Quick summary: Spray foam can be installed over any existing roofing system. It can also go over flat, sloped, and irregular-shaped roofs. Since spray foam is fluid-applied, it can be installed around any pipe, skylight, or drain quickly. It can go up, over, and down any vertical wall in one continuous application. A spray foam roof can be renewed over and over again, meaning it likely will be the last roofing system you ever install on your building.
Perhaps this is your first time hearing about a spray polyurethane foam roofing system? If so, you’re probably wondering what’s so great about it?
In this article, you’ll learn the capabilities of a spray foam roof, including:
- How foam can be installed over any existing roofing system
- How it’s easily installed around any penetration (and why this matters)
- How it seamlessly goes up, over, and down walls
- Why being seamless is a big deal
- How a foam roof can be renewed over and over again
And just so you’re aware, West Roofing Systems has been applying spray polyurethane foam since 1979. There have been many changes to building codes, R-values, blowing agents in the spray foam product, etc. To explain the capabilities of spray foam, one must be in the field for a long time.
This article has been reviewed, edited, and approved for publishing by a spray foam roofing expert with more than 30 years of experience.
Let’s get started.
How spray foam can be installed over any existing roofing system
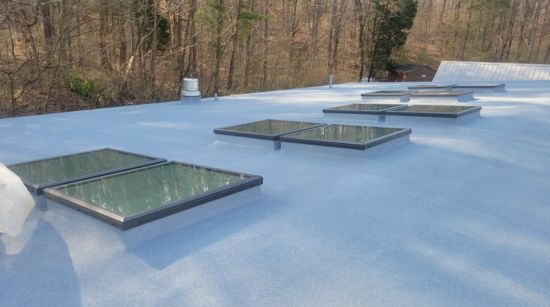
Spray foam can be installed over an existing TPO, EPDM, PVC, Metal, Smooth or Granulated Built-up, Smooth or Granulated Modified Bitumen, or Shingle roofing systems
There are some added details for some roofing systems.
- On a ballasted roof (a roof with loose rock on top), the loose rocks need to be removed first. Spray foam needs a fully-adhered surface for the foam to attach to.
- Depending on the condition of a TPO, EPDM, or PVC roof, sometimes a coverboard needs to be installed first before installing foam. Spray foam needs to have excellent adhesion to the surface below.
- No roofing system should be installed over wet insulation. An ethical roofing contractor will identify these areas, remove and replace the wet insulation, and install a similar material in its place. Then a roofing system can be installed. Spray foam roofs are installed the same way.
- Per building code, the maximum number of roofing systems a building can have is two. If a roof already has two roofing systems installed, at least one system must be completely removed before a spray foam roof can be installed.
99% of the time, spray foam is installed over an existing roofing system. It’s meant to greatly improve the existing roof with minimal tear-off.
Minimizing tear-off is the easiest way to reduce the cost of a roofing project.
How spray foam is easily installed around penetrations
Since spray foam is fluid-applied, it can easily be installed around penetrations, such as:
- Pipes
- HVAC units
- Drains
- Skylights
- Curbs
- Ductwork
Anything that comes through the roof is considered a “penetration.” Spray foam is simply sprayed around its base.
Here’s a photo of spray foam being installed around a penetration:
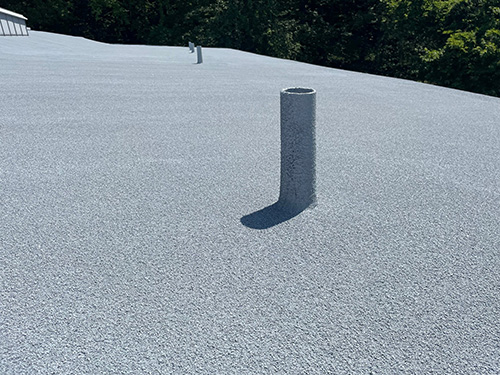
Why does this matter to a building owner?
The spray application reduces labor hours. Any other roofing system needs to be custom cut, sealants must be used, and so on for the penetration to be watertight. Every penetration interrupts the install, adding time and cost to a project.
One penetration could take 30 minutes to roof around with a single-ply system. For spray foam, it would be installed in 1 minute.
And besides reducing labor hours, you must consider the added room for installer error. On a single-ply roof, the sheet must be cut and termination metal and adhesives are used. More parts, more steps, more room for error.
I’m not saying a single-ply roof can’t work around a roof with penetrations, but there’s significantly more room for an installation error than a foam system.
NOTE: Some roofs have hundreds of penetrations or have difficult areas to roof around (see below). The ease of installation must be considered when choosing a roofing system.
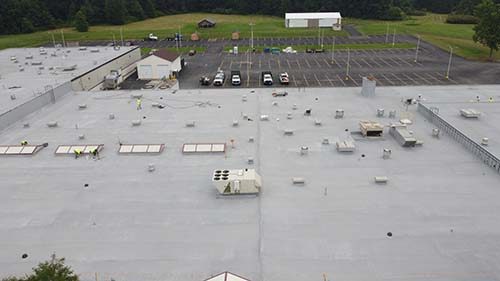
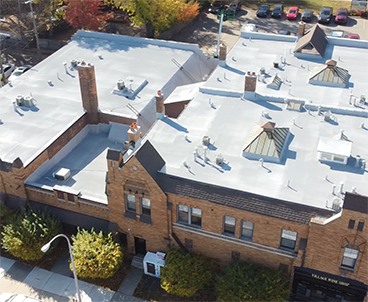
How does spray foam seamlessly goes up, over, and down walls
Since spray foam is fluid-applied, an installer simply sprays the foam up, over, and down any wall. It doesn’t matter what size the wall is. The membrane is 100% continuous. There are no fasteners used in a spray foam installation.
Why would a building owner care about a continuous membrane over a wall?
Well, it’s kind of two-fold.
Using foam is much easier to install than other roofing systems, which need more materials and more time to correctly install a roof up a vertical wall.
More materials = more opportunities for a faulty installation.
More time = more labor hours = higher project cost.
Why is a seamless membrane a big deal?
A seamless membrane is a big deal for two reasons:
- It’s easy to maintain. If there are cracks or punctures in the membrane, they will be easy to locate and fix.
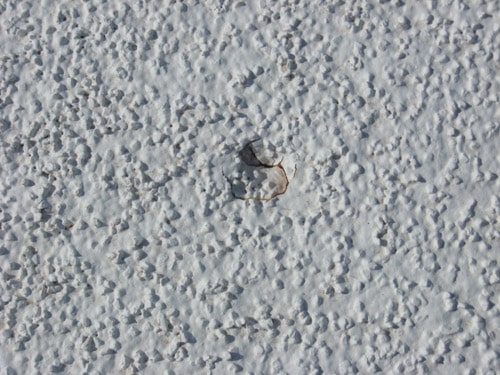
On a roof with thousands of fasteners, it’s very difficult to determine which of them are creating issues.
- It keeps more of the heat/cool inside of the building. There are no fasteners or seams where air can escape through.
Take a look at this roof. You can see heat is clearly escaping through the fasteners:

When heat/cool escapes through the roof, energy costs increase.
How is a spray foam roof capable of being renewed?
The spray foam roofing system consists of four parts:
- Spray polyurethane foam
- Base coat of coating
- Top coat of coating
- Embedded granules (optional)
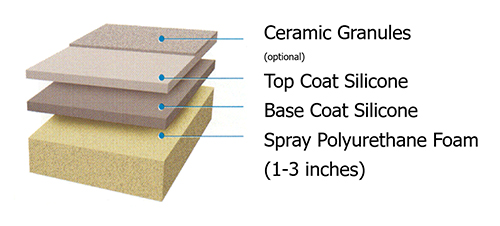
A spray foam roof can be renewed because of the coating. The coating naturally wears away over time and can be reapplied. The spray foam section never loses R-value, waterproofing, or any other type of performance.
Here’s a common example:
A building owner has a rubber roof at the end of its lifetime. Instead of a complete tear-off, they install a spray foam roof.
Spray foam is applied 2” around the perimeter and penetrations and 1” everywhere else. The owner decides they would like a 15-year warranty.
The warranty on a spray foam roof is always determined by the thickness of the coating. Most owners choose a 10, 15, or 20-year warranty. Let’s just say, in this case, a 15-year warranty is desired. For a 15-year warranty, 25 mils of coating would be installed (in two separate coats) over the spray foam roof.
Over time, the coating naturally wears away. In year 15, 5-6 mils of coating could still be present. At this time, a contractor can clean the roof, install 25 mils of coating, and grant a new 15-year warranty.
This process can be repeated over and over again.
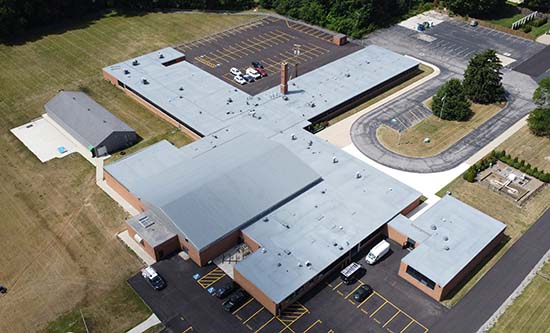
Why would a building owner care about a renewable roofing system?
Having a renewable roof reduces lifetime costs. A “roof renewal” costs 33% – 50% of the original installation. At the end of a single-ply or metal roof’s life, it will most likely need to be 100% ripped off and replaced. A new roof will cost 100% of the original installation (or more because of labor costs with tear-off, transporting the material, and landfill fees disposing of the old roof).
Here are some other articles building owners may be interested in: