You may not be aware of the two newest roofing solutions available to commercial buildings: Silicone Restoration Membranes and Spray Polyurethane Foam roofs.
Which roofing option is better for your building?
The best answer will always come after a roof assessment. But other factors matter too, such as:
- Which roofing option provides a better opportunity for energy savings?
- Which roofing option provides waterproofing?
- Which roofing option is more cost-effective?
- Which roofing option is easier to maintain?
- Overall, which roofing option is better?
Let’s get started…
SRM vs SPF – Which roofing option provides a better opportunity for energy savings?
SRM
One reason building owners transition from a rubber roof (TPO or EPDM) and choose a Silicone Restoration Membrane roofing option, do so because of the gray/white color of the coating.
With rubber being dark, it absorbs the sunlight’s rays and is always so dang hot! In an SRM roofing job this year, we noticed a temperature of 192 degree (F) on rubber, and 142 degree (F) on the SRM area ten feet over.
Using white silicone coating can decrease your building’s energy use by 15 to 35%.
SPF
Spray polyurethane foam provides the greatest R value of any roofing solution. R value is the capacity of an insulating material to resist heat flow, thus keeping the cool/heat from escaping your building.
Industry standards suggests that a spray foam roof can pay for itself with energy savings in 5-7 years.
That number can go up or down depending on your current roofs condition.
EDGE = SPF
SRM vs SPF – Which roofing option provides waterproofing?
SRM
A silicone restoration membrane is spray or rolled over an existing roofing system. It’s smooth and covers all seams and holes from a previous system. Therefore, since SRMs are monolithic (just on the top layer though), they are considered waterproof.
SPF
Spray polyurethane foam is sprayed as a monolithic layer over an existing system. SPF will also, cover all seams and holes from a previous roofing system. SPF is closed-cell and therefore impenetrable by water.
EDGE = SPF
SRM vs SPF – Which roofing option is more cost-effective?
SRM
An SRM involves less materials than a SPF. An SRM is also less labor intensive. The process of how an SRM roofing system gets done is:
- Identify wet areas
- Make repairs
- Power wash entire roof
- Reinforce seams
- Lay down silicone
Overall, a ballpark price for an SRM roofing solution is $4-$7 per square foot.
SPF
A SPF involves all the steps the SRM does, except you might have to lay down cover board so the foam adheres properly. Then you need to add in the cost of the materials and processes to create and distribute the actual foam.
Overall, a ballpark price for a SPF roofing system is $5-$10 per square foot.
EDGE = SRM
SRM vs SPF – Which roofing option is easier to maintain?
SRM
Maintenance on an SRM system is quite minimal. Since the SRM is restoring and strengthening the existing membrane, you may have penetrations that vibrate and pull apart, but it’s highly unlikely.
SPF
More maintenance issues can happen on a spray foam roof, such as:
- HVAC contractors who aren’t careful (jabbing panels) can penetrate the foam
- Other workers dropping screws and stepping on them, breaking the foams membrane
- Animal damage can occur. Raccoons can dig holes, birds can peck at the foam.
Although more issues can happen on a spray foam roof, repairing these problems is very simple. It usually includes a knife, cleaning/drying, applying sealant and smoothing.
EDGE = SRM
Overall, which roofing option is better?
According to Greg “Barney” Haas, a 30+ year veteran in the roofing industry, Spray Polyurethane Foam is a better roofing option.
The #1 reason is that on an SRM, you’re relying on the underlying insulation. Also, the boards you have underneath the SRM are not monolithic, so if it’s not done correctly, you could be losing R value.
You’re getting more R value with spray foam because you have a 1.5”, pure monolithic, closed-cell and waterproof layer.
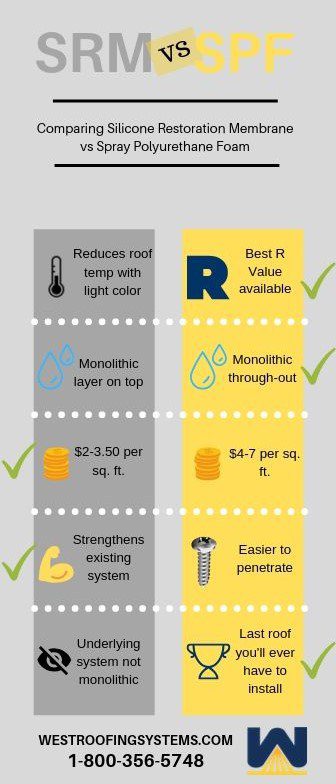