So you have a roof leak and you’re weighing your options. You’ve decided to go with spray polyurethane foam because of it’s high R value and easy maintenance.
Now you’re curious as to how it gets laid down.
Here at West Roofing Systems, we’ve installed over 60 million square feet of spray polyurethane foam on commercial and industrial buildings. Because of this, we know exactly how spray foam should be laid down and how certain items fit into the process.
In this post, we’re going to tell you how cover board fits into the overall process of laying down spray foam for roofing. We’re also going to explain its purpose and why it’ll be the best fit for your roof.
Let’s jump right in…
What is a cover board?
A cover board is a thin substrate to which a roof membrane is adhered. Cover boards are made from many different materials. The type of cover board typically used for spray foam roofing is called a wood fiber board. There are many other types of acceptable cover boards but we will stick with the most common for this discussion.
A wood fiber board is made from wooden fiber and is bonded together with a resin.
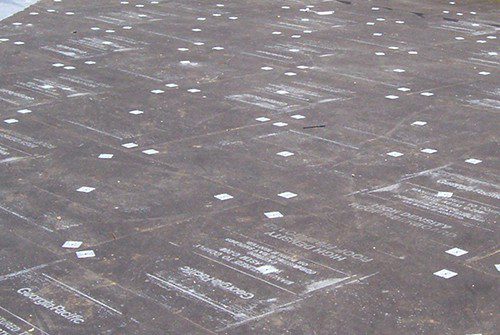
What’s the cover boards purpose in the roofing project?
The primary purpose of a cover board in a re-roofing situation is to provide a substrate that we are certain is attached to the roof deck and provides the best surface for adhesion. Some existing roof systems are not the best candidates for SPF to be sprayed directly to. The installation of the cost-effective cover board beats the cost of tearing the existing roof off every time.
On metal roofs, if you have a standard “V neck” roof panel profile, you will struggle to get spray foam into the corrugation and have it level off, so we’ll use a cover board and flute filler to provide a flat surface. Cover boards also provide a little R value to your roof, coming in around an R2.
Can spray foam be installed directly over a cover board?
Yes. It does depend on the type of board though. Different cover boards are made for different roofing applications. Wood fiber is used in many roofing solutions. Some membrane applications will adhere directly to polyisocyanurate insulation board and omit the wood fiber board and other single-ply installations require a wood fiber board.
A lot of times, a roofing contractor will mechanically attach a wood fiber board, and then they will spray foam directly to that board.
Some roofing contractors will want to spray foam directly onto an existing roof, perhaps rubber, and completely skip the cover board step.
If you choose not to use a cover board, you may have trouble with adhesion. People think spray polyurethane foam will stick to anything, and that’s not the case.
We’ve been using wood fiber board for years and it’s never been an issue. With wood fiber board only costing 35-40c/sq. ft. it’s a small price to pay for something we know works right.
Finishing touches on cover boards
The biggest argument comes from using, or not using, cover boards on a rubber roof. Some say it’s hard to get the rubber roof cleaned enough for spray foam to adhere properly.
Some manufacturers will allow a roofing contractor to spray directly onto EPDM with a primer.
It’s ultimately up to the roofing contractor’s expertise, current condition of the building, and what the building owner is expecting out if its roof.
We have a good history with cover boards, we’re comfortable with it, and at the end of the day, we’re married to this roof for at least 10 years, so we must do what we feel is right.