So, you have a sloped roof and you’re interested in spray foam roofing?
Congrats, you’ve come to the right spot!
Since West Roofing Systems has been installing spray foam over sloped roofs since 1979, we feel confident in answering all the top questions that building owners with a sloped roof are concerned with.
Let’s roll…
Can a sloped roof be installed with spray polyurethane foam?
Yes, you can install spray foam over a sloped roof.
Spray foam can be installed on any angle of a sloped roof, anywhere from a 1:12 to a 12:12, and right up to vertical.
If you’d like to know the slope of your roof, here’s a quick chart:

If you’d like to determine roof slope yourself, use the same formula you used in your grade school years: rise over run.
For example, a 6:12 roof “rises” 6 inches for every 12 inches of “run,”or you can measure from the roof edge to the center to determine slope. Say your roof rises 72 inches from the edge to the center, and this goes over a 144-inch area.
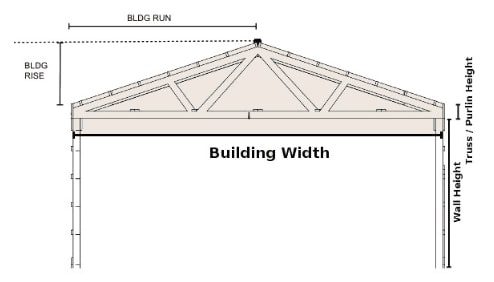
Rise = 72 in.
Run = 144 in.
Slope = 72/144 = .5 = 6:12 slope.
Here’s a roof pitch calculator where you can enter your own dimensions if you’d like to take that route.
Does spray foam for a sloped roof cost more than a flat roof?
Yes. Installing spray foam on sloped roofs costs approximately 20-30% more than a flat roof. Here are three reasons why:
1. Need for additional fall protection (lifts, restraints, etc.)
On a flat roof, a lift is not needed to access areas where a contractor needs to spray foam because they can safely walk to where they need to be.
Fall protection is always required, but additional measures are required when the slope exceeds a 4:12 slope.
On some sloped roofs, the fall protection is a lift.
A good example is a dome roof, where a lift would be a more cost-effective and efficient method of fall protection than any other.
Using a lift vs not using a lift increases the cost of a roofing project, but safety is #1 priority on every roofing job.
2. They take longer to install
Using a lift or fall restraints systems in general slows down a sprayer’s installation rate by approximately 30-40%.
Every time you move, you need to stop spraying and hit a button or relay to a team member that you need re-positioned.
Restricting movement, as opposed to walking freely on a roof, will increase the cost of a roofing project because it takes more time.
3. Overspray exposure increases the chances for delays
One of the disadvantages to the spray foam roofing system is the constant element of overspray. Overspray happens when wind picks up the foam, causing it to land on a window, car, etc.
When you’re spraying foam out of a lift, it’s just you and a lift operator. On a flat roof where it’s windy, a sprayer will have a team member besides them to hold a wind screen to prevent overspray.
When you’re in a lift, there are no team members near where you’re spraying, thus, there’s no overspray protection.
The sprayer needs to be very aware of weather conditions and perhaps slow their rate of installation because there’s no overspray protection present.
Are there any differences in preparation for a sloped spray foam roof?
Yes.
When spraying over a sloped roof, the substrate is most likely going to be shingles or metal, so the preparations used are different from those normally found on a flat roof, such as single-ply or BUR.
On a shingle roof, curled-up shingles need to be scraped off and replaced. Removing the shingles and not replacing them will cause an aesthetic issue, as you will notice the areas with no shingles.
A metal roof could be severely rusted, to the point that spot priming is needed before installing foam.
What safety concerns are present when spraying foam on a sloped roof?
Here are statistics from West Roofing System’s Director of Safety, Robert “Boz” Bosley:
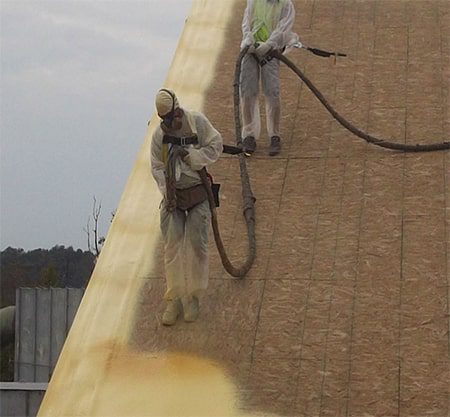
- There are no requirements where you NEED to use a man lift at a certain slope
- Anything less than a 4:12 slope, you need to use at least a warning line system
- Anything equal to, or more than a 4:12 slope, you need to use a regulatory fall protection system, such as a:
- Warning line system
- Guardrail system
- Personal fall arrest system
- Safety net system
What are some examples of a sloped roof with spray foam?
West Roofing Systems has sprayed foam over hundreds of commercial buildings with a sloped roof. One that comes to mind is Iowa Salt Domes and Utilities.
Here’s a before and after photo:
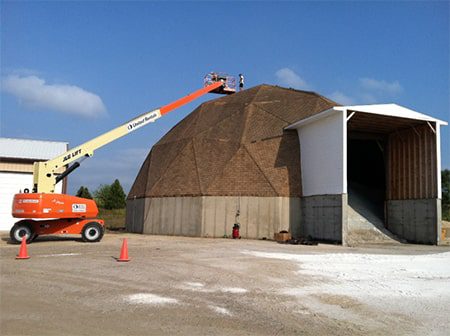
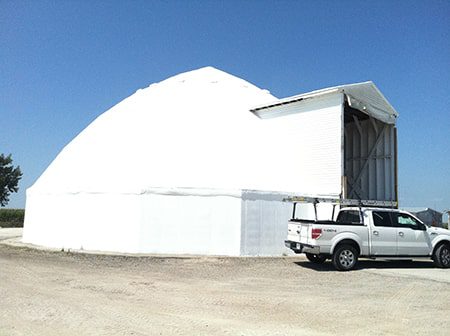
Here is another at Al-Rec LLC in Millwood, WV. This metal sloped roof had severe wind damage that was fixed with a spray foam roof.
Here are before and after photos:
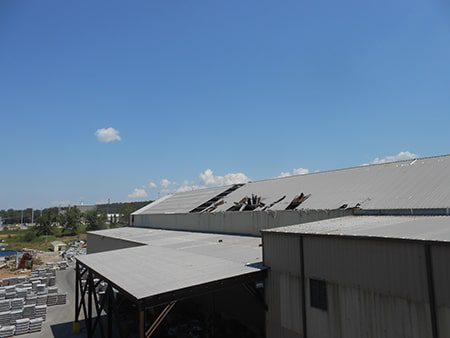
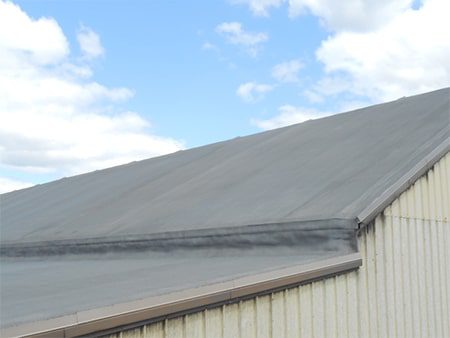
Ready to learn more about SPF for your roof?
As you’ve seen today, it’s 100% possible to spray foam on a sloped roof.
While it may be a little bit more expensive due to additional safety measures and the limitations of spraying foam while restrained or inside of a lift, any sloped roof can have spray foam installed.
At West Roofing Systems, we’ve done work on all types of sloped and flat roofs since 1979.
Here are some other questions building owners have requested answers to:
- How much does a spray foam roof cost?
- What kind of warranties does a spray foam roof get?
- How long will a spray foam roof last?