So, you’ve heard of spray foam roofing and you’re trying to learn more about it.
One thing to consider when looking at different roofing systems is “what can go wrong with it?”
In this article, you’ll learn:
- What can happen if a spray foam company doesn’t know what they are doing
- What happens if the spray foam company goes out of business during the warranty period
- What are the consequences of skipping routine maintenance?
- What is overspray and how is it minimized?
- What if the protective coating is installed “light”?
- What if the contractor installed the foam roof over wet insulation?
And just so you’re aware, every piece of content written at West Roofing Systems is produced in-house. Every article is reviewed and edited by a roofer/salesman with more than 30+ years of experience in the field.
West Roofing Systems has been installing, servicing, and recoating spray foam roofs since 1979.
Let’s get started!
What can happen if a spray foam company doesn’t know what they are doing
If a spray foam company is NOT an expert installing spray polyurethane foam, you might get a roof that doesn’t cure correctly, looks like a moon crater, or doesn’t perform as it should.
Most installation issues come from a misunderstanding of the three E’s of spray foam:
- Electrical – the equipment used in mixing/heating foam
- Environmental – the air temperature, deck temperature, sun, etc.
- Exothermic – the heat created from the chemical reaction when the A and B components meet
A constant eye is needed on all three areas to install good foam.
One example is installing foam on an area of the roof that’s been in the shade all day versus an area that’s been in the constant sun.
The deck temperature in the shade is much lower than the deck temperature that’s been in the sun.
The “electrical” temperature would need to be increased when spraying foam in a shaded area. Once you’re out of the shade, the “electrical” temperature needs to be reduced to apply good foam in the warmer/sunny areas of the roof.
This is a simple example.
Changes in elevation, climate, humidity, wind speed, the temperature one day versus another day, even using a different manufacturer’s foam can affect the “Three E” measurements.
It’s very important to choose a contractor that not only knows how to install good-performing foam, but understands the science so adjustments can be made while they are installing your foam roof.
What happens if the spray foam company goes out of business during the warranty period
Most spray foam roofing installations come with 10-20-year warranties.
This is awesome…unless the spray foam company goes out of business after 3 years.
Since we’ve been in business since 1979, we’ve had several calls from business owners that had spray foam roofs installed, but once they reach out to the company, no one ever picks up.
There’s no voicemail.
There’s no website.
There are no social media pages.
What should a building owner do?
In this case, you’re probably out of luck. We doubt there’s a manufacturer’s warranty.
There’s a difference between a manufacturer’s warranty and a contractor’s warranty.
A contractor’s warranty is solely through the contractor. If they close shop, they close work on your roof (unless there’s something different in the contract).
A manufacturer’s warranty is through the manufacturer of the materials used to install your foam roof. Think Carlisle, Henry, Progressive Materials. All these companies make the “A-side” and “B-side” of materials that combine to produce spray foam.
If something happens to your roof with a manufacturer’s warranty, they can contact West Roofing Systems to perform the warranty work. Or they can choose another contractor in their network to perform the work.
There’s a lot of detail in who does the work, is the contractor responsible for the first 4 years and then less and less responsible as time goes on, etc.
The bottom line is that you don’t want to choose a spray foam company that hasn’t been around long. Or one that puts you in a position where your warranty won’t be transferred.
What are the consequences of skipping routine maintenance?
Taking care of your commercial roof is the same as taking care of your car.
They both need routine maintenance to perform as they are designed to.
Think about your car…how long would it last if you never changed the oil. 20,000 miles?
How long would it last if you did change the oil (and did all the other routine maintenance items)? 150,000 miles?
The same goes for your roof—any roofing system, not just spray foam.
On a spray foam roof, routine maintenance includes:
- Cleaning out all the gutters and drains so water can easily run off the roof
- Repairing any nicks or cuts in the roof
- Making sure all the flashings and penetrations are still fully adhered and watertight
- Removing debris
- Looking for ponding water and investigating the cause
A likely scenario is when a company has a lot of equipment on the roof. That equipment needs to be serviced. Servicemen don’t know when they drop a heavy or sharp tool, it sometimes can cause a small intent.
This is why having a spray foam contractor that knows what to look for is important for your roof’s longevity.
You paid a lot of money for your roof! Protect your investment as best you can.
NOTE: Spray foam manufacturers require roof maintenance to keep a warranty active. Any damage to their products by negligence, act of God, or mechanical damage caused by another contractor won’t be covered by any type of warranty.
What is overspray and how is it minimized?
One problem that spray foam roof installations have that other roofing systems don’t is overspray.
This is because spray foam is “sprayed”, or fluid applied.
Overspray is when the foam material is taken by the wind and carried onto undesirable items, such as cars and windows.
NOTE: If overspray occurs, the foam can be gently removed off of any object.
This is an extra part of a roofing project that spray foam contractors like to minimize (and completely avoid if possible).
Overspray is minimized by:
- Using windscreens when spraying near the roof’s perimeter
- Using spray foam booths that don’t let any overspray occur
- Not spraying foam at all if it’s too windy
This is another reason to choose a trustworthy spray foam contractor. If the contractor won’t clean up overspray in a contract, it’s probably a red flag.
Also, make sure that they have windscreens and spray booths. If they don’t, overspray or project delays can occur.
What if the protective coating is installed “light”?
One thing that would worry me if I was a building owner would be the thickness of the coating.
Coating is installed over spray foam for UV protection and is part of a complete spray foam roofing system:
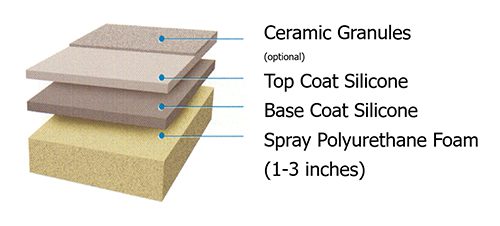
If you get a 20-year warranty (which gets 30 mils of coating), how do I know the coating will be installed 30 mils thick?
30 mils = 0.03 inches.
20 mils = 0.02 inches.
Can the naked eye notice a 0.01-inch difference?
NOTE: A 0.01 inch (or 10 mils) is the difference between a 10-year warranty and a 20-year warranty.
If you choose a contractor who’s “light” on the coating, the roof’s life can be greatly reduced. Make sure when the project is finished, there’s proof that you got the correct milage of coating installed.
What if the contractor installed the foam roof over wet insulation?
This is another installation error that can happen if you choose a fly-by-night contractor.
All of the wet insulation should be removed and replaced before the installation of any new roofing system (not just spray foam).
To find the wet areas, roofing contractors use thermal imaging and/or take core samples.
Once the areas are found and replaced, then the new roofing system can be installed.
If the contractor doesn’t perform an infrared survey and/or pull core samples, it could be a red flag for an improper installation.
When spray foam is installed over wet insulation, the water that’s trapped can’t evaporate and try to escape through the new roof.
What you’ll get are blisters that can affect roof slope (and cause ponding water), but they can also pop, resulting in easy access for water to enter your building.
Some would blame the roofing system for causing the blisters when in reality, it’s because a contractor cut corners by not investigating (and replacing) wet insulation.
Want to learn more about spray foam roofing?
Here are some posts that answer other questions building owners have:
- How much does a spray foam roof cost?
- How long should a spray foam roof last?
- An Honest Comparison: Single-Ply Vs. Metal Vs. Spray Foam Vs. Roof Coating Systems
West Roofing Systems has been installing, servicing, and recoating spray foam roofing systems since 1979. If you’d like us to reach out to discuss a roofing project, you can request a quote here.