Commercial roofs have issues just like your car does.
Think of the possible issues your car can have:
- The rim can get bent
- The air conditioning stops working
- A rock can crack your windshield
There are so many issues with your car that the list can go on forever.
It’s the same thing with commercial roofing.
But what most people don’t know is that there’s a solution called spray polyurethane foam roofing.
If you’re unfamiliar with what it is, here’s a video explaining what spray foam is:
Since spray foam is fluid-applied, it can solve many roofing issues much easier than traditional systems.
In this article, we’ll cover:
- Ponding water, sloping, and draining issues
- Roofing up and over vertical walls and awkward shapes
- How to cost-effectively get a roof under a new warranty
- Leaking skylights and roofing around penetrations
- Hard to identify damaged areas
- The membrane being punctured and leaking
- Avoiding a complete tear-off
- Rising energy bills
- Leaking internal gutter system
- Avoiding tear-off on steep slope metal roof
- Need new roof done in a quick timeframe
Before we start, this article has been read, edited, and approved for publishing by a commercial roofing expert with more than 30 years of experience.
Let’s get started!
1. Ponding water, sloping, and draining issues
Some roofs get worn down over time (or installed incorrectly) and have water that will not run off the roof. This is called “ponding water,” which occurs because the roof’s slope isn’t proper.
Since spray foam is fluid-applied, you can install more foam around an area to “raise it up.” It’s as easy as pulling the trigger of the spray gun.
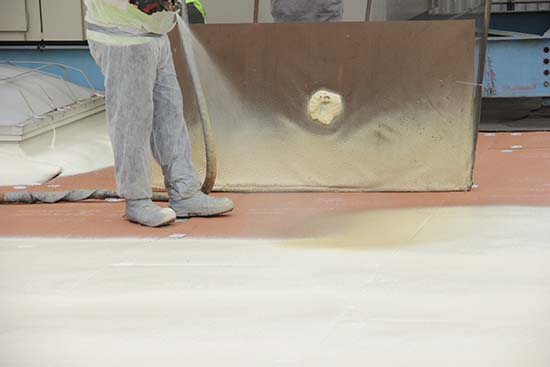
Traditional roofing systems can only manipulate the slope by installing a pre-manufactured, tapered insulation board system below the membrane.
Think about a rubber roofing system that once had proper sloping but is now holding water. How would a contractor fix this issue?
They would have to cut through the rubber, cut out the insulation, and install a different thickness of insulation board to fix the slope. Then put new rubber back on and make it watertight with the existing roof.
Complicated, timely, and costly.
Using spray foam to eliminate ponding water or change slopes is more cost-effective than traditional roofing systems.
2. Roofing up and over vertical walls and awkward shapes
Since spray foam is fluid-applied, it can go up and over vertical walls. It can also form to any shape. This is beneficial for roofs that are “super busy” or complex.
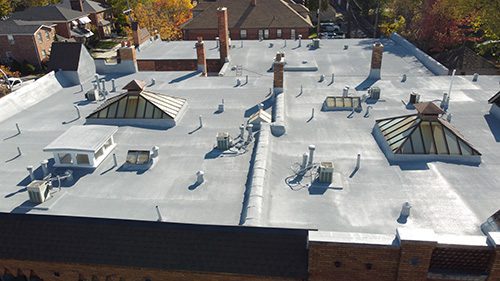
These roofs are issues for traditional roofing systems because it’s complicated and time-consuming to install their system on a roof like this.
3. How to cost-effectively get a roof under a new warranty
When a commercial roof is out of warranty, some building owners will let the roof go until it needs completely replaced.
If it’s not broke, don’t fix it…right?
The problem is they let the roof go until it’s in so bad of shape that it needs 100% replaced.
Spray foam can be installed over an existing roof as long as it meets certain criteria. If the roof is almost out of warranty and there’s been routine maintenance, then there probably won’t be much saturated insulation.
Let’s say 2% of the roof has wet insulation. You can remove and replace those areas only, then install spray foam over the entire roof.
A 2% tear-off today versus a 100% tear-off three years from now is a huge price difference. Minimizing tear-off is the best way to reduce the cost of a commercial roof installation.
PS: Spray foam roofs come in 10, 15, and 20-year, renewable warranties.
4. Leaking skylights and roofing around penetrations
One of the best things about spray foam roofing is that it’s fluid-applied and self-flashing. This means when it’s installed around a skylight, pipe, HVAC unit, or any type of flashing, spray foam simply encapsulates it, creating a monolithic layer of waterproof insulation.
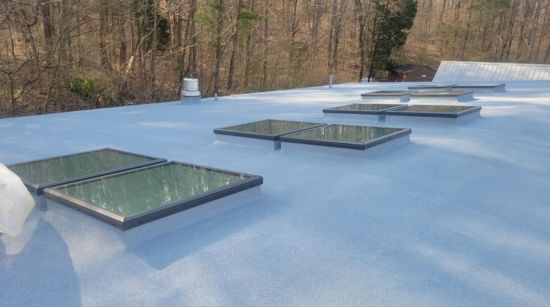
Here’s a photo of spray foam installed around a cardboard box, simulating a penetration:
The problem with traditional roofing systems that are rolled out as sheets, is that penetrations interfere with the install.
The installer must stop, cut, and use adhesives and termination metal to make that section watertight. Traditional roofing systems have no problems around penetrations, but they take way more time to install, and there are more parts to piece together, which adds unnecessary variables to the possibility of a leak.
5. Hard to identify damaged areas
One common roofing issue is the difficulty of identifying leaks. Metal roofs have hundreds of fasteners that could be damaged, have backed out, or were installed incorrectly. It’s challenging to determine areas of lost adhesion in a seam with a single-ply system that covers an entire roof.
A spray foam roof is one continuous layer. If there’s a crack or puncture, water will not travel through the spray foam because of it’s closed-cell nature and will be easily recognizable.
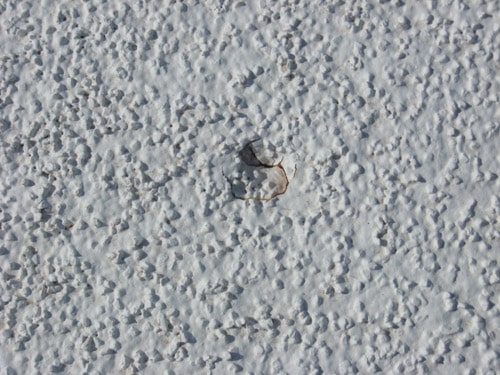
6. The membrane being punctured and leaking
Since roofs are exposed to the elements 24/7/365, they will all be weathered to some extent. Hail can crack a membrane, flying debris can puncture a membrane, and the maintenance guy can drop tools or step on screws, causing damage.
What’s different about spray foam is that it has closed-cell properties. This means water will sit in a hole and not travel through the system.
This is different from traditional roofing systems that use pre-manufactured boards for insulation. If the membrane cracks and the insulation board is exposed, water can saturate it and/or run through the joints in each board; eventually allowing water to continue traveling down into your deck and building.
Here is a link explaining open vs closed-cell insulation.
7. Avoiding a complete tear-off
One issue with commercial roofing is the complete tear-off. Complete tear-offs are expensive, labor and material-intensive, bad for the environment (materials go into a landfill), and….usually avoidable.
Some building owners will get a roof inspection where it’s determined that 15% of the roof is wet…and they still opt for a 100% tear-off.
Why rip 100% of the roof off when 85% is still in good condition?
One of the best things about spray foam roofing is that it can be installed over an existing roof.
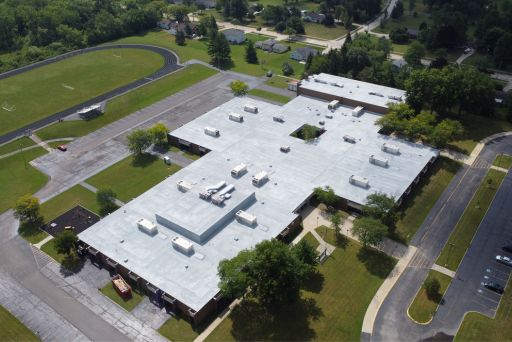
Granted, there are times when this cannot happen, such as when there are two roofing systems already installed.
In the example above, if there’s only one roofing system installed, only the wet insulation of the roof (15%) would be removed and replaced with similar material. Then spray foam can go over the field of the roof.
PS: Minimizing tear-off is the #1 way to reduce the cost of a roofing project.
8. Rising energy bills
Perhaps your HVAC units are constantly running to maintain a comfortable temperature inside your building?
Most commercial roofing systems use seams, fasteners, and other components to keep the roof watertight.
Since the roof gets hot and cools down, the roof actually expands and contracts, putting stress on these areas.
Over time, the adhesion between seams degrades. Fasteners can back out or become damaged. Adhesives can break down when exposed to UV rays.
When this happens, your roof has diminished its ability to keep energy inside the building.
Since spray foam is fluid-applied and self-flashing, no seams, fasteners, or adhesives are used. It expands 30x its size within a few seconds. The usual thickness is 1-2”.
Spray foam has an R-value of 6.5 per inch of thickness (the highest R-value per inch of thickness of any roofing insulation.) With a high R-value and self-flashing ability, you should expect a reduction in your energy bills.
9. Leaking internal gutter system
Internal gutter systems leak very often. The best way to solve this problem is to stop using the internal gutter and find another way to run the water off the roof.
On some roofs, we’ve covered the internal gutter system with a board, sprayed foam over everything, and installed the foam at a particular slope to run water toward a traditional drain or gutter.
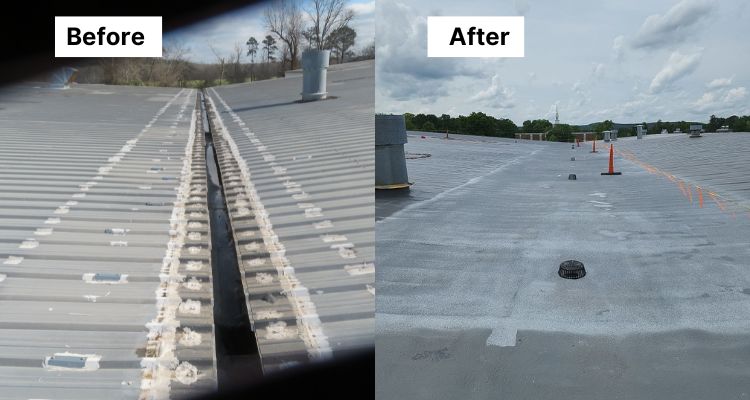
With spray foam’s easy application, solving this issue is much easier than with a traditional roofing system.
10. Avoiding tear-off on steep slope metal roof
Steep slope metal roofs are super expensive to remove and replace. Not only is the material costly, but with the severe sloping, the job is difficult to do.
After proper preparation, spray foam can be installed over the existing roof. This saves tons of money because you avoid the tear-off, landfill costs, the price of new material, and much more.
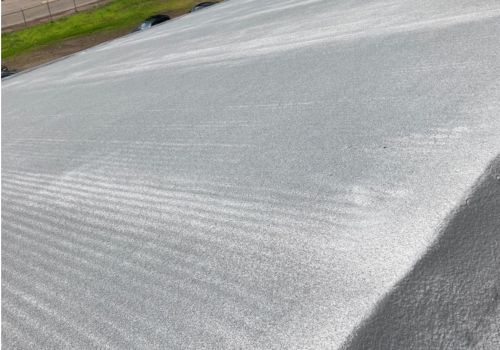
11. Need new roof done in a quick timeframe
Some companies that need a new roof need it done in a certain amount of time. Maybe they are planning on shutting the company down for the installation? Maybe they’ll have to restrict people coming in and out of the campus during the roof install?
In this case, you’ll need a roof installed quickly.
Spray foam roofs are installed with the least amount of tear-off possible. Usually, only the wet insulation and damaged membrane areas are removed. Minimizing tear-off reduces the time to install the new roof.
Since spray foam is fluid-applied, it can easily be installed around pipes, drains, HVAC units, skylights, etc. Easy installation reduces project time…especially on a roof with irregular objects, vertical walls, and many penetrations.
Conclusion
Hopefully, this article helped you learn a little about spray foam and the common roofing issues it can solve.
Here are some other articles you may be interested in: