The best roof for a shopping center is a spray foam roofing system. There are several reasons:
- They have closed-cell insulation, which will not allow leaks
- They are easy to maintain with caulk or coating
- They can save on installation costs because the tear-off is minimized
- They can be recoated, which extends the warranty
- They are a fluid-applied system that 100% seals HVAC units, drains, etc.
In this article, we’ll go into more detail about each of the points above.
And just so you’re aware, West Roofing Systems has been in commercial roofing since 1979. We’ve installed spray foam roofs over many shopping centers that we still maintain today.
Each article written has been reviewed and edited by a spray foam roofing expert with more than 30 years of experience.
Let’s get started!
Closed-cell insulation
If you’re unaware, the spray foam roofing system has four parts:
- Spray polyurethane foam
- Base coat of coating
- A top coat of coating
- Embedded granules
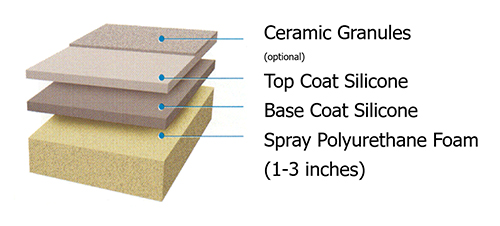
The spray foam part has closed-cell properties. Being closed-cell means that water cannot travel vertically through it. Closed-cell stops water from saturating other areas of the insulation. It also prevents water from traveling into the deck and your building.
Eliminating leaks is important for shopping centers because you don’t want your renters’ assets ruined, whether that’s food, clothes, equipment, or anything else.
Closed-cell is the opposite of open-cell. The commonly used “Iso-board” on traditional roofing systems has open-cell properties.
When water gets through the membrane and enters an “open-cell” insulation, the water can travel vertically. Water will saturate other insulation, get to your deck, and into your building.
Even a microscopic opening can create a large area of saturated insulation.
Spray foam roofs are easy to maintain
Every roofing system needs routine maintenance. It’s no different than oil changes with your vehicle.
The difference, though, is how difficult it is to do.
On a spray foam roof, you might see punctures or small cracks created by flying objects, hail, or something sharp.
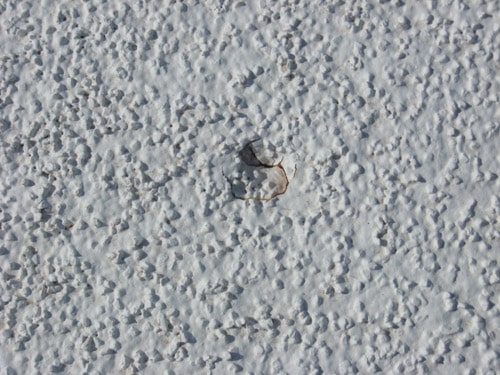
To repair a spray foam roof, you need to dry the area, cut around the puncture, and fill it with caulk or coating. Smooth the area, so it’s level with the foam around it, and you’re done.
The repair is different on traditional roofing systems.
On traditional roofing systems that use an open-cell insulation board, once water hits it, it can travel and saturate other areas.
A roofer will have to lift multiple rubber sheets and inspect how much insulation is wet. The repair can take a long time and require the installation of new insulation and membrane.
With shopping centers (and any roof), you want the maintenance to be minimal in terms of time and cost.
Minimal tear-off
When researching a new roof for your shopping mall, consider the amount of tear-off. With a busy shopping mall, you want to limit the number of interruptions to regular business.
One of the best attributes of spray foam roofing is that it can be installed over an existing roof. Foam can go over an existing roof as long as there aren’t two or more roofing systems already installed. You want to be code compliant!
On a spray foam installation, you want to determine where the wet insulation and damaged membrane are. Remove those areas and replace them with similar, dry material.
Once that’s done, you can clean the roof and install the system.
Some roofs, such as TPO and EPDM, could require the installation of a coverboard for added adhesion.
If an existing roof is 25% or more saturated, it might be worth tearing everything off and starting over.
But if someone suggests you remove 100% of the roof, ask them why.
We’ve had countless discussions with building owners about how the majority of the roof is in good shape, so why rip it all off?
Spray foam roofs can be recoated, which extends the warranty
Shopping centers are usually around for a long time. Therefore, you want a leak-free roof for the longest time possible.
Spray foam roofs are unique because they are renewable.
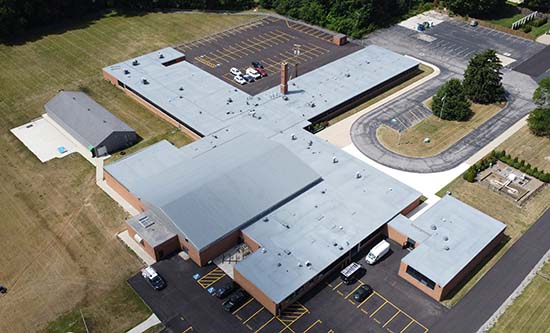
A typical spray foam installation can come with a 10-20-year warranty. The thickness of the coating determines the warranty length:
- For a 10-year warranty, a 20-mil thickness of coating is installed.
- For a 15-year warranty, a 25-mil thickness of coating is installed.
- For a 20-year warranty, a 30-mil thickness of coating is installed.
Let’s say you want a 20-year-warranty. In year 20, the 30 mils of coating might have worn down to 7-8 mils. The coating is sacrificial and is intended to wear away naturally.
Through rigorous testing, the coating will not 100% wear away before the warranty is over.
But let’s say it’s year 20, and you want the warranty to extend.
You can choose a new 10-year, 15-year, or 20-year warranty and have a contractor install the required coating thickness in the bullet points above.
A spray foam contractor will inspect the roof and make any repairs if needed. Then they will clean the roof, usually through power washing. Then they will add the required amount of coating for the desired warranty length.
This procedure, known as a “recoat,” is very simple to install. The cost for a recoat is about 33% to 50% of the original installation.
On traditional roofing systems, when the life of the roof is over, most of them need 100% removed and 100% installed. A new roof would cost 100% of the original installation.
Bonus info: You might wonder if the spray foam needs to be replaced over time. The answer is no. As long as the foam is continually protected by coating, it won’t lose any R-value or other performance measures.
Spray foam is a fluid-applied system
Shopping centers have multiple businesses, requiring lots of equipment on the roof.
Multiple HVAC units, exhausts, drains, skylights, there can be an assortment of rooftop items depending on the business below.
The “busier” a rooftop is, the more efficient (time and money) that a spray foam roof is versus traditional roofing systems.
Spray foam is the only fluid-applied roofing system, meaning it’s sprayed on.
Going around HVAC units and other penetrations is no issue for spray foam. You spray around it, and that’s it.
Other roofing systems that are rolled out sheets need to cut the membrane and use boots or sealants to create a custom watertight solution for each penetration.
We aren’t saying that single-ply roofs aren’t watertight around penetrations. It’s a more complicated process than spraying up and around the unit.
Conclusion
Now that you know a little about spray foam roofing, you may have other questions, such as:
- What problems can spray foam roofs have?
- How much does a spray foam roof cost?
- What are some case studies of spray foam roofs installed years ago?
And if you’d like to compare spray foam to other traditional roofing systems, such as:
- Metal
- Single-ply (TPO and EPDM)
- BUR
Please consider downloading our eBook below.