If you’re trying to fix a leaky, aging roof without spending a fortune on tear-off and replacement, you’ve likely heard about spray foam roofing.
But is it the right solution for your building?
At West Roofing Systems, we’ve applied foam to thousands of roofs and seen exactly where it shines—and where it may not be the best fit. In this article, we’ll break down who is (and isn’t) a good fit for spray foam so you can make a confident, informed decision.
Who Is a Good Fit for a Spray Foam Roof?
1. Buildings with Gravel Built-Up Roofs (BUR)
With their textured surfaces, Gravel BUR roofs are ideal candidates for SPF (Spray Polyurethane Foam) applications.
After the gravel is removed, typically via hydro-vacuuming, the existing substrate (because it’s fully adhered) is perfect for the foam to attach to, eliminating the need for a complete tear-off. This not only reduces labor and disposal costs but also minimizes business disruptions.
Here’s a video of the hydro-vacuuming process:
And here’s a video of foam being installed afterward:
Installing a coating system wouldn’t be cost-effective because it would take an incredible amount of coating to fill in all the textured areas, then install the correct amount of coating (20-30 mils) to get a warranty.
A single-ply system is also non-cost-effective.
You can’t lay single-ply over a surface with gravel (well, you can, it’s not standard practice and highly recommended).
If you remove all the rocks, the grainy surface is not ideal to install over as it’s unlevel and covered with the remaining sharp and jagged gravel.
You would need to remove all the loose gravel, then fasten a board across the entire surface before installing the single-ply system.
Case in Point: At Heskett Middle School, West Roofing Systems hydro-vacuumed loose gravel from the existing Gravel BUR and applied 1.5″ of spray foam topped with protective coatings. This approach revitalized the roof without a full replacement. The client also received a 20-year renewable, manufacturer’s warranty.
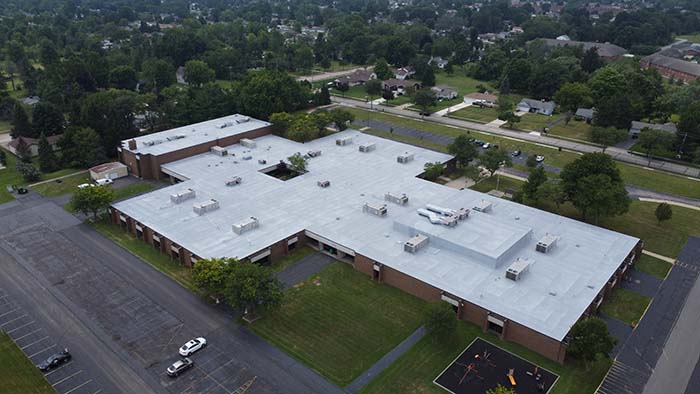
2. Facilities Requiring Enhanced Insulation (R-Value)
SPF boasts the best R-value per inch of thickness at approximately 6.5 per inch, surpassing traditional roofing insulations. This superior insulation translates to significant energy savings
Real-World Impact: Oakview Elementary is a school in Pennsylvania that runs heat and cool year-round. They chose the spray foam roofing system because it eliminated the complete tear-off and increased their R-value by 10.5.
Significant energy savings are expected.
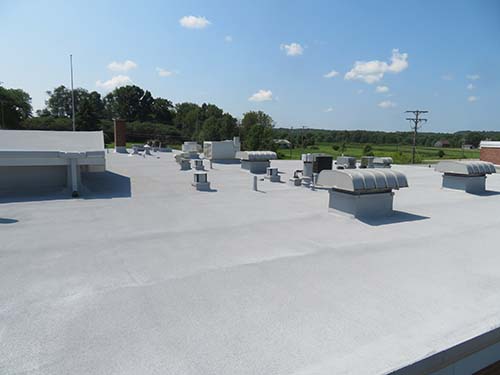
NOTE: Avoiding tear-off is super important. Not only in cost savings, but in building codes and minimum R-value requirements. Doing a tear-off qualifies a roof as “new construction” in most municipalities, and a minimum R-value must be hit. If you’re in Ohio (or anywhere in zone 5), an R-30 must be hit. That’s a lot of insulation and/or foam!
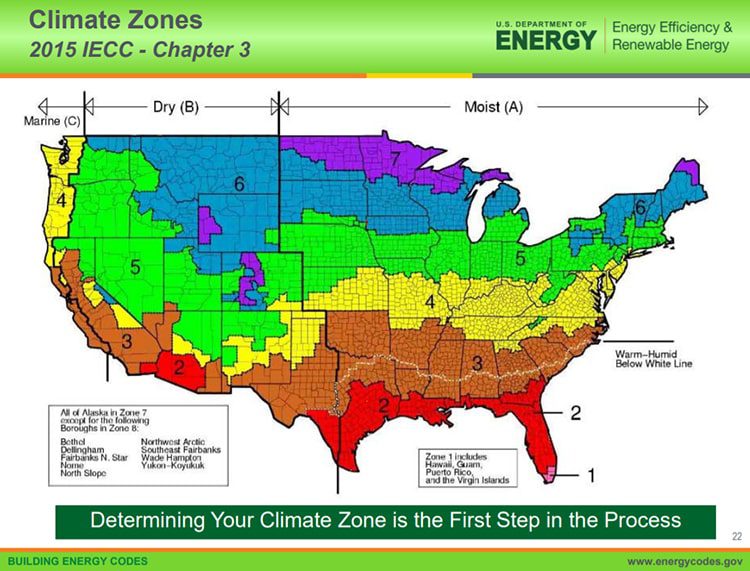
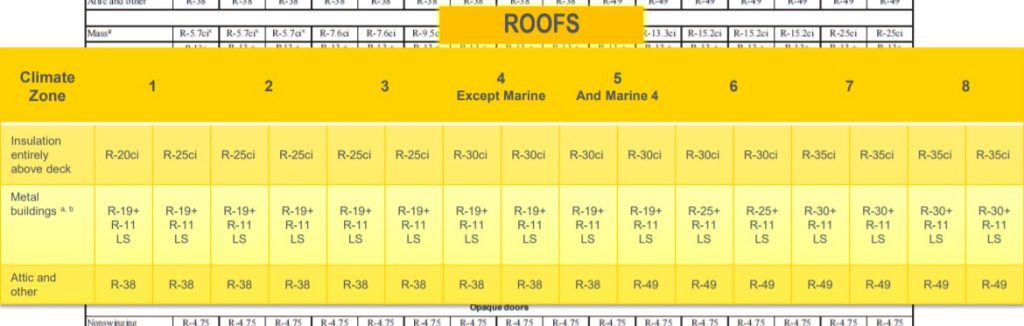
3. Roofs with Complex Layouts and Multiple Penetrations
Roofs with many penetrations—like HVAC units, skylights, and drains—are challenges for traditional roofing systems because they interrupt the installation, require custom cutting, fitting, boots, termination metals, and other items to make the penetration watertight.
SPF’s fluid-applied application ensures a watertight install without any of those items.
Example 1: The Chardon, OH building featured a uniquely complex roof. West Roofing Systems applied SPF on and around all penetrations, walls, and transitions without any interruptions or concerns with installer error.
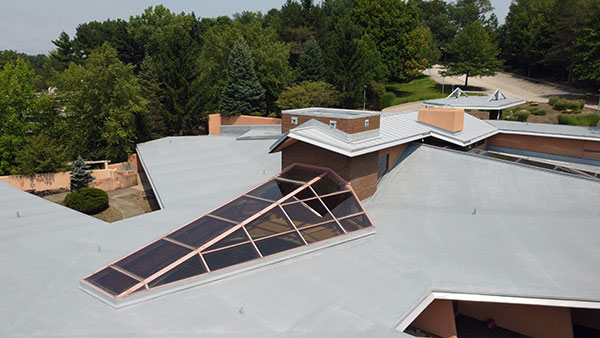
Example 2: Maryland Court is a roof with multiple levels and penetrations every 2 feet (not literally, but you know what I’m saying). A traditional roofing system installation would be interrupted nonstop, costing a fortune.
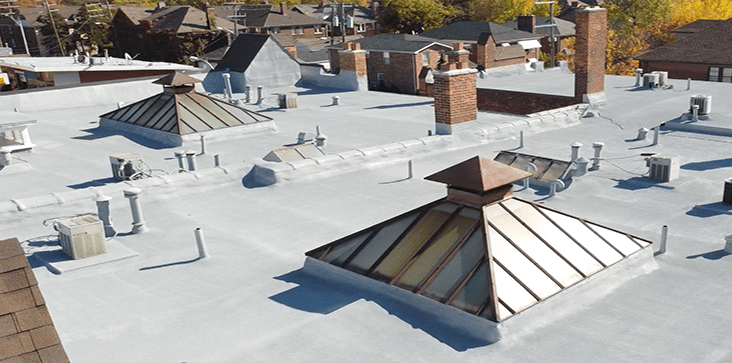
4. Metal Roofs Prone to Leaks and Fastener Issues
Case Study: At the Jabala Military Base in Iraq, aging transite roof panels with penetrations, cracks, and openings throughout compromised HVAC efficiency. Applying SPF sealed these vulnerabilities, enhancing the building’s insulation, weatherability, and comfort levels.
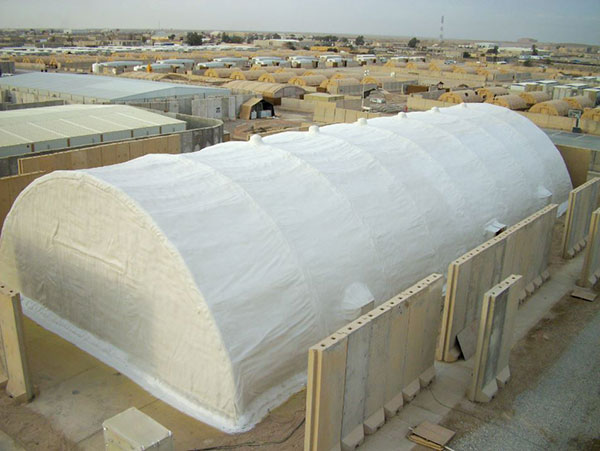
5. Roofs with Sloping Issues
Some roofs we see have a pond here, a pond there, etc. What’s happened is that the insulation below has gotten wet or damaged, making that section of the roof sag.
The “sagging” creates a little pond that doesn’t allow water to run off the roof or toward a drain as originally designed.
Since spray foam is fluid-applied, you can “spray a little more here or there” to build up areas as needed. It’s as simple as that.
NOTE: The wet insulation needs to be removed and replaced. Leaving it there and only spraying on top is an unethical roofing solution. Future problems will happen if left alone.
Building slope with a traditional roofing system is not as straightforward. The wet insulation needs to be removed, but laying down a board and matching it up level-wise with the existing dry insulation is no easy task.
Very labor-intensive and prone to error. It’s not impossible to do it this way, but spraying foam is soooooo much easier, faster, and less prone to error.
6. Any Roof with Seams
TPO, EPDM, PVC, Metal, Build-ups, and Modifieds all rely on seams for the roofing system to work correctly. When the roof temperature fluctuates (as it does daily), the roof expands and contracts, creating stress on the seams, which can lose adhesion over time.
Even a microscopic opening at the seams creates a water entry point.
Installing spray foam is perfect for these systems because it makes the roof completely seamless.
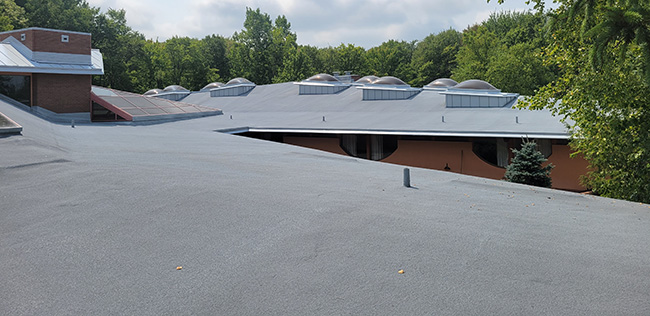
Having a seamless roof eliminates the most likely cause of a roof leak…the loss of seam adhesion.
Who Is Not a Good Fit for a Spray Foam Roof?
While spray foam roofing can be a great system, it’s not the best choice for every situation. Here are a few types of buildings or owners who might not benefit from an SPF roofing system:
1. Residential or Aesthetically-Sensitive Roofs
Let’s be honest: Spray foam is functional, not flashy.
If the roof is highly visible—like on a home or a building with rooftop patios or architectural design features—it may not be the most visually appealing option. For these cases, a more polished-looking system like shingles or a white TPO may be preferable.
2. Owners Who Are “Married” to Their Existing System
Some building owners are loyal to what they know.
If a property owner is committed to sticking with single-ply’s regardless of the project goals or challenges, SPF may never get a fair shot. In these cases, no matter how ideal SPF might be for the building, the mindset makes it a poor fit.
3. Roofs in Super Busy Areas
For the unaware, spray foam overspray is a real concern. Since SPF is fluid-applied and very lightweight, the wind can carry the foam onto undesirable assets, such as cars, people, windows, etc.
Here’s a short video of foam being sprayed. You can see how lightweight it can be:
Car dealerships are not the easiest place to apply foam 😊 .
Yes, covering a few cars is one thing. When hundreds of cars are right under a roof, it can create a challenge that other roofing systems don’t have to deal with.
Spray foam roofing companies combat this problem by not spraying on windy days or using a spray foam booth.
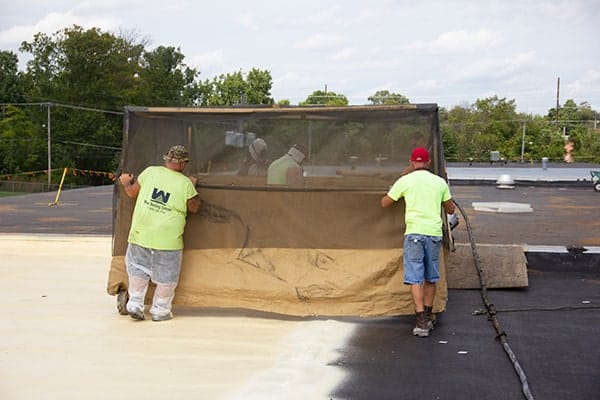
Both could lead to an extended installation.
If overspray does get on your employees’ cars, the contractor can pick up the tab on detailing. It’s a way to make things right, but it’s an extra hassle that can be avoided.
Final Thoughts
Spray foam can be an energy-efficient, low-disruption roofing option—but only if your building is the right fit. If you’re facing leaks, insulation issues, or an aging gravel BUR roof, this could be the solution you’ve been looking for.
But it’s not for every building or owner—and knowing that ahead of time saves you time and money. Still evaluating your roofing options? Let us help you compare systems and choose what’s best for your roof.