Have you ever heard the phrase “A moment on the lips, a lifetime on the hips”? If not, we’re talking about eating a delicious, yet unhealthy food item that tastes great today, but isn’t beneficial for you in the long run.
Similar short-term wins and long-term disappointments have happened in the spray foam roofing universe.
And that is…some roofing contractors think it’s a good idea to apply spray foam over a dry, top surface that has wet insulation underneath.
Yes, bad things will happen (we’ll get into this in more detail later).
At West Roofing Systems, we’ve seen every type of problem and issue with spray foam applications since we’ve been installing spray foam roofs since 1979.
Today we wanted to explain the dangers of spraying foam over wet insulation, how you can be sure your roof insulation isn’t wet, and why some contractors don’t care if they spray foam over wet insulation.
Let’s begin…
Why you should never spray foam over wet insulation
In short, the trapped moisture underneath your spray foam roof will get very hot in the Summer, begin to vapor, and cause a blister while trying to escape your roof. Here’s a photo of multiple blisters on a spray foam roof:
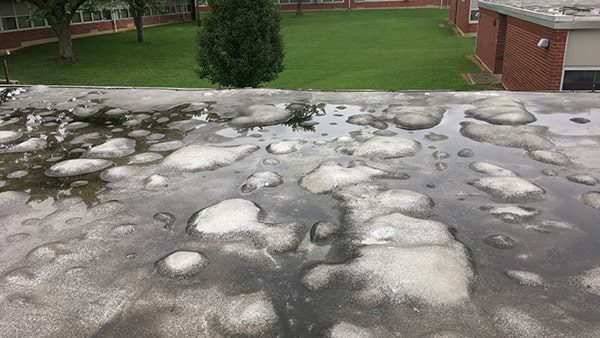
Blisters are major issues for multiple reasons
Reason #1 – A blister creates an uneven roofing surface that interrupts the way water was designed to run off the roof
For example, say your spray foam roof was sprayed 1” thick in the center and 2” near the perimeter. Your spray foam roof was designed that way because you have drains located in the center.
Let’s say you get a few blisters…now water flow has been interrupted.
With water having an unclear path to a drain, you may experience standing water (water that doesn’t flow), which increases the rate your roof will degrade.
Reason #2 – A blister can pop which can eventually lead to a roof leak
A blister that pops on a spray foam roof will not cause an immediate leak, but it will expose the foam to UV rays, which will degrade the foam.
If left untreated for a few weeks, no big deal.
If left untreated for years, that foam could wear all the way down to the substrate where water could enter your building.
How do you tell if your insulation is wet?
A roofing contractor will use what’s called an infrared survey.
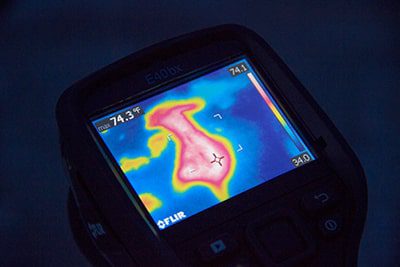
An infrared survey can determine saturation where the naked eye cannot see.
A roofing contractor will come out after dusk, when the roof begins to cool. During this time, the roof will be cool, but the water underneath will still be warm from the day’s sun.
The infrared survey will identify those warmer areas, which is an indication that water is present.
A roofing contractor will mark those areas with spray paint to highlight the saturated areas of the roof that need removed.
Before spray foam can be applied, a roofing contractor will remove those identified saturated areas, transport them to a landfill, and replace those areas with similar materials that were removed.
For example, if an EPDM roof has insulation that’s saturated, a roofing contractor will replace that area with new, similar insulation, then lay down new EPDM over the area.
Why some roofing contractors don’t care if they spray foam over wet insulation
Some roofing contractors will spray foam over wet insulation because once the job is complete, they don’t want anything to do with the roof.
That’s why is very important to choose a roofing contractor that’s been around for a long time, has tons of references, is insured, and is an expert in spraying foam.
The main reason a roofing contractor will spray foam over wet insulation is to win the job by being the lowest bid.
They will become the lowest bid because they won’t have to include the costs of:
- performing an infrared survey
- removing all the saturated areas
- transporting those materials to landfills
- replacing the saturated areas with similar materials
By skipping these important steps, business owners will be left with a blistering roof in the near future.
That’s why it’s important to get quotes from at least 2-3 roofing contractors. Then you can compare apples to apples and figure out why someone might be priced higher or lower than someone else.
Read More: The lies roofing contractors will tell you to win your business.
Your next steps?
There are plenty of issues that come up when a building owner is considering a spray foam roof, such as:
- Can you walk on a spray foam roof?
- Will a spray foam roof hold up against wind?
- What is the estimated install cost of a spray foam roof per square foot?
Hopefully today’s read and the resources above can help you in making the best roofing decision for your building.
If you need anything else, please contact West Roofing Systems at anytime and we’ll respond as fast as we can.