Quick answer: The easiest way to seal crevices in a commercial roof is to install a fluid-applied, seamless, fastener-less product.
Maybe you have leaks from your commercial roof and don’t know where it’s coming from? You go on your roof, and nothing is obviously causing the leak.
There’s no ponding water.
No seams are ripped apart.
What could it be?
Perhaps there are tiny crevices in your commercial roof that are hard to see?
In this article, you’ll learn:
- What can you do to seal crevices in your roofing system?
- What roofing systems can leave behind crevices?
- Why should a building owner care about roofing systems that can get crevices?
And so you’re aware, West Roofing Systems has been in commercial roofing since 1979. We’ve been trying to educate building owners on the importance of fluid-applied, seamless roofing systems for a long time.
This article has been reviewed, edited, and approved for publishing by a spray foam and coating expert with more than 30 years of experience.
Let’s get started!
What can you do to seal crevices in your roofing system?
Some crevices are noticeable, and some aren’t. To seal every gap, you need to install a fluid-applied product.
There are two options depending on what you’re looking for and the current conditions of your roof.
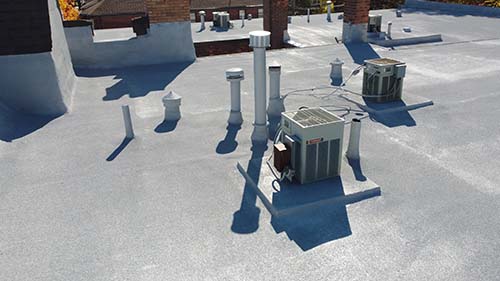
If your roof is in decent shape, you’re budget-strapped, and R-value isn’t important
If this is you, a silicone roof coating system is your best bet. A roofing contractor will identify and replace the areas with wet insulation, clean the roof, reinforce the seams, and then apply a coating over the roof.
Here’s a start-to-finish video of a roof coating system installed over an existing rubber roof:
The coating will seal any existing crevices because it’s a liquid. Even if a crevice is microscopic, the coating system will 100% cover them and stop any future water intrusion. Most applications are 20-30 mils in thickness.
Coating systems are less expensive than other roofing systems. The cost is around $4 – $8 per square foot.
Read more: What variables increase (or decrease) the cost of a roof coating system?
What’s bad about a roof coating system?
One problem is coating systems provide no R-value. If you’re looking at significantly reducing your energy costs, a spray foam roof might be a better option.
Yes, if you add a white/grey coating over an existing darker roof, you can lower the roof’s temperature, reducing energy expenses, but officially, coating systems have no R-value.
The biggest problem with coating systems is eligibility. For a roof to be eligible for a coating system and a warranty, the roof:
- Needs to have had annual maintenance
- Less than 25% of the roof’s insulation is wet
- The seams and field of the roof are in decent shape
If you’re not eligible for a coating system, look into the spray foam roofing system.
If your roof is in decent shape, you’re budget-strapped, R-value is important, and you’re not eligible (or interested) in a coating system
Go with a spray polyurethane foam roofing system. Spray foam is fluid-applied. Once it cures, it will be a minimum of 1 inch thick.
A 1” thick membrane will seal any crevices your existing roof had.
If you’ve never seen a spray foam roof, here’s a link to our photo gallery. And if you’ve never seen spray foam installed before, here’s an installation from start to finish:
Spray foam has the best R-value per inch of thickness of any roofing insulation. Although the cost of spray foam is more expensive than a coating system, there are many advantages it has over other popular roofing systems.
What’s bad about a spray foam roofing system?
One problem is that wind is always a factor. Windscreens and booths are used, but wind taking spray foam onto cars and windows is always a concern.
Another problem is that it needs to be at least 50 degrees to install. There’s a lot of chemistry involved with the heating, mixing, pressurizing, and curing with spray foam. Installing foam at less than 50 degrees will result in an inferior product.
The last problem with spray foam roofing is the limited number of contractors that know how to apply it correctly. We’ve been a company for over 40 years, and we’re still learning something new daily about spray foam chemistry.
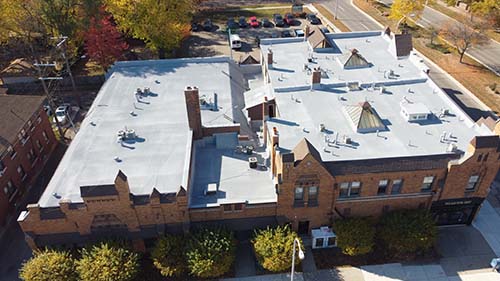
What roofing systems can leave behind crevices?
Any commercial roofing system can get crevices.
Metal roofs can rust, and seams can crack.
Single-ply roofs (TPO and EPDM) can get hail damage, the seams can lose adhesion, get a nail stepped on, have a large branch puncture the roof, get blisters, UV rays can dry out and crack the membrane, adhesives used can dry out and get a tiny hole.
Spray foam and coating systems can get hail damage, get a nail stepped on, and have blisters.
The advantage of spray foam and coating systems is that if they get crevices, they are easy to locate. This is because these roofs are seamless, are one continuous layer, and don’t use fasteners.
Why should a building owner care about roofing systems that can get crevices?
You pay a lot of money for a commercial roof. You want to set it and forget it. The last thing a building owner wants is a roof that leaks. Repairs are costly, time-consuming, frustrating, and can damage internal assets.
Leaks can cause more stress on HVAC units because the roof isn’t as energy-efficient; therefore, it’s working harder to maintain temperature.
Trapped water can freeze in the winter and cause an even greater water entry point when it thaws. In the Summer, water can evaporate and travel north, possibly breaking apart seams, loosening fasteners, or causing blisters.
How can this be avoided? Install a seamless roofing system that doesn’t require fasteners.
Conclusion
If there’s one thing to take away, it’s that some roofs have microscopic crevices that allow water into the building. The best way to seal crevices is to install a fluid-applied product engineered for roofing.
Now that you learned about spray foam and roof coatings, here are some other articles you may be interested in:
And if you’d like to learn the pros and cons of metal, single-ply, roof coatings, and spray foam, please download the eBook below.