So, you’re a property owner with a roof that has gravel or stones as the most outer layer of your roofing system.
I’m assuming you have some leaks and are looking for the most cost-effective solution to get those fixed.
You may think, “I’ll just install silicone coating overtop of all these rocks and then I’ll have a seamless, watertight roofing system.”
The problem is, installing coating overtop of a gravel surface roof is not cost-effective. Even if you remove all the gravel and then install coating, it’s still not cost-effective.
In this article, we’ll explain a solution that’s about half the cost, and explain in great detail why that’s so.
West Roofing Systems has been in commercial roofing since 1979. In this time, we always give the property owner the most cost-effective solution to their roofing issues. Sometimes, it’s as simple as cleaning the roof and installing the coating. Other times, it’s cost-effective to rip everything off and install a spray foam roof.
But investing in your property is a HUGE investment. And you want to choose a roofing contractor that you can trust. That’s why we don’t just advise you on what the best solution is, we explain it in your terms so you fully understand why that solution is best for you.
Now if you got some rocks on your roof, let’s get started!
What kind of gravel-surfaced roofs are there?
Before we get into why silicone over gravel is a bad idea, we wanted to point out that we aren’t just talking about built-up roofs.
There are ballasted single-ply roofs that also have gravel and stones overtop.
Yes, silicone can be installed on any single-ply roof, but if it’s ballasted, meaning there are stones, rock, or some sort of loose gravel that’s holding the single-ply roof in place, simply installing silicone coating overtop is not a cost-effective way to stop your roof leaks.
Now let’s get into why silicone over gravel is not cost-effective.
Why is silicone coating over a gravel-surfaced roof not cost-effective?
To stop any leaks on a gravel-surfaced roof, the first step is to remove all the gravel. This is usually done using a wet-vac system, which not only removes the gravel but also cleans the existing membrane at the same time.
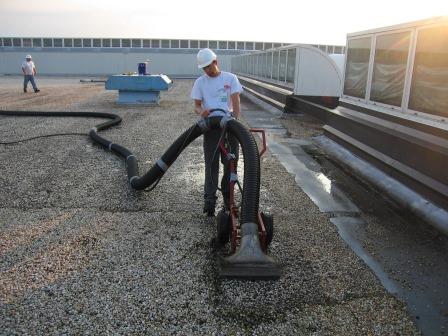
What’s left is a rocky, coarse surface.
Throughout the years, the gravel has been pushed down into the tar or single-ply roofing system by weather or foot traffic, which has created little embedment’s into that roofing system.
Ronnie Perdue, a 30+ year commercial roofing expert, says “you’ll need to install about 10 gallons per square just to seal it off.”
For easy calculation, let’s divide the above numbers in half and say that 5 gallons of coating will seal a half a square, which is 50 sq. ft.
5 gallons = 50 sq. ft.
According to Home Depot, a 4.75 gallon of Henry silicone coating is $239.
For easy calculation, let’s say that 4.75 gallons is the same as 5 gallons.
So, 50 sq. ft costs about $239 to cover with silicone.
If we multiply each of the figures above by 200, we could say:
10,000 sq. ft. would cost about $47,800 to cover in silicone.
And this cost is just for materials. It doesn’t include the expenses for removing the saturated areas of the roof, replacing those areas with dry material, seam treatment, adhesion tests, primer installation, and much more that goes into the cost of a complete silicone roof coating system.
*10,000 sq. ft. is a normal-sized commercial roof, which is the reason for the example.
**The prices for silicone can be lower by becoming a certified installer and buying in bulk, but even if the cost of the silicone is cut in half, it’s still a lot of money.
While the pricing can change for every roof, the point is, you’ll use a lot of silicone coating just to fill the embedment’s the gravel left on your roof.
Filling in all the embedded areas adds an extra (very expensive) step in the normal silicone roof coating installation process, which is shown here:
Now that we know that filling in all the embedment’s on a gravel-surfaced roof with silicone is extremely expensive, what cost-effective options do I have?
How does a gravel-surfaced roof get fixed cost-effectively?
An option that we recommend is to install a spray foam roofing system.
Once you remove the gravel and remove the wet/saturated areas, you can simply spray foam right over the top of what’s there and you’ll have a watertight roofing system.
Since spray foam is “spray-applied”, it fills in all the nooks and crannies and leaves a smooth roofing surface behind.
Here’s a video showing how a spray foam roof is installed:
A spray foam roofing system typically costs between $4 and $7 per square foot, but there are plenty of variables that increase or decrease the price, such as:
- How large is your roof?
- How many wet/saturated areas need to be removed and replaced?
- How much R-value you’re seeking?
- How long of a warranty you’re seeking?
Now that we know spray foam is a more cost-effective option than silicone, what can happen if you choose the wrong roofing contractor?
A $30,000 horror story about gravel-surfaced roofs
A property owner gave us a call because they had just gotten roofing work done by another roofing contractor.
The roof had a gravel surface and the contractor suggested spraying asphalt over the roof.
The same kind of asphalt that’s used to refinish driveways.
The problem is that asphalt has zero waterproofing capabilities. The next time it rains on that roof, water will pass through the asphalt and enter the roofing system, which is already allowing leaks.
Basically, the contractor just painted the gravel black and did not stop the roof from leaking.
The cost of the job was around $30,000. How unbelievably devastating.
That’s why it’s important to choose a roofing contractor that knows what they are doing. It’s also a good idea to get multiple quotes so you can compare what solutions are being offered.
If two companies are suggesting one way of repair, and a third company is offering something different, then it might make sense to investigate which repair options are the best.
Ask questions.
Ask contractors #1 and #2 what they think of contractor #3’s solution. And vice-versa.
This is the only way you can have some assurance that you’re choosing the best solution for your roof.
What’s a property owner’s next step with silicone coatings?
Now that you know it’s super expensive to add silicone coating onto a roof with a gravel surface, and you learned that a spray foam roof is a cost-effective solution, why not learn more about it?
Since West Roofing Systems has been installing spray foam roofs since 1979, we’ve heard all the common questions business owners ask, such as:
- What kind of warranties come with a spray foam roof?
- What R-value does spray polyurethane foam have?
If you have any other questions, please contact us and we’ll answer as best we can.