Are you a building owner who’s doing their research on commercial roofing options?
If so, we’re happy you considered learning about spray polyurethane foam roofing.
Many people hear about the benefits, such as:
- Spray foam roofs are seamless (most leaks begin at the seams)
- Spray foam roofs have the greatest R-value of any roofing material (reduces your energy costs)
- Spray foam roofs are renewable (you can recoat them after 10-20 years and the roof is back to 100%)
However, most building owners don’t consider when the actual installation can be performed.
There are plenty of restrictions that limited the window of installation of a spray foam roof, and that’s what we’ll get into today.
For over 40 years, West Roofing Systems has dealt with these installation obstacles and still manages to properly install over 100 commercial spray foam roofs every year.
Before we get started, I wanted to paint the picture of a scenario.
You, as the building owner, have already chosen spray foam as your roofing choice. The roofing contractor has already performed an infrared inspection, which identified that 10% of your commercial roof had water saturated underneath your top roofing layer.
Those areas have been removed and replaced with like material. The roof has been power washed and cleaned.
Tomorrow is supposed to be installation day, until one of these scenarios pop up, which will push back your install date…
Enter restriction #1…
Rainfall the night before will delay a spray foam installation
Let’s say it rained the night before your installation was to begin.
For spray polyurethane foam to adhere to your roof correctly, and for the foam to cure and settle properly, the roofing surface needs to be completely dry.
Without getting to “science-y”, if there’s ANY water left on your roof, the water will react with the spray foam material and greatly reduces its effectiveness.
A roofing contractor will start by using a broom to remove the bulk of the water off the roof, then they will use what’s called “air-lancing” to dry the field of the roof.
Air-lancing is the process of using compressed air to remove an object. In roofing, it’s used in pressures up to 100 PSI to remove water from a roof quickly.
Once air-lancing is complete, the installation of your spray foam roof will begin.
This process will work on all existing roof substrates besides gravel built-up.
NOTE: On a gravel built-up roof, extra measures need to be used to get your roof dry because of its loose surface. The most used option is to use a propane gas blow torch to get underneath and around all the loose gravel.
Rainfall during the job will delay a spray foam installation
During the actual installation, the foreman needs to keep a constant eye on potential rainfall.
Just because it says there’s a 10% chance of rain today, doesn’t guarantee a dry day to spray foam.
If there’s a chance of rain, the roofing contractor will spray foam in small sections as to make sure which ever areas are foamed, that coating is immediately applied on top.
If you’re unaware, spray polyurethane foam degrades with UV rays, therefore coating is sprayed (or rolled) over top of the foam to protect it.
If rain does come down over foam, the project is stopped for that day. The next day, the crew will need to identify if any of the foam is damaged and re-spray those areas if necessary.
A roofing contractor always tries to get coating installed over foam during the same day the foam was sprayed. Coating withstands rain very well, and it dries much easier the next day due to its darker color (usually gray).
Coating needs around 2 hours to completely dry. If rain comes down 20 minutes after it’s applied, the contractor will need to dry those areas and re-apply the coating.
If there’s a high chance of rain (more than 50%), then your spray foam roofing project will be delayed until the next dry day.
What temperature does it have to be to install a spray foam roof?
The ambient temperature cannot be below 50 degrees Fahrenheit.
For spray foam to adhere and cure correctly, the surface it’s sprayed onto needs to be at least 50 degrees Fahrenheit.
Ambient air temperature is the temperature that’s in the air (the one reported on the news). Ambient air temperature is usually colder than the roof temperature because the roof absorbs the sun’s light.
To share a quick example, there were times last Summer where it was 90 degrees “ambient”, but over 180 degrees on a black roof.
What if it’s 45 degrees “ambient”?
If the temperature is close to 50 degrees ambient, a spray foam roofing contractor will perform detail work around parapet walls, flashings, and penetrations until it gets warmer later in the day.
But other than that, the field of the roof will not be sprayed with foam until we’re 100% sure it’s more than 50 degrees.
Are there any restrictions with silicone roof coatings?
The only restriction with the silicone roof coating that’s installed over spray foam is that the surface cannot be freezing upon application.
Since a roofing contractor always wants to install coating over top of spray foam on the same day, worrying about temperature restrictions with silicone coating is usually non-existent.
Can spray foam be installed when there are high winds?
One of the problems with spray foam roofing is overspray. Since spray foam is fluid-applied, it’s a very light material that can be taken for a ride with high winds. You can see how “light” spray foam looks upon application:
Overspray is an issue because the material can land upon cars, windows, etc. To combat overspray, a roofing contractor (in addition to covering vehicles) has three levels of defense:
Use of windscreens
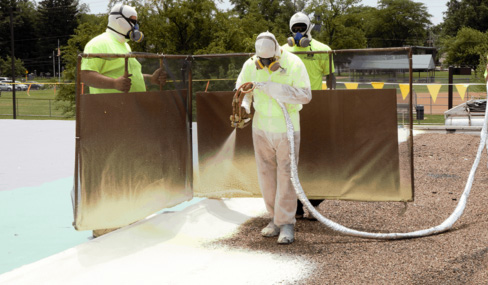
Windscreens are in every work truck. When we see that foam is going off course, or we’re spraying near an edge, roofers will hold windscreens to make sure all the spray foam stays on the roof. If the wind is worse, a roofing contractor will use…
A spray foam booth
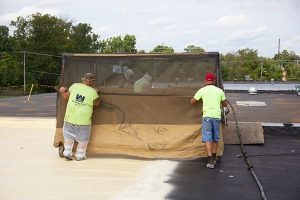
A spray foam booth creates a perimeter around the sprayer to contain the spray foam from “winding” off. And if the booth isn’t working properly, we’ll use…
A spray foam booth lined with burlap
This is the ultimate weapon against overspray. Burlap is lined around the perimeter of the spray foam booth. If overspray still exists, the project is stopped until the wind dies down.
Overspray can always be removed and if foam gets onto a vehicle, a roofing contractor will pay for the detailing of that vehicle.
Contractors don’t want to go through this hassle, which is the project is delayed if wind is too severe.
Can you spray foam when there are large gatherings on a property?
A scenario that happens often is that a school will schedule a spray foam roofing project in the Summer. This is because school buses, students, and teachers are away from the property.
But then next week, football tryouts are taking place, and the week after that, the city fair is going to be set up in the school’s parking lot.
Events like these will halt a spray foam roofing project. The risk of overspray is too much when there are hundreds of people close to the building, or expensive assets (roller coasters) too close to the roof.
Having these events occur on the same week a roofing project is going happening is rare, but it’s certainly something that will come up with your roofing contractor when scheduling your project.
Have any other questions about spray foam roofing restrictions?
If you have any other questions, please contact us and we’ll answer them ASAP. There’s an email address (info@westroofingsystems.com) that gets monitored 8-5pm M-F as well as a form that gets monitored by me (the author) so I’ll answer your questions as fast as I can.
One last nugget of advice before I let you go…it’s beneficial to the building owner to schedule a commercial roofing project in advance.
If you wait until the end of roofing season (September/October) and you’re one of 20 buildings that waited until the last minute to start your project. The roofing contractor can increase their price. It’s just simple supply and demand.
So, if you have plans of getting your roof done this year, fill out a quote form and get your project booked well in advance. (Yes, I monitor quote forms too ?)
Better pricing, no events going on, and hopefully the weather’s good!