Looking for a way to stop the leaks on your shingle roof? If so, you have a few options. You can replace the shingles with new ones, or you can install spray foam.
You may be thinking, “Spray foam? That’ll make my roof look, well…not the greatest.”
If aesthetics are important to your business or building, spraying foam over your shingle roof may not be the best option for you.
However, if you run into a situation where you have a roof leak, and it’s an area of the roof that’s hidden from public view, spray foam might be the best waterproofing roofing option for you.
West Roofing Systems has been spraying foam on roofs since 1979, which have included shingled structures such as churches, factories and schools.
All of these structures have used spray foam to stop leaks over their shingled roofs because it’s an easy repair (can spray foam right over top of shingles) and it creates a monolithic layer over an area prone to leaks, such as shingles running into a vertical wall.
Let’s begin…
What is a spray foam roof?
Spray foam roofs are installed by spraying a liquid on the existing roof and allowing it to expand into a foam. This process means that the foam can conform to all roof shapes and types, even irregularly shaped roofs. After cleaning the existing roof, the spray foam roof can be applied directly over asphalt, shingles, concrete, metal and wood.
Building owners choose spray foam over other roofing solutions for three main reasons:
- Spray foam has the highest R-value of any roofing system, therefore saving money on energy bills
- Spray foam roofs can last indefinitely
- Spray foam roofs can go over an existing roof (if unsaturated) saving money on costly tear off charges
NOTE: most shingle roofs have zero insulation. A reduction in energy costs is expected with the addition of a spray foam application.
How does spray foam get applied to shingle roofs?
Step 1: Determine the condition of the shingles
If the shingles are curled up or degraded so badly that the nails are exposed, you’re better off tearing off all the shingles and replacing with new ones.
If some shingles are in bad condition, the remainder of them are probably not too far behind.
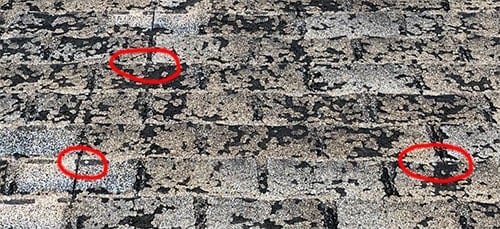
Look at the photo below to see an example of exposed nails, an indication the shingles are past their lifetime.
If your shingle roof doesn’t have nails exposed and the ends of the shingles are not curled upwards, then your shingle roof is in good condition to be spray foamed.
Step 2: Determine the condition of the underlying substrate
The underlying substrate on a shingle roof is 99% of the time wood. To identify saturated areas, a roofing expert will determine saturation in two ways:
- By performing a visual inspection inside of the building, looking up and noticing the bottom of the wood decking. If all the wood is there and there is no deterioration, then you’re in good working order. If wood is missing, or completely rotted, then you’ll need to replace the wood before putting new shingles on.
- By walking on top of the shingle roof and determining signs of weak support. Areas of concern will be located from the inside of the building, but during an inspection, a roofing contractor will notice signs of weak support while walking around the roof.
Step 3: Clean the shingles
A roofing contractor will usually use air (such as a powerful leaf blower) to remove all loose sediments off the shingles, but if there’s moss or plant life present, pressurized water will be used.
Cleaning the shingles is important for spray foam to adhere properly. If the shingles are not clean (and dry) before spraying foam, there can be adhesion problems.
Step 4: Spray foam over the shingles
Depending on the R value you’re seeking, that will determine the thickness of the spray foam application. For most roofs, an average of 1.5” of thickness is the usual diagnosis.
Spray foam has an R value of 6.6 per inch, so when a 1.5” application is sprayed down, you’ll have an R value of 9.9. If you seek more R value than a 9.9, increase the thickness of spray foam until you get your desired R value.
Since spray foam degrades with UV exposure, a thin layer (20-30 mils) of silicone coating is applied on top. The silicone coating not only protects the foam from UV degradation, but also increases its strength.
Successful spray foam over shingle roof scenarios
Here are two scenarios where spray foam has helped restore a shingled roof:
Scenario #1 – John Muir Elementary School
The school had leaks coming from chimney locations, as well as a couple of leaks that deteriorated the roof deck.
The school’s roof was installed with slate shingles that were almost 90 years old! It was drastically more cost-effective to spray foam the shingles as opposed to tearing off all the shingles and replacing.
The first step was to spot remove the slate shingles in the location of active leaks. The second step was to remove the locations of deteriorating wood decking.
Next, we replaced the saturated wood decking with upgraded, exterior grade plywood that was laminated together with construction adhesive and fastened to the structural members.
The chimneys were fully encapsulated with spray foam. This eliminated concerns for additional deterioration and provided a waterproof and watertight structure.
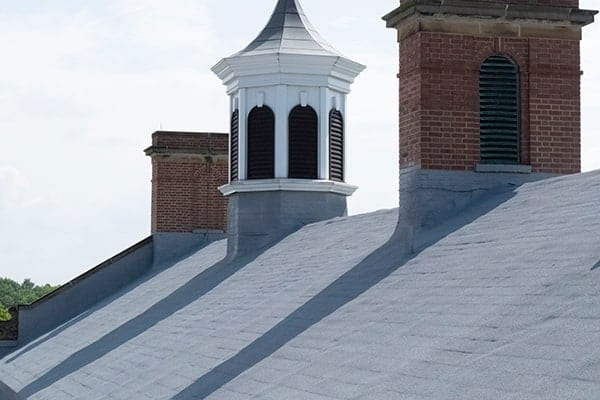
Spray foam was laid down at 1.5” thick and silicone coating (two coats) was laid down at 30 mils thick. Special attention was given to the topcoat of coating, which included a granule application, which not only added strength to the roof, but also eliminated visible pass lines.
Scenario #2 – Shingle roof on a Church
This church with a shingle roof had some leaks. We went up onto the roof and determined the water was draining into a vertical wall.
We sprayed the whole back wall with spray foam to create a monolithic layer that runs high up the vertical wall.
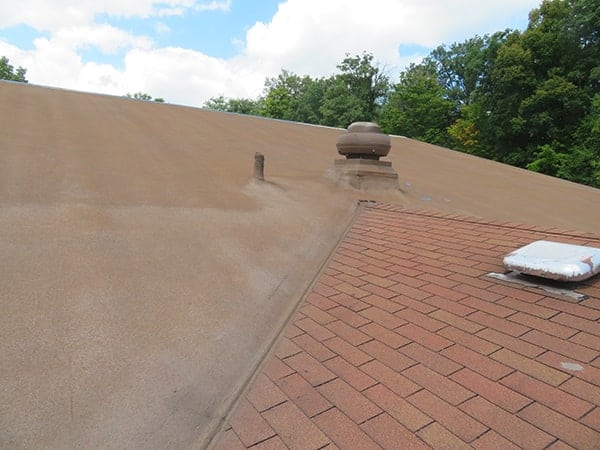
With the shingles running into a wall, water pooling occurs, and it created an opportunity for water to enter the church.
The decision to spray foam over a certain area, as opposed to removing all the shingles and replacing was a far superior cost-effective option. In addition, spray foam stops the leaks where water was most prone to enter the building (where the shingles met the vertical wall).
Recap of shingle roofs and spray foam
As we said before, shingle roofs can absolutely be spray foamed, it just a matter of purpose and aesthetics that come into equation. If you care greatly about the look of your roof (like the front of a church), spray foam might not be the best option.
If you don’t care about aesthetics and are concerned with stopping your leaking shingle roof, spray foam is a great, cost-effective option.
Need more information about spray foam roofs? Be sure to take a glance at our Ultimate Guide to Spray Foam Roofing (no download required!)
In this guide, you’ll find more information about spray foam roofs such as:
- costs
- installation
- performance
- how long it lasts
- how the re-coat process works
- and much more