Quick Summary – the answer is a fluid-applied roofing system. Since they are fluid-applied, they can go around, up, or down anything on a roof without interruption. Penetrations interrupt a traditional roofing system’s installation, causing more labor hours to install.
Depending on your experience, one might think a roof is unique, and another might think it’s just… another roof.
What do you think about this one…unique or not?
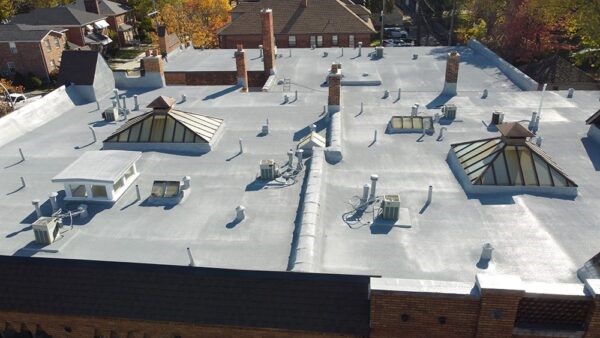
I would say it’s unique.
It’s super busy. There are multiple vertical walls and a penetration every 5 feet.
How long would it take for a rolled-out-sheeted roof to be installed here when there’s constant interruption?
Probably a long time.
There’s a better, more cost-effective option for roofs like these.
Fluid-applied roofing systems.
In this post, we’ll explain:
- What are the only two fluid-applied roofing systems
- What’s an example of a unique or unusual roof
- The problems with traditional roofing systems on busy roofs
- What’s the projected cost difference (of fluid-applied vs traditional,) and what factors make the difference larger
And just so you know, this article has been read, edited, and approved for publishing by an internal commercial roofing expert with more than 30 years of experience.
Let’s get started:
What are the only two fluid-applied roofing systems?
- Spray polyurethane foam
- Elastomeric roof coating systems
Spray polyurethane foam
Spray polyurethane foam is a material sprayed as a liquid that expands into a foam, creating a solid layer across an existing roof.
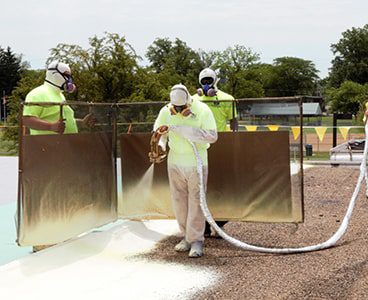
The product is a 1-1 ratio mix of an A-Side and a B-Side. Once the foam cures, it’s protected from UV rays with an elastomeric coating.
Optional granules can be embedded into the topcoat of the coating for added strength and stability.
Elastomeric roof coating systems
The three most used elastomeric coatings are:
- Acrylic
- Silicone
- Urethane
Each has its own pros and cons with price and performance. Silicone is right in the middle of the spectrum, and it’s the coating we use most often.
Most warranties for elastomeric coating systems range from 5-20 years.
After the roof is prepped, the coating is installed by spraying or by snake-and-rolling.
What’s an example of a unique or unusual roof?
Here are some of the characteristics of unique or unusual roofs:
Internal draining system
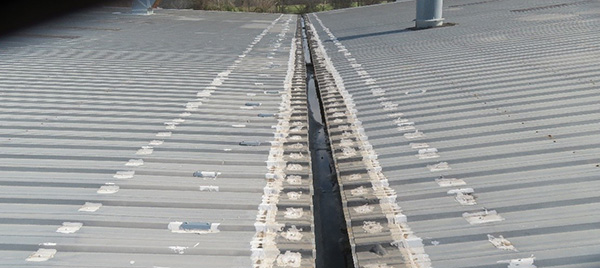
Vertical Walls
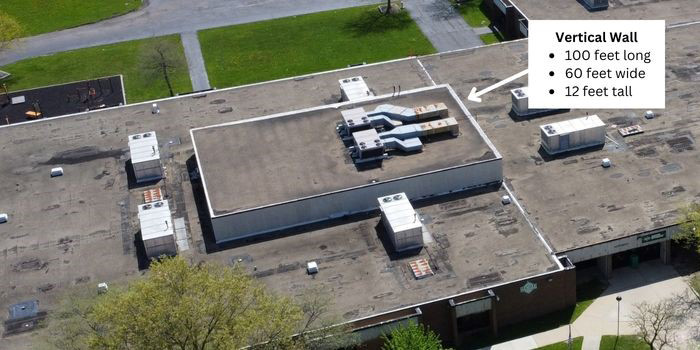
Skylights
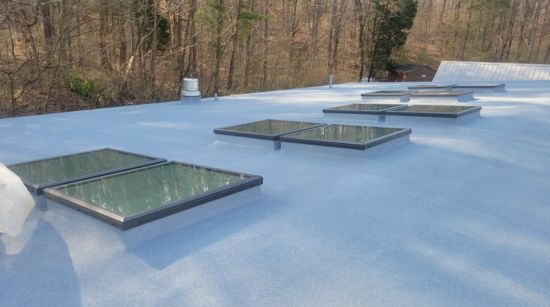
HVAC Units
Most commercial roofs have HVAC units on their roofs, but their quantity and size can make a roof unique.
Multiple Levels
Hospitals and schools often fall into this category. Roofs with multiple levels are challenging to roof because of the constant stoppage to move onto another roofing level. Plus, transitions between the levels may be challenging to roof.
Different roofing systems already installed
We’ve seen a building have a smooth built-up, metal, and a rubber roof. And a 6ft. stucco wall. This was all on a one 9,600 sq. ft. roof.
Extreme amount of penetrations
We beat this one up earlier, but every penetration halts a traditional roofing system’s installation. It doesn’t halt a fluid-applied one. When the install is interrupted, labor hours increase, and the project costs more.
The problems with traditional roofing systems on busy roofs
The use of extra materials
Traditional roofing systems need to use termination metal, adhesives, boots, sealants, fasteners, or other materials to properly install a sheet around a penetration.
Extra materials make the job more expensive and increase the labor hours needed to complete the job.
A fluid-applied roof usually doesn’t require any of the materials above. If they do, it’s very minimal.
Risk of leaking
Piecing together materials and creating more seams exposes the roof to an increased risk of leaking. It could be installed perfectly fine, and it never leaks. However, the installation has more moving parts and more room for installer error.
What’s the projected cost difference, and what factors make the difference larger
It all depends on the difficulty of the roof. The more unique, complex, and unusual, the larger the cost difference will be.
It would be impossible to tell you that for every 10 penetrations, the cost of a traditional roofing system is $1 more dollar per square foot than a fluid-applied roof.
It would also be impossible to tell you that for every roof level and roofing system already installed…add $1 per square foot to a traditional roofing system.
How do you really figure out the price difference?
Get a quote for a traditional roofing system, such as TPO. See what the cost and scope of work is.
Then do the same with a fluid-applied system.
Getting a quote from a commercial roofing company is usually free. It’s in your best interest to at least learn about all the different options you have and compare everything, such as:
- Price
- Warranty
- How they will ensure penetrations will be watertight
- R-value increase
- Any changes to the slope
- Trust in the roofing contractor themselves
All of these should factor into the best decision for you.
Here are some other resources you might find helpful:
- The Pros and Cons of Spray Foam Roofing
- The Pros and Cons of Roof Coating Systems
- Case Study – Maryland Court – Spray foam renews a roof with many penetrations and multiple roof levels.
- Case Study – Heskett Middle School – Learn how spray foam was installed 50% faster and for $1M less than a complete tear-off.