A new or restored commercial roof isn’t a small purchase. The installation can be costly. Then after the installation, there are other costs that your roof plays a part in, such as:
- Energy bills each month
- Maintenance going forward
- HVAC efficiency
- What happens once the warranty expires?
And several other factors.
In this article, you’ll learn the 8 ways spray foam roofing saves you money. Here’s what’s covered:
- A spray foam roof can minimize tear-off before the installation
- Spray foam eliminates standing water more cost-effectively than other systems/techniques
- It makes maintenance easy
- It makes the roof penetrations watertight (and a part of the roofing field)
- Spray foam has the highest R-value per inch of any roofing insulation available
- The coating used to protect a foam roof from UV rays adds reflectivity
- Foam can seal HVAC ducts, increasing efficiency
- When the warranty is over, a spray foam roof can be renewed for 33%-50% of the original install price (in today’s dollars)
We’ll get into more detail on each of these points below.
But before we start, we wanted to let you know that West Roofing Systems has been installing spray foam roofing systems since 1979. If there’s anyone that knows about foam, it’s…you know 😊
This article has been approved by an internal spray foam roofing expert with over 30 years of experience.
Let’s get started!
1) A spray foam roof can minimize tear-off before the installation
In some cases, spray foam can be installed over the existing membrane. If the existing roof is:
- Fully adhered to the insulation (or deck) below
- There’s no wet insulation
- And there’s only 1 roofing system currently installed
Then it’s likely the spray foam roofing system can be installed over what’s already there. This is important cost-wise as you aren’t tearing off any of the existing roof.
- No labor costs tearing the roof off
- No transportation costs to take the material to the landfill
- No landfill costs
- No cost of purchasing new roofing materials to replace what’s been removed
- And you get to keep the existing R-value the roof already has
If the roof isn’t fully adhered, a coverboard could be mechanically fastened to make it an acceptable substrate. Then foam it.
If there’s wet insulation, identify, remove, and replace it. Then foam the roof.
And if there are 2 (or more) roofing systems already installed, perhaps 1 of them can be removed instead of both. Then properly prepare and foam it.
In each scenario, tear-off is minimized, which saves building owners money.
2) Spray foam eliminates standing water more cost-effectively than other systems/techniques
When water doesn’t run off the roof in adequate time, it can reduce the lifetime of the membrane, add unnecessary weight to the roof, and freeze in the winter.
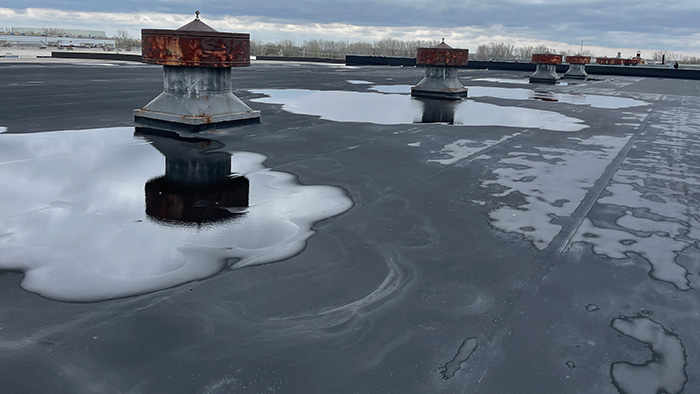
On a flat roof with a single-ply system, the slope is created with different heights of insulation board. This is called a “tapered system,” and it’s pricey to install.
You must rip out the membrane, rip out the insulation (because it’s probably sagging due to saturation), install new tapered insulation and a new membrane, and then seal it to the existing membrane.
This means if you need to raise an area, just spray more foam there. If there’s wet insulation, this would need to be removed and replaced. But the new membrane and piecing it back together with the existing membrane is eliminated.
Sometimes it’s the little details that matter. The ease of fixing standing water can save money on the overall project.
3) It makes maintenance easy
Just like your car, your roof needs routine maintenance. You wouldn’t drive 30,000 miles without an oil change, would you?
Depending on what roofing system you have, this can be easy or harder.
A metal roof requires all seams and fasteners to be checked. How long would it take to check out every seam and fastener on this roof?
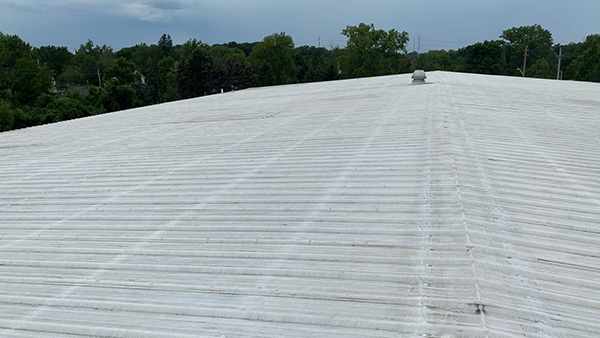
On a single-ply roof, seams run across the entire roofing system. Any uplift is an instant potential water entry point.
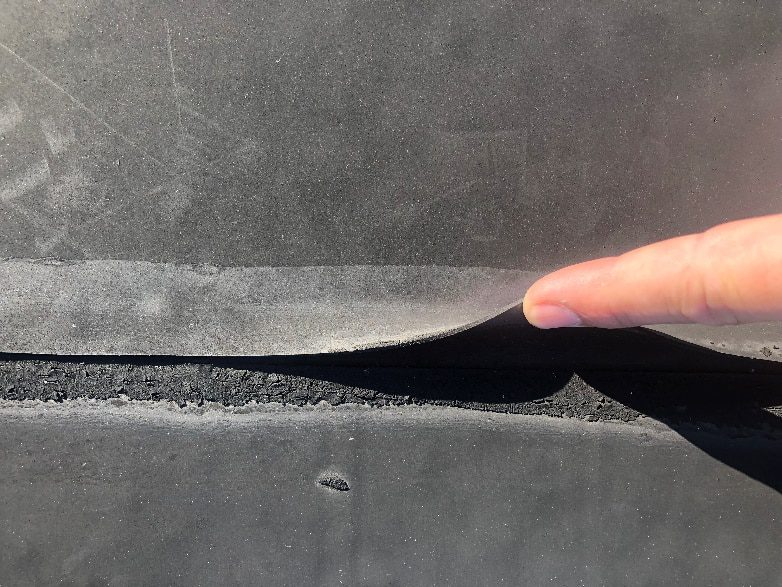
A spray foam roof is fastener-less…and seamless. The entire roof, including around/up all HVAC units, pipes, drains, etc., is one fully-adhered and monolithic layer.
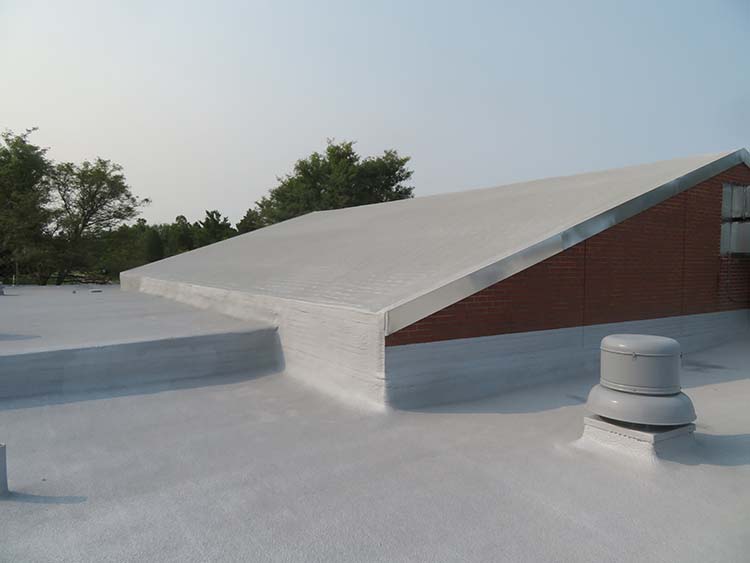
Many things happen during spray foam maintenance, but it’s much easier to spot imperfections and less time-consuming than other roofing systems.
4) It makes the roof penetrations watertight (and a part of the roofing field)
I want to make a point: any roofing system can make penetrations watertight. It’s all about the quality of the installation.
There’s a lot of custom-cutting, sealants, and termination metal used when installing a single-ply roofing system on a roof with penetrations.
Each penetration interrupts a single-ply install because it’s rolled out in sheets.
And when there are tons of penetrations, this is tough. Look at this roof:
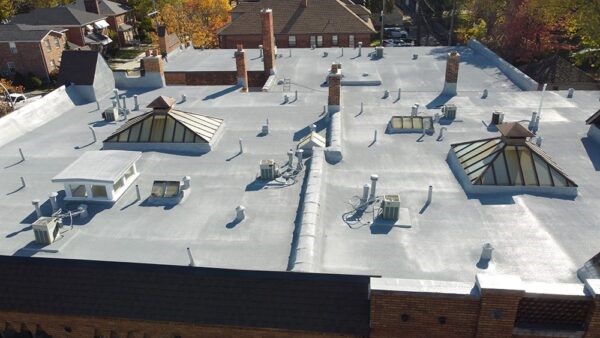
You couldn’t roof for 10 feet without something interrupting a single-ply install.
A spray foam roof is fluid-applied and self-adhering. This means it can be simply sprayed around a penetration, and the install can continue quickly.
It could take 30 minutes to install a single-ply roof around 1 penetration, whereas spray foam would take 2 minutes.
Here’s a video of spray foam being installed around a box. This simulates any penetration, whether that’s a skylight, pipe, drain, curb, or anything that comes through the roof. You’ll see the foam system makes the penetration a part of the roofing field.
Like I said before, any roofing system can make penetrations watertight. But more parts are involved, and there’s more room for installer error with non-fluid applied roofing systems.
NOTE: The reduced install time/labor cost is a money saver for building owners, but one thing that isn’t tied to a wallet is the project install time. Do you want a contractor on your premise for 1 month or 1 week? Ease of install should be of importance to building owners.
5) Spray foam has the highest R-value per inch of any roofing insulation available
Spray foam has an R-value of around 6.5 per inch of thickness. Next in line is polyiso-board, which has an R-value of 5.5 per inch of thickness (values vary based on individual product type).
Spray foam’s R-value will not reduce over time. Iso-board will lose R-value over time.
R-value is important because it’s a measurement of how much air can pass through a material. The higher the rating, the less air that can pass through.
So, in the Winter, when your HVAC unit pumps heat into your building, less will escape through the roof.
And in the Summer, when you’re pumping cool air into the building, less will leave through the roof.
Reducing the energy your HVAC unit needs to make your building comfortable will reduce energy costs. With the HVAC unit not working as much, it’ll increase its lifespan.
6) The coating used to protect a foam roof from UV rays adds reflectivity
If you aren’t aware, spray foam starts to degrade from UV rays immediately after it’s installed and must be coated within 72 hours. Therefore, on every spray foam roofing system, an elastomeric coating (usually silicone) is installed over the foam almost immediately once the foam fully cures.
Elastomeric coatings are usually installed in two coats, with the top coat being white or light grey. The light color will add reflectivity to an existing roof with a darker color.
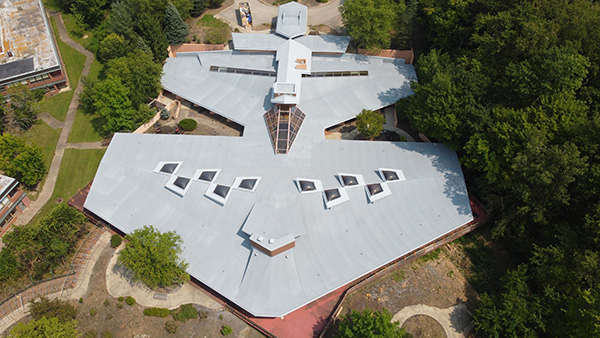
This reduces roof temperature, which reduces the air temperature that enters your building.
Cooler air that comes into your building = less HVAC usage = reduced energy bills + longer lasting HVAC unit.
7) Spray foam can seal HVAC ducts, increasing efficiency
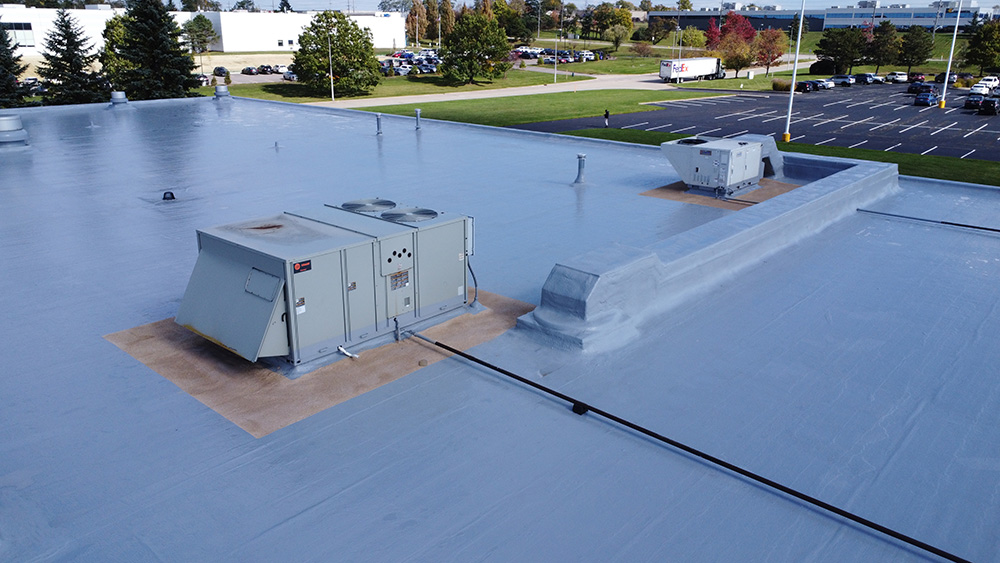
A lesser-known advantage of the spray foam roofing system is that it can encapsulate HVAC ductwork. This will help insulate the ducts, making them more efficient.
If these weren’t covered, they would be cold as ice in the Winter, reducing the hot air temperature going into the building.
This makes the HVAC unit work harder, which increases your energy bills.
8) When the warranty is over, a spray foam roof can be renewed for 33%-50% of the original install price (in today’s dollars)
Let’s say you get a spray foam roof installed today and it came with a 15-year warranty. The warranty length for a spray foam roof is always determined by the thickness of the elastomeric coating that’s installed.
On a 15-year warranty, a 25-mil thickness of coating is installed.
In year 16, coating will remain. But just because the warranty is expired, this doesn’t mean the coating is gone and the roof will begin to fail.
The amount of coating at this stage of the roof’s life will have been reduced due to weathering and wear from what was originally installed. The remaining thickness will vary depending on more/less severe weather, more/less volume of foot traffic, etc.
But 99.99999% of the time, coating will be left on that roof.
To get a new warranty, a contractor will prepare the roof and install a new thickness of elastomeric coating. If that’s another 25 mils, a new 15-year warranty is granted. No new foam needs to be installed. Foam doesn’t lose any performance measures over time.
This is called a “recoat.” And it roughly costs 1/3 to ½ of the original install in today’s dollars.
The process can be repeated over and over again. That’s why a spray foam roof can be the last roof ever installed on a building.
This saves the building owner money as they don’t have to perform any tear-off, which might happen when the warranty runs out on other roofing systems.
NOTE: Some building owners ask if the warranty is transferrable. When the next warranty ends, they’d rather be playing golf, hunting, or doing anything but building more widgets. Yes, the warranty can be transferred to another building owner.
Conclusion
Hopefully, you learned why spray foam roofs save building owners money. Want to learn more?
Here are a few posts that would be helpful:
If you want to compare the pros and cons of all commercial roofing systems, please download the free eBook below: