We all have businesses to run, and we want to run them with the least amount of interruptions possible.
One interruption that can happen is a roof leak.
Roof leaks are expensive to fix, can create safety hazards, can damage equipment and inventory, and many other negatives that impact business performance.
West Roofing Systems has been installing, restoring, and repairing commercial roofing systems since 1979. For most of our installations, we install spray foam, or silicone coatings, over top of an existing single-ply roof.
For more than 40 years, we’ve seen all the problems that single-ply roofing systems create.
In this article, we’ll go through them one by one, to educate yourself so you can make the best decisions going forward with your commercial roof.
Let’s get started!
If you’re short on time, here are the 5 problems with single-ply roofs that we’ll cover today:
- Single-ply roofs have seams
- Single-ply roofs have problems with penetrations
- Single-ply roofs have difficulty obtaining required R-values
- Single-ply roofs are not renewable
- The costs of a single-ply system mainly go towards labor
Problem #1 – Single-ply roofs have seams
A roofing system where the pieces are put together with seams can be a problem.
Why?
Because over time, these seams can lose adhesion, which leaves an opportunity for water to enter your insulation.
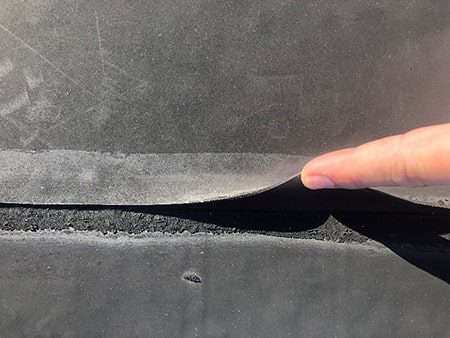
Even a little loss of adhesion is an issue. Every time there’s excessive wind, that seam rips apart wider and wider.
And even a little opening is a way for water to get into your insulation.
Most single-ply systems use Polyiso, XPS, or EPS as their choice of insulation.
The problem with these insulations is that once water enters, it gets saturated into the insulation and begins to move horizontally throughout.
Once water passes through the insulation, it enters your roof deck, and eventually, it will get inside your building.
What worries building owners the most about single-ply roofs is that a tiny loss of seam adhesion can result in water making its way into the building.
Is there a better alternative?
One alternative is to install a spray foam roof instead. Spray foam roofs have no seams, meaning there’s no possibility of water coming through an uplifted portion of the roof. Spray foam roofs are also closed-cell, which means that water cannot travel horizontally. The water will sit inside of a hole and not move.
Problem #2 – Single-ply roofs have problems with penetrations
Every roof has penetrations. The most common are:
- Skylights
- HVAC units
- Exhausts
- Pipes
- Flashings
A penetration is anything that comes through the roofing system.
Leaks are very common in these areas for single-ply roofing systems because they need to “fit” around the penetration.
A boot is used to fit around a penetration:
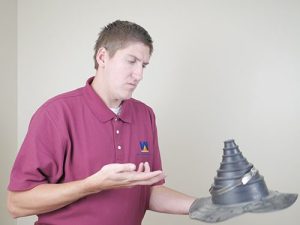
Once the boot is down, a single-ply system will need to be custom-cut to fit around the boot correctly to make sure the area is watertight.
If there are any mistakes in the installation, water will have an easy entry into your insulation.
Most roofs have multiple penetrations:
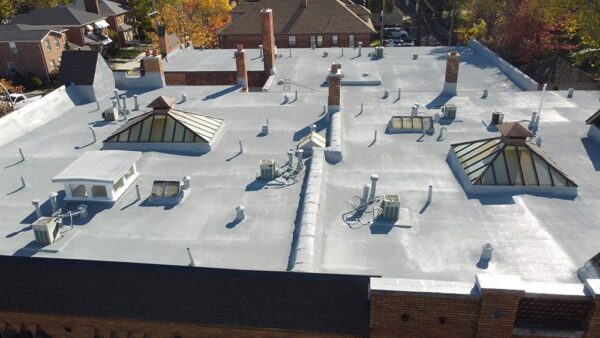
The highest number of penetrations we’ve seen on a single roof is 317!
Is there a better alternative?
Yes. There’s one roofing system out there that’s spray applied. They include the penetration as part of the overall roofing system. This means no custom cutting, no boots, and no room for error on the installation.
Here’s a video showing how that’s done:
Problem #3 – Single-ply roofs have difficulty obtaining required R-values
If you have a roof leak, the first thing that will be done is a roof inspection.
During the roof inspection, a roofing contractor will perform an infrared survey to determine how much of your insulation is saturated with water.
If less than 25% of your insulation is saturated, it’s cost-effective to replace those saturated areas. In this case, there’s no minimum R-value that your roof needs to hit.
If more than 25% of your insulation is saturated, it’s cost-effective to replace the entire roof instead of doing repairs.
In this case, you’ll have to hit a minimum R-value to comply with building codes.
In Ohio, an R-25 is required.
The two most popular forms of single-ply (EPDM and TPO) both have less than an R-1 on normal applications.
Here’s a list of popular roofing insulations and their R-values per inch of thickness:
- Spray Polyurethane Foam: 6.6 per inch of thickness
- Metal: 0.00 per inch of thickness
- TPO: 0.24 per inch of thickness
- EPDM: 0.33 per inch of thickness
- BUR Gravel: 0.34 per inch of thickness
- BUR Smooth: 0.24 per inch of thickness
- XPS Insulation: 5.0 per inch of thickness
- EPS Insulation: 3.85 per inch of thickness
- Polyiso: 5.5 per inch of thickness
Now if you need to replace your entire roof, and you choose to install a single-ply system, getting to an R-25 can be expensive.
The reason is that you’ll have to use 4-5 inches of Polyiso or XPS to get there.
4 inches x 5.5 R-value = R-22.
Also, you’ll have to install a tapered system, which means the slope is created by the thickness in insulation boards that are installed.
A tapered roofing system is expensive, which on average is $10-$15 per square foot.
Is there a better alternative?
Yes. A spray foam roof can be installed for $6-$12 per square foot. Spray foam also has the highest R-value per square inch of thickness, meaning you don’t need as much material to get the desired R-value.
Problem #4 – Single-ply roofs are not renewable
One mistake that building owners make is to ignore the life-time cost of their roofing system. Most building owners only look at what the roof installation will cost them today, and that’s final.
The average cost of a single-ply roofing system is $6-$12 per sq. ft.
The average cost of a spray foam roof is $6-$12 per sq. ft.
Just using the minimal costs for a 20,000 sq. ft. roof, a single-ply roof would cost $120,000 ($6 x 20,000), and a spray foam roof would cost $120,000 ($6 x 20,000).
However, after 10 years, your single-ply roof will need to be completely removed, costing you $120,000 again.
A spray foam roof is renewable by a process called a recoat. A recoat costs about 1/3 to ½ half of the original installation. To keep it simple, let’s use half the cost, which is $3 per sq. ft.
10 years later, your spray foam roof would cost $60,000 to install.
Is there a better alternative?
Yes. A spray foam roof costs less over the lifetime of a roofing system. Plus, the materials of a single-ply system get removed off the roof and contribute to landfills, which is bad for the environment. No material is removed from a spray foam roof.
Problem #5 – The cost of a single-ply system mainly goes towards labor
Would you rather your money for a roofing project go towards the labor, or into the materials of your roof?
My guess is the materials.
A single-ply roof needs more roofers to install than a spray foam roof, on average 6 roofers vs 10 roofers, and the projects take longer (usually 50% longer).
The materials needed for a single-ply installation are a roller and some hand tools.
Is there a better alternative?
A better investment is for your roofing budget to go into the roofing system you’re going to get, as opposed to labor. A spray foam roof requires expensive equipment, such as air compressors, heated hoses, and mixing guns to properly apply the materials that make up a spray foam roof.
Are there any problems with spray foam roofing?
Of course!
You didn’t think that spray foam was perfect, did you?
West Roofing Systems has been installing spray foam roofs since 1979, and there are some problems with the system/installation process that you should know about.
That’s why we created the article below…for you, the building owner, so you can see from the other side what kind of problems spray foam roofs have.