Perhaps your roof is leaking, and you know it’s ancient. It’s time for a brand-new roofing system.
But what roofing system should you get?
Like most building owners, you want the roof that costs the least.
The problem is there are many variables when it comes to cost, such as:
- Different roofing systems cost different
- Current material prices versus previous material costs
- The size of your roof
- The number of penetrations
- How far away are you from the roofing contractor
- How much wet insulation does your current roof have
- How long of a warranty is desired
- How much R-value is desired
- How much roof preparation is needed
- How easy is it to access the roof?
- Scope of work/roof details
And so you’re aware, West Roofing Systems has been in commercial roofing since 1979. We want to give every building owner an accurate ballpark cost, but it isn’t easy with so many variables. Hopefully, after this article, you’ll get a good look at the cost of a new roof for your building.
This article has been reviewed, edited, and approved for publishing by a West Roofing Systems salesperson with more than 30 years of experience.
Let’s get started!
Different roofing systems cost different
Here are the most common ballpark costs per roofing system:
- Metal – $10 – $15 per square foot
- Single-Ply (TPO, EPDM) – $8 – $12 per square foot
- Spray Foam – $6 – $12 per square foot
- Roof Coatings – $4 – $8 per square foot
As you’ll see later, these cost ranges can vary depending on other factors. For example, a 100,000 sq. ft. flat roof with very few penetrations could cost $5 per square foot. There’s not much cutting and custom fitting, so it’s easy for a single-ply system to be rolled out and installed.
That same roof could have hundreds of penetrations, such as pipes, windows, skylights, exhausts, drains, etc. The cost is likely $12 per square foot for single-ply and only $7 for a spray foam roof. Spray foam is fluid-applied, so penetrations don’t interrupt the installation process.
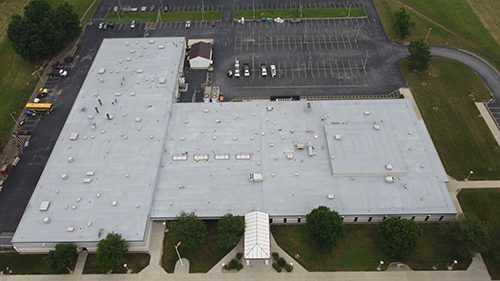
Current material prices versus previous material costs
Two years ago, $4 – $7 per square foot would be the ballpark cost for a spray foam roof. Today, it’s $6 – $12.
The materials used to install every roofing system have substantially increased in cost.
It’s pretty much in line with gas prices. The prices have skyrocketed and more recently (September 2022), have come down a little.
Will they ever be the same as 2020 prices? Probably not.
Note: Prices in New York or California are higher than in Ohio. Location and “Cost of Living” are higher and lower in different states.
The size of your roof
The larger the roof, the lower in cost per square foot. This is because overhead costs don’t vary much per job.
Say there’s a 1000 sq. ft. job and a 100,000 sq. ft. job.
And the cost for a new commercial roof is $6 – $12 per sq. ft.
The 1000 sq. ft. job will probably be $12 per square foot.
The 100,000 sq. ft. job will probably be $6 per square foot.
It’s economies of scale. It’s similar to buying a 24pk of Pepsi versus a 6pk. The price per can is smaller with the higher bulk amount.
The number of penetrations
A penetration is a skylight, pipe, HVAC unit, exhaust, drain, or anything that comes through the roof. These add costs to traditional roofing systems (such as TPO) because the sheets need to be cut. Adhesives, boots, and sealants also need to be used to make penetrations watertight.
Since spray foam and roof coating systems are fluid-applied, the installation process isn’t interrupted. Therefore, the number of penetrations only adds costs to single-ply and metal roofs.
How far away are you from the roofing contractor?
The further away you are from the roofing contractor, the more gas that’s needed to haul equipment, materials, and labor to the job site.
This doesn’t mean automatically choosing the roofing contractor closest to you.
A quality installation is much more critical. It’s more beneficial to pay more for a roofing contractor far away, knowing the job will get done right.
The headaches involved with leaking, service calls, repairs, warranty work, etc., can all be erased by choosing a contractor that knows what they are doing.
How much wet insulation does your current roof have?
No roof should be installed over wet insulation…period. If you don’t remove it, blisters can happen when that trapped water gets warm over the summer and tries to evaporate through the roof.
Water under the membrane can freeze in the winter and expand an existing water entry point when it thaws.
A roofing contractor will pull core samples and/or perform an infrared inspection to determine the presence of wet insulation.
The project’s cost will be less if only 5% of the roof is saturated versus the same roof that’s 15% saturated.
These areas need to be torn out and replaced with similar material. The wet materials need to be transported to a landfill.
Suppose 25% or more of your roof is saturated. In that case, a complete tear-off may be recommended, which will significantly increase the cost of your project.
How long of a warranty is desired
Most roofing systems offer different warranty durations. According to A-Denver Roofing, a thicker TPO membrane (45 mils to 60 mils) can offer a more extended warranty. The cost is only increased by 4%.
For spray foam and roof coating systems, the thickness of the coating determines the length of the warranty. For example:
- For a 10-year warranty, 20 mils of coating are installed
- For a 15-year warranty, 25 mils of coating are installed
- For a 20-year warranty, 30 mils of coating are installed
There is an additional cost because more materials are being used. The cost increase fluctuates with material prices.
How much R-value is desired
This goes along with warranty durations. The more R-value that’s desired, the more materials that will be needed.
On metal and single-ply roofs, the most common way to increase R-value is to install a polyiso board. Polyiso board has an R-value of 5.5 per inch of thickness. If you need to hit a minimum R-value, because by code, it’s a new construction project, you’ll likely need to hit a minimum of an R-25. In this case, you’d need more than 4 inches of polyiso board to be code compliant.
Suppose you’re roofing over an existing roof. In that case, there’s no minimum R-value, and you can install as much or as little insulation as you’d like.
Spray foam roofs create R-value through the foam itself. The foam has an R-value of 6.5 per inch of thickness. For more R-value, a contractor increases the amount of foam that’s installed. The typical application (for an existing roof) is an average of 1.5 inches of foam. In some cases, more than 4-5 inches of foam can be installed.
Roof coating systems don’t increase R-value.
How much roof preparation is needed
The more labor hours needed to prepare your roof for a new installation, the more your project will cost.
- Some roofs have a bunch of wet insulation to remove.
- Some roofs have a damaged or cracked membrane that needs to be replaced.
- Some roofs have loose rocks that need to be vacuumed off.
- Some roofs have loose seams that need to be tightened or removed.
- Some roofs need a primer for adhesion purposes.
- Some roofs require the existing roof to fully adhere to the insulation. If that’s not the case, a coverboard must be installed first.
Every roof system requires different ways of preparing the existing roof.
How easy is it to access the roof?
Not all commercial roofs are flat; not all roofs can be walked on. Additional costs can occur when your contractor has limited access to the roof.
The roof’s height and distance can influence your installation’s cost. Sloped roofs often require the contractors to use a man lift or rappelling gear for installation.
To move the crew and equipment, contractors may need to rent conveyance equipment, such as a crane or passenger hoist.
Teams working in secure locations, such as airports, often need to update their Secure Identification Display Area (SIDA) authorization. This includes background checks and fingerprinting, which is an added cost for the contractors.
Scope of work/roof details
Sometimes additional work is added to a project to ensure the roof is watertight and doesn’t allow any standing water. These additional roof details can add cost to your project.
For example, does an internal draining system need to be installed? Is the roof currently sagging? If the slope is off, a tapered polyiso board installation will be required, which is an expensive add-on.
You can use spray foam to raise select roof areas by simply spraying more product.
Conclusion
Hopefully, you’ve learned a few things that can alter the cost of a commercial roofing project. One word of advice: get a quote from contractors installing different roofing systems. Get a metal quote, a TPO quote, and a spray foam roofing quote.
If you’d like to learn the pros and cons of each roofing system, please download the eBook below.