If you’ve received multiple quotes for a commercial roofing project, you might wonder why some are significantly higher than others.
While it may be tempting to go with the lowest bid, understanding everything that goes into a roofing quote can help you make an informed decision.
This article covers:
- Travel costs
- Experienced workers
- Top-of-the-line materials and equipment
- The cost of doing things right
- The learning curve for installing certain roofing systems
- Material versus labor costs
If you’re pressed for time, skip ahead to the section about “The cost of doing things right.” This will have the greatest impact on costs and the pitfalls of choosing an unethical contractor.
Let’s get started:
- Travel Costs
If your roofing contractor has to travel a considerable distance to your location, this will factor into the overall cost. Fuel, hotel stays, and travel expenses for the crew usually cost 5-10% of the total project’s price.
Local contractors may have lower travel costs, but that doesn’t necessarily mean they are the best choice for your project.
A high-quality roofing contractor from out of town may still be the better option if they install a better roofing system, have more experienced and trained workers, and/or have a better track record of successful projects.
NOTE: Spending 5-10% more is nothing to ensure the job is done right. It would be unwise to save the 5% and have a project that you aren’t confident will be done absolutely perfectly.
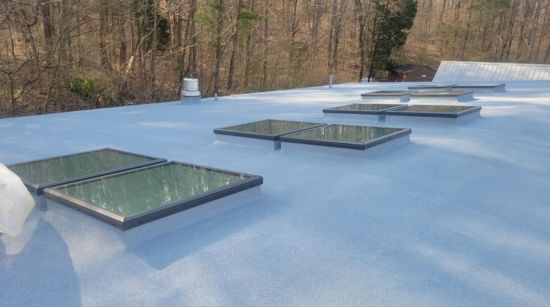
- Experienced Workers
A well-trained, experienced roofing crew costs more than a crew of lower-paid, less-experienced workers.
Lower quotes might come from companies that rely on temporary labor or contractors with little longevity.
It would be foolish to compromise quality for cost.
- Top-Of-The-Line Materials and Equipment
Not all roofing materials are created equal. There’s a difference between purchasing materials at Home Depot and purchasing products through manufacturers.
Manufacturers don’t sell their products to just anyone. They want to ensure that whoever installs their materials is an approved contractor and does it according to their specifications. Therefore, extensive training and company longevity are required to purchase materials.
High-quality roofing systems, including premium silicone coatings and spray foam, are more expensive than other alternatives like single-ply systems.
Additionally, reputable roofing contractors invest in state-of-the-art equipment to ensure precise installation. Cutting corners on materials and equipment may reduce the upfront cost, but it often leads to higher maintenance expenses and a potentially shorter roof lifespan.
Note: This is eye-opening. The cost of a roofing project is the combination of material and labor costs. For example, roughly 60% of the cost of a spray foam roofing project is materials, and 40% is labor. The reverse is true for all other traditional roofing systems.
Think about that for a second.
Wouldn’t you want the majority of the cost to be materials? Materials that “essentially” work on your roof for 10+ years, every day and night, instead of labor costs that disappear once the installation is over.

- The Cost of Doing Things Right
Some contractors will do the bare minimum (we’ve seen it all too often) to install a roof and move on to the next project, while others take the time to do things the right way.
This includes looking at the roof today and assessing its current conditions. Here are some questions a salesperson could be thinking about:
- What areas are leaking, and why is that so? Are there rooftop units in that area?
- Is water building up in certain areas? Why is that so? Are the drains clogged?
- Is there a way to re-route water to reduce future leaks?
- Can the roof slope be redesigned to improve water flow?
- Is there enough ventilation? Should additional vents be installed?
- Do new or additional drains need to be installed? Is the gutter system working correctly?
Here are other things to consider that can greatly influence the cost of a project:
- Removing wet insulation before installing the new roof. Skipping this step will reduce costs and labor hours, and the roof will look great on day 1, but it can lead to blistering, improper slope, membrane damage, and continued leaking down the road.
- Recommending a restoration versus a complete tear-off. Some contractors will automatically recommend a complete tear-off because it’s a higher-dollar job. If your roof has less than 25% wet insulation, the membrane adhesion is decent, and there’s been annual maintenance, your roof could be eligible for a restoration. A restoration will likely cost half of a complete tear-off and replacement (or in some cases, even less).
- Keeping budget and goals in mind. Can we do this section this year and hold off on others until next year? Would the company benefit from increasing the roof’s R-value by an R-10, R-15…or not at all?
A higher quote often reflects doing the right thing. Make sure to compare “scopes of work” when reviewing proposals.
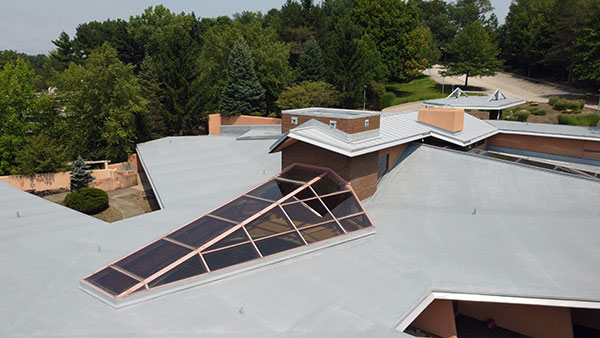
- The Learning Curve for Installing Certain Roofing Systems
Some roofing systems require more expertise than others.
For example, spray polyurethane foam (SPF) requires significant training and skill to apply correctly, whereas single-ply roofing systems are more straightforward.
Because the SPF application has a steeper learning curve, hiring a team that knows what they’re doing is crucial—otherwise, you could end up with an ineffective roofing system.
The extra training and experience required to install spray foam properly contribute to the overall cost.
- Material Costs vs. Labor Costs
One reason TPO quotes tend to be lower is that the material itself is inexpensive, and the labor required to install it doesn’t need years of experience.
However, SPF has a different cost structure—while labor costs can be lower because fewer workers are needed, material costs are higher. This is important to consider when comparing quotes.
A single-ply installation might save money upfront, but may not provide the same energy efficiency as an SPF system. Spray foam roofs are seamless with no fasteners, which greatly reduces the likelihood of a leak and eliminates thermal bridging when compared to other systems.
Here is a short video of spray foam roofing being installed:
Making the Right Choice
When comparing roofing quotes, looking beyond the bottom line is important.
A cheaper bid might seem attractive, but it often comes with trade-offs, such as lower-quality materials, inexperienced workers, and shortcuts that can lead to costly repairs down the road.
At the end of the day, investing in quality workmanship, premium materials, and ethical roofing practices will always pay off.
When evaluating roofing quotes, ask questions, understand what’s included, and choose a contractor who prioritizes the long-term health of your roof, not just the initial installation cost and how it looks on Day 1.