- Slippery – creates a safety risk when it’s wet
- Eligibility – the existing roof needs to be in decent-to-good shape before the install
- Dingy – they can get dirty
- Not cost-effective for existing Built-Up Roofing Systems
- Nothing sticks to silicone…besides more silicone
- Doesn’t increase R-value
Roof coating systems are becoming increasingly popular, and it’s not hard to see why. They’re more cost-effective than a complete roofing tear-off, provide a 10-20-year warranty, and are environmentally friendly.
But along with those advantages, they also come with their own set of disadvantages.
Restoring, repairing, or replacing your roof is an ultra-important decision that needs to be made, so any building owner interested in making this decision would be wise to learn all the facts.
NOTE: if you’d like to read the blog post, please continue on. If you’d like a summary of this content in video format, please watch the video below.
Here are the most common problems roof coating systems have:
1. Slippery
When roof coating systems get wet, they can be very slippery. For areas of high foot traffic, such as near HVAC units, a roofing contractor will add sand into the wet coating during application.
The sand provides a more stable walking area, and it also provides some strength to handle the abuse when HVAC panels and tools get placed down.
2. Eligibility
For an existing roof to be eligible for a roof coating system installation, the roof needs to be in better condition than most roofs at the end of their serviceable life. Some signs of a roof in good condition include:
- The seams of the existing membrane are relatively intact
- The field of the roof has been properly maintained over its life
- Less than 25% of the underlined substrate and insulation is wet (It is still cost-effective to do spot replacement of small saturated areas rather than a complete replacement.)
Typically, 20-30% of roofs will be ineligible due to neglect of the roof or the lack of a previous maintenance program.
3. Dingy
When a roof coating system is first installed, it’s a white/gray, shiny product of pure elegance.
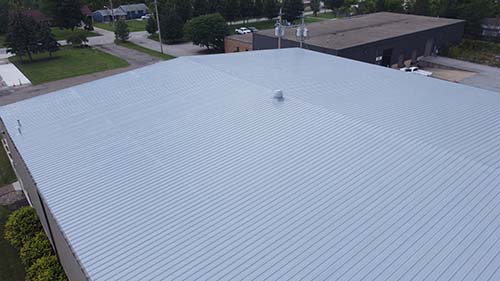
Like your new car after a few years, the shine doesn’t last.
Some of the outside elements, such as leaves, dirt, and algae tend to stick to a roof coating system.
Having outside elements on your roof coating system won’t affect the performance of the roofing solution, but it’s just a foreseen problem in having something so gleaming white.
4. Built-up roofs
Built-up roofs tend to have uneven gravel or stones on the outermost layer of the roof. When spraying down silicone, it’s hard to get a smooth surface over this rocky area.
Some roofing contractors will lay down roof coating systems over built-up, and some won’t.
5. Nothing Sticks to Silicone
If you go with a silicone roof coating system, you’re pretty much stuck with that solution.
Why?
Because nothing sticks to silicone besides more silicone.
This isn’t necessarily a bad thing since silicone roof coating systems are renewable. But if you ignore routine maintenance, and the roof isn’t eligible to be recoated, you have to remove 100% of the roof before installing a new system.
6. Doesn’t increase R-value
Roof coatings don’t increase R-value. If you’re trying to reduce energy costs with your new roof, roof coating won’t do it. According to the datasheets from the top coating manufacturers, coatings have an “unrecognizable” R-value.
The actual increase in R-value may be 0.5 since you’re adding a layer to a roof, but officially there is no increase in R-value.
A better solution for increasing the R-value is to install a spray foam roofing system. Spray foam roofs increase the R-value of the existing roof by 6.5 per inch of thickness.
Do these roof coating problems scare you away?
Those are the main roof coating system problems. You may have heard of others. Just remember to consider the source when someone tells you about everything that can go wrong with a roof coating system.
Roof coating systems are somewhat of a newer roofing solution, so many building owners haven’t worked with this solution.
When considering a roof coating system, it’s recommended to get advice from a roofing contractor with 40+ years of experience working with silicone.
Many of the biggest problems can be prevented by using a reliable, reputable roofing contractor.