In this article, you’ll learn the pros of spray foam roofing, such as:
- How they have lower installation and lifetime costs than other commercial roofing systems
- They are easy to install (reduces labor costs)
- It has the highest R-value per inch of thickness
- It’s easy to maintain
- It’s seamless
- They are environmentally-friendly
- It has closed-cell properties (which means it won’t leak)
- It’s renewable and sustainable
But nothing’s perfect. We’ll go through the cons as well, such as:
- There are bad spray foam contractors out there
- Overspray is a constant issue
- And it needs to be at least 50 degrees to install
Just so you’re aware, this article has been reviewed, edited, and approved for publishing by a spray foam roofing expert with more than 30 years of experience.
Let’s get started!
Pros of Spray Foam Roofing
Costs
As of July 2024, spray foam roofs costs around $5-$10 per square foot. Many variables influence the cost. The installation cost is in the ballpark of other traditional roofing systems.
Did you know spray foam can be installed over most existing roof systems? This can reduce tear-off costs. It’s also good for the environment, as you won’t be contributing to landfills.
Spray foam roofs can be recoated after their warranty expires, making them a better long-term cost play.
A foam roof can be recoated (or renewed) for 33% – 50% of the installation costs. On a traditional roof that needs to be torn off and replaced after the warranty expires, the cost is 100% of the installation cost.
Easy Installation
The ease of installation can save you time and money. The foam and coating are applied quickly and without interruption to the facility’s daily routine.
Spray foam roofs are installed by spraying a liquid on the existing roof and allowing it to expand into foam.
This process means the foam can conform to all roof shapes and types, even irregularly shaped roofs.
After cleaning the existing roof, the spray foam roof can be applied directly over asphalt, shingles, concrete, metal, and wood.
Here’s a video of a spray foam roof being installed on a school from start to finish:
Energy Efficient
Spray foam roofing delivers thermal, air, and moisture barriers to provide the highest R-value per inch, which means the material offers better insulation for the building.
The polyurethane foam keeps heat out in the summer, in during the winter, lowering energy costs for facility owners. The silicone top coating resists UV light, protecting the foam and reducing heat absorption (emissivity).
Easy Maintenance
Once installed, a spray foam roof requires minimal preventative maintenance and repair. If properly maintained, it can last over 50 years.
Spray foam roofing systems should be inspected semi-annually, in the Spring and again in the Fall. Additional inspections are also suggested following any event that might have caused damage to the system.
If silicone recoating is needed, the existing materials are not torn off; the new coat is applied on top of the current system.
Seamless
Seams and penetrations are the primary sources of leaks in roof systems. Spray foam eliminates this vulnerability. Since the spray foam mixture is applied as a liquid, it can fill gaps, seams, and cracks in the existing roof and substrate.
Applying the polyurethane foam allows the contractor to level out the roof to decrease the chance of ponding water.
The foam material can expand and contract with the building per outside temperatures, reducing the likelihood of cracks and splitting.
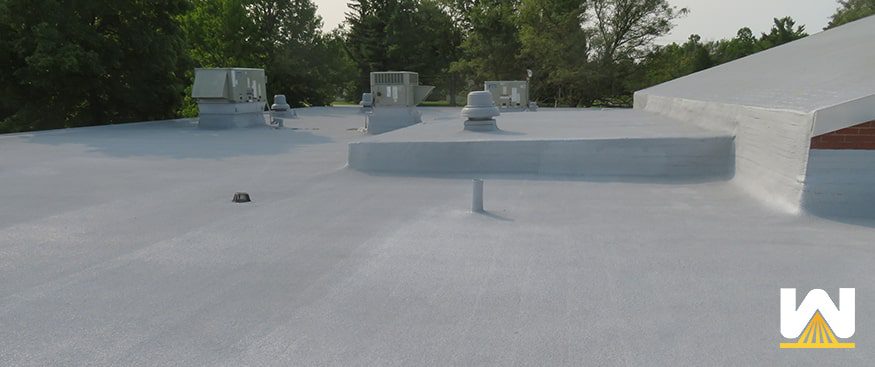
Traditional roofing systems need to cut the membrane, use adhesives, termination metal, screws, fasteners, etc. to make penetrations watertight. An example of a penetration is an HVAC unit, skylight, pipe, or anything that comes through the roof.
With spray foam being fluid-applied, none of those materials are needed. The foam is sprayed around the penetration, and it becomes watertight.
Watch this video in our training center on how foam can make a box (simulating a penetration) watertight by becoming a part of the flat roofing area:
Environmentally-Friendly
Spray foam roofs create little to no waste during their lifetime. In most cases, there is minimal stripping of the original roof, as only the wet and saturated areas are removed.
A spray foam roof is installed on top, eliminating the need for costly roof tear-offs and waste.
The materials that are used for spray foam roofing systems are also environmentally friendly:
- Zero Ozone Depleting Potential (ODP)
- Low in the Emission of Volatile Organic Compounds (VOCS)
- Free from Chlorofluorocarbons (CFCS)
- Ultra-Low Global Warming Potential (GWP)
Closed-cell properties
If a spray foam roof gets a cut, puncture, or hole, it will not leak. That’s because of the foam’s closed-cell structure. Water will sit in a hole and not move further south into the roofing system:
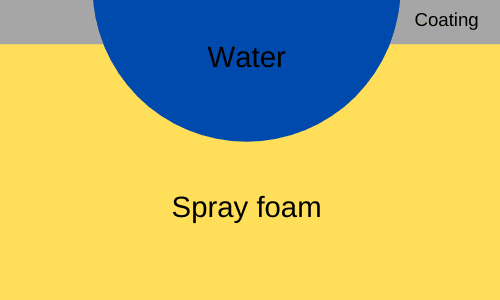
The opposite is true with polyiso board or other commonly used insulation wood types. These types of insulation have open-cell properties, which means the water can travel vertically and horizontally, saturating more roofing material.
Even if there’s a slight uplift (or puncture) in a single-ply’s membrane, if water can get into the insulation, it will travel and saturate more of the insulation. This can lead to a labor-intensive repair and water coming into your building.
Renewable and Sustainable
The spray foam roofing system has four parts:
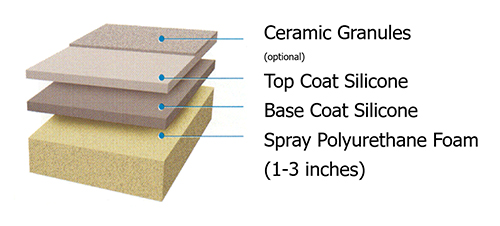
The two coats on the spray foam roof will naturally wear away over time.
For example, on a spray foam roof with a 20-year warranty, a 30-mil thickness of the coating will be installed. In year 20, there will most likely be 7-8 mils of coating left.
A contractor can clean the roof, install a new 30-mil thickness of the coating, and you’ll get a new 20-year warranty.
This is how a spray foam roof can be renewed repeatedly. The spray foam is sustainable as it doesn’t lose any R-value or performance metrics over time.
Cons of Spray Foam Roofing
There are bad spray foam roofing contractors
Applying spray foam is a process that needs to be done correctly from the beginning. The contractor needs to be precise with the application and understand its chemicals.
Installing a spray foam roofing system doesn’t require a large crew. Still, it requires a high degree of technical knowledge and experience.
The Spray Polyurethane Foam Alliance (SPFA) has an ISO-17024-compliant certification program with multiple levels. The program requires the contractor to pass an exam and meet the criteria for certification.
If the roofing system is installed incorrectly, it can be detrimental to the roof’s lifespan and the underlying substrate.
Make sure you choose a contractor that has proven to install spray foam roofs that have lasted. They should have a list of foam roofs they’ve maintained and recoated.
Limited Installation Window
Spray foam can only be sprayed when it’s at least 50 degrees Fahrenheit. Installation of a spray foam roofing system cannot be performed when the existing roof has ice, frost, surface moisture, or visible dampness.
While the installation does not interrupt the building’s daily functions, the weather requirements can leave only a small window of opportunity.
Overspray Potential
Since the spray foam roof is installed by a spray application, there is a risk of the wind carrying overspray onto surrounding cars and other surfaces.
While this does not pose a health concern, it’s a concern for the surrounding property.
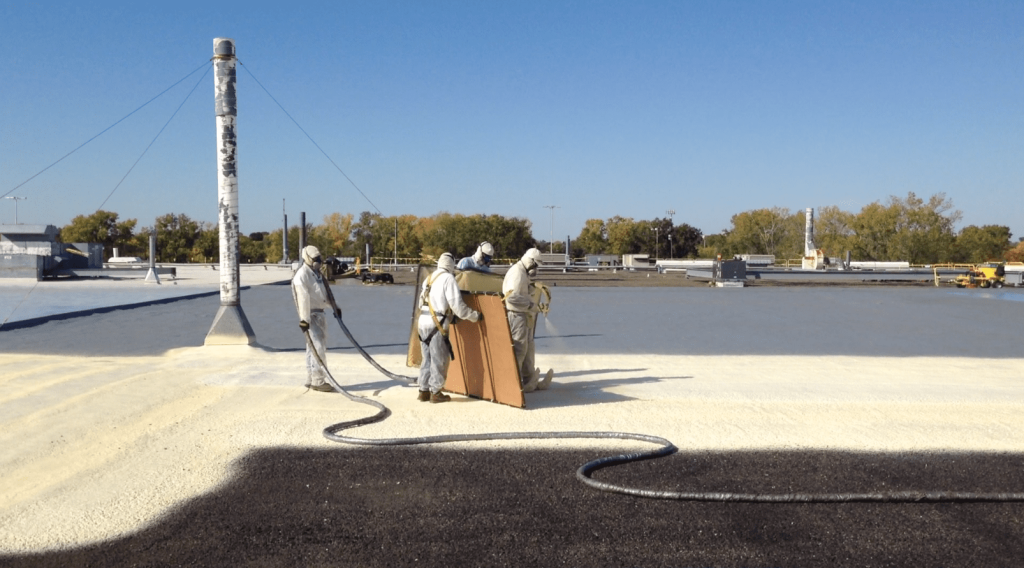
Conclusion
Now that you know the pros and cons of spray foam roofing, what about the pros and cons of all the other commercial roofing systems?
In the downloadable eBook below, we talk about the pros/cons of:
- Single-ply
- Metal
- Shingles
- Built-up roofs
- Roof coating systems