So, you have a metal roof and it’s leaking.
Your first thoughts might be “how much is it going to cost to rip all these panels off and install new ones?
You wonder if there are other cost-effective options?
The good news is, if the metal roof isn’t in that bad of shape, you can install a fluid-applied roofing system over what’s there.
In simplest terms, spray-on roofing systems save money because it eliminates the complete tear-off.
In this article, you’ll learn:
- How metal roofs leak
- If you need to remove all your metals panels or not
- What spray-on roofing systems you can install
- The benefits (and problems) of spray-on roofing systems
- A case study of spray foam installed over a 384,000 sq. ft. metal roof
And so you’re aware, we only write articles about true events and experiences. West Roofing Systems produces every piece of content in-house. Every article is reviewed and edited by a roofer/salesman with more than 30+ years of experience in the field.
Let’s get started!
How do metal roofs leak?
Old age
After 20 years, metal roofs can begin to rust out. It’s what happens when things get old, they break down.
Flashings
Flashings are pieces of metal installed around vertical structures.
Their purpose is to prevent water from entering the building.
The most common type of vertical structures are pipes, skylights, curbs, HVAC units, and exhausts.
Custom cutting, termination metal, and sealants all need to be used to correctly install a flashing. If flashings aren’t installed correctly or degrade over time, these become common areas where water enters the building.
Bad Seams
Seams can be installed incorrectly during installation, or they can degrade over time. When metal panels expand and contract with the weather, it’s the seams that take on the most pressure.
Will you need to remove all your metal panels?
If you already have two roofing systems installed, you will have to remove all your panels. According to building code, the maximum number of roofing systems that a building can have is two.
If you have one roofing system, you won’t need to remove all your metal panels.
To determine if a metal panel needs to be removed, a roofing contractor looks at the overall health of the panels and decides.
What fluid-applied roofing systems can you install?
There are two, spray polyurethane foam and silicone roof coating systems.
Spray polyurethane foam (SPF)
SPF is a mixture of two reactive chemicals, an A and a B side, that are heated and mixed to produce closed-cell spray foam.
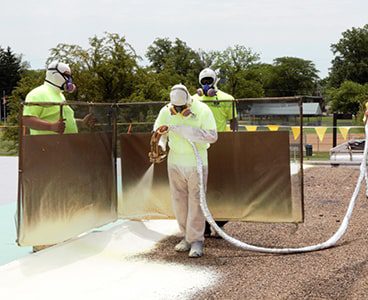
Spray foam fills in all the tiny pinholes that a metal roof can have.
Spray foam also makes the metal roof all one seamless layer, which greatly reduces the likelihood of future leaking.
Spray foam has an R-value of 6.5 per inch of thickness, so if you’re interested in reducing your energy costs, SPF is a great option.
Here’s a start-to-finish video of spray foam being installed over an existing metal roof:
Silicone roof coating systems
A popular restoration option is to install silicone roof coatings. Silicone is fluid-applied onto a metal roof.
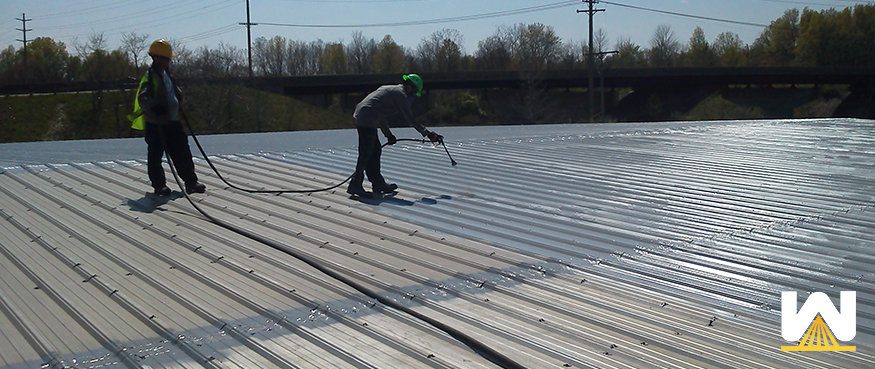
Silicone also fills all the pinholes that a metal roof can have, creating a seamless membrane.
The benefits (and problems) of spray foam roofing systems
Here are some of the benefits of spray foam roofing systems.
Seamless
Metal roofs provide entries for water entry through tiny pinholes, rusted away areas, etc.
Spray foam is fluid-applied that expands 30x in size within seconds. It will fill in any openings, big or microscopic.
Leak-free
Spray foam is closed-cell, which means that even if the foam gets a crack, cut, or puncture, water cannot expand. Water will sit in that cut until it’s repaired.
This is far different than typical roof insulation, in which when water enters, it can spread and saturate a large area.
R-value
Spray foam has the highest R-value per inch of thickness than any other roof insulation. SPF has an R-value of 6.5. This helps to restrict the heat/cool from leaving or entering your building. You should expect a reduction in your energy bills after a spray foam installation.
Click here to learn more benefits of a spray foam roof.
Here are some of the problems with spray foam roofing systems.
Limited Installation Window
For spray foam to cure and perform correctly, it needs to be at least 50 degrees when it’s installed. Also, it’s recommended to not spray foam when it’s too windy outside. Spray foam is very light, which allows wind to carry it onto undesirable items, such as nearby cars.
Non-certified Installers
It’s sad but true, but some spray foam contractors don’t know what they are doing. Spray foam is a chemical reaction that can change with several variables. It’s important to use a contractor that knows the science of spray foam, and one that’s certified with the SPFA (Spray Polyurethane Foam Alliance).
Maintenance is recommended
A building owner should have a maintenance/service plan with any roofing system they install. Spray foam is a little different though.
If a spray foam roof gets a cut, crack, or puncture, and foam is exposed, UV rays from the sun will degrade the foam.
The crack would have to penetrate the granules and coating on the roof to get to the foam, but it’s happened before.
The problem is when minor issues get ignored. If any roof is abandoned for years and years, minor repairs can become big repairs.
When a crack is noticed, a contractor will dry the area out, apply caulk/coating, and smooth the area out.
Maintenance/service is recommended 2x/yr and costs roughly 2-5 cents per sq. ft.
Click here to learn more about the problems with spray foam roofing.
Case study: Spray foam installed over a 384,000 sq. ft. metal roof
MTD in Willard, OH had a metal roof that was leaking. Instead of removing 384,000 sq. ft. of metal panels, they learned that it would be cost-effective to apply spray foam over their existing roof.
They were skeptical though. So, they tested a 16,000 sq. ft. section and looked at the performance after 5 years.
The spray foam performed great, so the rest of the roof was given the go.
But there was a problem…there was a 52-day timeline to complete the project.
Robots…yes, robots were used to help complete the project on time.
Click here to learn more about spray foam over the metal roof at MTD.
What should you do now?
If I had a leaking metal roof, I would research the different repair/restoration options I had.
Then once I had a good idea of what I was looking for, I’d reach out to a couple of roofing contractors to give me their opinion on what options I have.
If you’d like West Roofing Systems to look at your roof, please request a quote.
We’ve been around since 1979. We always provide the customer with the most cost-effective repair options.
If you’d like to learn more about spray foam roofing, please check out the Spray Foam Cheat Sheet below.