Perhaps this is the first time you’ve considered installing a spray foam roofing system? If so, you’re probably wondering how this stuff gets installed?
Some people think that a tank is installed on the roof.
Some think that roofers are equipped with backpacks that spray out the foam.
In this article, we’ll answer:
- How does a typical spray foam roof get installed?
- What equipment is needed to install a spray foam roof?
- How does the spray foam product get formed?
- How does the coating process go?
- What are the proper installation requirements?
And just so you’re aware, every piece of content written at West Roofing Systems is produced in-house. Every article is reviewed and edited by a roofer/salesman with more than 30+ years of experience in the field.
West Roofing Systems has been installing, servicing, and recoating spray foam roofs since 1979.
Let’s get started!
How does a typical spray foam roof get installed?
At West Roofing Systems, when we pull into a job site, we would have a 24-foot box truck with equipment in the back that allows us to install the foam roof.
In the truck are two 55-gallon drums.
Two products combine to make spray foam. They are often identified as “A-Side” and “B-Side”. These two chemicals are pumped from the truck, heated and pressurized, and brought up to the roof through a hose.
At the end of the hose is a spray gun, where the two materials are mixed at the gun to create foam. The liquid then expands 30x in size, cures, and the foam product is created.
There’s a separate truck with coating equipment. Coating is pumped from the truck through the hose and up to a coating installer.
The coating installer follows behind the foam installer.
What equipment is needed to install a spray foam roof?
- 24-ft box truck and a stake side. These need to be parked near the building.
- Crew cab
- 2 hoses that are 400-600 feet in length
- Spray gun used by the installers
- Generator
- Air Compressor
- Windscreens and/or a spray foam booth in case of high winds
How does the spray foam product get formed?
Inside the box truck are two 55-gallon drums. These two drums contain the “A-side” and “B-side” of the chemical reaction that produces spray polyurethane foam.
These two chemicals are pumped from the drums, heated in a hose, and brought to a mixing spray gun.
The first time the two chemicals mix with each other is when they are sprayed out of the gun.
It’s a 1:1 ratio of A-side and B-side. If it’s not a 1:1 ratio, off-ratio foam is produced, which is not good.
Off-ratio foam can be resin-rich or iso-rich.
Resin-rich spray foam will look more like a sponge.
Iso-rich spray foam will be more brittle and crunchier, which can crack very easily.
It’s very important to choose a spray foam contractor that understands the science of spray foam, also known as the Three-E’s.
What comes out of the spray gun is a liquid. When the mixture hits the roof, it’ll begin rising to about 30x in size. After a minute, the liquid cures and the foam product is formed.
How does the coating process go?
The final step for a successful spray foam roofing installation is the coating process.
In short, the coating installer follows behind the spray foam installer.
Coating is necessary because UV rays will begin to degrade spray foam within 72 hours. The coating acts as a sacrificial line of protection for the foam.
The thickness of the coating determines the warranty length for the roof. For a:
- 10-year warranty, 20 mils of coating is installed
- 15-year warranty, 25 mils of coating is installed
- 20-year warranty, 30 mils of coating is installed
It’s important to know that coating is installed in two coats: the base coat and topcoat. In the topcoat, granules are embedded into the wet coating to increase strength.
What are the proper installation requirements?
You may be wondering if any temperature restrictions can halt the installation process.
And you’re right, there are restrictions where spray foam cannot be installed. These are important to know in case your project is on a tight deadline.
Restriction #1 – it must be 50 degrees and rising
For spray polyurethane foam to cure correctly and to perform at its max, it needs to be 50 degrees and rising when installed. If it’s 45 degrees, spray foam cannot be installed.
This is important for buildings in colder climates where it’s 50+ degrees only 6-8 months of the year. Sometimes spray foam contractors get a backlog and cannot come to your facility for a month or so. If this pushes the start date into colder weather, you may have to wait until the next roofing season to get your spray foam roof installed.
Restriction #2 – it cannot be super windy
There’s no exact MPH on when foam can be installed or not, but if you have installers with experience, they know when it’s safe to spray foam and when it’s not.
The problem with strong winds is that it can harm the reaction of the foam, blow the spray foam to undesirable places, such as on windows and cars.
This is what’s called “overspray”.
To remove foam off a car or window is not hard. It gently gets scrapped off.
To combat overspray, spray foam contractors will use windscreens. If it’s more severe, spraying foam out of a booth is an option.
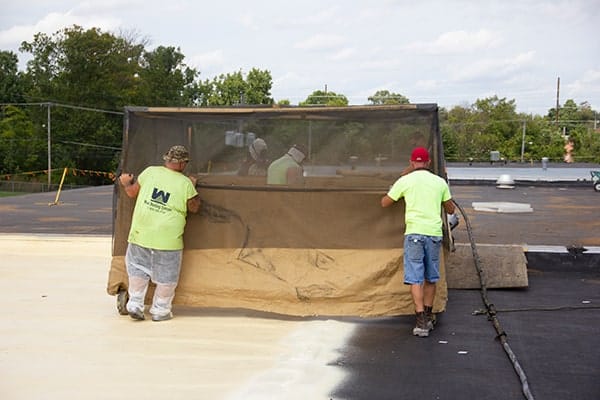
Restriction #3 – the existing roof needs to be dry, clean, and sound
If it’s raining, or about to rain, spray foam cannot be installed. The curing process will be interrupted if it rains before the foam is done curing.
The roof needs to be 100% dry before foam can be installed. If the foam is installed over a wet area, the chemicals will react with the water, creating an inferior product.
The roof also needs to be very, very clean. Foam needs a clean environment to mix, react, expand, and cure correctly.
NOTE: One of West Roofing System’s owners has famously said that before spray foam can be installed, the roof needs to be so clean, that if you dropped your sandwich on the roof, you’d still eat it!
The last part is that the existing roof needs to be sound. Sound means that the existing roof is fully-adhered to the existing substrate.
If a substrate isn’t fully-adhered, like a TPO roof that’s only fastened at the seams, then a coverboard will need to be fully-adhered to the TPO roof before foam can be installed.
A fully-adhered substrate is needed for proper sloping. Since spray foam is fluid-applied, the slope can be created by installing more or less foam.
What are your next steps?
Perhaps you have other questions you’d like answered, such as:
If you’re ready to talk to West Roofing Systems about your project, you can request a quote here.