If your commercial roof can be restored, you are one lucky camper.
Why?
Choosing to restore your roof instead of a complete tear-off, will save you money, get you a brand-new warranty, and reduce your energy costs.
Can every roof type be restored?
At West Roofing Systems, we’ve been working on commercial roofing systems since 1979, so we know which roofing types make sense (and don’t make sense) to be restored.
In this article, we’ll explain what makes a roof eligible to be restored, as well as what roofing types a silicone restoration coating can be applied to.
What is a roof restoration?
A roof restoration is a way for a commercial roof to extend it’s life (and add performance) while spending 50-70% less than a complete tear off.
What are the benefits of a silicone restoration membrane?
People choose a silicone restoration membrane over re-roofing for numerous reasons.
Cost Savings – One of the top benefits of a Silicone Restoration Membrane is the cost savings. If the existing roof substrate is dry and stable, no roof removal is required, which is a costly addition to roof projects.
Considered Maintenance – The Silicone Restoration Membrane provides a new waterproofing layer over the existing roof membrane, which is considered a maintenance application in lieu of roof replacement. This means the coating application can be done many times without adding additional roof systems, which would eventually require removal per building codes.
Short Project Duration – Another benefit to the SRM system is that it’s installed very quickly, thus reducing any disruptions to the facility operations. A restoration can be completed 60-70% faster than a complete tear off.
Energy Efficient – Most installations utilize a bright white coating application. This reduces energy costs by reflecting more sunlight and absorbing less heat than a standard roof, therefore reducing HVAC usage to cool your building. Using a white silicone roof coating can reduce your energy costs by as much as 15 to 35%.
What makes a commercial roof eligible to be restored?
For a commercial roof to be eligible to be restored, three scenarios need to happen:
1. Less than 25% of the substrate is wet or saturated
If your roof is more than 25% wet, you’re better off tearing the entire roof off down to the deck and starting over. The roof is in bad shape and is more prone to future leaking.
2. The roof has been maintained by a roofing contractor throughout its life
If your roof has been maintained by a roofing contractor throughout its life, chances are repairs have been fixed in a timely matter and you have very little to no saturated areas in your insulation.
3. If it’s a rubber roof, the seams are relatively intact
If you have a rubber roof and the seams aren’t intact, chances are that water has already infiltrated your insulation. And if one seam is lifted, chances are that more seams are in the same shape and will lift very soon.
In this case, it’s best to remove all the rubber and either replace the entire system with new insulation and rubber, or move onto another roofing system, such as spray polyurethane foam.
Now that you know the shape your roof needs to be in order to be eligible for restoration, and you know the benefits of white silicone coating, let’s look at the different types of roofing systems and see if they can be restored.
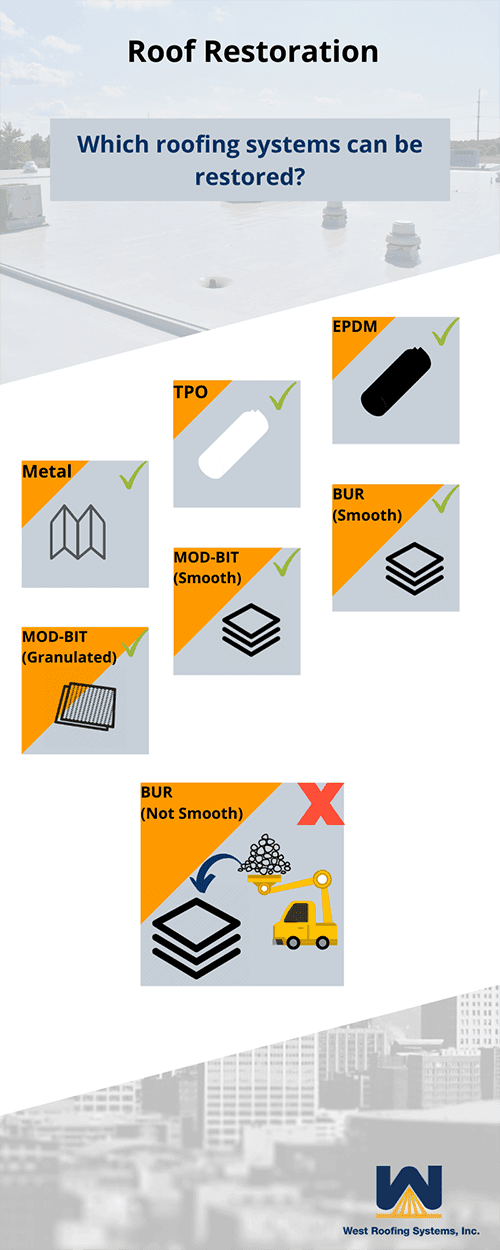
What roofing systems can be restored?
Rubber Roofing Systems (TPO and EPDM)
Rubber roofs are perfect candidates to be restored.
Why?
Restoring your rubber roof is a simple process:
Step 1 – Perform an infrared survey to check for saturated areas
Step 2 – Removing and replacing those saturated areas
Step 3 – Clean the roof with a power washer
Step 4 – Reinforce all seams with polyester-reinforced mesh or self-adhering, reinforcing tape
Step 5 – Spray or roll silicone (depending on the wind and overspray potential) and you’re done.
Some roofs have large amounts of foot traffic, so sand can be embedded into the silicone to not only strengthen the walkway, but also mark the walkway clearly.
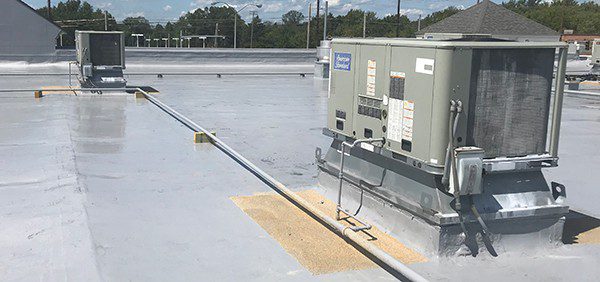
Metal Roofing Systems
Metal roofing systems need to be treated before silicone coating can restore the roof. The reason is so the silicone adheres properly.
Here are the steps for restoring a metal roof:
Step 1: Power wash the entire roof (use primer if there’s rust)
Rust will continue to oxidize your metal roof if not treated.
Step 2: Reinforce all your seams (horizontal and vertical) in one of two ways:
- With polyester reinforced mesh into a liquid top coating
- With self-adhering, reinforcing tape
It’s important to pay special attention to seams because these areas are most prone to leaks. When you have two metal panels coming together, if they aren’t adhered perfectly, it can create an opportunity for water to enter the building.
Step 3: Address fastener heads
Overtime, fastener heads can wear out and degrade, or they can be installed slanted or with too much or too little pressure. Either way, with fasteners creating a hole in the metal, if they’re worn out or installed incorrectly, it’s an easy opening for water.
A roofing contractor will use mastic tape over the fastener or use a self-leveling material that goes over them (which is similar to caulking that oozes over the top of the fastener).
Step 4: Apply silicone coating
Spray or roll silicone coating over your metal roof and it’ll be restored.
Modified Bitumen Roofing Systems
Modified Bitumen roofing systems come in two types, smooth-surfaced and granulated. Both types are eligible to be restored with silicone coating.
However, there are some differences.
For one, the cleaning process is slower on a granulated surface than on a smooth surface. This is due to the granules’ ability to hold dirt better.
Another major difference in these systems is that a bleed blocker is normally used to prevent the black membrane “bleeding” into the new, white coating.
Built-up Roofing Systems
Here’s where it gets interesting.
Built-up Roofs (BUR for short), also come in two types, smooth and not smooth.
BUR’s have alternating layers of tar, felt, tar, felt, etc. and the only difference between the two is the top layer.
On a smooth BUR, tar is the final layer. On an unsmooth BUR, embedded rock or loose gravel is inserted into the final layer of tar, creating a “rocky” surface.
On a smooth BUR, silicone can be applied to restore the roof after cleaning.
With the embedded rocks, even if you remove and clean the roof, there’s so much embedment into the tar that it would be ½ the cost to just spray foam the roof.
If you did go the silicone restoration route, you would need double the coating to either fill all the embedment’s or to level the roof surface over the stones. Either way, restoring an un-smooth BUR is not a cost-effective option. A more cost-effective option would be a spray foam roof.
Ready to learn more about roof restoration?
At West Roofing Systems, we restore commercial roofs anywhere in the Eastern part of the US. We begin restoring these roofs by carefully examining the previous roofing system in search of saturation. We replace saturated areas with like material, clean the existing roof, and apply a level of silicone overtop that aligns with your warranty preference.
We frequently get asked if roofs can be restored or not, and it’s easy to see why. A complete roof tear-off is very expensive, so if you can avoid it, save on energy costs and get a new warranty, it’s a cost-effective solution.
We hope this article has helped you learn about the different roofing systems and which ones can and cannot be restored.
Want to learn more about silicone restoration membranes? Our free eBook below will answer all of your questions, such as:
- What is a silicone restoration membrane?
- What makes a roof eligible for restoration?
- How much does a roof restoration cost?