Say you’re a building owner.
Say you’re having roof issues.
Say you’d like to take care of the problem as quickly…and as cost-effectively as possible.
If this is you, I’d like to introduce you to a roofing system that most don’t know about.
It’s called spray polyurethane foam roofing and we’ll explain how the system works below.
Before we get started, we wanted to point out that West Roofing Systems has been installing spray foam roofs since 1979. In that time, we’ve installed more than 60 million sq. ft. of spray foam roofing.
We didn’t want you to think we’re the new guy on the block explaining the newest, unproven innovation.
Let’s get started.
NOTE: if you’d like to watch a video on how spray foam works from start to finish, please view the video below.
What chemicals produce spray foam roofing?
A spray foam roof is produced by spray polyurethane foam (SPF). SPF is made by a 1:1 ratio mixture of two chemicals:
- Polyol/Resin, or Side A
- Isocyanate, or Side B
These two chemicals are brought to the job site, which are stored in separate 55-gallon containers. The chemicals are pumped through heated, high-pressure hoses, and are mixed at the spray gun.
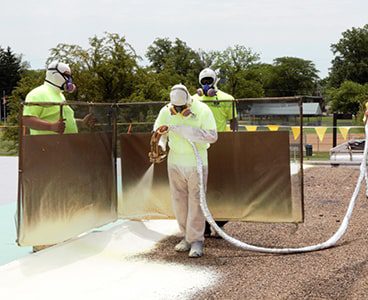
What preparation is needed before spray foam is installed?
The roof must be properly prepared before spray foam can be installed on a roof.
The first step is ensuring the existing roof is dry and sound.
A visual inspection, the pulling of core samples, and/or an infrared inspection are all used to identify the wet (or saturated areas) of a roof.
All wet areas must be removed before any roofing system (not just spray foam) is installed.
Once the wet areas are removed, they are replaced with similar roofing material.
The next step is to ensure the roof is sound, meaning the top layer is fully-adhered to the insulation below. Some additional fastening may be required.
Spray foam needs a fully adhered substrate to be applied to.
A common example is a single-ply roof where the seams are fastened together. Since the roof only adheres at the seams, this wouldn’t qualify as a fully adhered substrate.
In this scenario, a cover board may be installed over the single-ply roof to create a fully-adhered substrate for spray foam to be installed on.
Spray foam can be applied to every existing roofing system, but depending on the roof system that’s already there, the preparation is different.
NOTE: Here’s a link to a blog post about how spray foam is installed over common roofing systems, such as TPO, EPDM, Metal, Gravel-Built Up, and more.
How does spray foam go onto a roof?
Spray foam is “spray-applied” onto an existing roof, where a thin layer of foam will adhere to a substrate. In about 30-60 seconds, spray foam will expand 20-30x in size.
Spray foam is installed at a minimum of 1” thick. The usual application is 1.5-2” thick.
Thickness is determined by R-value requirements or preferences, slope, building codes, how much heat/cool is lost throughout the building, and many other variables.
When a spray foam roofing contractor gets to a penetration, such as HVAC units, skylights, or pipes, spray foam is installed around the penetration, keeping the roof seamless.
Here’s a video of spray foam being installed around a box, simulating a penetration:
What is a complete spray foam roofing system?
A complete spray foam roofing system consists of:
- Spray polyurethane foam
- An elastomeric coating basecoat
- An elastomeric coating topcoat
- And embedded granules
Once spray foam is installed, it needs protection from UV rays. To protect the foam, an elastomeric coating (usually silicone) is installed over the spray foam no less than 2 hours after application and no more than 72 hours.
Once the basecoat of silicone has been applied and cured, a second application (the topcoat) of silicone is applied. In the topcoat, granules are embedded in the wet topcoat for increased strength and stability.
Once the spray foam roofing system is complete, you’ll see a roof similar to this:
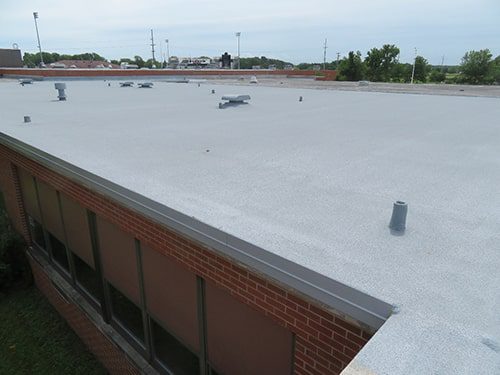
After installation, is maintenance required?
Yes.
This can be done internally, or through a spray foam roofing contractor, but the bottom line is that it needs to be done!
Why?
It’s the same reason maintenance is done on the car you drive. If you don’t change the oil or replace the brakes, the car will not last as long as it could have if routine maintenance were performed.
For a spray foam roof, a visual inspection is recommended twice per year, once in the Fall (before winter) and once in the spring (after winter).
This timing of maintenance is recommended because you’ll be able to clear all the drains, debris, and patch up any holes after all the Fall leaves have dropped. Then in the spring, once all the spring blossoms have fallen off the trees, that way you’ll have a clean roof that performs great during April showers and the intense heat of Summer.
A visual inspection should also happen after intense weathering events.
Something that could happen is when bad storms arise, debris is blown around. A small crack could happen if a large branch with a sharp point were to land on your spray foam roof.
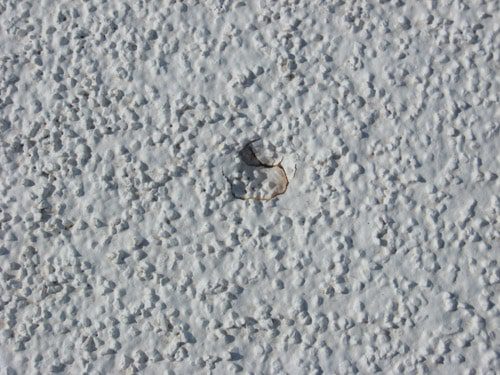
A small crack is easy to repair. All you need to do is cut around the area, make sure it’s dry, fill it with caulk or coating, and then smooth it out.
If a small crack is ignored, water could enter the crack and not move off your roof.
Now, this won’t ever cause a leak in a spray foam roof because it’s closed-cell (but, if ignored for a long period, constant water sitting in the crack can freeze and thaw, and under certain weather conditions, it could eventually allow water into the underlying insulation).
Water that doesn’t move towards drain locations can wear out any roofing system sooner than intended.
How long will a spray foam roof last?
A spray foam roof can last as long as the building is around. Most spray foam roofs come in 10-15-20-year warranties, but it’s what happens once the warranty expires that keeps them performing.
After the initial installation, a spray foam roof is protected with 20-30 mils of coating with granules. After 15 years, what started as 25 mils of coating, would naturally wear down to around 7-10 mils of coating. On year 16, what happens is what’s called a “recoat”.
A recoat of a spray foam roof is generally power washing the roof clean, making any small repairs, and then adding more coating onto the roof.
A contractor can bring that 7-10 mils of coating back up to 25 mils, and a new 15-year warranty can be granted.
In this process, the spray foam is never touched and doesn’t lose any R-value or insulating properties.
This is how a spray foam roof is a truly, renewable roofing system.
NOTE: A recoat costs about ½ to 1/3 of the original installation. A single-ply roof would generally last the same amount of time but would need to be completely ripped off and removed, which would cost 100% of the original installation.
What are your next steps?
There are two ways you can go.
- If you’d like to start a conversation about your roof, please request a quote, and we’ll contact you as soon as possible.
- If you’d like to learn more about spray foam roofing, we’ve created a cheat sheet: