Let’s say that you’re a property owner who’s researching a new roof. You come across a term, such as “R-Value” and you wonder:
“How much R-value do I need?”
“Which roofing system will give me the best R-value?”
“I’ve heard of a spray foam roof, but how much R-Value will that provide?”
We will answer all of these questions in this article.
Let’s begin.
How much R-value does spray polyurethane foam provide?
Spray polyurethane foam has an average R-value of 6.5 per inch of thickness. If you install 3 inches of spray foam on a roof, it will gain an R-value of approximately 19.5 (6.5 x 3).
If a roof already has an R-value of 10 based on the existing underlying insulation, and you install 3 inches of spray foam overtop, the roof will then have a new R-value of 29.5.
10 + 19.5 = 29.5.
Property owners who want to install a spray foam roof, usually fall into two categories:
- Ones who have a roof that can be repaired, and then have spray foam installed over the existing roof assembly.
- Ones where the roof needs to be completely removed down to the deck, and then install a new spray foam roof.
Let’s get into the details of each scenario.
What is the R-value when spray foam is installed over an existing roof?
You may have a roof that’s already in good condition, to where it makes sense to keep the majority of the existing roof assembly and install a spray foam roofing system over top.
In some cases, 90% of the insulation will be dry and only 10% will be damaged/wet.
So why throw away 100% of a roof where 90% of it is performing well?
If you’re considering a spray foam roof, one of the first steps is to have your roof inspected by a professional roofing contractor.
Then, if needed, an infrared inspection can be performed to see how much of the roof’s insulation is saturated.
When the seams and field of the roof are in good condition, there’s no standing water, and after a few core samples are pulled in areas where saturation could be (usually reported leak areas and low spots), there’s no saturation detected.
In this case, there’s no need for an infrared inspection. The spray foam installation process can begin.
In most cases, roofs will have some saturated areas that need to be removed before spray foam can be installed. It’s not good roofing practice (financially and performance-wise) to install any roofing system over wet insulation.
In these cases, you’d take what R-value the roof currently has, and then add 6.5 to it for each inch of spray foam installed.
Here are the R-values of the most popular roof membranes and insulations (per inch of thickness):
- Spray polyurethane foam: 6.5
- XPS: 5.0 – 5.5
- EPS: 3.85 – 4.5
- Polyiso: 5.5
- TPO: 0.24
- EPDM: 0.33
A common example is a commercial roof with an R-value of around 11. This could be 2 inches of Polyiso board and a single sheet of EPDM.
If the roof is in good condition and an average of two inches of spray foam is installed over top, the new roof will have an R-value of around 24.
11 + 6.5 + 6.5 = 24
But what happens if the roof is not in good condition? How is the R-value of a roof calculated when the entire roof needs to be replaced?
What is the R-value of a spray foam roof where the existing roof is removed?
There are some instances where it’s beneficial to remove the entire roof and start over, such as:
- There’s a high level of saturation in the insulation (high level = more than 25%)
- The existing roof is old, signs of deterioration throughout the existing roof assembly
- The roof is constantly having issues with leaks
- The roof is not providing enough energy savings, due to wet underlying insulation
If you remove the existing membrane and the existing insulation, your roofing project is considered new construction.
Having a project be considered new construction means that in order to comply with building codes, a minimum R-value will need to be achieved.
Below is a map of the US showing what R-value is needed in each region.
Your first step is to determine which region (1 through 7) that your building is in.
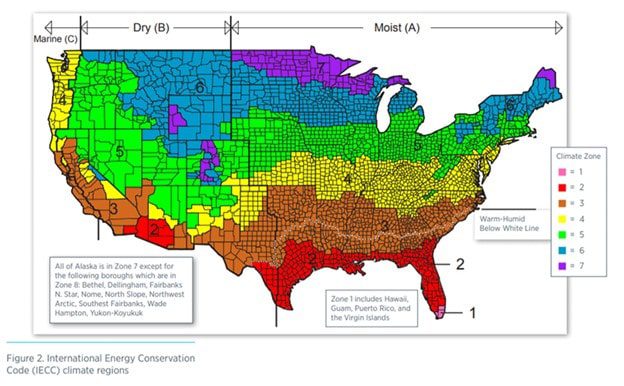
Then look at the chart below to see what the minimum R-value requirement is.
NOTE: Group R is for residential occupancies, hotels, motels, or boarding houses.

For example, commercial roofs in Cleveland, Ohio need a minimum R-value of 25. (Group 5)
A commercial roof in Jacksonville, Florida would need a minimum R-value of 20. (Group 2)
Since your roof is completely removed, you start with an R-value of zero.
Each inch of spray foam that’s installed on your roof would add 6.5 to your roof’s R-value.
How much R-value is cost-effective for your commercial roof?
Say you live in Cleveland, Ohio, and you know you need to get a minimum R-value of 25.
What if you want to achieve a higher R-Value?
Is there a point where the cost of installing more underlying insulation and spray foam isn’t beneficial to the property owner?
Yes, once you achieved the recommended R-Value, anything above that value would not be very economical.
Many variables determine the right amount of R-value for your specific building, such as:
- Building code requirements
- How many people are coming in and out of your building?
- How much heating and cooling is lost throughout your building?
- What climate/location is your building in?
- How efficient is your HVAC unit, is it running constantly to heat and cool your building?
Anything above the measurements above, and the cost to install additional spray foam wouldn’t exceed the energy savings the additional spray foam would provide.
If that were the case, facilities would install so much spray foam on their roof that the HVAC unit would only be needed if a door was opened.
This is unrealistic. No roofing insulation keeps heat/cool in that good.
Besides R-value, why do property owners choose spray foam roofing?
Now that you know what R-value a roof will have after a spray foam installation, what other reasons do property owners install spray foam roofs?
If property owners know they need to get to an R-25, they can accomplish this with other roofing systems besides spray foam.
Most property owners consider other factors about their roofing systems besides initial cost and R-value.
One thing to consider is the probability of a roof leak. Spray foam roofs are seamless, closed-cell, and are installed as one monolithic layer. All these attributes create a roofing system that’s less likely to leak than a traditional roofing system.
Another thing to consider is the cost of the roofing system once the warranty expires.
Spray foam roofs can be renewed (which gives you another 10-20-year warranty) for ½ to 1/3 of the initial installation.
A single-ply roof will most likely need to be torn off and replaced after 10-20 years, which costs 100% of the initial installation cost.
What are your next steps?
Your next step is to learn more about spray foam roofing, as well as other traditional roofing systems. Here are some popular articles:
- What is the cost of spray foam roofing per square foot?
- What problems can spray foam roofs have?
- What are the pros/cons of metal, single-ply, spray foam, and roof coating systems?