Quick Answer: Industry standards require no water area to exceed 100 square feet at ½” deep after 24 hours of dry conditions.
Perhaps you’re wondering how commercial roofing contractors install the right amount of slope.
In this article, we’ll cover:
- How fluid-applied roofing systems are installed with the right amount of slope
- How non-fluid-applied roofing systems are installed with the right amount of slope
- What’s the cost difference in how they achieve proper sloping?
And just so you’re aware, West Roofing Systems has been in commercial roofing since 1979. We’ve seen millions and millions of square feet of commercial roofing systems. All different kinds with various problems.
One problem that we often face is, “You guys install a spray foam roof or a roof coating system, both of which are fluid-applied, so if a roof has sloping issues, how do you fix that with a liquid product?”
This article has been reviewed, edited, and approved for publishing by a commercial roofing expert with more than 30 years of experience.
Let’s get started!
How are fluid-applied roofing systems installed with the correct slope?
What is a fluid-applied roofing system anyways?
Spray polyurethane foam roofing
Spray foam (or SPF) is a 1-1 ratio of two chemicals that produce a foam. The foam cures and hardens, and rises a minimum of 1 inch. The thickness can be adjusted by installing more or less product.
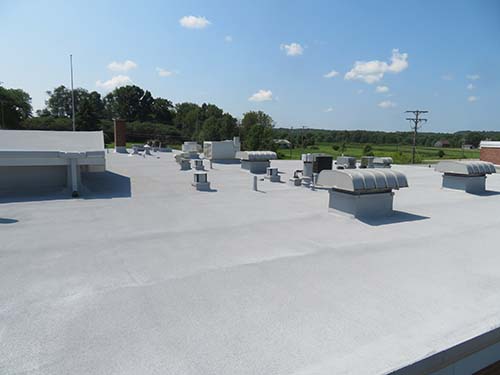
Roof coating systems
A roof coating system is a super thick paint engineered to withstand weathering elements. Roof coatings can be urethanes, silicones, or acrylics. They can be sprayed out of a gun or rolled on, depending on the amount of wind. The thickness can be adjusted by installing more or less product.
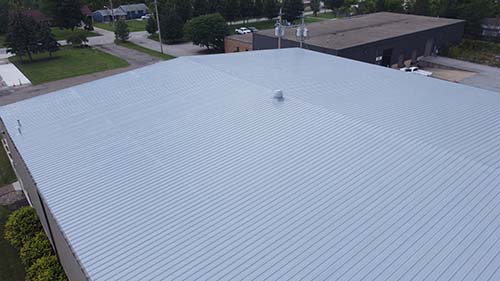
So, how are fluid-applied roofing systems installed with the right thickness to ensure the right amount of slope?
It’s simple…and it’s not simple.
The simple answer is to install more or less of the product, and you’ll have proper sloping.
The not-so-simple answer is spray foam needs to be installed at 1” thick at a minimum to maximize its performance.
If you have a drain (the lowest point of a roof), the foam will need to taper from that point to the perimeter.
A simple example can be 2” thickness at the perimeter and 1” at the drains.
A contractor with experience will constantly monitor the thickness of the product they are installing to ensure proper sloping.
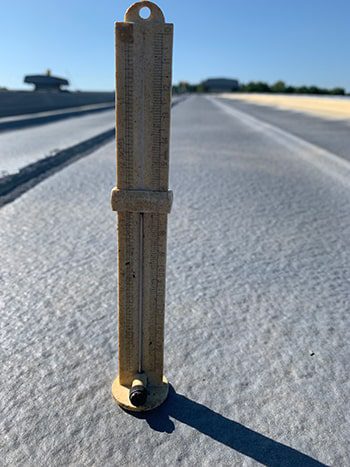
Depending on how the warranty is structured, a third-party (most likely the manufacturer of the products installed) will monitor the installation and perform their own thickness tests.
They will not grant a warranty unless they are 100% sure there’s enough slope to prevent ponding/standing water.
How are non-fluid-applied roofing systems installed with the right thickness to ensure the right amount of slope?
Since non-fluid-applied roofing systems are flat, they use the insulation below the membrane to influence the slope.
They can install different thickness levels of insulation to where there’s proper sloping towards a drain.
Let’s say there’s 100 feet from the perimeter of a roof to a drain.
- At the drain, the insulation is installed at 1” thick.
- 50 feet away, the insulation is installed at 1.5” thick.
- And at the perimeter, the insulation can be 2” thick.
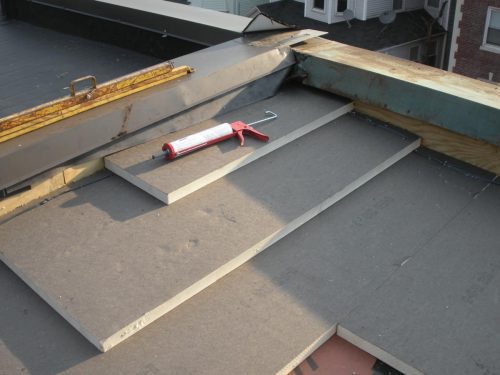
Is there a cost difference in how these two roofing systems achieve proper sloping?
Yes! Huge difference.
The problem with non-fluid-applied systems is that you must remove the existing membrane to install the new insulation. This is much more costly than a fluid-applied roofing system, which can be installed over the existing membrane.
Going with a fluid-applied product eliminates tear-off and extra labor hours, as well as landfill costs and contributions.
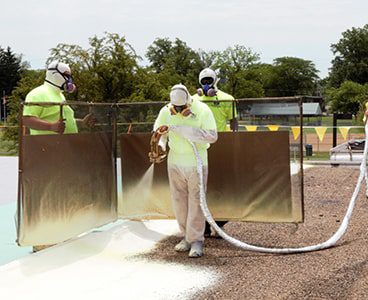
Conclusion
Hopefully, you learned how each roofing system could achieve proper sloping.
While a fluid-applied roofing system can achieve proper sloping more cost-effectively, it can be harder to accomplish if the contractor isn’t an expert in applying the system.
Want to learn more?
Here are some popular articles: