So, you have a single-ply commercial roof that’s leaking, and you want to know the best solution.
The short answer is that it depends on the current conditions of the roof, along with what your goals are.
Some single-ply roofs are in too poor of a condition to repair or restore.
Some are in fair condition, and it would be a waste of money to rip everything off.
Some building owners are just trying to stay leak-free for the next 2 years until a new building is built.
And others are looking for a long-term, cost-effective, hands-off solution.
Each one of these scenarios is very different.
So, which one fits you the best?
NOTE: If you have a roof leak, contact a roofing professional. Most do free roof inspections, and they will give you a few options depending on what they see and what your goals are.
In this article, we wanted to go through two different scenarios:
- A leaking single-ply roof when less than 25% of the insulation is saturated
- A leaking single-ply roof when more than 25% of the insulation is saturated
As you’ll see below, each scenario has its own “best” solution.
Let’s get started.
The best solution for a leaking single-ply roof with less than 25% saturation
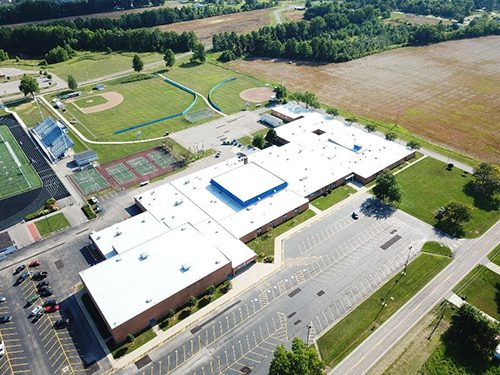
The short answer solution is a silicone roof coating system.
Analysis: After a roofing contractor performed an infrared scan or after core samples were pulled, it was determined that less than 25% of the single-ply roof’s insulation was saturated.
In this case, why rip off 75% of the roof’s dry insulation?
A roofing contractor would identify the areas with saturated insulation, remove them, and replace these areas with new, dry insulation.
Then they would repair the membrane. For example, if EPDM had to be removed, then they would replace that area with new EPDM and accessories.
The next step is to clean the field of the roof. This is usually done with power washing. In conjunction with a primer.
Then, the contractor would perform 3-course seam reinforcement.
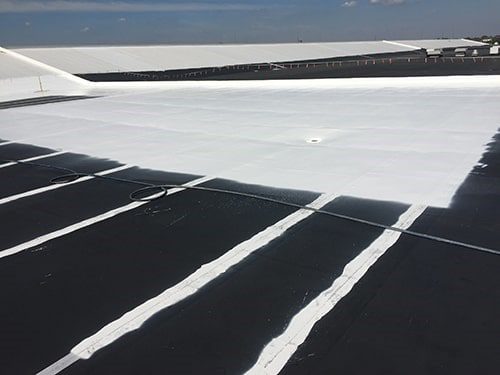
The next step is to apply silicone coating over the entire roof system.
Once that’s done, depending on who the warranty is through (contractor or manufacturer), a post-job inspection will take place.
This is to ensure that if 30 mils of coating were supposed to be installed, 30 mils were installed.
Final analysis: silicone roof coatings are a great cost-effective solution. The cost is around $2-$4 per sq. ft.
The best solution for a leaking single-ply roof with more than 25% saturation
The short answer is a new roofing system, either single-ply or spray polyurethane foam.
Analysis: Since this roof is too bad of a condition to restore with coating, the best solution is to remove the membrane and insulation and install a new roofing system.
Now you have a few options on which roofing system you’d like to install. Both options have their own set of pros and cons.
Single-Ply Advantages:
- Proven track record. Single-ply’s have been used since the 1960s
- Choice of insulation. Popular choices are EPS, XPS, or Polyiso
- Reflective. TPO’s can come in a white or light grey color to reflect the sun
- Lots of contractors can install single-ply roof systems
Spray Foam Advantages:
- Energy-efficient. Has an R-value of 6.5 per inch of thickness
- Seamless. Which means no seams, no leaks
- Fluid-applied. No custom cutting, termination metal, adhesives, or sealants need to be used to install around penetrations
- Fully-adhered. Spray foam is 100% adhered to the existing membrane
- Renewable. No total removal just power wash and recoat
- Even if it gets a crack/hole/puncture, the roof will not leak because of its closed-cell insulation
Single-Ply Disadvantages:
- They have seams
- They require custom cutting, termination metal, various adhesives, and sealants to install around penetrations
- They don’t have any R-value. They need to be attached to an insulation source
- If it gets a tear, the wind can easily expand the opening
- If it gets a pinhole, water will get into the insulation below and expands throughout the roof
- UV rays can degrade the sealants used in the installation faster
Spray Foam Disadvantages:
- Can only be installed when it’s 50 degrees and rising
- Cannot/Shouldn’t be installed on very windy days
- Lots of contractors don’t have experience, hard to find one that does
- Building owners are skeptical because it’s not a well-known roofing system
What are the costs of each system?
The cost of a single-ply roof is between $6 and $10 per square foot.
The cost of a spray foam roof is between $6 and $10 per square foot.
There are tons of variables that influence the price of each system, such as:
How difficult will the installation be?
On a flat roof with minimal penetrations in the way, a single-ply roof may be a more cost-effective option because of the ease of installation.
A spray foam roof may be more cost-effective on a roof with many penetrations because it’s easily sprayed around skylights, pipes, HVAC units, etc.
How much R-value does your roof need?
A single-ply roof uses insulation boards for R-value. Common roof insulation, known as Polyiso board, has an R-value of around 5.5 per inch of thickness.
A spray foam roof is a roofing membrane and insulation in one. Spray foam has an R-value of 6.5 per inch of thickness.
If R-value is something you want out of your next roof, it would be smart to get quotes for a single-ply and a spray foam roof.
Other variables that influence price are:
- How much of the existing roof will need to be torn off?
- How fast will the installation take?
- How long of a warranty is the building owner seeking?
- How much will it cost for a maintenance plan for the roof?
And many, many more.
Are there any case studies for single-ply roof repairs?
Yes!
Here’s a case study of Gorilla Glue. They had an EPDM roof with only 2.5% saturation. The most cost-effective solution was a silicone roof coating system.
Here’s a case study of Midview High School. They had a leaking EPDM roof with a 4-year life expectancy. To avoid a complete tear-off and replacement before the new school was built, Midview used silicone roof coatings.
Are there any photos of spray foam roofs over single-ply?
Here’s a photo of an existing EPDM encapsulated with a cover board and spray foam:
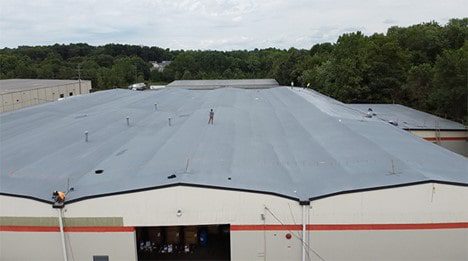
Here’s an in-progress photo of a spray foam roof incorporated with an EPDM:
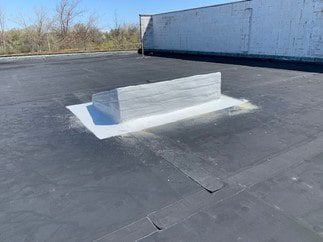
Here’s a photo of an existing TPO encapsulated with a cover board and spray foam:
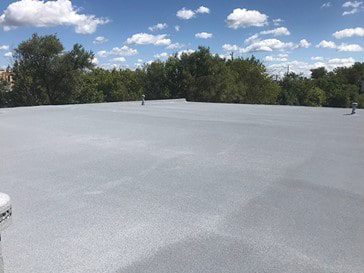
What should you do now?
The first thing I would do is to have a conversation with a roofing contractor. I’d give them information on my roof, such as:
- The TPO roof is 20+ years old and it’s leaking
- There’s ponding water
- And we’re looking for a cost-effective, long-term solution
The contractor will then look your roof up online through Google Earth and begin to collect details about your roof.
If it’s a good fit, the contractor will schedule a time to walk the roof with you and perform a visual inspection.
Once the inspection is complete, recommended repair options and a proposal will be submitted.
Then you just need to choose the best repair option and the best contractor to do the job.
If you’d like to learn more about silicone roof coatings or spray foam roofing systems, please download the “cheat sheets” below: