Maybe you just got your quote back from a spray foam roofing company and the price came back higher than expected?
Maybe you got a quote last Summer and the quote was $50,000, but this year it’s $80,000?
What the heck happened?
There are three main reasons why the price of spray foam roofing has increased:
- The manufacturers of spray foam materials have increased their prices by almost double.
- It’s hard to find roofing labor, therefore starting wages have increased
- Gas prices are high
Supply chain delays, raw material shortages, and labor shortages all factor into the equation.
But as a building owner who needs their roof fixed, what should you do? Below are four options:
- Option 1 – wait until the economy recovers
- Option 2 – do a temporary fix instead
- Option 3 – get your entire roof fixed now
- Option 4 – go with another roofing system
Some of these options are recommended…and some aren’t. Please read below.
And just so you’re aware, West Roofing Systems has been in commercial roofing since 1979. We’ve seen the companies that get burned with repair after repair and finally have to replace the entire roof anyways. We’ve also seen the ones where it makes sense to get their roof done now because it’s the better lifetime cost decision.
Every piece of content written is reviewed and edited by a former spray foam installer, who is now a spray foam roofing salesman with more than 30 years in the industry.
Let’s get started!
Option 1 – wait until the economy recovers
You can wait and see if the prices go back down, but there’s no guarantee that it will. It seems that once prices increase, it’s rare they ever go back down.
Think: Has your steak bowl at Chipotle ever gone down in price?
There is some optimism.
Here’s the 15-year-history of gas prices in Ohio:
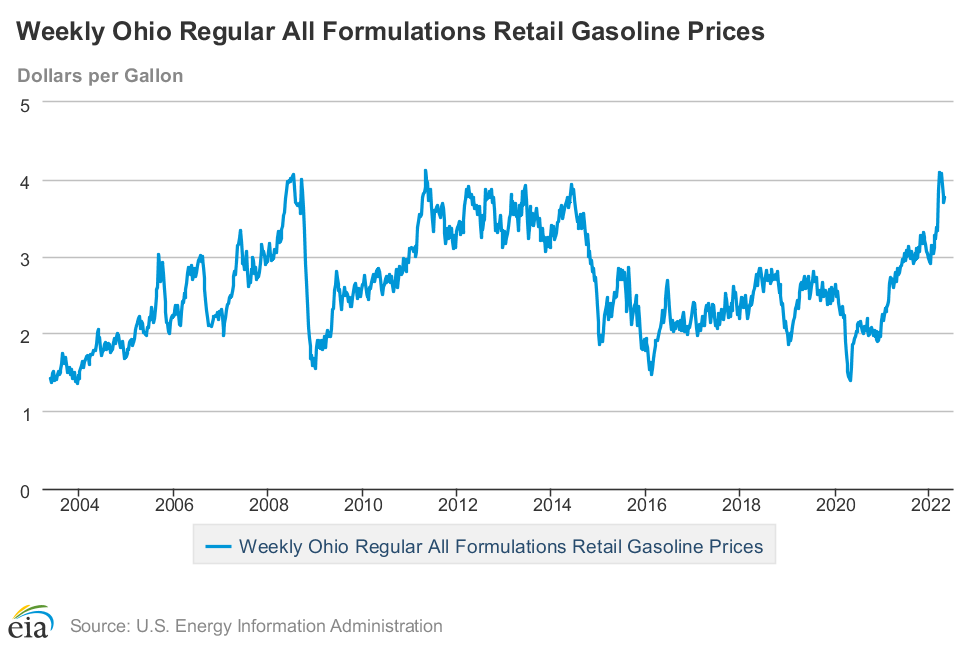
Here’s a 15-year-history of gold prices:
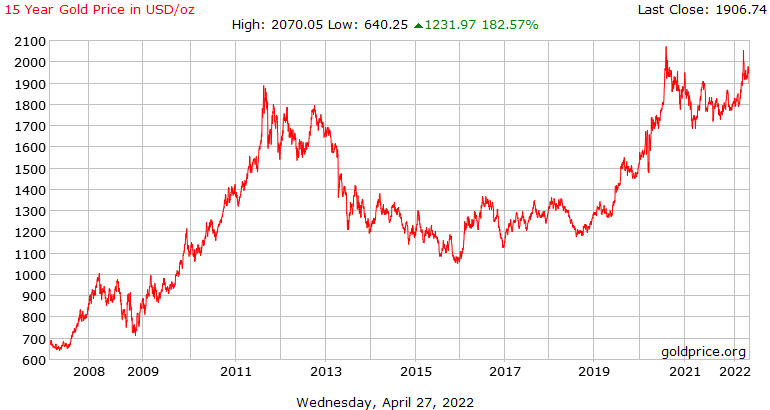
Unfortunately, we couldn’t find the 15-year prices of isocyanate and polyol/resin (the two chemicals that make spray polyurethane foam).
As you can see, prices fluctuate differently in every market.
So, how does this help you when considering a spray foam roof? Will the price of materials fluctuate like these markets?
Who knows?
The best thing to do is to contact an expert who can tell (and show you with pictures) the current conditions of your roof and provide recommendations that are based on what they found while surveying your building.
They may recommend waiting it out…or that it’s beneficial to act immediately.
Option 2 – temporary fix
If your roof is in good shape and is only leaking in a few areas, you might be able to repair the roof. This way, you can wait out the current price hike and get a roof next year when “hopefully” everything is back to normal.
One thing to look out for is continual repairs.
We’ve seen roofs that get repaired over and over again…and then have to get a full roof replacement anyways.
To make sure this doesn’t happen to you, be sure to get a full roof report with a life expectancy.
In many cases, once one part of the roof is failing, other parts of the roof aren’t far behind.
It would be detrimental to a company’s bottom line to spend $10,000 after $10,000 on repairs, and then have to pay for a complete tear-off and replacement two years later.
Option 3 – get your roof fixed now
Yes, spray foam roofing prices are higher now than ever. But if you have a roof that’s leaking, you’re losing money every month with higher energy bills.
Say your energy bills are $1000/month with a roof that’s performing well. Now it’s $1500 because heat/cool air is going right through the roof.
Spray foam can reduce your energy bills by an average of 15-30%. Your new energy bills could be $850/month if it was reduced by 15%.
$850 vs $1500. Every month you’re losing $650.
That was just a simple example.
Every roof, climate, amount of leaking/damage, HVAC efficiency, business operations, etc. can greatly fluctuate these numbers.
NOTE: And who knows, what if the cost of materials never comes down?
One last thing to consider is if your roof is leaking, water is getting under your membrane and saturating your insulation.
Every time it rains in the future, more of your insulation is getting wet. When it’s time to get your spray foam roof, all the wet insulation needs to be removed, transported to a landfill, and replaced before the installation can happen.
A roof where 5% of the insulation is wet versus the same roof where 20% of the insulation is wet, is a big difference in cost.
No matter what roofing system you choose, all the wet insulation needs to be removed and replaced before a new system can be installed.
Every month you wait, you increase the cost of the project, no matter which roofing system you choose to install.
Option 4 – could you go with another roofing system?
You can go with a metal roof, but metal is more expensive than spray foam. You’ll get longevity, but you won’t get any of the other benefits of a spray foam roof, such as being seamless, increasing R-value, ease of maintenance, etc.
You can go with a single-ply roof, but with supply chain issues and labor shortages, polyiso board isn’t available. Since TPO and EPDM have no insulating value, they lay the polyiso board down first, then lay the rubber sheets over the board.
Single-ply roofs also rely on fasteners to make their rubber sheets watertight. There are talks that fasteners aren’t available for the same reasons as polyiso board.
With no polyiso board or fasteners available, single-ply roofs aren’t an option right now.
Should you wait to get your spray foam roof installed or do it now?
Ultimately, this comes down to the current conditions of your roof, your budget, and whether you believe the prices for spray foam materials will come down.
Since none of us can control the cost of materials, your best option is to get your roof looked at.
A spray foam contractor can provide you with recommended options based on what they find after pulling core samples, doing a visual inspection, and possibly doing an infrared survey.
Other related posts: