Let’s say that you’re a building owner. Your building is leaking here and there, and you’ve paid good money to get those leaks fixed.
But you’re sick of paying for repairs.
It’s time to get a new roofing system that’s known to stop leaks.
You’ve read that a spray foam roof is a watertight roofing system because they are seamless.
But what happens if someone installs the spray foam roof wrong?
It would be devastating to invest thousands of dollars into a new roofing system, and it doesn’t perform right, starts leaking, and overlooks are not pleasing.
Spray foam isn’t like other roofing systems where you see the finished product before it gets installed. For example, if you’re getting a rubber roof, you can see the rubber sheets before they get installed.
Spray foam comes in 55-gallon drums and is spray-applied, so you don’t see the finished product until it’s installed on your roof.
Building owners may be skeptical and have questions, such as:
- How do I know if the contractor installed the spray foam roof the right way?
- What happens if there are errors in the application?
- Will a warranty cover the repairs if needed?
Since we’ve been installing spray foam roofs since 1979, and unfortunately, have come across roofs where spray foam was incorrectly applied. We know the headaches it causes when your project is done incorrectly, so hopefully, this article helps you avoid that.
After this article, you’ll be able to:
- Understand what a good spray foam roof looks like
- Know what a bad spray foam roof looks like
- How to avoid having a bad installation by choosing a good spray foam roofing contractor
Let’s get started.
What does a good spray foam roof look like?
Here are a few examples are what a good spray foam roof looks like:
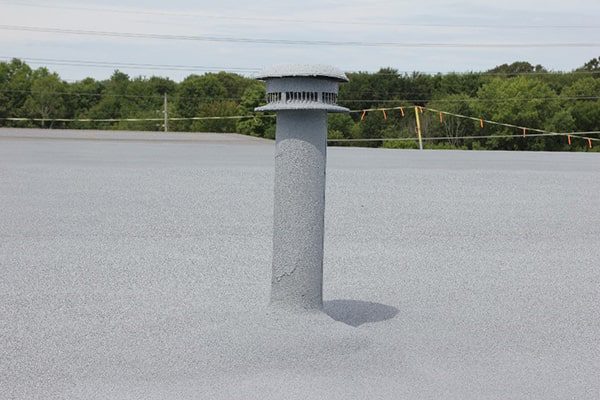
You can see in the picture above that the spray foam roof looks smooth and that it fully encapsulates the pipe into the overall layer of the roofing system.
There are no seams in spray foam roofs, which is an area where most roofing leaks begin.
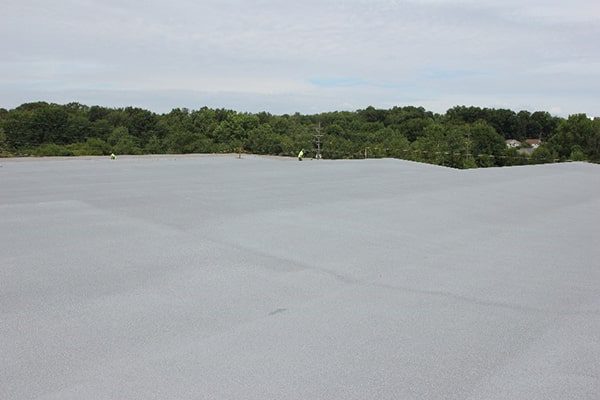
You can see in this photo that there are no blisters, no weird discolorations, and no areas in which coating wasn’t protecting the roof.
NOTE: Coating is usually gray. Most don’t know this, but the actual color of spray polyurethane foam is yellow.
If you see a spray foam roof and there are yellow areas exposed, that’s the sign of a bad spray foam installation.
Spray foam that’s exposed to ultraviolet rays/sun will deteriorate the undying foam and eventually become an issue.
What does a bad spray foam roof look like?
The only way to spot a bad spray foam roof is unfortunately after the roof is already sprayed.
Here’s a photo of a spray foam roof that probably looked perfect when the job was completed, however, this is what it looks like now:
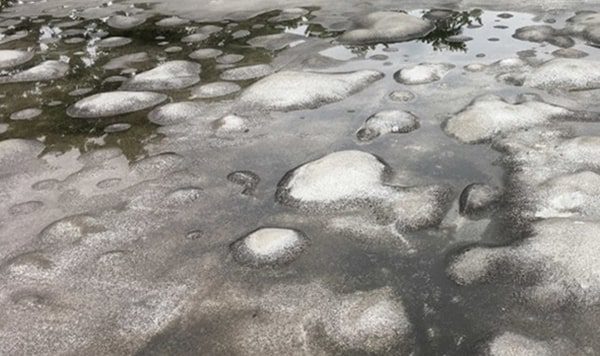
You can see there are a ton of blisters on this roof. Blisters usually form because there was water trapped in the insulation. Those areas are supposed to be removed before installing any roofing system.
Over time, that trapped water can get hot in the Summer, evaporate, and try to escape the roof by going up.
When enough pressure builds up, a blister forms.
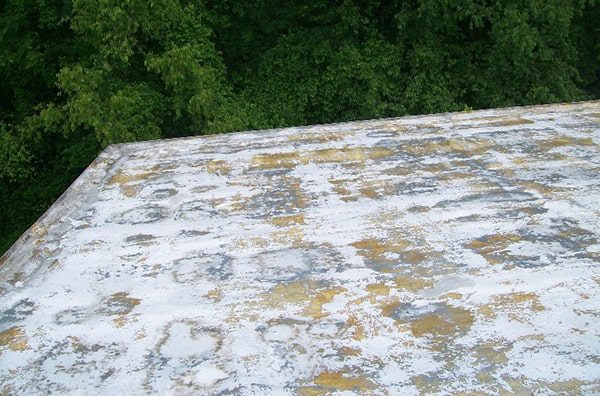
Here is a spray foam roof that has yellow exposed. This means that either there wasn’t enough coating installed on the installation or the coating has worn away because of its age and the roof is well past its warranty.
Now that you know what a good and bad spray foam roof looks like, how is a spray foam roof properly installed?
Advice: These installation disasters come from a lack of knowledge in the proper way to apply a spray foam system. It’s very important to choose a contractor who has years (if not decades) of experience installing foam roofs.
How is a spray foam roof installed?
If you’re new to spray foam roofing, let’s walk through the installation process.
Step #1 – Remove all saturated areas
Before applying any foam, we need to make sure there is no spray foam installed over saturated areas. With water trapped in these saturated areas, the water can move down towards your roof deck, or evaporate and go up, which can cause blisters in your new roof.
A contractor will identify these areas by walking the roof and inspecting the areas of the roof with a high probability of holding water.
A contractor can pull core samples of your roof to detect saturated insulation, and, if needed, can also perform an infrared inspection.
Once all the saturated areas are identified, they are removed and replaced with similar materials.
For example, say some of your Polyiso board insulation is wet, this is removed and replaced with new Polyiso board insulation.
Step #2 – Clean and dry the existing roof
Now that we know there’s no saturation present underneath your roof membrane, we can focus on everything on top of the membrane.
For spray foam to adhere, cure, and perform correctly, it needs to be applied to a dry and clean surface.
A roofing contractor usually does this by power washing the roof clean, blowing all the water towards drains, and then letting the roof sit overnight to dry.
The next morning, the roofers will use leaf blowers to get rid of any contaminants, and then the prep work is complete.
Step #3 – Install the spray foam roof
Spray foam is a combination of two materials, an isocyanate, and a polyol resin, which are pumped from two separate barrels.
The barrels are stored in a box truck that’s parked alongside your building. The materials are pumped through a machine that heats and pushes material equally through heated hoses coming from the truck, and onto your roof to a mixing gun which creates spray foam by mixing a 1-1 ratio of each material.
The fluid comes out of the gun and then expands to 30 times its size within 1 minute to create polyurethane foam.
A spray foam contractor will apply the foam over the existing roof, encapsulating all the penetrations, and making the roof all one layer. The foam can be installed at a consistent thickness or with a taper to create a seamless membrane.
The usual thickness of the foam roof is 1.5 inches to 2.5 inches in thickness, but this is all customized based upon the slope of the roof and the desired R-value the building owner is seeking.
Step #4 – Install protective coating and granules
Once all the foam is applied, it must be protected with coating within 72 hours. UV rays from the sun will begin to degrade the foam if left unprotected. If a coating is not applied within the required time frame, the coating that’s applied will not adhere to phased foam.
What is phased foam?
Phased foam refers to spray foam that has been unprotected beyond the required time frame.
The coating is applied in two separate coats, with the second coat having granules embedded in it.
The granules give the spray foam roof the protection it needs from foot traffic, flying debris, and other objects that could penetrate through.
Some roofs don’t always require granules.
How do you know if there are errors in your spray foam installation?
You should always read your warranty thoroughly, to know what’s covered or not.
When your spray foam roof is finished, whoever is granting your warranty will come to inspect the work.
Here are some things they will look out for:
- Is the correct thickness of foam sprayed around the entire roof?
- Is the correct thickness of coating and granules sprayed around the entire roof?
- Are the correct physical properties of spray foam evident?
- Have all the opportunities for ponding water been eliminated?
- Are all the penetrations watertight?
- Are all the perimeters watertight?
- Is there any off-ratio spray foam installed?
Off-ratio foam can look more like a sponge if it’s resin-rich. Iso-rich spray foam will be more brittle and crunchier, which can crack very easily.
If any of these issues happen, they will most likely be covered under warranty from the manufacturer or the roofing contractor.
All of these installation problems could lead to water entering your roof system.
The warranter knows that if a spray foam roof is installed correctly, the products and materials will hold up for the length of the warranty.
However, here are some unnatural problems that can occur, such as:
- A tornado comes through and damages the roof
- A large branch pokes a hole in the foam roof
- The HVAC technician drops a heavy tool on the foam roof
- Nails are left behind and stepped on which caused a small hole or crack
These issues don’t have anything to do with the products performing how they should, and therefore wouldn’t be covered under warranty.
Here are some other instances that would not be covered under warranty:
Incorrect Repairs – If your roof does have damage or a leak, it’s important to stay within your warranty provider/contractor that installed the roof to resolve the problem. If another contractor/owner uses the wrong materials or methods, it could void the warranty.
Unauthorized Alterations– If a contractor that is not listed on the warranty makes repairs or changes to your roof system, any leaks or damage will not be covered.
Standing Water – Standing water, or ponding water on a roof, can decrease the lifespan of your roof. Standing water typically occurs when there is no proper drainage on your roof (usually due to clogged drains).
Any damage from standing water that is not caused by the installation will not be covered under warranty.
Now that we know about warranties, what’s covered, and what’s not, how do we avoid all of this mess and choose a good spray foam roofing contractor?
How to identify a good spray foam roofing contractor
Here are a few ways you can identify a good spray foam roofing contractor:
- Experience in the application of foam roofs.
- The amount of spray foam roofs they installed.
- They have a list of spray foam roofs they have recoated
Once a spray foam roof is installed, it will have enough coating and granules on it to protect the roof for a certain amount of time.
For 10 years, 20 mils of coatings will be installed.
For 20 years, 30 mils of coating will be installed.
Once this time is over, more coating is installed and the process repeats.
If a spray foam contractor has recoated a bunch of roofs, this means that the foam and coating lasted as long as they were intended to.
This also means that the client has been happy all those years.
If a spray foam contractor doesn’t have a list of recoated clients, you may end up with a contractor who doesn’t have a lot of experience.
They have a list of clients with similar problems that you have
An experienced company has done spray foam jobs over every type of roof out there.
Have a TPO roof that’s been leaking? A good spray foam contractor can give you 5 examples of TPO roofs where spray foam was installed.
Have a gravel built-up that’s been giving you issues. A good spray foam contractor can give you multiple roofs where the gravel has been removed and the spray foam has been installed.
They have industry certifications and awards
The SPFA (Spray Polyurethane Foam Alliance) gives out awards every year to several different spray foam roofing projects.
The SPFA also has training and certifications they award based upon certain credentials. Two of them are becoming a spray foam master installer & a project manager. To get this certification, you must spray (or manage) 500,000 sq. ft. of foam under tight supervisor.
A contractor with SPFA awards and certified installers should give the building owner confidence that they will be receiving a greatly installed spray foam roof.
They can explain the science of spray polyurethane foam roofing
Can the spray foam roofing contractor you chose explain the science of spray polyurethane foam?
If not, installation issues can happen.
For example, if the temperature outside increases throughout the day, what adjustments should be made to make sure good spray foam is being installed?
You may need to adjust the temperature of the foam that is being sprayed out, or you may need to use a different type of foam that cures at a different speed.
There are three energies needed to install spray foam the way it was designed to. If a contractor cannot explain these in great detail, there may be installation issues when there are changes to the environment to properly apply polyurethane foam.
Why should you care if the roof is done right the first time?
In this article, we stated that there is a warranty that comes with a spray foam roof.
You may be wondering “So if the roof is not performing as it should or a lot of issues are occurring, then with the warranty, the contractor will have to come out and redo it and will be covered under warranty at no cost to you.
Yes, that’s true, but aren’t you contradicting why you’re interested in a spray foam roof in the first place?
Most building owners want a spray foam roof because it has a very low chance of leaking, which reduces the number of headaches you’ll have with your roof.
If the roof is installed badly, you’ll have a year’s worth of headaches trying to get ahold of the contractor, making a warranty claim, getting on their schedule, making emergency repairs so water stops entering your building, etc.
It will save you time and a ton of headaches if the roof is installed correctly the first time.
Want to learn more about spray foam roofing? Download our free cheat sheet below: