If you’ve seen a bright white roof, you may be familiar with TPO roofing. As one of the most common roof types of commercial facilities, TPO has some of the best energy savings in commercial roofing.
This article covers everything you need to know about TPO roofing, including:
- What is TPO?
- What insulation options do you have with a TPO roof?
- How much does a TPO roof cost (and the factors that make the price go up or down)
- What advantages does TPO have over other roofing systems?
- How does TPO save money?
- How is a TPO roof repaired?
- How existing TPO roofs (with less than 25% saturated insulation) are repaired or restored
- How existing TPO roofs (with more than 25% saturated insulation) are repaired or restored
At the end, there’s an option to download a free eBook that compares the pros and cons of all commercial roofing systems (TPO, EPDM, Spray Foam, Roof Coating Systems, Metal, BUR, etc.)
What Is TPO?
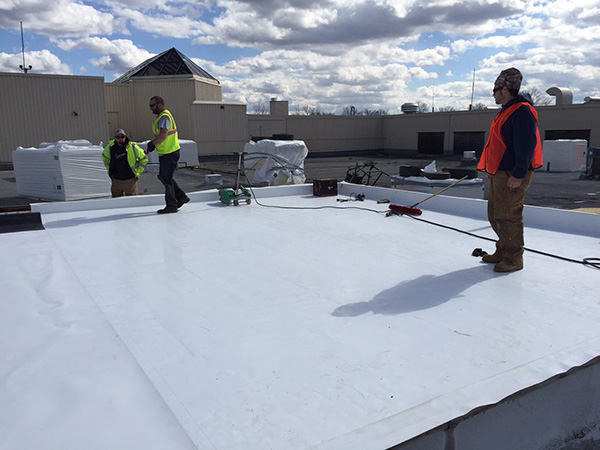
Thermoplastic Polyolefin is a single-ply roofing membrane that is one of the fastest-growing commercial roofing systems on the market. TPO roofing systems are a single layer of synthetics and reinforcing scrim used to cover flat roofs.
TPO membranes are manufactured in sheets 10, 12, or 20 feet wide. They are then rolled up and taken to the commercial facility.
TPO has gained industry acceptance because of its naturally reflective surface, which reflects UV rays. The National Roofing Contractors Association (NRCA) reported that TPO has about 40% of the commercial roofing market share.
TPO Roofing Installation
After the existing substrate is prepared, either by cleaning or removing the existing roof, the insulation is installed. There are a few types of insulation options the facility manager/owner can choose from:
- Polyisocyanurate (Polyiso) – The most used insulation type for roofing applications, Polyiso is more expensive but pays off with a higher R-value rating.
- Expanded Polystyrene (EPS)—With the highest R-value per dollar, EPS is used for roof, wall, and floor insulation. It can be used for ground contact and does not retain water over time.
- Extruded Polystyrene (XPS)—Usually defined by its blue, green, or pink color, XPS falls between Polyiso and EPS in price and performance ranges. It is semipermeable and has a perm rating of 1.
The TPO membrane can be attached to the cover board with a bonding adhesive or mechanically fastened. When the membrane is rolled out, the contractor returns and uses a hot-air gun to weld the seams together.
Here’s a video of a TPO roof being installed:
TPO Roofing Costs
An average 20,000 sq. foot commercial roof usually costs between $5 and $10 per square foot in materials and labor to install a typical TPO roofing system.
However, prices today (April 2025) are higher. A $6 – $12 per square foot range is more likely. The costs for all roofing materials are very volatile.
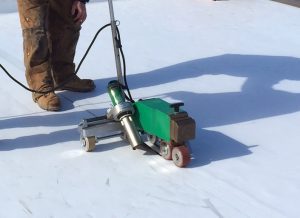
All of these factors influence price:
- The size of your roof
- The condition of the existing roof
- Access to the roof
- Insulation choice
- Membrane choice
- Installation choice
- Roof penetrations
- Type of warranty
Advantages of TPO Roofing
A commercial single-ply membrane roof can last 30 years if properly installed and maintained. There are quite a few other benefits of single-ply membrane roofing systems:
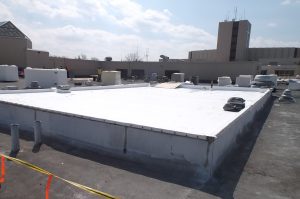
- Class A Fire-Rated – TPO membranes and EPDM can achieve Underwriters Laboratories (UL) Class A fire resistance listings by adding fire retardant chemicals during manufacturing.
- Customer Choice of Insulation—Since single-ply does not include the insulation factor, customers have more options to insulate their facility’s roof.
- Reflective or Retentive – TPO is generally white and highly reflective. On the other side of the spectrum, EPDM is often described as “Black Roofs” due to the naturally dark color of the membrane.
How TPO Roofing Saves Money
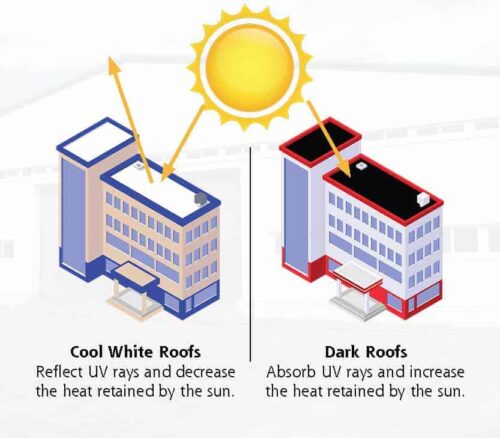
The most common TPO material is bright white, which has highly reflective properties. A bright white roof installation can reflect UV rays and heat from the building, saving money during the summer months by decreasing energy usage to cool the interior.
How is a TPO roof repaired?
A TPO will last approximately 15-20 years. During this time, seams can rip apart, flashings can fail, the membrane can become punctured, etc., which will cause a roof leak.
Water entering the building is the first sign of a TPO roof needing repair. This usually happens when seams lose adhesion, allowing water to enter the roofing insulation.
Once the insulation accumulates enough water, it enters your roofing deck and eventually starts leaking inside your building.
At this stage, it’s time to call a commercial roofing contractor to perform a roofing inspection.
During the inspection, a roofing contractor will be able to tell:
- Where water is coming through the membrane
- How much of the insulation is wet
- How old is the TPO roof
- How many layers does the roof have
- What condition are the seams in
What comes out of this conversation is the building owner’s repair options. Say the roof is 12 years old, and the seams are slightly uplifted, like this:
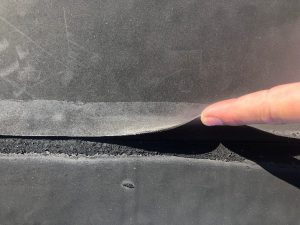
On this roof, the seams are getting close to failure. If something isn’t done now (or very soon), with every wind gust, the seams separate further, allowing more water to enter the insulation.
A roofing contractor will perform an infrared inspection to check the amount of insulation’s saturation.
They will come to your roof about 30 minutes after the sun goes down. At this time, the roof’s surface will be cooler than the water saturated in your insulation.
The infrared camera will detect the heat difference, and the contractor will mark those areas with spray paint.
Repair options if your TPO roof has less than 25% saturation
After the complete infrared survey, it’s determined that the roof doesn’t have much saturation. If your roof is under 25% saturated, then what can be performed is a silicone restoration membrane system.
What will happen during a silicone restoration membrane installation is:
- The saturated areas will be removed and replaced with similar material
- The entire field of the roof will be power-washed and cleaned
- The seams of the TPO roof will be strengthened and reinforced
- Silicone coating will be applied to the entire field of the roof
- Then a new 10-20-year warranty will be granted
Here’s a video showing a silicone restoration membrane installation from start to finish:
Another scenario is that although there’s less than 25% saturation, the seams are in too bad a condition to be restored with a silicone restoration system.
In this case, if there’s only one roofing system, install a cover board over the TPO roof, cut the flashings off, and then install a spray foam roofing system. This will save money from completely tearing off the existing roof and installing a new TPO system.
If you already have two roofing layers and the seams are in too bad of a condition to restore, you’ll need to remove all the TPO and install a new roofing system.
Repair options if your TPO roof has more than 25% saturation
After the complete infrared inspection, it’s determined that the roof has excessive saturation. The roof is in too bad a shape to restore. In this situation, a silicone restoration membrane system isn’t beneficial.
Unfortunately, removing all the TPO and insulation and revealing the roofing deck is the only choice.
You can now install a new TPO system. However, trying a different roofing system might be cost-effective after what happened last time.
One recommendation is a spray foam roofing system.
Why?
- Spray foam has the greatest R-value per square inch of thickness of any roofing system.
- Spray foam is a renewable roofing system. You can recoat the roof after 10-20 years and keep the warranty going. Recoating a roof is less expensive than a complete tear-off.
- Spray foam is a seamless system. Seams are where most roof leaks occur.
- There are no fasteners used when installing a spray foam roofing system. Fasteners can back out or be installed wrong, creating a water entry point.
A spray foam roofing system has more advantages, including how easily it can be installed.
On a TPO roof that needed to be torn off, a spray foam roofing contractor could install a cover board and spray foam over that.
Here’s a video of a spray foam roofing installation from start to finish:
If there’s anything you can take away from this section, the saturation level of the insulation determines which repair options you can take.
If more than 25% of your roof is saturated, you’ll need to do a complete tear-off and get all that wet insulation off your roof. If you’re less than 25% saturated, you have more options.
It’s cost-effective to catch repairs early before they cause too much damage.
Next Steps? How does TPO compare with other commercial roofing systems?
In our free guide, you’ll learn the pros and cons of the most popular commercial roofing systems out there, including:
- Single-ply
- Spray foam
- Metal
- Roof coating systems
- Built-ups
- Shingle