In this article, you’ll learn:
- What is commercial roofing, and what “systems” are being phased out
- What popular trends are building owners doing with their roofs?
- What is the future of energy efficiency with commercial roofing systems?
- Why renewable warranties are cost-effective solutions to building owners?
- Other trends/facts to be aware of
And just so you’re aware, West Roofing Systems has been in commercial roofing since 1979. In the past 40+ years, there have been many law changes, formulation changes with material, warranty options, and much more.
This article has been read, edited, and approved for publishing by a commercial roofing expert with over 30 years of experience.
What is commercial roofing?
Commercial roofing is the roof of a building where a company manufactures a product or provides a service. This is different from residential roofing where the roof protects a place where people live.
Shingles are the main roofing system for residential homes.
Commercial roofs have many different systems, such as:
- Metal
- Smooth or Gravel Built-Up
- Single-Ply (TPO, EPDM, or PVC)
- Spray Polyurethane Foam
- Modified Bitumen
In 2024 and beyond, “Built-up” roofing systems are being used less and less. All the other roofing systems are more cost-effective to install and can be easier to maintain.
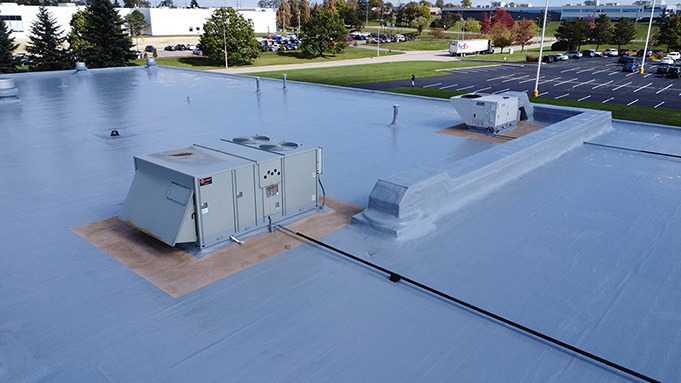
What are the popular trends that building owners are doing with their roofs?
The popular trend is to beat the complete tear-off and get a renewable warranty.
You want to avoid landfill costs as much as possible. It’s terrible for the environment and it’s bad for your wallet.
To do this, companies install elastomeric roof coating systems over their existing roof. Elastomeric means the product can stretch, return to its original length, and not lose performance. This is needed because roofs expand and contract throughout the day.
Elastomeric coatings are similar to a very, very thick paint that’s engineered to withstand weathering elements.
Elastomeric coatings come in:
- Acrylic
- Silicone
- Urethane
They each have their pros and cons.
There are restrictions to installing a coating system and getting a manufacturer’s warranty. Here are the requirements:
- The roof must have had at least annual maintenance
- Less than 25% of the roof’s insulation is wet
- The seams are intact and have good adhesion
If any requirements aren’t met, you can most likely avoid the complete tear-off by installing a spray polyurethane roof.
But before any roofing system is installed, 100% of the wet insulation must be identified, removed, and replaced.
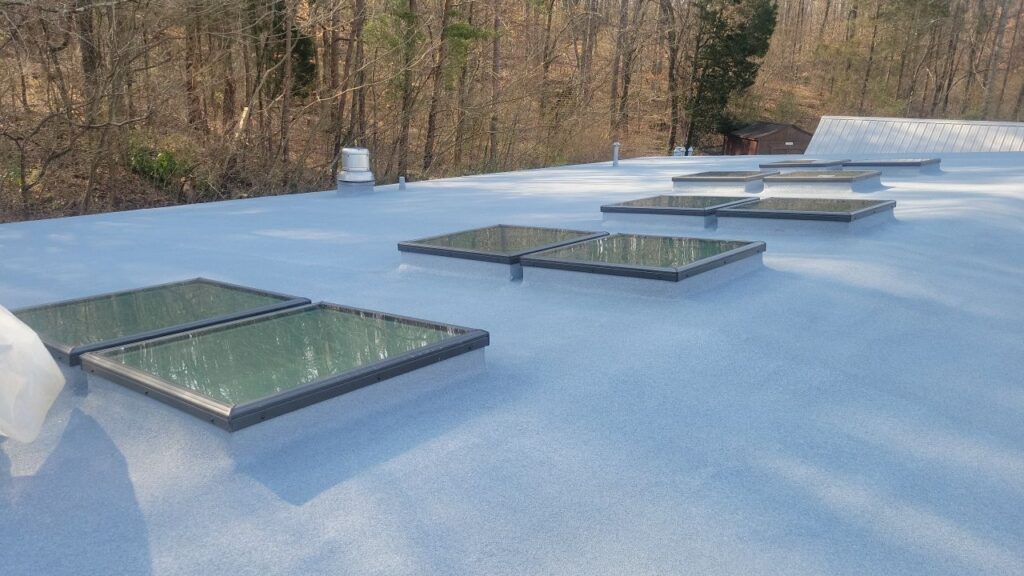
What is the future of energy efficiency with commercial roofing systems?
New construction in Ohio requires a new roof to have at least an R-25. If your existing roof is in bad shape (like 90% of the roof’s insulation is wet) and a contractor recommends a complete tear-off, your project will be considered “new construction” and will have to hit the R-25.
With trends like being “carbon neutral,” becoming more energy-efficient is going to be the new normal.
Although you may have a roof that works fine today, energy costs in the future may be expensive. There are two ways you can increase the R-value of your existing roof:
- Install Insulation Board
- Polyiso board has an R-value of 5.5 per inch of thickness.
- EPS has an R-value of 3.85 per inch of thickness.
- XPS has an R-value of 5.0 per inch of thickness.
The boards are tapered to create a slope.
- Install Spray Polyurethane Foam
Spray foam has an R-value of 6.5 per inch of thickness. An elastomeric coating is always installed over spray foam to protect it from UV rays.
Since spray foam is fluid-applied, the slope can easily be manipulated by spraying more or less foam. Creating slope with spray foam is easier, less timely, and more cost-effective than using polyiso board.
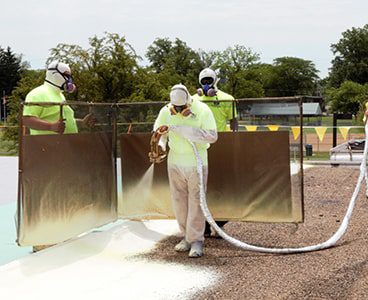
Why are renewable warranties cost-effective solutions for building owners?
Building owners are interested in getting renewable warranties for their roofing systems. This is much more cost-effective than tearing the roof off when the warranty is over.
How does this work?
Example 1 – Coating over Single-ply roofing system
Say you have a TPO or EPDM roof installed 15-20 years ago. You’ve kept up with the maintenance, but the membrane’s lifespan looks about over.
You can rip it all off and install a new membrane. Or you can go with a coating system. Since elastomeric coatings come with renewable warranties, you calculated this to be the more cost-effective option.
A contractor will make sure there’s no wet insulation. If there is, it’s removed and replaced. Then, the seams are inspected to ensure they have proper adhesion.
A contractor will reinforce the seams by striping them with coating, laying reinforcement fabric into that coating, letting it cure, and then installing more coating over the top (a 3-course process).
Then, the contractor will install coating over the field of the roof at the required thickness level to grant a warranty.
In most cases, a:
- 20 mil thickness = 10-year-warranty
- 25 mil thickness = 15-year-warranty
- 30 mil thickness = 20-year-warranty
The coating is sacrificial. It’s meant to naturally wear away over time. Let’s say you go with a 15-year warranty. In year 15, the 25-mil thickness will be less than it was when it was installed.
At this time, a contractor can clean the roof and install a new 25-mil thickness of coating. A new 15-year warranty would then be granted.
The process can repeat over and over again.
Recoating a roof is approximately 33-50% more cost-effective than ripping off a membrane and installing a new one.
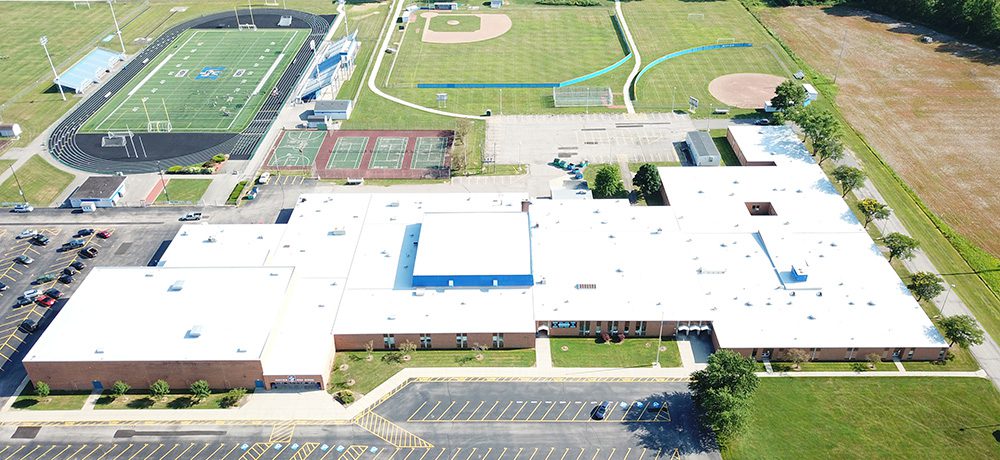
Example 2 – Spray foam roofing over existing gravel built-up roof
So, you have a Gravel Built-up at the end of it’s life. You chose to install a spray foam roof over it for numerous reasons:
- Added R-value
- The ease of adding slope
- Waterproofing
- Once the loose gravel is removed, foam can be installed right over what’s remaining
Coating must be installed over the spray foam to protect it from UV rays.
How the system is renewable is the same as the coating system described above.
However, on a spray foam roof, the foam never loses R-value or any other performance measures over time.
Install the coating, let it wear away, clean, install more coating, let it wear away……repeat and repeat.
This is how a spray foam roofing system is renewable.
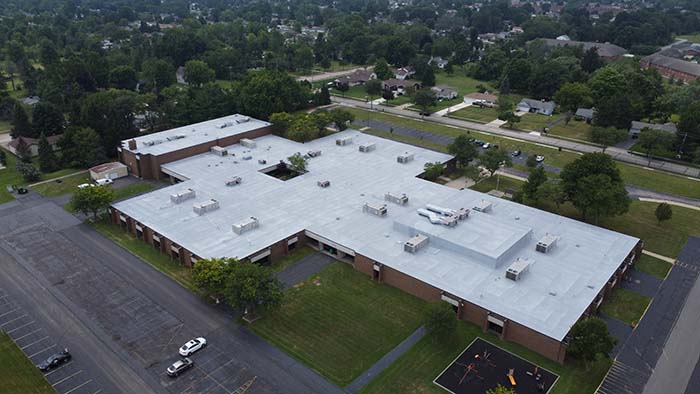
Other facts/trends to look out for
- On roofs with two roofing systems installed, sometimes the top roof is in bad condition, but the bottom one is in good shape. Don’t remove/replace good insulation with new “good” insulation. This can be a money grab if you’re not careful.
- Per building codes, two roofing systems are the max that can be installed. Elastomeric coatings do not count as a roofing system.
- The R-value of an elastomeric coating is 0. Well, according to manufacturer’s it’s “negligible”. Which basically means 0.
Conclusion
The most important takeaway is that complete tear-offs are expensive, take a lot of time to install, and are usually avoidable. Energy efficiency is important now but is likely to be even more prevalent in the future. Renewable warranties are long-term, cost-effective options.
Here’s other content you may be interested in: