Summary: When installed correctly, spray foam roofing or a roof coating system is the best option to fix a flat, commercial roof. This is because they minimize tear-off. Minimizing tear-off reduces labor hours and landfill contributions. Both systems get the roof under a new warranty. They also provide a seamless membrane that’s easy to maintain, easy to install around penetrations, and provides energy savings. Spray foam has incredible R-value, and roof coating systems increase a roof’s reflectivity.
So, you have a flat, commercial roof, and you’re wondering what the best option is. Should you install a single-ply roof? Should you install a metal roof? Or should you look into spray foam or roof coating systems?
In this article, you’ll learn:
- Why spray foam or roof coating systems are your best option
- Why single-ply and metal roofing systems are not your best option
- What problems to look out for in spray foam or coating installations
- Does the existing roof system influence the best option?
Keep in mind: Every roof system can perform perfectly if it’s installed right. The most important thing with any roof installation is the quality. Granted, every roof system is installed perfectly; other things make one system better than another. Things like minimizing tear-off, not using adhesives or screws, or worrying about seams ripping apart are attractive benefits of fluid-applied roofing systems
Why spray foam or roof coating systems are your best option
Spray foam or roof coating systems are your best option because:
- They are seamless. This eliminates any wind uplift that would occur on seams that are losing adhesion or not installed properly. Seams are stressed as they move with the roof when the temperature changes, causing the roof to expand and contract.
- They minimize tear-off. If the roof is less than 25% saturated, meaning 75% or more of the existing insulation is dry, you can remove and replace JUST the wet insulation and foam or coat over everything else.
- They reduce energy expenses. Spray foam has an R-value of 6.5 per inch of thickness. When you add R-value to an existing roof, a significant reduction in energy bills is expected. Roof coating systems don’t increase R-value, but they reduce the roof’s temperature when installed with a lighter color than the existing roof.
Why single-ply and metal roofing systems are not your best option
Single-ply roofs, such as TPO and EPDM, are prominent today. I don’t know if it’s because people are just familiar with roofs that come in sheets or what, but these roofs have a dominant market share.
Here are some of the negatives about single-ply roofing systems:
- The membrane (top layer of a roof) can have fasteners going through it. Fasteners can back out, be installed incorrectly, become damaged with foot traffic, etc. When a fastener doesn’t perform correctly, water gets under the membrane.
- All single-ply roofing systems have seams. These are overlapped and sealed by a heat-weld, adhesives, fasteners, or it’s ballasted (loose gravel is laid overtop). Seams fluctuate with the roof when the temperature changes. Stress on seams is the #1 cause of a roof leak.
- They are difficult to install around pipes, HVAC units, drains, etc. Since TPO and EPDM are sheets, they need to be cut to fit around the penetrations. Adhesives and termination metal are used to make a penetration watertight.
- Since TPO and EPDM are flat, they cannot raise any areas that may be sagging and holding water. The slope has to be increased with the insulation below. This is called a “tapered” roof system, and it adds a significant cost to a roofing project.
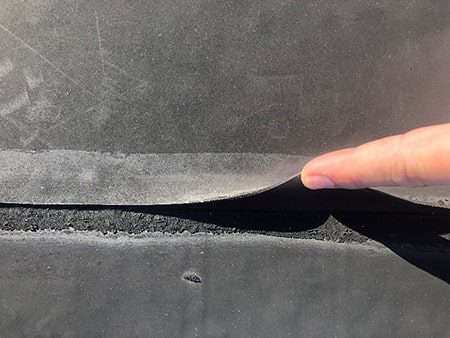
Here are some of the negatives about metal roofing systems:
- Metal roofs have seams and fasteners, just like a single-ply roof system. Some metal roofs have thousands and thousands of fasteners. If the roof ever leaks, it will be tough to determine which seams or fastener allows water into the roof.
- Metal roofs are the most expensive roof systems out there. As of May 2023, they will likely exceed $12 per square foot for a new install.
- Metal roofs don’t provide any R-value. The R-value is made through the insulation below.
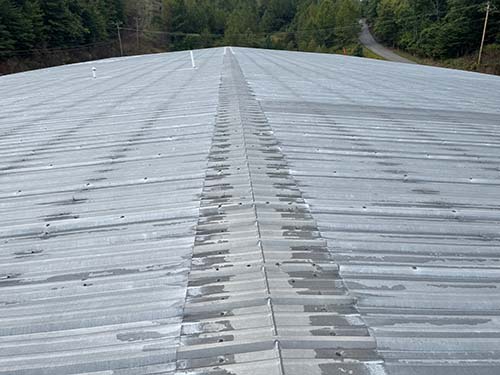
What problems to look out for in spray foam or coating installations
The #1 problem with spray foam and coating installations is inferior installations. Spraying foam is more complicated than rolling a rubber sheet and fastening it down.
Here are some installation issues that spray foam and coating systems can face:
- The roof is improperly prepared before installation. For example, installing foam over wet insulation will damage the foam roof after some time. Water will evaporate and cause bubbles or blisters. An unethical contractor could skip removing and replacing wet insulation to cut down on costs. This will leave the building owner with a roof with issues soon.
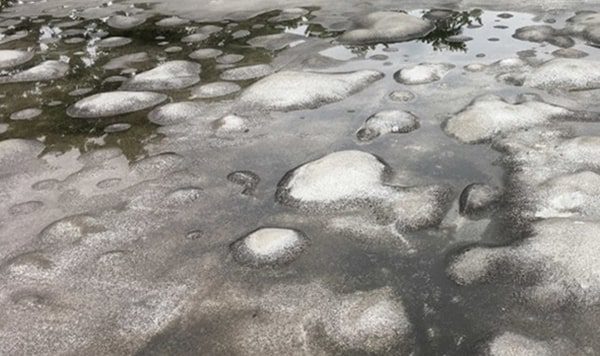
- The installer doesn’t understand the chemistry of spray polyurethane foam. There is heating, mixing, and curing of two materials (a polyol resin and an isocyanate). These are the A and B materials that produce closed-cell spray foam. Many adjustments will need to happen during installation. For example, spraying foam in the morning instead of the afternoon is different. The roof temperature can be much hotter in the afternoon. This requires an adjustment to the temperature the foam is heated up to before it gets to the surface. Not knowing this will produce an inferior product.
- Not spraying the proper amount of foam. Spray foam must be installed at least 1” thick to work correctly. Spraying the correct thickness of foam to produce the appropriate slope so that rain runs toward the drains is another skill. Water that has no chance of running off the roof will cause issues with the roof membrane.
Does the existing roof system influence the best option?
Yes.
Spray foam can go directly over most existing roofs. Sometimes if the adhesion between foam and the existing roof isn’t perfect, a coverboard is installed first.
A roof coating system is not a great option if you have a gravel-built-up roof. Since there are crevices and voids from the embedded gravel in the roof, a significant amount of coating would be needed to fill them all in and produce a proper seal. In this case, a spray foam roof would be much more cost-effective.
Here’s a finished photo of spray foam over an existing gravel-built-up roof:
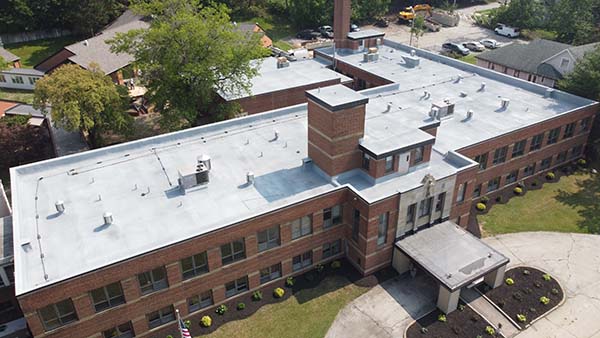
The quality of the contractor
Even though the spray foam and coating roof system has many advantages, it still won’t work right if installed incorrectly.
A single-ply or metal roof can work perfectly if it’s installed right.
Keep in mind the quality of the contractor.
- How long have they been in business?
- What case studies do they have?
- What references do they have?
Here’s one thing to keep in mind. Ask a contractor to give you the contact information for a building owner in the same position you were in 10 years ago.
Say you have a rubber roof and are considering installing spray foam. Ask the contractor for a reference for a rubber roof with spray foam installed 10 years ago. Is it still going strong today?
If you have any questions about the best option to fix a flat commercial roof, contact a few different contractors and compare their solutions.
What’s next?
Here are some common questions we hear: