The best way to restore an old TPO roof is by installing an elastomeric coating over it. If the roof is in bad shape (seams apart, is super old, lots of wet insulation, or no routine maintenance), then it won’t be eligible for a coating system.
If your TPO roof is in bad shape, it’s best to only remove the damaged/wet areas and install a spray foam roof over it.
What’s the best way to restore a TPO roof in good shape?
The best way to restore an old TPO roof is to install a roof coating system. Roof coatings are “elastomeric”, meaning they can stretch and contract without losing performance.
There are three main types of elastomeric coatings:
- Urethane
- Silicone
- Acrylic
They each have their own pros and cons, but at West Roofing Systems, we almost exclusively use silicone. Silicones are the best bang for the buck in terms of performance and price. And since we’re headquartered in Ohio, where there are hot summers and cold winters, we feel silicone handles the large swings in temperatures very well.
Here are some photos of a roof coating system over an existing TPO roof
TPO roof that needs to be restored
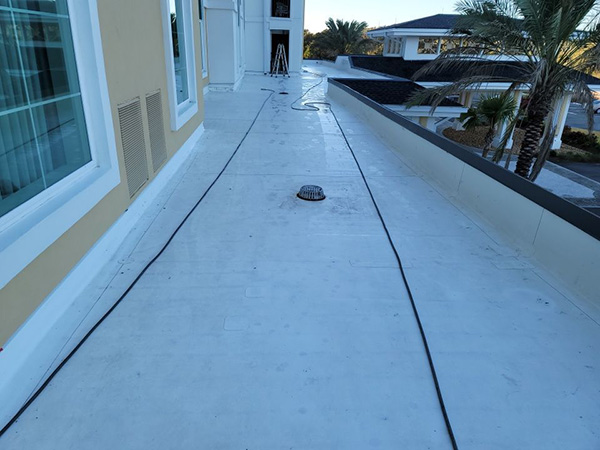
TPO roof with seams reinforced w/mesh and coating
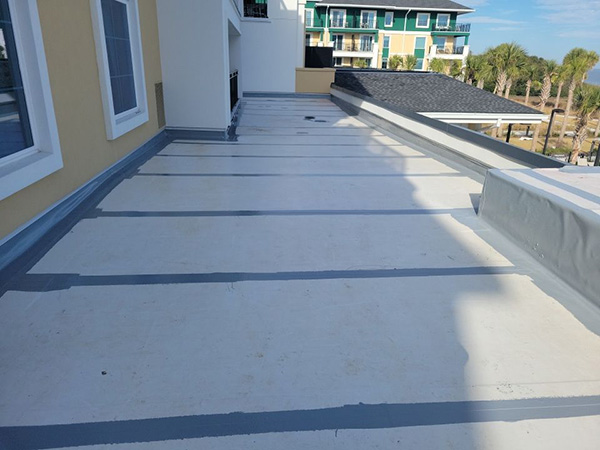
Finished TPO roof with silicone roof coatings
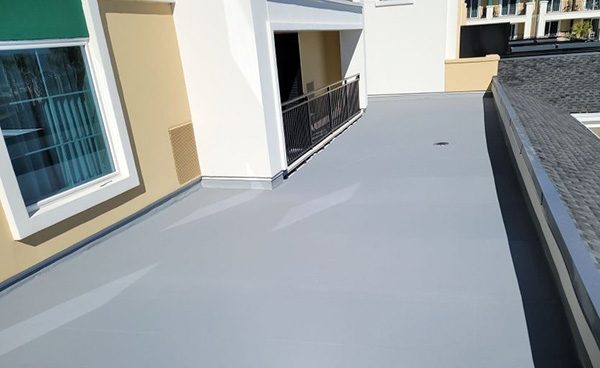
However, there is a HUGE problem with roof coating systems…eligibility. The existing TPO roof needs to:
- Have seams that still have good adhesion
- The total roof’s insulation cannot be more than 25% wet
- There had to be annual routine maintenance
If any of these are not true, a roof coating system will not be an option. Yes, you can still install one, but a manufacturer (or roofing contractor) will never grant you a warranty.
If your roof is in bad shape, then what’s the best way to restore an old TPO roof?
What’s the best way to restore a TPO roof in bad shape?
A spray foam roofing system is your best option here. There are many reasons, such as:
- You can minimize tear-off. Tear-off greatly contributes to the overall project cost. You must remove the wet insulation, drive it to a dumpster, pay the landfill fees, buy new products, and install it. It’s very labor-intensive, which means it’s costly. You can leave behind the areas with dry insulation and spray foam over it. Other roofing systems, you’ll need to remove 100% of the roof and replace it.
- Spray foam is fluid-applied, which is very easy to install (even on roofs with many penetrations). This reduces labor hours, which reduces cost. Here’s a start-to-finish video of spray foam being installed:
- Spray foam has an R-value of 6.5 per inch of thickness, likely reducing your energy bills going forward.
- Spray foam is protected by an elastomeric coating (yup, the same coating that’s used in a roof coating system), which wears away over time and can be recoated. This is how spray foam is a renewable roofing system.
Spray foam minimizes tear-off, it’s easy to install, reduces energy costs, and is renewable.
How would spray foam go over an existing TPO roof in bad shape?
Step 1: In some cases, you will need to remove all of the TPO.
Step 2: Remove and replace any wet insulation.
Step 3: Install ½ inch high-density fiberboard over the entire roof (this will give foam the best possible adhesion)
Step 4: Apply spray foam at least 1.5 inches thick. The thickness can be adjusted for a desired R-value, drainage, to avoid ponding water, or to complete a feathered edge.
Step 5: Apply the base coat of the coating and let it cure
Step 6: Apply a top coat of coating
Step 7: Install granules into the top coat of the coating and let it cure
Here are some photos of spray foam over an existing TPO roof
TPO roof that needs to be restored
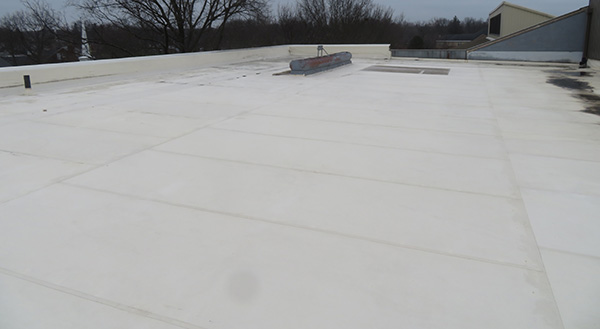
Fiberboard installed over the existing TPO roof
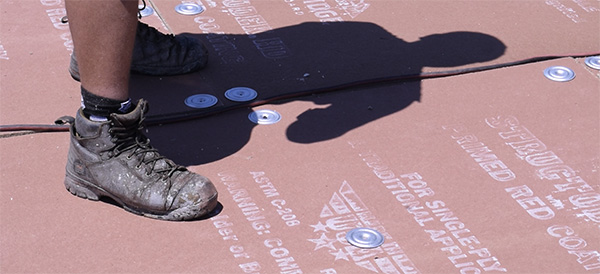
Spray foam installed over coverboard

Finished spray foam, coating, and granules over an existing TPO roof
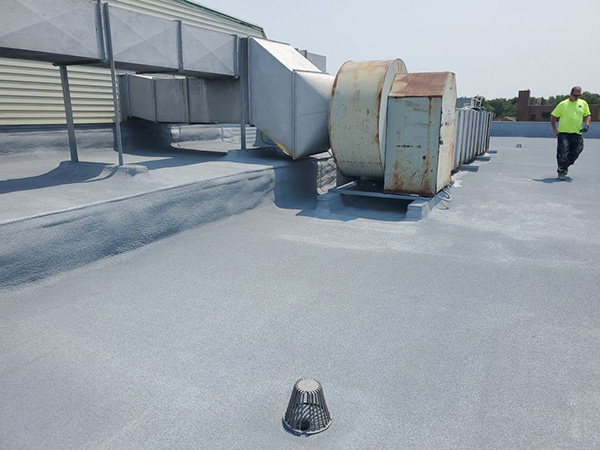
Conclusion
If you have a TPO roof and you’re unsure what to do, please contact us. Perhaps your TPO roof is still in good condition, and you can install a roof coating system. Or maybe it’s in really good condition, and you don’t have to do anything for a few years.
But the only way to find out is to have a professional take a look at your roof.
One of the worst financial decisions building owners make is to ignore their roof until it begins leaking. I understand, it’s “out of sight, out of mind”. But when your roof cannot be coated, you’ve missed out on a very cost-effective solution.