Are you worried that a spray foam roof won’t hold up against foot traffic, is only a temporary solution, or is difficult for contractors to install correctly?
In this article, we’ll tackle the five biggest myths about spray foam roofs, back them up with real facts, and share what we’ve learned from over 45 years of installing SPF roofs across the country.
Here are the myths:
- Spray foam roofing is just a temporary fix.
- Spray foam roofs are “weak” and cannot handle foot traffic.
- Spray foam is a new and unproven commercial roofing system.
- Spray polyurethane foam is very difficult to install correctly.
- Nobody installs spray foam roofing systems.
Myth 1: Spray Foam Roofing Is Just a Temporary Fix
Many building owners think spray foam is a short-term patch, not a real roofing system. The truth? A properly installed and maintained SPF roof can last decades — not just a few years.
Some of the roofs we installed in the early 1980s are still performing well today. Instead of full tear-offs, SPF roofs can be recoated every 10–20 years, extending their life at a fraction of the cost of replacement.
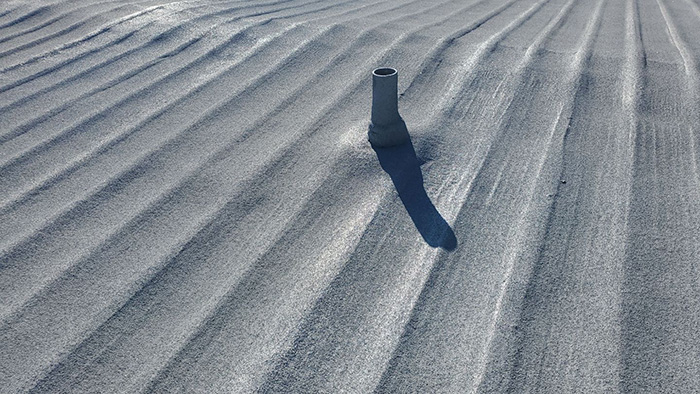
Myth 2: Spray Foam Roofs Are Too Weak for Foot Traffic
We often hear, “Won’t spray foam dent or get damaged if someone walks on it?” Not when it’s installed correctly.
The average compression strength of spray polyurethane foam is 60 PSI. This is stronger than the commonly used “ISO-Board”.
Spray foam roofs are topped with a protective coating embedded with granules, adding strength and slip resistance. For areas with regular foot traffic, we install designated walkways with extra sand or coating layers for stability and safety.
Maintenance crews, inspectors, and contractors walk on these roofs every day without issue.
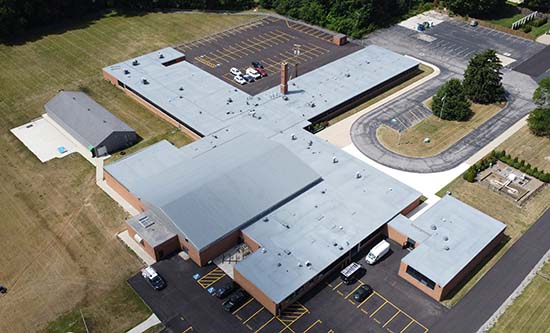
Myth 3: Spray Foam Roofing Is New and Unproven
While SPF roofing might feel like a newer system compared to older ones like gravel built-ups or metal, it’s far from new or unproven.
Our company began installing commercial spray foam roofs back in 1979.
That makes SPF older than TPO membranes, which own a large share of the market. Today, spray foam is trusted on schools, warehouses, government facilities, factories, all different kinds of slopes, flat roofs, and even high-wind coastal buildings.
Most spray foam roofing projects come with a 10-20-year warranty. This depends on the thickness of the protective coating that’s installed over it.
- A 10-year warranty gets a 20-mil thickness of coating
- A 15-year warranty gets a 25-mil thickness of coating
- A 20-year warranty gets a 30-mil thickness of coating
Hundreds of commercial spray foam roofing systems have been installed, lasted the warranty without any issues, are recoated, and a brand new 10–20-year warranty begins.
If you’d like a list of customers who have had their roofs recoated, please contact us at anytime.
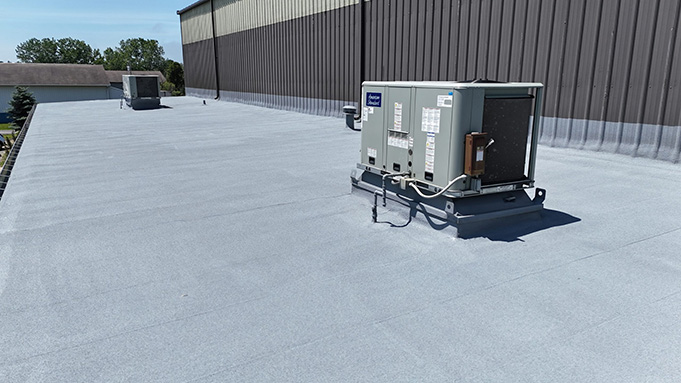
Myth 4: Spray Foam Is Hard to Install Correctly
Here’s a partial truth: Spray foam installation does take skill and experience.
For Spray foam to be laid down correctly, it needs three types of energy:
- Electrical – the equipment (hose heats/pre-heats) used in heating the foam to the required temperature.
- Environmental – the air temperature, deck temperature, sun, etc.
- Exothermic – the heat created from the chemical reaction when the A and B components meet.
To learn more about this, please read this article about the 3 E’s of spray foam roofing.
It’s exactly why fewer contractors do it — and why you should only trust spray foam roofing professionals. Our crews go through ongoing training and follow strict manufacturer application specifications to ensure the roof performs as promised.
THIS IS VERY IMPORTANT!: Many contractors say they can apply foam…they don’t know what they are doing…the customer is left with an underperforming roof…and the system (not the contractor) is to blame. The short of it is that the spray foam installer needs to be a roofer, not just a foam installer.
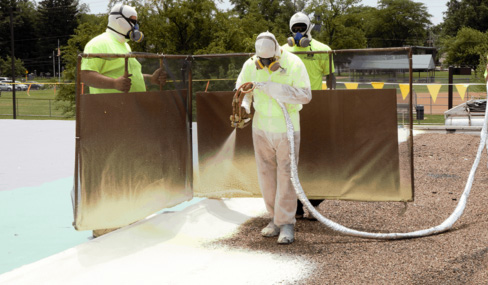
Myth 5: Hardly Anyone Installs Spray Foam Roofing
Some building owners assume finding a qualified spray foam contractor is impossible. It’s true there’s a higher barrier to entry — the rigs are expensive, and the crews must be skilled.
But there are far more qualified SPF contractors than most people think — and the market has grown steadily as more building owners see the benefits of the system, including:
- An increase of R-value by 6.5 per inch of thickness. This provides a higher R-value than any other insulation available. This reduces energy costs considerably, especially with an existing roof that has little to no R-value.
- A seamless membrane. There are no fasteners, seams, or screws that can back out or lose adhesion. Roofs fluctuate daily with changing temperature, creating stress on seams. Loss of seam adhesions is the #1 cause of roof leaks.
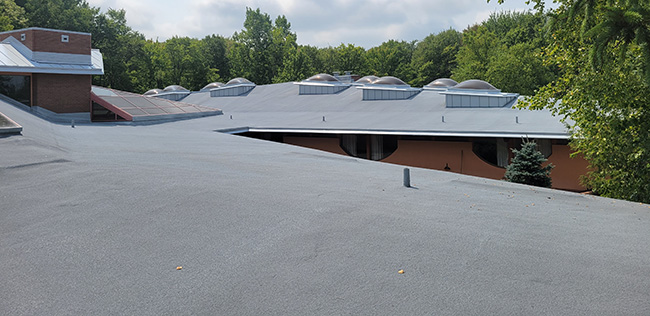
- The ease of maintenance. Since there are no seams or fasteners, it’s easy to see potential problems when the entire roof is one layer:
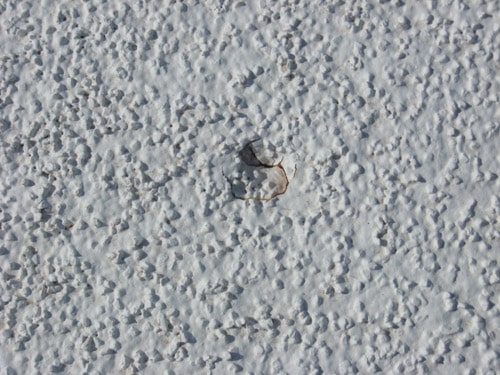
If you need help evaluating local options, contact us, and we’ll be happy to point you in the right direction.
Take the next step by checking out our Ultimate Guide to Spray Foam Roofing or request a free roof assessment to see if SPF is right for your building.
We’ve been pioneering commercial spray foam roofing since 1979. If you have any questions, we’d love to help — just contact us here.