What’s unique about spray foam roofing?
- The application
- The ability to minimize tear-off
- High R-value and closed-cell insulation
- The slope can be customized
- There are no seams
- Ability to be renewed over and over again
It’s no secret that spray foam roofing is unique and different from any other commercial roofing system out there.
For most, this is the first time they’ve heard about spray foam being used as a roofing application.
FYI: West Roofing Systems has been installing, maintaining, and recoating spray foam roofing systems since 1979.
Let’s explore some ways spray foam differs from traditional roofing systems.
The application
Have you ever seen (or heard of) a commercial roofing system that’s installed through a spray gun?
Until I worked at West Roofing Systems…me either.
Here’s a photo of spray polyurethane foam installed on a commercial roof:
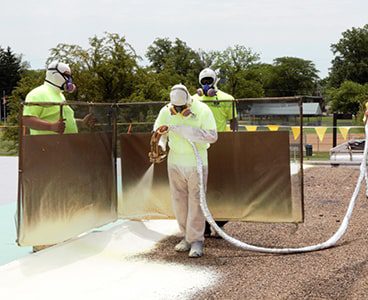
The material is a combination of two chemicals, an isocyanate and a polyol resin, which are pumped from separate containers through approximately 400 feet of heated, high-pressure hoses to an internal mixing spray gun from a truck that sits near the building.
The foam is sprayed as a liquid which increases in size by 20-30x within a manner of seconds. Once the product cures, it’s usually around 1.5 inches in height.
Traditional roofing systems are installed on a roof by attaching sheets throughout a roof. The sheets can be fastened down, welded together, or ballasted (adding rocks to weigh it down).
But when it comes to uniqueness…spray foam roofing is the only system that’s heated, mixed, and fluid-applied.
The ability to minimize tear-off
When a building owner reaches out to collect bids, there are instances when no one can do the project under budget.
Why is that so?
Is the budget too low?
Or is it very expensive to remove an entire roof, transport all the materials to a landfill, and then install a new roofing system?
One roofing system that can be installed without removing the entire roof is a spray foam roofing system.
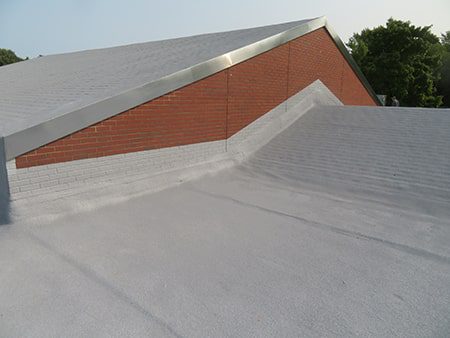
A factor that makes spray foam roofing unique is that in most cases, only the saturated (or wet) areas of the roof’s insulation need to be removed.
These areas are identified by pulling core samples, through a visual inspection, or using an infrared camera.
Once those saturated areas are removed and replaced, a spray foam roofing system can be applied over the entire roof.
Traditional roofing systems in most cases need to remove and replace 100% of an existing roof. A spray foam roofing system is usually installed by removing and replacing less than 25% of the existing roof.
By minimizing the amount of tear-off, the cost for a project is greatly reduced.
NOTE: There are some cases where you need to remove 100% of an existing roof no matter which new roofing system is installed. This could be that the roof is very old, in poor condition, or there are already two or more roofing systems installed. But the best thing to do is to call a commercial roofing contractor. They will inspect your roof and give you the most cost-effective solution to your problem.
High r-value and closed-cell insulation
Spray foam roofing is unique because it has the highest R-value per inch of thickness of any roofing insulation.
If you’re unfamiliar with R-value, it’s:
“the capacity of an insulating material to resist heat flow. The higher the R-value, the greater the insulating power.”
The more R-value that your roofing system has, the better it’ll be able to keep heat or cool inside of your building, reducing your energy costs.
Depending on the current condition of your roof, the reduction in energy bills could be enough to pay for the entire installation of the roofing system, as was the case for Texas A&M University, which recovered the cost of the installation through energy savings in 4.5 years.
Case Study: Texas A&M University
Here’s how spray foam compares to popular roofing insulations by R-value:
- Spray Polyurethane Foam: 6.5 per inch
- XPS Insulation: 5.0 per inch
- EPS Insulation: 3.85 per inch
- Polyiso: 5.5 per inch
What else is unique about spray foam roofing is its closed-cell properties. Closed-cell means that water cannot move horizontally through it.
Imagine that there’s a hole in a spray foam roof. The yellow and grey represent spray foam (yellow) and coating (grey).
If there’s a hole, water fills the hole and doesn’t move.
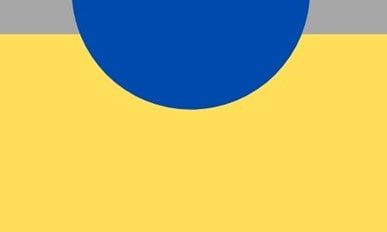
This is different from the other insulations above, which are not closed-cell.
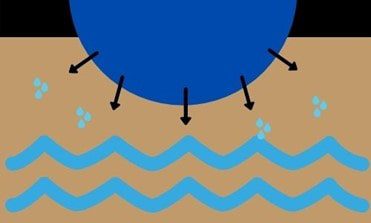
Water that enters non-closed-cell insulation, will travel to other areas.
Why does this matter?
If you get a hole on a spray foam roofing system and it rains, the water will sit in the hole and not travel. On a roof without closed-cell insulation, the water will get into the hole, travel, and saturate a large area of insulation.
Think of it as pouring water onto a paper towel. Although water is only entering at one point, eventually the entire paper towel would be soaked.
The slope can be customized
Since spray foam roofing is…sprayed on, you can spray as much or as little as needed.
This plays an important role in directing the path that water moves on your roof.
On any roof, you want water moving towards the drains. If not, water that doesn’t move off the roof, called standing water, will decrease the life of your roof.
If a roof has lower areas that hold water, spray foam can be installed to raise the slope of the area, so that in the future, water will not stay there and head towards a drain.
If this scenario happened on a traditional roofing system, a “tapered” solution would have to be installed.
“Tapering” is when the slope of a roof is created through the insulation. This is very expensive and time-consuming.
A spray foam roof is seamless
It’s beneficial to have a roof without seams because the seams are a common area where roof leaks occur.
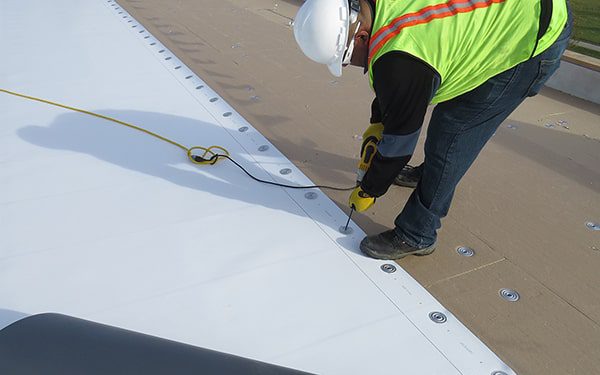
The seams can come apart for many reasons, including improper installation, wind, old age, etc.
With a spray foam roof being seamless, you eliminate one element of a roof that can leak.
Recoating and sustainability
A unique feature of a spray foam roof that gets overlooked is that it can be recoated over and over again…and therefore last a very, very long time.
Let me explain.
Let’s say you get a spray foam roof installed in 2021. Your roof came with a 10-year warranty. On the installation, you got 1.5” of foam, and the foam is protected with 20 mils of silicone coating.
In 2031, 10 years later, the 20 mils of coating may have worn down to 7-8 mils.
NOTE: Coating wears away naturally due to UV rays, wind, flying debris, foot traffic, etc.
In 2031, what’s performed is a recoat.
During the recoat process, the roof is power washed clean, any small cracks or holes (if any) are repaired, and coating is installed onto the roof.
This will bring the coating thickness back to the original 20 mils. A new 10-year warranty would be granted.
You can see that the spray foam is never touched, only the protective coating is.
A recoat can happen over and over again. Some of the roofs that West Roofing Systems installed in the 1980s are on their 3rd and 4th recoat. The foam has the same R-value now as it had upon installation.
How is this unique?
A recoat costs about ½ to 1/3 of the original installation. A traditional roofing system would need to be completely ripped off after the roof’s lifetime is over. You would then pay 100% of the original cost of the installation in today’s dollars.
Want to learn more?
Here are some of the best resources that will educate you further about spray foam:
Blog Post – How much does a spray foam roof cost?
Blog Post – What problems do spray foam roofs have?
Case Study – Metzenbaum Center. A spray foam roof installation that came in under budget and was installed in 1/3 of the time allotted.
Case Study – MTD. A 384,000 sq. ft. spray foam installation that used 3 robots to complete the project on a tight 52-day deadline.
Video – Spray Foam Installation from Start to Finish
Video – Pros and Cons of Spray Foam Roofing