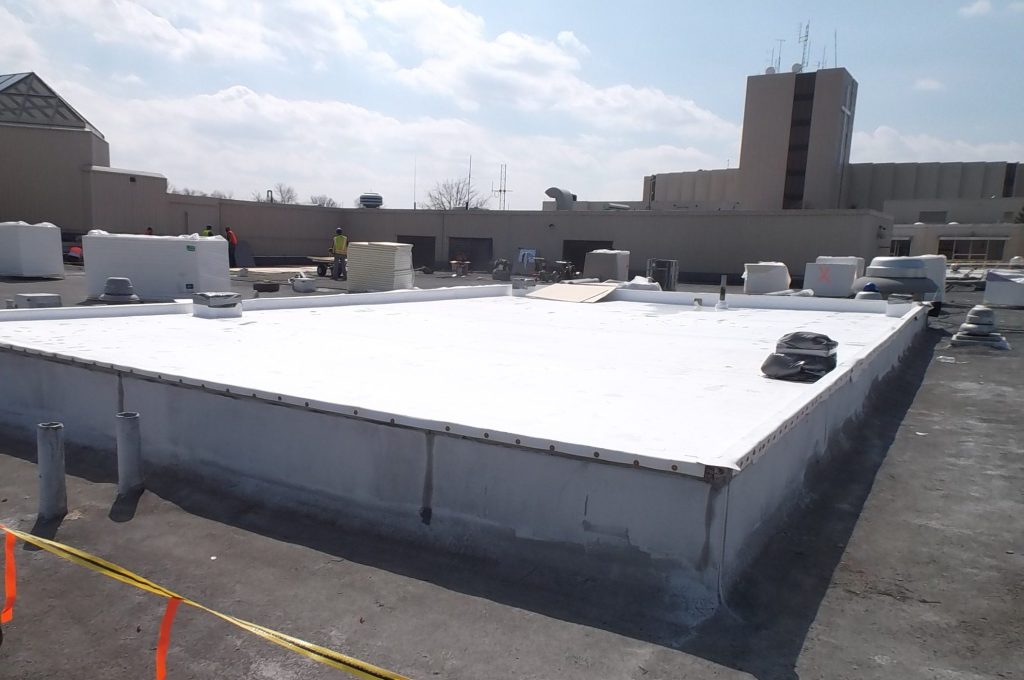
Insulation Choice
After the existing substrate is prepared, either by cleaning or removing the existing roof, the insulation is installed. In general, two layers of insulation are used.
There are a few types of insulation options the facility manager/owner can choose from:
Polyisocyanurate (Polyiso)
Polyiso is the most commonly used insulation for roofing. It’s a rigid material that can be cut to size for installation. The R-Value for Polyiso lasts longer, and the aged R-Value is still higher than EPS and XPS.
Below are the costs for three different thicknesses:
- 1 in. – $1.40 – $1.75 per sq. foot in materials and labor
- 2 in. – $2.00 – $2.50 per sq. foot in materials and labor
- 3 in. – $2.80 – $3.15 per sq. foot in materials and labor
*Attached Polyiso cost associated with a mechanical attachment would be based on industry average applications.
Expanded Polystyrene (EPS)
EPS can be used for roofing, walls, or floor insulation, but is more commonly used with concrete. You get more R-Value per dollar with EPS being the lowest-cost insulation choice.
Extruded Polystyrene (XPS)
XPS insulation can be found in blue, pink, or green and is most commonly used for wall insulation. This is probably what you think when you hear insulation because it is the middle of the road regarding cost and R-Value.
Read More: Choosing Rigid Foam by Green Building Advisor
Membrane Choice
When considering single-ply membrane roofing, there are two types of membranes to choose from, TPO and EPDM.
TPO
Thermoplastic Polyolefin is a single-ply roofing membrane that is one of the fastest-growing commercial roofing systems on the market. TPO roofing systems are made up of a single layer of synthetics and reinforcing scrim that can be used to cover flat roofs.
An average 20,000 sq. foot commercial roof will usually cost between $6 and $12 per square foot in materials and labor for a TPO membrane.
EPDM
Ethylene Propylene Diene Monomer is a single-ply membrane with a synthetic rubber compound that allows it to be flexible. EPDM has been used on commercial roofing facilities since the 1960s and is considered a time-tested option.
An average 20,000 sq. foot commercial roof usually costs between $6 and $12 per square foot in materials and labor for an EPDM membrane.
Infographic: TPO vs. EPDM Systems
Infographic: TPO vs. EPDM Systems
Installation Choice
When installing the membrane of your choice to your roof (whether it’s to the insulation or a cover board), there are three ways to choose from, Ballasted, Fastened, or Adhered.
They each have their own advantages and disadvantages regarding price, longevity, and ease of installation.
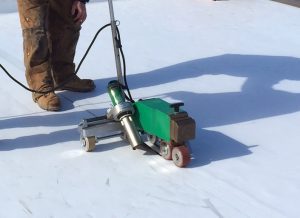
Ballasted
A Ballasted attachment is a low-cost option. It consists of laying down the membrane (TPO or EPDM) and covering it with gravel, pavers, river rock, and other similar materials. While this option can save you money (and look pretty cool), it adds up to 10 pounds per square foot to your building structure. And as the rocks degrade over time, they can easily damage the membrane underneath. Maintaining this type of system is very difficult since the ballast would need to be moved to see any deficiencies in the membrane.
Fastened
Fastened attachment is when the membrane (TPO or EPDM) is mechanically attached to the cover board with metal screws and plates. These are inserted along the seams of the membrane sheet.
Adhered
A chemically adhered membrane is rolled out onto the cover board after applying a bonding adhesive. This method does not penetrate the membrane, alleviating the chance of leaks even more.
Cost Table
Your cost could vary depending on the type of membrane thickness and attachment.
Below is a table of cost estimates based on an average-sized roof:
045 mils Thickness | 065 mils Thickness | |
TPO | ||
Ballasted | $1.90 – $2.35 per sq. foot | $2.00 – $2.50 per sq. foot |
Fastened | $2.50 – $3.00 per sq. foot | $2.65 – $3.15 per sq. foot |
Adhered | $2.75 – $3.25 per sq. foot | $2.85 – $3.50 per sq. foot |
EPDM | ||
Ballasted | $1.80 – $2.25 per sq. foot | $2.00 – $2.35 per sq. foot |
Fastened | $2.00 – $2.25 per sq. foot | $2.20 – $2.70 per sq. foot |
Adhered | $2.80 – $3.20 per sq. foot | $3.00 – $3.50 per sq. foot |
Roof Penetrations
Most commercial roofing systems have accessories such as A/C units, skylights, air vents, plumbing vents, and more. These penetrations on the roof can be in the way of rolling out a straight section of the membrane.
When the contractor approaches these penetrations with single-ply membrane roofing, they need to cut smaller membrane pieces to size. They essentially build up the roof around the vents/units, which takes up more time and can cost more money to work around.
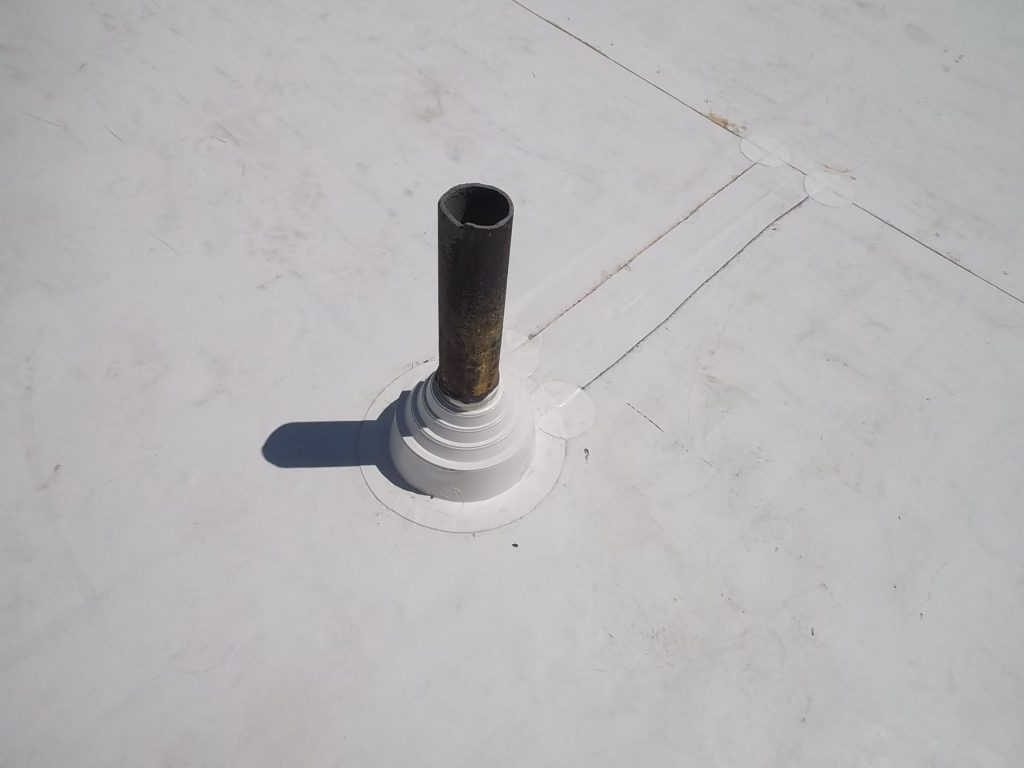
Type of Warranty
You will have a few warranty options when you install a new single-ply membrane roofing system. The three most common types of warranties include:
- Contractor’s Warranty – No expense or less than $1,000
- Manufacturer’s Product Warranty – Low cost and low coverage
- Manufacturer’s Full System Warranty – $0.08 – $0.15 per sq. foot