Summary: In most cases, the best repair option for a gravel built-up roof is to install a spray foam roof. The reason is that it can be installed over the existing roof, eliminating the cost of a tear-off or laying down a cover board. A spray foam roof fills in all the nooks and crannies, increases R-value, is renewable, makes the roof seamless, and provides a new 10-20-year warranty.
So, you have a gravel built-up roof and you have some leaking issues. What repair options do you have?
In this article, you’ll learn:
- The 7 reasons why spray foam roofing it’s the best repair option?
- What is a spray foam roof?
- How can the current conditions of your roof affect what options you have?
- What other roofing systems (besides spray foam) can you install?
Just so you’re aware, we only write articles based on true events and experiences. Every piece of content written at West Roofing Systems is produced in-house. Every article is reviewed and edited by a roofer/salesman with 30+ years of experience in the field.
West Roofing Systems has been specializing in spray foam roofing systems since 1979.
Let’s get started!
Why are spray foam roofs the best repair option for gravel built-up roofs?
There are multiple reasons:
- You don’t need to install a cover board to apply foam. All you have to do is remove the loose gravel and spray foam right over the top of what’s there. This makes the installation very easy, less time-consuming, and less expensive than all other roofing systems.
- Since spray foam is fluid-applied, it will cover all the nooks and crannies of the existing roof.
- Since spray foam is fluid-applied, the slope can be easily customized by spraying more or less foam.
- Spray foam roofs have the best R-value per inch of thickness of any roofing insulation. This will reduce your energy bills every month going forward.
- Spray foam roofs are renewable. When the warranty expires (there are 10, 15, and 20-year options), the roof can be renewed by applying more protective coating. To renew a roof is 33%-50% more cost-effective than installing a new roof. No other roofing system besides SPF is renewable.
- Spray foam roofs are seamless. Seams handle the most stress on a roof and are the leading cause of roof leaks. Since there are no seams on an SPF roof, the most likely cause of roof leaks is eliminated.
- Spray foam roofs are closed-cell. This means if the membrane is punctured, water will sit in the hole and not move. This is different from standard, open-cell insulation which absorbs water and allows it to move throughout the system, eventually causing a leak. Think of continuously dropping water into the corner of a paper towel, eventually the entire towel will be soaked.
Ok, so there are some clear benefits to installing a foam roof over a gravel built-up. But what is a spray foam roof anyways???
What is a spray foam roof?
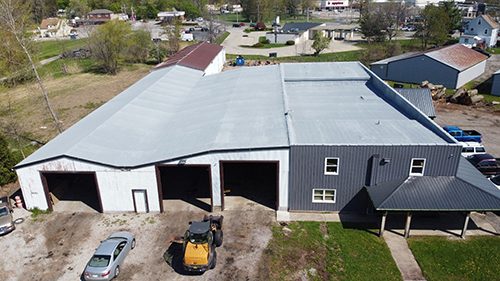
Spray foam roofing is a watertight roofing system that has three parts:
- Spray polyurethane foam
- Silicone coating
- Granules
The foam is produced by combining and heating two chemicals. These chemicals are pumped from a truck, get transferred through a heated hose, and then sprayed right onto an existing roof.
The foam increases in size by 30x, reaching a height of around 1.5 inches. The height (or thickness) of spray foam is customized to every roofing system to create a slope for water to run towards drains.
Spray foam by itself gets damaged by UV rays from the sun. Therefore, a thin layer of silicone coating will be installed over the foam. The thickness of the silicone coating is usually around 20 – 30 mils.
The silicone coating is installed in two separate coats, where the topcoat will be embedded with granules.
The granules are there for added strength and traction for walking.
Here is a video of a spray foam roof application from start to finish:
Now that you understand what a spray foam roof is, you might be wondering how the current condition of your gravel built-up roof can affect what repair options you have?
What are the current conditions of your gravel built-up roof?
Two things greatly influence what roofing options you have. One is how many roofing systems are already installed; the other is how much wet insulation you have.
How many roofing systems are installed?
Is gravel built-up the only roofing system installed on your building? If so, you can make simple repairs (such as identifying and replacing wet insulation) and install a new roofing system over what you already have.
Building code allows for a maximum of two roofing systems.
If you already have two roofing systems installed, then legally you need to remove at least one roofing system before installing another one.
A commercial roofing contractor can identify the number of roofing systems installed on a building through visual inspections and core samples.
How much wet insulation is under the membrane?
If you have gravel built-up roof where 99% of the insulation is wet and saturated, there’s no reason to save this roof.
The usual threshold to determine restoring or tearing off a commercial roof is a saturation level of 20-30%.
If 10% of your roof has wet insulation, then it’s probably in your best interest to restore the roof instead of tearing it all off.
One of the most expensive parts of a roofing quote is the amount of tear-off that’s required. Tear-off is labor-intensive and you must pay to transport all the materials to a landfill.
The amount of wet insulation is determined through core samples and infrared inspections.
Now that you understand how the current condition of your gravel built-up roof can influence the repair options you have, are there other roofing systems (besides spray foam) that can be installed?
What repair options do you have?
Let’s say that the gravel-built-up roof is your only roofing system, and you have some wet insulation, but not much.
Let’s say 10%.
What repair options do you have?
The truth is that you can install any roofing system you’d like. Some people will lean towards single-ply (EPDM, TPO, or PVC) because they are familiar with what they are.
The problems with them are that some contractors won’t remove the gravel before install. This is to save money on installing a cover board. The cover board is recommended to give the rolled sheets something good to adhere to.
Here’s a photo of a single-ply roof over an existing gravel built-up:
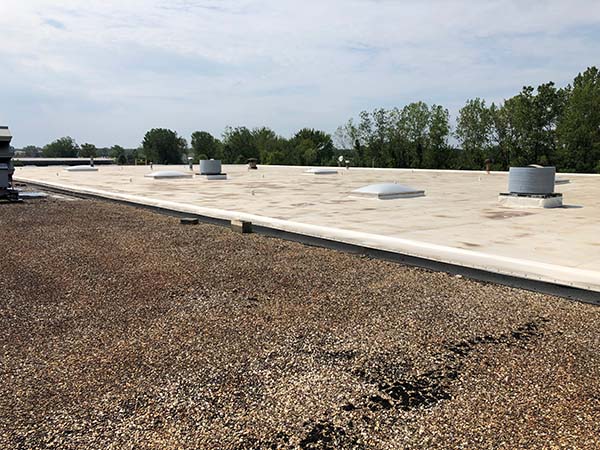
The problem with this setup is all the standing/ponding water that hasn’t run towards a drain. This is likely due to the rock’s underneath moving somehow. This can cause fluctuations in the membrane and provide a bumpy surface. The result is an unpredictable slope that causes random areas to hold water.
Conclusion
Hopefully, you learned a little bit about the options you have if you have a gravel-built-up roof that needs to be repaired.
If you’re new to hearing about spray polyurethane foam roofing, please check out the downloadable “Cheat Sheet” at the end of the article.
Here are some other articles that may be of interest to you: