The cheapest commercial roofing system is a spray foam roof. It’s the cheapest when you consider everything involved with the total cost:
- The cost of the installation (process + labor + materials)
- R-value and future energy savings
- Roof renewability
- Ease of repairs and maintenance
We’ll get into each of these in more detail below.
And just so you’re aware, West Roofing Systems has been in commercial roofing since 1979. We specialize in spray foam roofing and are constantly battling other traditional roofing systems when it comes to cost.
Some building owners only look at the cost of the installation. While others would look at the costs of everything involved over the roof’s lifetime.
Every article written at West Roofing Systems has been reviewed and edited before publishing by a commercial roofing specialist with more than 30 years in the industry.
Let’s get started!
The cost of the installation (process + labor + materials)
If this was 2 years ago, we could say that spray foam and single-ply are roughly the same cost (around $4 – $7 per square foot).
Today, they are both in the realm of $5 – $10 per square foot.*
*NOTE: This is a general range. A high-rise that wants an R-40, a 25-year-warranty, half the roof is wet, and it’s located 500 miles away; this roof could be $20 per square foot. Every roofing situation is different.
However, there are scenarios when either could be cheaper:
- Since single-ply roofs are rolled-out sheets, they can be installed quickly on a flat roof with minimal interruptions, such as HVAC units, pipes, drains, etc.
- If there are a lot of interruptions (also called penetrations), a spray foam roof can be installed a lot quicker because it’s fluid-applied/sprayed out of a gun.
Metal roofing has always been more expensive than spray foam or single-ply.
Some tips for gauging the cost of installation:
– Is the whole roof going to be torn off or just the areas with wet insulation and/or damaged membrane? This will fluctuate the cost a ton!
– How long of a warranty are you seeking? There’s a big difference in cost for a 10-year warranty versus a 15 or 20-year warranty. Single-ply’s will use a thicker membrane (more expensive) and a spray foam roof will use a thicker application of protective coating (also more expensive).
– What R-value are you seeking? More (or thicker) polyiso boards will be installed for a single-ply roof. And a thicker application of spray foam will be installed on foam roofs. More product, more R-value, more cost.
Long story short…
Spray foam and single-ply roofs are about the same cost. Metal roofs are a little more expensive. Hundreds of variables can influence the cost of any roofing project.
R-value and future energy savings
When you’re thinking about the cheapest commercial roofing system, you need to consider R-value and future energy savings.
Why?
What if two roofing systems cost the same to install, yet one saves you 15% on your energy bills every month for 20 years?
Would you then consider both roofing systems to cost the same?
This is all about how R-value is created.
Metal roofs generally don’t have much R-value. There is no insulation board or anything along those lines on most metal roofs.
Single-ply roofs use polyiso board (or a similar type of board) to create R-value. At best, polyiso board comes with an R-value of 5.5 per inch of thickness. Polyiso board loses R-value over time. It also loses a significant amount of R-value if it ever becomes wet.
A spray foam roof is four parts: spray foam (which goes over an existing roof), a base coat of coating, a top coat of coating, and granules.
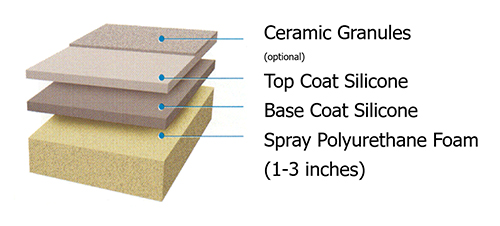
The spray foam part is where the R-value is created. Spray foam has an R-value of 6.5 per inch of thickness.
Single-ply’s can get the same R-value as a spray foam roof, but a thicker product needs to be installed.
Another small tidbit about R-value is thermal bridging. This is where heat/cool escapes through the fasteners that go through the membrane and iso board.
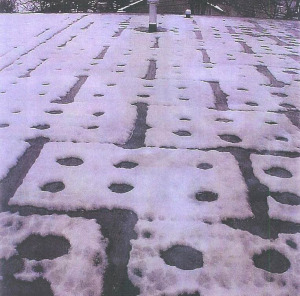
A spray foam roof is self-flashing, so no fasteners are needed. A foam roof is also seamless, so obviously there are no seams ?.
Long story short…
Metal roofs don’t have insulation. Single-ply roofs don’t create R-value as efficiently as spray foam. Single-ply roofs lose R-value performance over time when it’s wet and because of thermal bridging.
Roof renewability
A question to consider is, “what happens to the roof once the warranty ends?”
On metal and single-ply roofs, the answer is usually “it gets torn off and replaced”.
A spray foam roof can be renewed for 1/3 to 1/2 of the original installation.
How does this work?
Say you get a spray foam roof with a 20-year warranty. A 20-year warranty means that 30 mils of coating will be installed to protect the foam roof from UV rays.
In year 20, those 30 mils may have worn down to 7-8 mils. (They will no doubt last way past the length of the warranty.)
In year 20, a contractor will clean the roof and install 30 new mils of coating. A new 20-year warranty is granted. The foam doesn’t lose any performance or R-value over time. The “renewal” can happen over and over again.
Long story short…
Once the warranty ends on a single-ply or metal roof, they will usually be 100% ripped off, costing 100% of the initial installation. A spray foam roof can be renewed for 1/3 to ½ of the original cost of installation.
Ease of repairs and maintenance
Every roofing system needs routine maintenance. Every roofing system will endure damage from foot traffic, flying debris, dropped tools, hail, and hundreds of other events.
The easier it is to repair and maintain a roof, the quicker (and cheaper) the job gets done.
I want to explain open-cell vs closed-cell insulation.
Open-cell insulation
Polyiso board, or any other type of board for insulation, these have open-cell properties. This means water can travel through them. This is not good as water can saturate other boards or allow water to enter your building.
When a roofing membrane is 30-90 mils in thickness (A mil is 1/1000th of an inch), it doesn’t take much to get through them.
When water gets through a small cut in the membrane, it’ll saturate the insulation below and eventually make its way into the building.
Closed-cell insulation
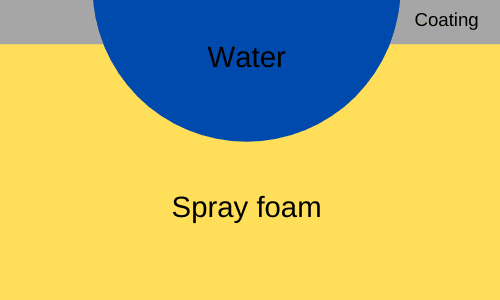
The picture above shows what happens if a spray foam roof gets punctured. Water will sit in the hole and not travel. The repair is simple.
A service technician will dry the area with a towel, then cut around the wet foam, insert caulk or coating, and smooth the area out.
Done deal.
If the same damage happened to open-cell insulation, a large area could be wet. A technician will have to remove the membrane, remove the insulation board, investigate if any surrounding boards/membranes are wet, and then replace all the materials.
Long story short…
How easily a roof can be repaired and maintained should determine the cheapest overall roofing system.
Conclusion
Hopefully, you learned that when you receive your quotes for a new roof, there’s much more involved than the price you see today.
How much are repairs going to cost over the lifetime of the roof? And how much damage is created when hail, flying objects, or dropped tools happen?
Is there going to be any energy savings with the new roof?
Once the warranty ends with “this” roof, what are the costs going forward? Roof renewability should factor into the costs of your roof today.
And what about the cost of the installation? Costs for materials and labor have changed dramatically since 2021 on all roofing systems.
The best thing a building owner should do is get a quote for a spray foam roof, a single-ply roof (TPO is the most popular), and a metal roof.
Weigh the pros and cons of each roofing system and choose a contractor you can trust.