Quick definition: Rock Ballast means any type of stone used in a roofing system, such as river rock, slag, and pea gravel.
So, you have a leak on a roof that has rocks on top. If so, what are you supposed to do? You might think that the only solution is to remove all the rocks, remove the entire roof system, install a new roof system, and then put the rocks back on.
A more cost-effective solution would be to remove all the rock, identify and replace only the wet areas, then install a spray polyurethane foam roofing system.
Leave the rocks behind!
In this article, we’ll talk about:
- Why are rocks installed on a roof in the first place?
- What problems do rocks on the roof present
- How would a spray foam roof be installed on a roof with rocks on it?
- How is a spray foam roof cost-effective?
- Photos of spray foam over built-up roofs with rocks
And just so you’re aware, West Roofing Systems has been in commercial roofing since 1979. We specialize in spray foam roofing, which is usually a cost-effective solution no matter what type of existing roof is there.
This article has been edited and reviewed by a commercial roofing specialist with more than 30 years of experience.
Let’s get started!
Why are rocks installed on a roof in the first place?
Reason #1 – to hold the roof in place
Single-ply roofs are rolled-out sheets that need to be secured to the deck or insulation below. If not, they would blow away in the wind.
On a ballasted roof, a contractor will most likely secure the seams, seal the penetrations and the walls with an adhesive, and then everything else is loose-laid. There are no fasteners used.
Reason #2 – UV protection
UV rays can wear out rubber roofs. They can make them dry, crack, and cause a split. With the roof covered with rocks, UV rays will not damage the roof below.
Reason #3 – Added wearability
Adding a layer of rocks increases the wearability of the roof. Foot traffic and flying debris can damage a roof, but it’s very unlikely if rocks are protecting it.
What problems do rocks on the roof present?
Problem #1 – Hard to identify leaks
With rocks on top, you can’t see what’s below. Therefore, you’ll have to remove rocks and guess where a leak is. Even if you have a general idea of where the leak is from looking under the roof, it’s still a guessing game.
Problem #2 – Rocks are very heavy
With rocks being heavy, they can create stress on your building structure.
Problem #3 – Rocks can cause damage
Rocks can break down and become flat, almost like a shard of glass. These can puncture the roof.
Problem #4 – Expensive to replace
Hiring a company to wet-vac rocks off a roof is very affordable (55 cents to $1 per sq. ft.). Hiring a company to add new rocks onto a roof is expensive.
Did you know…you don’t need to install rocks on a roof to protect it from UV rays.
There’s a much simpler solution…
Introducing the spray polyurethane foam roofing system.
How would a spray foam roof be installed on a roof with rocks on it?
The first step is to remove all the rock on the roof. This is done using a company that specializes in wet vacuuming.
The next step is to identify and replace any wet insulation. This is done with infrared scans, pulling core samples, and/or a visual inspection.
Then you install a spray polyurethane foam roofing system:
To protect the spray foam roof from UV rays, a thin layer of an elastomeric coating is installed. The coating is installed in two coats, with the topcoat receiving embedded granules.
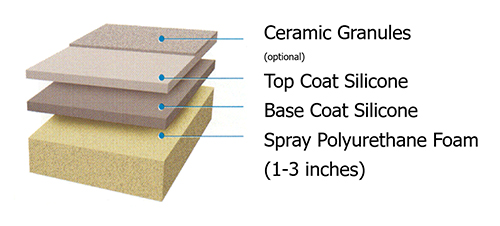
Why is a spray foam roof cost-effective for a roof with rocks on it?
Reason #1 – Spray foam customizes sloping
When rocks are removed, they will leave behind an unsmooth, unlevel, and grainy surface. This is from years of those rocks being stepped on, debris pushing the rocks down, hard rainfall, the weight of snow, etc.
You cannot put a flat membrane down and expect all the water to run off the roof. Ponding/standing water will occur, which will rapidly decline the roof’s life.
With spray foam being fluid-applied, it will fill all the nooks and crannies. It can also be applied a little more or less to customize the slope.
Why is it cost-effective?
Traditional roofing systems will need to create a slope with insulation boards. This is very expensive to do.
Reason #2 – Easy to identify repairs
When nothing is hiding the top layer of a roof, unlike roofing systems with rocks covering it, it’s easy to identify where repairs are needed.
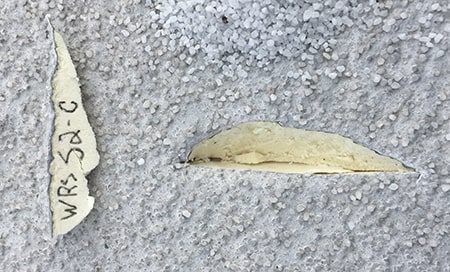
Roofs with seams and fasteners have problems with this as well. Which one of the 1000 fasteners is allowing water to come in? Which part of this seam that’s 250 feet long is allowing water to come in?
Reason #3 – Spray foam will not leak
Did you know that spray foam needs to be installed at least 1” thick for maximum performance? And did you know that 1 inch is equal to 1000 mils?
When you get a single-ply roof, most of the time you’ll get options such as 30 mils, 45 mils, or 80 mils. This is a very thin material.
But what happens when the membrane is penetrated. Flying rocks, branches, foot traffic, dropped screws or nails, hail, or any of these things can puncture a roof.
A spray foam roof has closed-cell properties. This means if there is a puncture and it rains, water will sit in that puncture and not move.
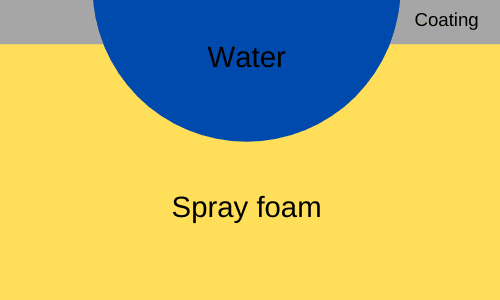
The iso board that’s installed underneath a traditional roofing system is open-cell. This means that water can travel through it and spread to other areas.
Think of a paper towel. Now think of an eyedropper dropping water into the corner of the paper towel.
Eventually, the entire paper towel will be soaked, even though there’s a very small water entry point.
The same thing can happen to traditional roofs when a fastener is loose (a very small entry point). The entire board can be soaked in one rainfall.
When the board is soaked, water will continue to travel, making its way into your building.
Other reasons related to cost-effectiveness
- A spray foam roof is fluid-applied, so it’s installed very easily and quickly around penetrations, such as HVAC units, parapet walls, drains, pipes, skylights, and anything that comes through the roof. This saves time, labor, and money.
- Spray foam has the best R-value per inch of thickness at 6.5. This reduces the heat/cool that escapes through your roof, reducing future energy costs.
- Spray foam roofs are renewable and sustainable, which makes them the best roofing system when talking about lifetime costs.
- Spray foam is the best system for a gravel built-up roof. The reason is that the foam “bites” very, very well.
Photos of spray foam over gravel built-up roofs
Gravel Built-up in Middleburg Heights, Ohio (in-progress)
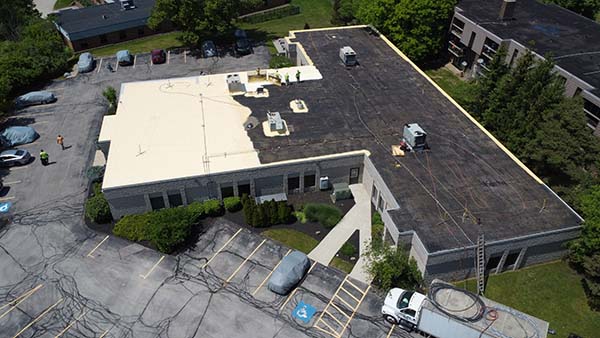
Gravel Built-up in Middleburg Heights, Ohio (finished)
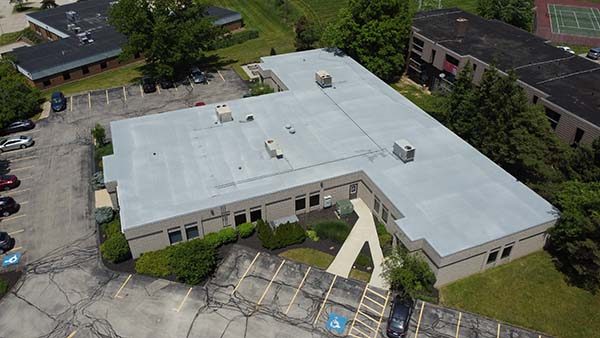
Gravel Built-up in Euclid, Ohio (finished)
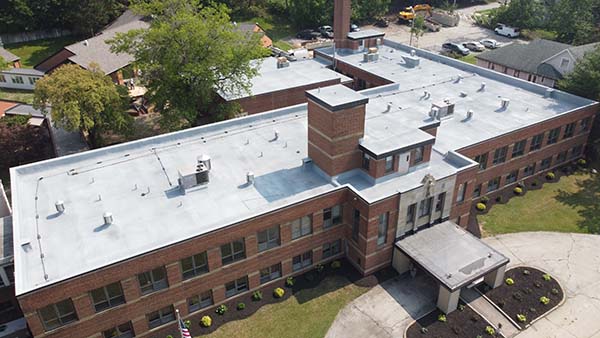
Gravel Built-up in Norwalk, Ohio (finished)
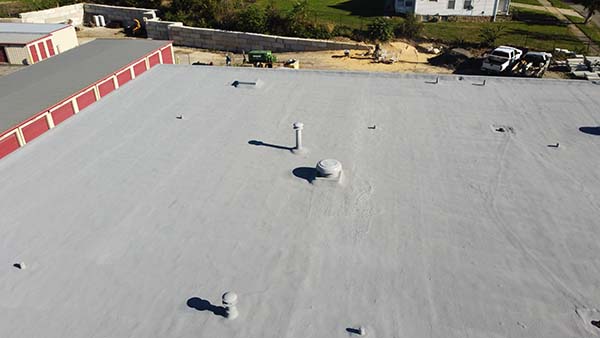