You know you need a new roof; it’s just a matter of which roofing system to choose.
In this article, we’ll compare spray foam roofing and TPO. Here’s what we’ll discuss:
- How much does each of them cost per square foot?
- How is the cost allocated between labor and material?
- What problems does each system have?
- Can you walk on them?
- How are they installed?
- What warranty length options do they have?
And so you’re aware, this article has been read, edited, and approved for publishing by a commercial roofing expert with more than 30 years of commercial roofing experience.
How much does Spray Foam Roofing and TPO cost per square foot?
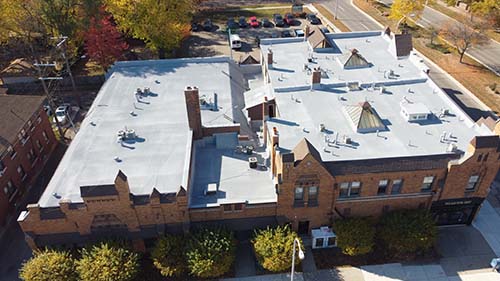
A spray foam roof costs roughly $6 – $10 per square foot. A TPO roof costs roughly $6 – $10 per square foot as well.
Many factors will make one roofing system more or less expensive than the other.
Probably the most influencing factor is the difficulty or uniqueness of the roof. Spray foam is fluid-applied, so the more complex/unique the roof is, the more cost-effective it will be versus TPO.
TPO is rolled out in sheets.
A skylight, HVAC unit, curb, drain, pipe, or anything that comes through the roof will interrupt a TPO installation. When there are many interruptions, it adds labor hours for a TPO installation.
Does the roof have vertical walls? Are there pipes along the roof deck? Is there HVAC ductwork everywhere? All of these can interrupt a TPO installation, making a spray foam roofing system more cost-effective.
Now, is the roof flat with very little penetrations? In this case, TPO may be more cost-effective.
Another factor with cost is if the roof has improper slope or ponding water issues. TPO is 100% flat. To influence the slope for a TPO system, it needs to be done with the insulation boards below the membrane. You’d have to cut out the membrane, stagger the boards appropriately, and then install a new membrane back over.
Since spray foam is fluid-applied, the slope can easily be manipulated by spraying more/less foam.
How are spray foam and TPO’s costs allocated between labor and material?
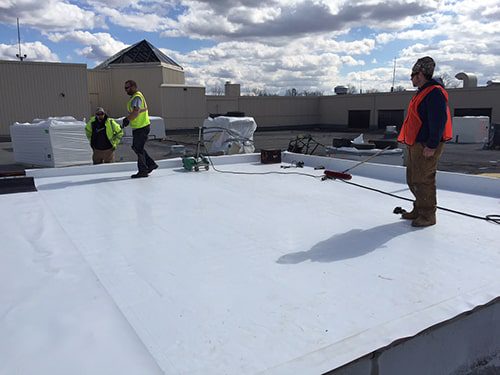
This is something that needs to get talked about.
When your roofing project is over, how much of the cost went towards labor, and how much went towards material?
And why would building owners care about this?
Well, the labor runs off your roof when the project is over. The material stays for the entire 10-20-year warranty period.
On a typical TPO installation, roughly 70% of the cost will go toward labor. It takes many guys to install TPO. And the installation can be slow, especially on a “busy” roof. The TPO itself isn’t that expensive; it just takes many hours to install it correctly.
On a typical spray foam installation, roughly 70% of the cost will go towards materials. It doesn’t take many guys to install a spray foam roof. You can’t just buy spray foam materials from Home Depot and install them. A lot of engineering goes into the “A” and “B” sides of spray foam.
What problems do spray foam and TPO roofs have?
Here are some problems with spray foam roofing:
Limited Installation Window
For spray foam materials to react correctly, it must be at least 50 degrees Fahrenheit. Depending on where you are in the U.S., that could be only 50% of the year. Other roofing systems, including TPO, can be installed in cooler weather.
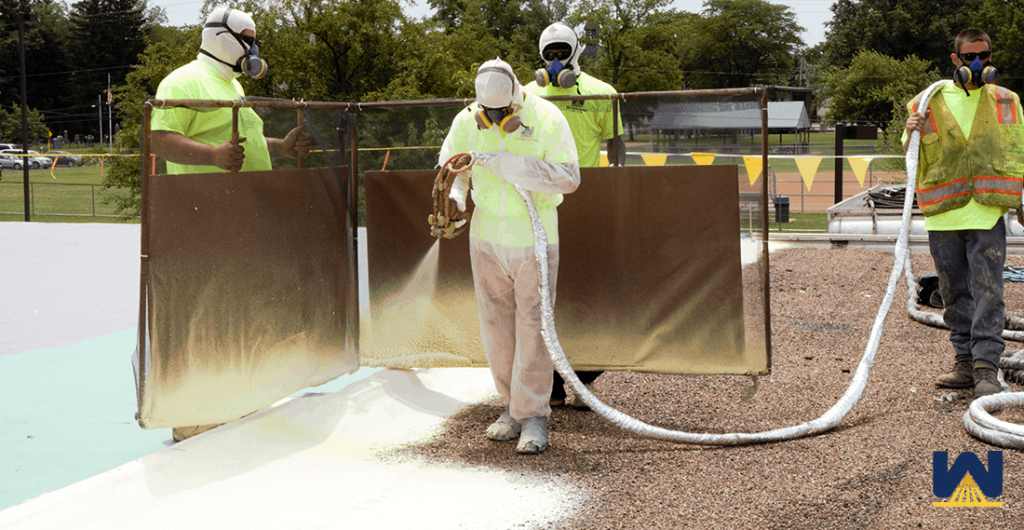
Hard to Install…Correctly
It’s easy to hook everything up and spray foam. It’s another to install it right. First, you need to be an educated roofer.
To install spray foam correctly, one must be a master of the three E’s of spray foam: electrical, environment, and exothermic energy. Here’s a brief summary of them:
- Electrical – the equipment used in mixing/heating foam.
- Environmental – the air temperature, deck temperature, sun, etc.
- Exothermic – the heat created from the chemical reaction when the A and B components meet.
There are some bad contractors out there who don’t understand the chemistry of spray foam. When they install a bad roof, the public believes it’s an unsatisfactory roofing system. It’s not; just a terrible installation.
We’ve been spraying foam for 40+ years and have kept roofs leak-free for that long.
The system works if you know how to install it correctly.
Overspray
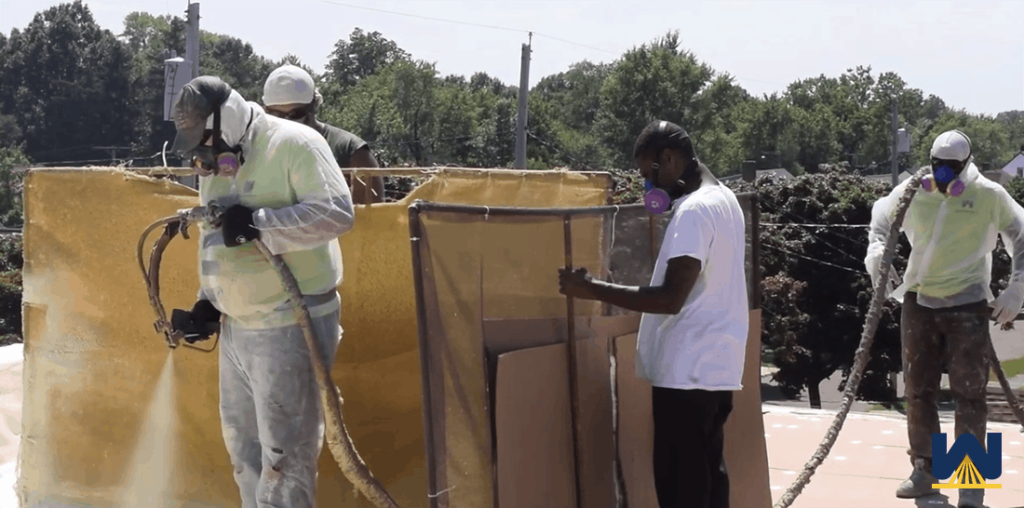
Since spray foam is fluid-applied (and very lightweight), it can be carried by the wind onto undesirable assets such as cars and windows.
Contractors minimize overspray risk by spraying out of a booth, using windscreens, or simply not spraying when it’s too windy.
Oversprayed foam can be removed from a car with a clay bar process. It will also “burn” away over time due to UV rays.
Overspray is a problem that other roofing systems don’t have to deal with.
Here are some problems with TPO roofing:
It’s a thin sheet
The first problem with TPO is that it’s a thin sheet. TPO usually comes in 45, 60, or 80 mils of thickness. A mil is 1/1000th of an inch. So, at best, TPO will be 8% of 1 inch in thickness. Being so thin makes the membrane vulnerable to punctures.
TPO is not self-adhering
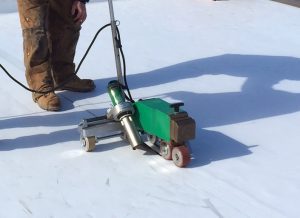
The next problem is that TPO is not self-adhering. This means something needs to secure it to the insulation and/or other sheets. There are three ways this can happen:
- Ballasted – meaning loose rock or gravel holds the sheet down
- Heat-welded – heat melts two seams together
- Mechanically-fastened – fasteners are installed in areas where two seams are overlapped
The installation can be perfect, but many errors can happen if the contractor isn’t an expert.
Expensive to create slope
Another problem with TPO is that it’s expensive to manipulate the slope. Since TPO is flat, it has no slope on its own. The slope has to be created using the insulation boards underneath.
The entire membrane would be removed prior to installing tapered insulation This gets time-consuming and expensive.
Extensive labor around penetrations
I know we’ve beat this up, but the number of penetrations and the uniqueness of a roof can really make or break a roofing system.
A TPO roof needs to be custom-cut, termination metal and adhesives must be used to correctly install it around skylights, drains, HVAC units, etc.
If a roof needs to go up and over a vertical wall, this is very difficult for a flat sheet to provide a waterproof and leak-free environment.
Look at the roof below. A roof laid out in sheets couldn’t go more than 10 feet without an interruption:
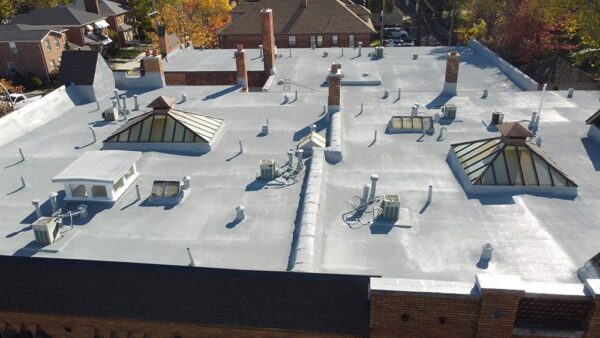
Can you walk on Spray Foam and TPO Roofing Systems?
As a building owner comparing the two systems, I would definitely ask this question. You might have multiple HVAC units that get regularly serviced. Or some other type of rooftop machinery that needs routine maintenance.
The good news is that both roofing systems are perfectly capable of handling foot traffic.
For added protection, some things can be done to handle excessive foot traffic.
Things like walkways and pads can be used on TPO. Walkways, pads, or a double broadcast of granules can be used on a spray foam roof.
How are TPO and spray foam roofs installed?
TPO roofs are installed in three different ways:
- Ballasted – meaning loose rock or gravel holds the roof assembly down
- Fully-adhered – adhesive is applied to 100% of each sheet
- Mechanically-fastened – fasteners are installed in areas where two seams are overlapped
Spray foam roofs are installed by combining two chemicals, an “A” and a “B” side, that sit in a box truck near the building. The two chemicals are heated, pressurized, and sent to a spray gun through hoses. The spray gun mixes the two chemicals at a 1:1 ratio. When the spray gun is squeezed, a liquid mist comes out. When the liquid hits the surface, it expands 30x its size within a few seconds. Spray foam has tenacious adhesion to the surface.
Once an area is foamed, it’s covered with an elastomeric coating, which can be rolled or sprayed on. Spray foam will degrade if exposed to UV rays for more than 72 hours. Once the base coat of coating has cured, a top coat is installed. Optional granules can be embedded into the top coat of coating for extra strength and to avoid a slippery surface.
I know that’s a complicated installation to write in words. Here’s a short video showing how spray foam is installed from start to finish:
What warranty length options do TPO and Spray Foam roofs have?
TPO roofs can come with 5-30-year warranties. It should be noted that the more extensive the warranty is, the better, thicker, and more expensive materials must be used. For example, on 25 and 30-year warranties, only an 80 mil thickness of TPO can be used.
An 80-mil thickness of TPO is much more expensive than a 45 or 60-mil thickness.
Other variables include:
- Types of cover boards
- Types of fasteners
- Fastening patterns
- And adhesive coverage rates
Most spray foam roofs come with a 10-20-year warranty. The thickness of the coating that goes over spray foam always determines the warranty length.
For example:
- A 10-year warranty will get a 20-mil thickness of coating
- A 15-year warranty will get a 25-mil thickness of coating
- A 20-year warranty will get a 30-mil thickness of coating
More coating is going to warrant a higher price. This is the only factor that fluctuates how costly the warranty will be.
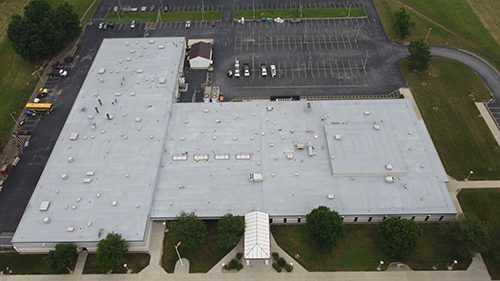
Which should I choose?
The characteristics of your roof should pull you one way or another.
Maybe you have a flat roof with little penetrations, no sloping issues, it’s in a very busy area, and you want it done in the Fall (when it’s less than 50 degrees).
In this case, you might lean towards TPO.
Maybe you have a roof with lots of penetrations and irregular shaping, ponding water, and you like the closed-cell insulation factor.
In this case, you might lean towards Spray Foam Roofing.
Either way, I would get a quote for both roofing systems. You never know what kind of solutions a contractor is going to propose.
Plus, the materials for all roofing systems increase or decrease at an alarming rate. Go the safe route, hear what contractors installing both systems say, and then compare the pros and cons based on your roof, budget, and preference.
Want to learn more? Here are some other resources you might find helpful: