Summary: The ballpark cost to restore a commercial gravel built-up roof is $6.50 – $10 per square foot. Many factors affect cost, such as how much gravel needs removed, how much wet insulation is present, and what warranty length the building owner desires.
So, you have a commercial building with a gravel-built-up roof.
It’s leaking, super old, or on the verge of failing, and you don’t know what to do.
One suggestion is to look into spray foam roofing.
A spray foam roofing contractor will:
- wet-vacuum the loose gravel off the roof (which also cleans the substrate)
- identify, remove, and replace wet insulation
- apply spray foam over the existing substrate
- install coating to achieve the desired warranty length
- install granules into the top coat of the coating
- do a final inspection and grant the 10-20-year warranty
The cost for spray foam roofing on a gravel BUR is roughly $6.50 – $10 per square foot.
In this article, we’ll quickly go through the factors that can increase or decrease the project’s cost.
And just so you’re aware, West Roofing Systems has been in spray foam roofing since 1979. Every year we install foam over hundreds of thousands of square feet of existing Gravel BURs.
Let’s get started!
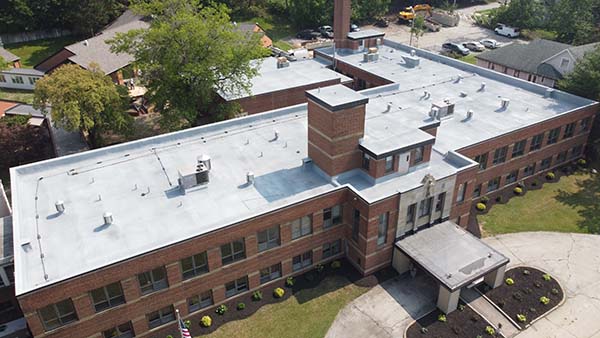
Here are the cost factors we’ll explain in this article:
- How much loose gravel needs to be removed?
- How much wet insulation is present?
- How much spray foam is required (or desired for R-value purposes?)
- How long of a warranty would the building owner like?
- How far away the roof is from the contractor
How much loose gravel needs to be removed?
Some roofs have more loose gravel on them than others, but at the end of the day, it all has to come off to reveal a clean surface.
A wet-vac company will basically vacuum the loose rocks right off the roof. The gravel goes through a pipe to a work truck that needs to be dumped when it reaches capacity.
The more trips to dump, the more gas that’s used, the longer it’ll take, and the more pricier a project will be.
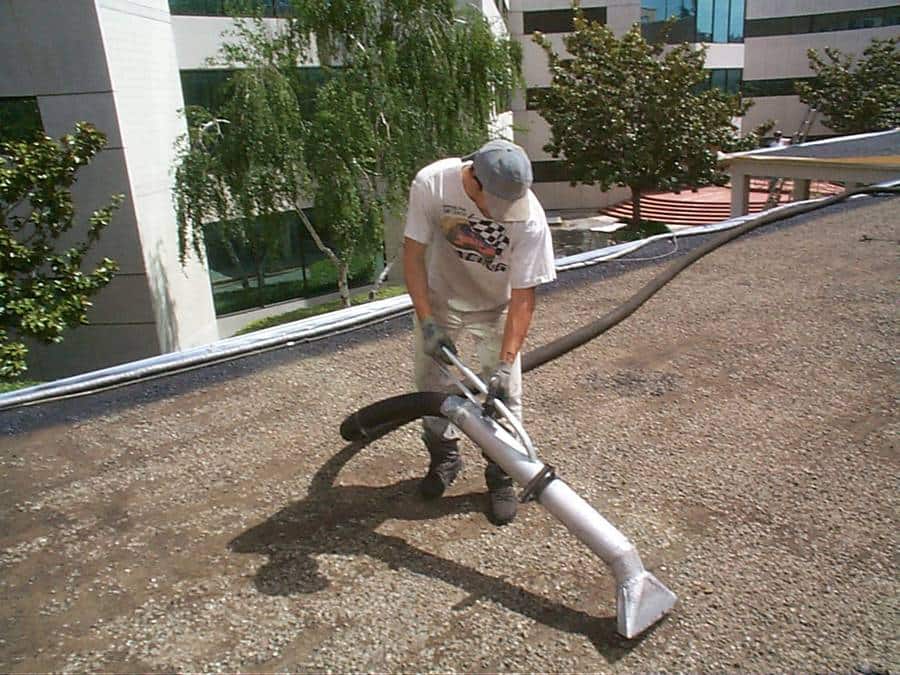
How much wet insulation is present?
No roofing system (including spray foam) should be installed over wet insulation. Doing so will only cause future problems, such as:
- The existing water can freeze and expand, damaging the insulation/roofing material
- Frozen water can thaw in the Spring and enter the building
- The water can evaporate and cause blisters in a new membrane
- The water can reduce the R-value of the insulation
- The trapped water can saturate the insulation and affect the roofs slope
And probably 20 more things (all bad) that can happen.
All wet insulation must be identified, removed, transported to a landfill, and replaced with similar material.
A 100,000 sq. ft. roof with no wet insulation will cost way less than the same roof with 20% wet insulation.
How much spray foam is required (or desired for R-value purposes?)
Spray foam must be installed at a minimum of 1” thick so that the product cures, performs to its max, and creates the desired physical properties. The usual application is 2-3” around penetrations, and 1-2” around the perimeter. The foam is tapered around drains to promote proper slope.
However, some building owners want to increase their R-value.
Spray foam’s R-value is 6.5 per inch of thickness.
More R-value = more product to install = more cost.
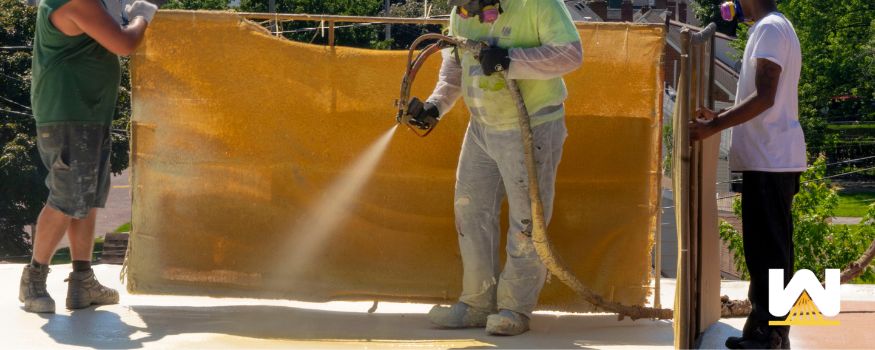
How long of a warranty would the building owner like?
An elastomeric coating is always installed over spray foam to protect it from UV rays. The coating also provides additional waterproofing.
The thickness of the coating is what determines the warranty.
Usually:
- For a 10-year warranty, 20 mils of coating is installed
- For a 15-year warranty, 25 mils of coating is installed
- For a 20-year warranty, 30 mils of coating is installed
Obviously, the longer the warranty, the more product that’s used, the more the project will cost.
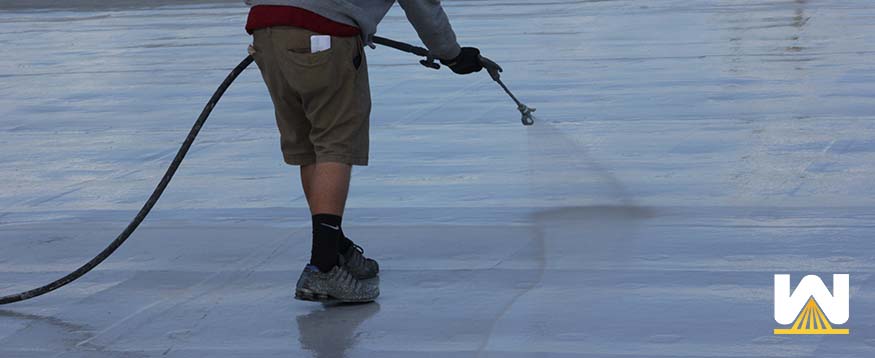
How far away the roof is from the contractor
We’d all like to have a commercial roofing contractor right next to us, right?
Likely, that’s not the case.
Gas, hotel stays, and flights can all add to a project’s cost.
Wait…why would a contractor fly or need hotels to perform a project?
It’s all about the trust and quality of work.
We are in Ohio, Georgia, and Florida, but we constantly are doing work in other states. This is because spray foam can be difficult to install correctly, not many do it, and the product has so many benefits over traditional roofing systems that it’s worth it.
And we’ve been around since 1979.
You don’t want to hire someone who has minimal longevity. Who knows if they’ll be a company for the length of the warranty.
One of the biggest mistakes building owners make is choosing a roofing contractor solely on cost.
The quality of the install probably isn’t going to be there. They might use inferior materials. Have little experience doing your specific project, such as working on Gravel Built-Up roofs, etc.
Conclusion
Here’s some other content you may be interested in: