When you think of a commercial roof, you may think of black tar being mopped on a flat roof. That’s because tar and gravel (built-up) roofs are one of the oldest commercial roof types in the US. But does one of the oldest types of commercial roofs have problems you should know about? Of course!
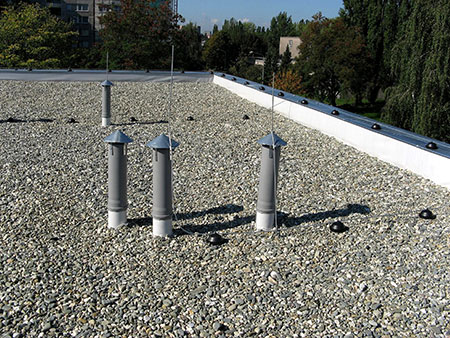
What is a Tar and Gravel Commercial Roof?
Tar and Gravel Roofing Systems have been used in the U.S. for over 100 years. These roof systems are commonly referred to as “built-up” roofs. Tar and gravel systems are installed by alternating layers of asphalt or tar and supporting fabrics directly onto the roof.
You can choose the number of layers (or plies) that are installed. The final layer of a built-up roofing system consists of stone or gravel.
Tar and Gravel Roof Installation
The first layer can adhere directly to the roof substrate. If needed, a base sheet can be fastened to the roof to create a flat and safe workspace. A tar and gravel roofing system is installed by alternating layers of bitumen and reinforced fabric. Property managers can choose three-, four-, or five-ply roofs to meet their needs and budgets.
The last layer is rock or stone; this layer protects the underlying layers from UV rays, extreme heat or cold, and wind damage. A layer of gravel can be added to be more aesthetically appealing as well, along with adding resistance to wind uplift.
Top Problems with Tar and Gravel Commercial Roofs
Added Weight to Structure
Tar and gravel roofs add substantially more weight to the building structure. After you add the layers of tar, supporting fabrics, and the top layer of gravel, your roof can be an extra 5 – 10 lbs. per square heavier than before.
This added weight can strain your roof, underlying substrate, and facility as a whole.
Difficult to Perform Maintenance
When you are on a gravel-covered roof, you can’t see the underlying tar layer. You may be able to tell your contractor where a leak is coming from, but your contractor will need to remove the entire area’s gravel to find the leak, this means extra time and cost compared to a membrane or polyurethane foam roof where you can spot examine the roof quickly.
A contractor can move or remove the gravel from a roof with a vacuum or the old-fashioned way by shoveling.
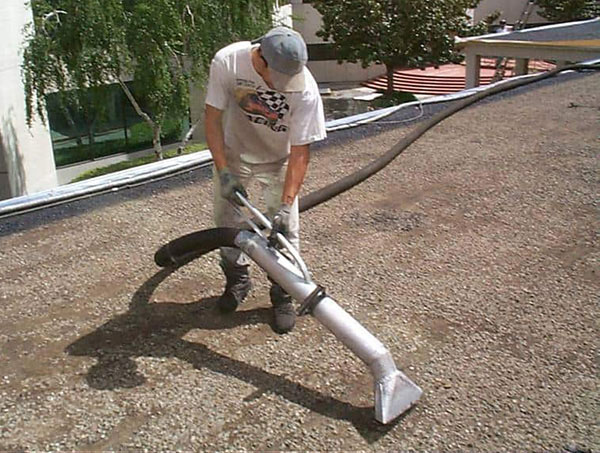
Stone Break Down
Between the weather, foot traffic, and time, the gravel stones on a commercial roof break down and become less effective as time passes.
Gravel is added on top of tar (and sometimes Single-Ply EPDM) roof systems as protection from UV rays, foot traffic, and wear from weather. If the gravel stones break down, they become less effective and leave your important roof layers prone to wear and damage.
Damage from Foot Traffic
Most commercial roofs have some foot traffic, whether it’s from window cleaners, HVAC maintenance, or any other maintenance team. Unless you have dedicated walking paths, when people walk directly on the gravel, breaking it down and causing damage.
If there is enough force, sharp pieces of gravel can be pushed into the underlying layer. This could create an area vulnerable to leaks. Over time, there may not be direct damage, but breaking down the gravel can shorten the lifespan of your roof by exposing the underlayer to UV rays and weather.
Prone to Mold
With any flat roofing system, you are prone to standing water; the goal is to install a roof system that eliminates water from sitting on top of your facility. When contractors install a single-ply or polyurethane foam roof, they plan to create a place for water to drain.
With a thick layer of gravel, you can get water trapped and slow to evaporate. This can lead to saturated substrates and areas that are more prone to growing mold.
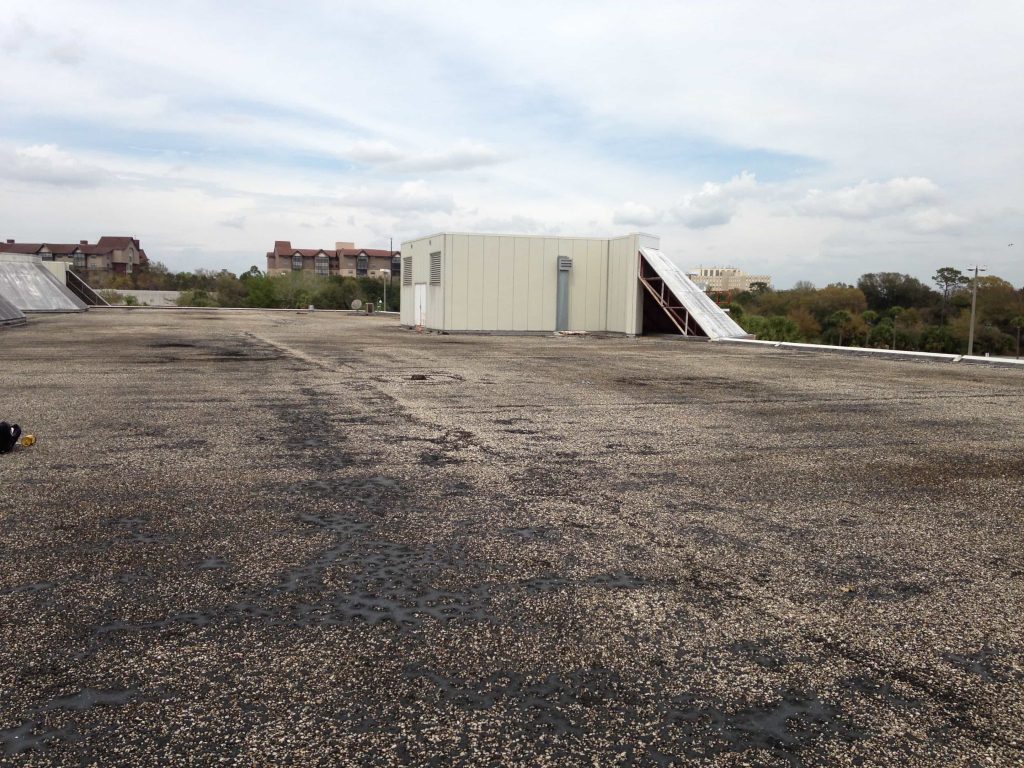
Alternatives to Tar and Gravel Roofs
Single-Ply Membrane Roofing
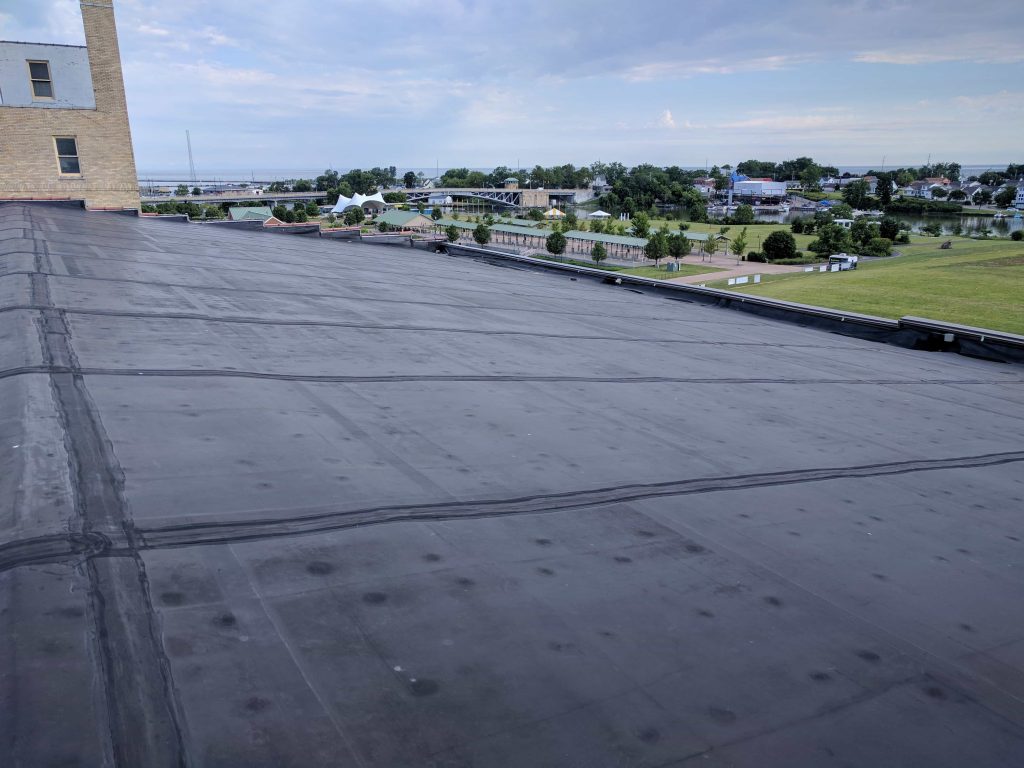
Single-Ply Membranes are sheets of rubber and other synthetics that can be chemically adhered to insulation or ballasted, creating a layer of protection on your commercial facility.
There are two main types of single-ply membrane commercial roofing: Thermoplastic Polyolefin (TPO) and Ethylene Propylene Diene Terpolymer (EPDM). They differ in their chemical makeup, how they are installed, and their energy efficiency.
Spray Polyurethane Foam Roofing
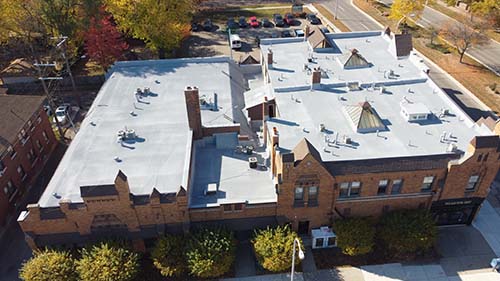
Spray Polyurethane Foam, more commonly referred to as SPF, is a liquid that is sprayed on the existing roof and expands into foam, creating a solid layer across an existing roof.
While SPF roofing is not the most known type of roofing material, the technology has existed since the early 1960s for industrial, commercial, and residential facilities.
Read more: What are the 8 Pros and 3 Cons of Spray Foam Roofing