So, your roof is leaking and you’re dreading getting it replaced.
How much is it going to cost?
How long will the company be here?
All these sorts of questions come up.
Then you hear about roof coating systems and how they cost half of a full roof replacement.
You think:
“Is that true?”
“How do they work”
And “Is this an option for my roof?”
In this article, you’ll learn:
- What’s a roof coating system?
- What existing roofs qualify for a roof coating system?
- Why do building owners choose coating systems versus a full replacement?
- Are there any benefits of going with a full replacement instead of doing a coating system?
At the end of this article, there are 2 case studies of roof coating system installations.
And just so you’re aware, West Roofing Systems has been in commercial roofing since 1979. We specialize in spray polyurethane foam roofing systems, which use roof coatings to protect the foam roof from UV rays.
Starting around 2008, roof coatings systems began to be used on their own as a way to restore a roof versus doing a complete tear-off.
Let’s get started!
What’s a roof coating system?
A roof coating system is a high-solid, long-lasting, waterproof, paint-like material that’s been engineered to withstand weathering events.
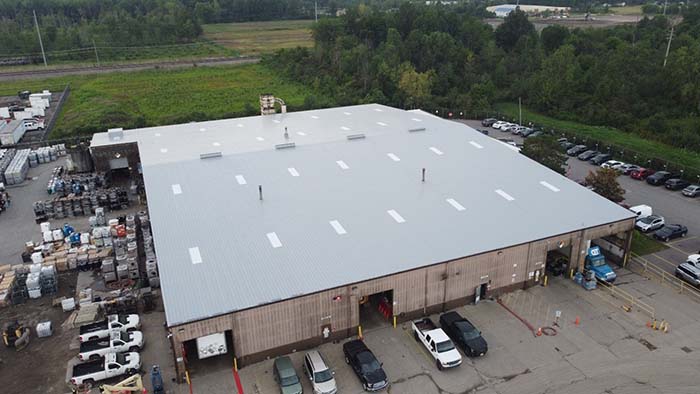
The coating can be rolled or spray applied.
The most important part of the system is the preparation of the existing roof. This includes:
- Identifying and replacing wet insulation
- Identifying and replacing any damaged membrane
- Adhesion tests with the coating
- Cleaning and/or priming the roof
- Seam reinforcements
Once the roof is prepared, a contractor will install the coating at the manufacturer’s recommended thickness to grant the desired warranty.
- A 10-year-warranty usually gets 20 mils of coating installed over the field of the roof
- A 15-year-warranty usually gets 25 mils of coating installed over the field of the roof
- A 20-year-warranty usually gets 30 mils of coating installed over the field of the roof
What existing roofs qualify for a roof coating system?
Every type of roof can be coated. This includes metal, single-ply, built-ups, and modified bitumen.
The only roof system that shouldn’t be coated is a gravel built-up roof. It’s not cost-effective because a large amount of coating would be needed to fill all the nooks and crannies.
Learn more about which roof systems should be coated or not in this blog post.
One of the biggest problems with roof coating systems is eligibility. To be eligible, a roof must have:
- 75% or more of the roof’s insulation is dry
- There’s been annual maintenance on the roof
- The seams are in decent shape
If anyone of these statements isn’t true, a roofing contractor will likely advise you to lean towards a complete tear-off.
Why do building owners choose coating systems versus a full replacement?
Reason #1 – Cost
A roof coating system costs around half of a full roof replacement. This is because, at most, 25% of the roof is removed and replaced. A full roof replacement removes and replaces 100% of the roof.
Reason #2 – New warranty
Most roof coating manufacturers offer 10-to 20-year warranties. This includes labor and materials.
Reason #3 – Renewable
Let’s say you get a coating system installed today with a 10-year warranty. Most likely, a manufacturer will require a coating thickness level of 20 mils.
10 years from now, the 20 mils may be down to 7-8 mils.
A contractor can clean the roof, bring the level of coating back to 20 mils, and a new 10-year-warranty can be granted.
This process can repeat over and over again, saving the building owner time and money in the long run.
Reason #4 – Seamless
Seams are where most roofing leaks occur.
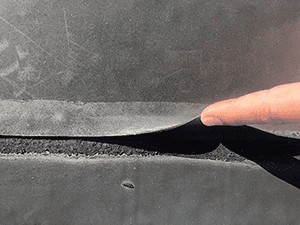
Seams separate because of old age (years of the roof fluctuating with heat and cold temperatures) or the adhesive holding them together wears away.
A roof coating system is fluid-applied, so the entire roof is completely seamless.
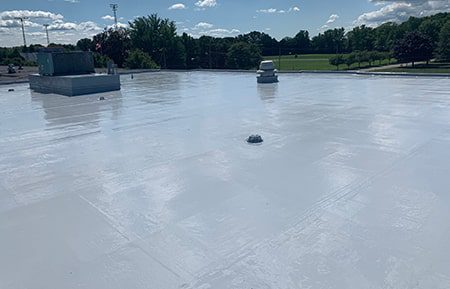
With no seams, the most likely cause of a roof leak is eliminated.
Reason #5 – Not considered a roof system
Per building code, you can have a maximum of two roofing systems on a commercial building.
If you already have two roof systems installed, you must install a coating system or remove at least one roofing system before installing another.
A roof coating system is considered “maintenance” and isn’t considered another “roofing system.”
Honorable mentions
- Since it’s fluid-applied, it can be installed very quickly, regardless of the number of penetrations. Other roofing systems that come in sheets need special attention when installed around HVAC units, pipes, drains, etc.
- Since there’s minimal tear-off (only the wet areas are removed and replaced) and very little equipment is required, there’s very little interruption to a building owner.
- Reflectivity. If your roof is dark-colored, it gets very hot in the Summer. By installing a white or grey-colored coating system, you will reduce the roof temperature. This will lower the heat entering your building and reduce energy costs.
Are there any benefits of going with a full replacement instead of a coating system?
Yes. If you choose a full roof replacement, you have the opportunity to increase your roof system’s R-value.
One of the downfalls with roof coating systems is that they do not increase your roof system’s R-value.
If you’re unaware, R-value is the capacity of an insulating material to resist heat flow. The higher R-value your roof has, the less heat or cool that will escape through the roof.
Every roofing system can increase R-value. Traditional roofing systems increase R-value through insulation boards.
A roof system that most don’t know about is spray polyurethane foam. Spray foam has the highest R-value per inch of thickness of any roofing system.
Although doing a full replacement is more expensive than a coating system, in some cases, you can increase the R-value so much that the roof will have a buyback period.
Check out this case study of Texas A&M, which recovered the cost of 27 spray foam roofing installations through energy savings in 4.5 years.
Roof Coating Case Studies
Here are some case studies of roof coating installations:
Midview High School – Learn how a silicone roof coating system gets Midview to critical year 11.
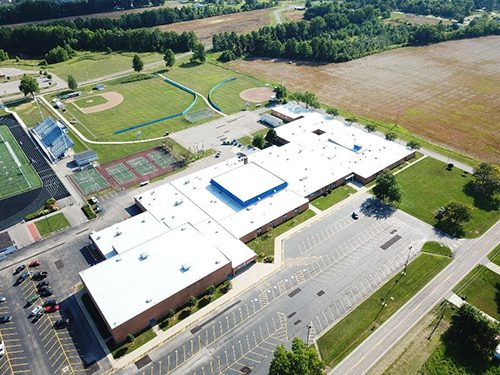
Gorilla Glue – Learn how Gorilla Glue saved $2.5M by avoiding a full roof replacement.
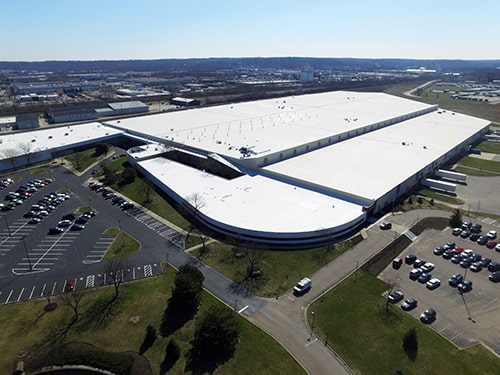